Столярный верстак – преимущества, изготовление, работа + видео
Необходимые инструменты
Олифа Клеи Доска Брус Шлифмашины Струбцина Саморезы Дрель электрическая Болты Показать все
Содержание
- 1 Применение инструмента и устройство столярного верстака
- 2 Выбор материалов и чертеж столярного верстака
- 3 Деревянный столярный верстак своими руками
- 4 Как сделать деревянный столярный верстак — пошаговая схема
- 4.1 Шаг 1: Создание основания
- 4.2 Шаг 2: Устройство столешницы
- 4.3 Шаг 3: Установка тисков и дополнительных элементов
- 4.4 Шаг 4: Создание упоров
В квартире, на даче, в гараже очень часто возникает необходимость создания места, которое будет подготовлено для работы с деревянными изделиями, металлическими деталями и даже камнем. И вряд ли получится придумать что-то лучше, чем верстак столярный складной. С его помощью вы сможете мастерить в любое удобное время!
Применение инструмента и устройство столярного верстака
Столярный либо слесарный верстак – устойчивый рабочий стол, предназначенный для выполнения работ с различными материалами. Чем больше будут его размеры, тем больше могут быть детали и запчасти для работы на верстаке. При этом работа с материалами может осуществляться и механическими изделиями (электродрель, электрорубанок) и ручными (например, ножовка).
Оборудование состоит из следующих элементов:
- Рабочий стол. Чаще всего создается из массивных досок с толщиной около 6-8 см. Из дерева лучше всего выбирать твердые породы – граб, бук или дуб, ведь так верстак прослужит дольше, а при выборе более хрупких пород вам придется чаще тратить время на замену;
- Тиски, которые навешиваются на лицевую сторону крышки – они нужны для крепежа изделий. Если размеры устройства превышают один метр, лучше смонтировать несколько пар тисков, используемых для небольших и для массивных деталей, при этом более крупная пара должна создаваться из дерева;
- Верстальные опоры, для создания которых лучше применять “мягкое” дерево – липу и сосну. При этом опоры должны для надежности соединяться между собой с помощью продольных планок;
- Полки верстака, которые могут закрепляться на опорах подверстачного пространства;
- В передней части рабочего стола нужно просверлить несколько отверстий для монтажа клиньев и иных запчастей для крепежа крупных элементов.
Заднюю часть нужно оборудовать углублением, необходимым для хранения деталей и различных материалов. Если не хотите делать сложную работу, замените углубление несколькими закрепленными рейками.
Верстаки имеют несколько видов исполнения:
- Стационарный, который прост в создании, однако “крепко” привязан к единственному месту. Лучше всего применять его при работе с запчастями из древесины и крепкими досками;
- Мобильный – маленький стол размером около 60*70 см и весом до 25 кг. Для создания максимальной устойчивости стоит сделать ножки из металла. Используется при работе с небольшими деталями;
- Третий вид – составные верстаки, которые держатся с помощью болтовых соединений. Их главное удобство – в простоте замены деталей и возможности разбирать инструмент.
Выбор материалов и чертеж столярного верстака
Размеры, в частности, высота столярного верстака, зависят от вашего роста, ведь он должен быть удобен для работы в полный рост, чтобы выполнять все операции, не сутулясь. Чаще всего это около 80-100 см. А вот конфигурация инструмента зависит от нужд и возможных операций, которые вы будете проводить, однако стоит присмотреть несколько тисков и упоров для крепления запчастей. Ширина устройства зависит от площади гаража или склада, где он будет храниться.
Однако наиболее удобным вариантом считается, когда его длина составляет 1,5-2 метра, а ширина – примерно 80 см. Для удобства сделайте под рабочим столом несколько ящичков, где можно хранить различные инструменты и мелкие детали. Также, занимаясь проектом, учитывайте, каким будет верстак, будет ли он мобильным либо установленным стационарно.
Если хотите сделать разбирающееся устройство, намного лучше сделать рабочую поверхность более тонкой, а ножки складными – для удобства, устанавливать оборудование желательно вблизи окна, также нужно предусмотреть вблизи розетки для возможности работы с инструментами.
Важно грамотно подойти к выбору материалов для создания верстака. Лучшим считается строганный брус, характеризующийся практичностью и долговечностью. Многие мастера в качестве рабочей поверхности берут цельное полотно – старые двери, ламинированное ДСП. Материал крепления подбирается с учетом структуры оборудования – это могут быть и деревянные, и металлические стойки. Прежде чем создавать верстак, подберите тиски – лучше, если их будет несколько штук. Одни будут использоваться для крепления длинных досок, вторые – для мелких деталей.
Деревянный столярный верстак своими руками
Создание верстака осуществляется в несколько этапов. Сначала проводятся работы по сборке основания, потом – по установке столешницы. Каждый этап должен быть проконтролирован на ровность установки всех элементов.
Как сделать деревянный столярный верстак — пошаговая схема
Шаг 1: Создание основания
Основание – рама из деревянных брусьев, которая скреплена так, чтобы конструкция в результате вышла максимально надежной. Для этого вам нужно между ножками расположить перемычку, а посередине установить царгу. Их лучше всего расположить на расстоянии около 40 см от уровня пола. К слову, они также пригодятся для создания дополнительных полок. Брусья совмещаются с помощью строительного клея.
Там, где проводить подобные работы невозможно, нужно эксплуатировать саморезы. Если вы собираетесь сделать разбирающийся инструмент, лучше всего опоры соединять металлическими уголками. В любом случае, сначала подготавливаются все пазы, затем собирается конструкция, клеем обрабатываются места соединения, закрепляем их с помощью струбцин. Лучшим вариантом при устройстве стационарного верстака считается возможность часть инструмента прикрепить к стене для надежности.
Шаг 2: Устройство столешницы
Если сооружать столешницу из нескольких досок, то важно максимально качественно сбить их, чтобы в зазоры не попадал мусор и опилки. Размеры должны превышать ширина и длину основания на 3-5 см – это позволит со всеми удобствами чистить инструмент. Столешница прикручивается и прибивается к нескольким доскам, которые находятся с другой стороны рабочей поверхности, а в основании необходимо расположить пазы для монтирования брусков. Рабочий стол нужно привести в порядок с помощью шлифмашины, покрыть олифой для снижения риска получения травм от щепок, а к его основанию болтами прикручиваются металлические уголки.
Шаг 3: Установка тисков и дополнительных элементов
К уже сделанной рабочей поверхности крепим тиски, под которые следует создать углубления в рабочей поверхности, это позволит расположить вертикальную пластину в одну плоскость со столешницей. С нижней стороны устанавливаем фанерную прокладку, при этом важно сделать так, чтобы губы тисков располагались на одном уровне с поверхностью. Приложив тиски, отмечаем участок, где будут сверлиться отверстия, и прикрепляем их с помощью гаек. Заранее фрезеруем отверстия, чтобы болты в них «потонули». Лучше всего устанавливать тиски не по углам, что сделает их надежными даже при условии больших нагрузок.
Шаг 4: Создание упоров
Кроме тисков, вы должны сделать и упоры. Их, конечно, можно сделать самостоятельно, но лучше приобрести и готовые. Однако если решили создать их своими руками, приготовьте прямоугольные упоры, которые можно будет регулировать по высоте. Болты применять не стоит, поскольку они могут повредить заготовки при работе. На рабочей поверхности проделываем отверстия под упоры, при этом располагать их желательно на расстоянии до 50 % от хода тисков – это позволит надежно закрепить любые заготовки.
Теперь, ознакомившись с тем, как самому сделать столярный верстак, можете приступать к работам.
- Автор: Менеджер Андрей
- Распечатать
Оцените статью:
(2 голоса, среднее: 5 из 5)
Поделитесь с друзьями!
window.yaContextCb.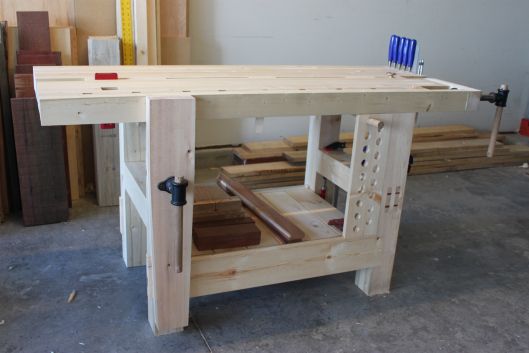
«+»ipt>»; cachedBlocksArray[281763] = «
window.yaContextCb.push(()=>{ Ya.Context.AdvManager.render({ renderTo: ‘yandex_rtb_R-A-1479353-86’, blockId: ‘R-A-1479353-86’ })})«+»ipt>»; cachedBlocksArray[281761] = «
«+»ipt>
((__lxGc__=window.__lxGc__||{‘s’:{},’b’:0})[‘s’][‘_226729’]=__lxGc__[‘s’][‘_226729’]||{‘b’:{}})[‘b’][‘_695142’]={‘i’:__lxGc__.b++};«+»ipt>»; cachedBlocksArray[281757] = «
«+»ipt>
((__lxGc__=window.__lxGc__||{‘s’:{},’b’:0})[‘s’][‘_226729’]=__lxGc__[‘s’][‘_226729’]||{‘b’:{}})[‘b’][‘_689910’]={‘i’:__lxGc__.b++};«+»ipt>
«+»ipt>((__lxGc__=window.__lxGc__||{‘s’:{},’b’:0})[‘s’][‘_226729’]=__lxGc__[‘s’][‘_226729’]||{‘b’:{}})[‘b’][‘_689910’]={‘i’:__lxGc__.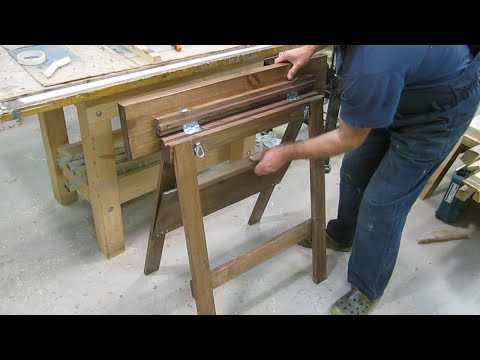
«+»ipt>
«+»ipt>
((__lxGc__=window.__lxGc__||{‘s’:{},’b’:0})[‘s’][‘_226729’]=__lxGc__[‘s’][‘_226729’]||{‘b’:{}})[‘b’][‘_689910’]={‘i’:__lxGc__.b++};«+»ipt>
«+»ipt>
((__lxGc__=window.__lxGc__||{‘s’:{},’b’:0})[‘s’][‘_226729’]=__lxGc__[‘s’][‘_226729’]||{‘b’:{}})[‘b’][‘_689910’]={‘i’:__lxGc__.b++};«+»ipt>»; cachedBlocksArray[281759] = «
«+»ipt>
(MRGtag = window.MRGtag || []).push({})«+»ipt>»; cachedBlocksArray[281758] = «
window.yaContextCb.push(()=>{ Ya.Context.AdvManager.render({ renderTo: ‘yandex_rtb_R-A-1479353-49’, blockId: ‘R-A-1479353-49’ })})«+»ipt>»;
Как сделать верстак своими руками
Для любого хозяйственного мужчины нужно свое оборудованное рабочее место для хранения инструмента и совершения столярно-слесарных работ. В таком случае просто необходимым элементом рабочего места станет верстак, и сейчас мы расскажем, как сделать верстак своими силами.
Действительно, чтобы купить его, потребуется выложить значительную сумму и, кроме этого, подобрать нужный размер именно под ваше помещение представляется довольно сложной задачей. Но если делать самому, то можно выбрать требуемый размер верстака с точностью до сантиметра.
Какие верстаки бывают
Верстак — это рабочий стол, на котором мастер производит ручные работы по обработке деревянных, металлических и других деталей. Самостоятельно сделанные верстаки устанавливают в гараж, на даче и даже в квартире. Верстак оснащен различными дополнительными устройствами, которые могут понадобиться при работе, такими как упоры и тиски. Кроме этого, в верстаках устанавливают емкости для хранения различных инструментов и даже документации. По типу работ различают столярные, плотницкие и слесарные верстаки.
Верстак своими руками видео:
Столярный верстак
Стандартный столярный верстак имеет такую конструкцию. Основными частями являются верстачная плита и подверстачье. Подверстачье выглядит как стойка (обычно две), которые соединены между собой деревянными брусками. Материал этого элемента стола обычно сосна или другая древесина мягких пород.
Верстачная доска или крышка изготовляется из твердых пород древесины, например, дуба, и имеет толщину до 8 см. Поверхность доски покрывается олифой. Если вы собираетесь собрать верстак своими руками, то вы должны знать, какие дополнительные устройства нужно установить на столешнице.
Обратите внимание!
В первую очередь это должны быть тиски, расположенные в передней части и использующиеся для фиксации деталей.
В задней части необходимо сделать углубление, для хранения в нем инструмента небольших размеров. На крае верстачной доски имеются отверстия, в которые вставляются деревянные чурочки и гребенки из металла. Стандартный верстак пригоден в основном для ручной работы, а если вы хотите пользоваться еще и электроинструментом, то для этого надо выбирать верстачную доску с большим количеством отверстий для упоров.
На фото столярный верстак своими руками
Слесарный верстак
Слесарный верстак более мощное сооружение. Оно имеет металлический каркас, на который укладывается деревянная крышка толщиной до 6 см и покрытая железным листом. Крышка окантована трехсторонним бортом и на ней, в большинстве случаев, устанавливаются слесарные тиски. Столешница на таких верстаках делается мощной, чтобы она могла выдерживать высокие ударные нагрузки, в том числе и кувалды.
Материал выбирается по желанию, но наиболее популярный МДФ с оцинковкой, которая позволяет защищать столешницу от влияния агрессивной среды, такой как бензин, масла или растворители. Кроме того, такая столешница легко чистится от загрязнений. Слесарный верстак оснащен несколькими выдвигающимися ящиками для складывания инструмента.
На фото слесарный верстак своими руками
Это интересно! Делаем шкаф-купе из гипсокартона своими руками: чертежи с размерами и подробная видеоинструкция
Плотницкий верстак
Еще одним видом таких конструкций является верстак плотника. Это рабочее место предназначено для обработки досок и имеет размеры, значительно превышающие два предыдущих варианта. Его габариты имеют длину до 6 м и ширину 1 м. На плотницком верстаке обязательно устанавливается упор для обработки доски. Он имеет вырез в виде треугольника, для закрепления доски при помощи клиньев, и используется во время обработки ее кромок.
[rek_custom1]
Изготовление строительного верстака
Давайте разберемся, как сделать столярный верстак своими руками. Сначала надо сделать каркас из брусьев, а между ножками, для прочности, установить перемычку и царгу (соединительный элемент, скрепляющий конструкцию). Желательно чтобы они располагались на расстоянии около 45 см от пола. Монтаж каркаса верстака происходит в таком порядке. Сначала нужно осуществить подготовку пазов, затем собираем конструкцию и промазываем точки соединения клеем. Окончательный крепеж проводим с помощью струбцин.
На фото верстак плотника
Это интересно! Трубогиб для медных труб: 4 разновидности и самостоятельное изготовление
Столешница для верстака
Стоит напомнить, что изготовление любой конструкции происходит более быстро и качественно, если у вас под руками есть хотя бы самый простой чертеж столярного верстака или его части. Ниже мы приведем чертеж столешницы, вид сверху.
Если столешница изготавливается из нескольких досок, то надо обеспечить отсутствие щелей между ними, во избежание, при последующей работе, забивания туда пыли. Размеры столешницы должны быть больше на 3—5 см самого верстака, для большего удобства чистки инструмента. Столешницу надо обработать шлифмашиной и покрыть лаком. Это будет служить защитой от попадания заноз в руки.
Установка тисков и создание упоров
После того как мы установили столешницу, нужно монтировать на них тиски. Для этого, на рабочей поверхности надо вырезать углубление, чтобы можно было поставить вертикальную пластину в одной плоскости со столешницей. Ставим тиски в место, где они будут стоять в будущем, желательно чтобы это был не угол, и делаем наметку для сверления. Затем прикручиваем гайками.
Обратите внимание!
Упоры можно приобрести в магазине, а можно сделать самостоятельно.
Тогда посоветуем сделать их прямоугольной формы с возможностью регулировки по высоте. Отверстия под упоры желательно производить на длину 50% от хода тисков. При таком раскладе вы сможете хорошо зафиксировать разные заготовки. Видео-инструкцию по изготовлению верстака можно посмотреть в нашей статье.
Деревянный верстак
Это интересно! Делаем угловой шкаф на кухню своими руками: от проекта до результата
Изготовление слесарного верстака
Давайте рассмотрим, как можно сделать слесарный верстак своими руками.
- Определим высоту будущего стола. Для каждого человека она может быть разная, к примеру, если мужчина имеет рост 180 см, то высота верстака составляет 90 см. Но все-таки для окончательного решения нужно ориентироваться только на себя.
- Не забываем, что чертежи слесарного верстака, нарисованные вами, пригодятся для более быстрой и качественной сборки.
- Для слесарного верстака каркас лучше всего сварить из профильной трубы и уголков, но в крайнем случае его можно сделать так же как и столярную конструкцию, из брусьев.
- Чтобы конструкция была максимально прочная, нужно поставить между ножками распорки. Иногда, вместо распорок устанавливают полочку, в которую в последующем можно складывать инструмент, лакокрасочные жидкости или другие нужные предметы.
- Для стойкости конструкции можно прикрепить ножки к полу. Это исключит шатание верстака при работе.
- Соорудите столешницу из МДФ и при возможности оцинкуйте. Это значительно повысит ее прочность.
- Если вы хотите, чтобы ваш верстак был оснащен выдвижными ящиками, то поставьте под верхними брусьями полозья, похожие на те, что устанавливаются для ящичков в компьютерных столах.
Тогда у вас будет место хранения для мелких деталей, шурупов и гвоздей.
Складной верстак
Есть еще одна разновидность верстаков, которые применяются как для столярных, так и слесарных работ. Это складной верстак. Он очень удобен при отсутствии лишней площади в помещении. Поработав на нем, его всегда можно сложить и поставить в угол для ожидания следующей работы. Кроме того, его можно в сложенном состоянии перевести на дачу. Такой верстак состоит из двух частей: съемной верстачной доски и складного стола. Он обычно изготавливается меньших размеров, чем стационарный стол.
Это интересно! Обратный молоток: рассматриваем принцип работы и делаем инструмент своими руками
Верстак своими руками видео:
Верстак 21 века | Популярные Деревообработка
Мы можем получать комиссию, когда вы используете наши партнерские ссылки. Однако это не влияет на наши рекомендации.
Этот гибридный дизайн позволяет работать так, как вы хотите.
Хороший дизайн — это не более чем выборочное воровство. Этот верстак — хороший тому пример. Сочетание особенностей нескольких исторических форм, от Roubo до Workmate, становится новой формой, подходящей для того, чтобы стать центром современного деревообрабатывающего цеха.
Я никогда не видел верстак, который бы меня полностью устраивал. У меня есть отношения любви/ненависти со многими общими чертами. Мне нравятся лотки для инструментов, но я ненавижу то, как в них скапливается стружка и другой мусор.
Я хочу иметь возможность быстро зажимать детали, но скорость ничего не значит, если зажим ненадежен и ненадежен. Хороший дизайн — это также искусство компромисса, нахождение золотой середины между крайностями.
Создание этой скамьи началось с идеи воссоздания английской скамьи Николсона. Николсон был популярен в колониальной Америке, и его вариации появлялись в книгах по деревообработке до 19 века. 20 с. Доминирующей чертой Nicholson является широкий передний фартук, который позволяет прикрепить работу к передней части скамьи, а также к ее верхней части.
Недостатком удлиненного фартука является то, что он ограничивает возможность зажима верхней части скамьи с края. Я сузил и опустил фартук, чтобы можно было прижимать работу к скамье в двух направлениях. Меня также заинтриговали разобранные столярные изделия на некоторых исторических скамейках Николсона. Хотя я не планирую часто перемещать свою скамейку, я решил сделать ее управляемыми кусками, чтобы облегчить процесс ее изготовления и сборки.
Дизайн основан на функции готовой скамьи, а также на процессе ее изготовления, перемещения и обслуживания. Инструменты, которые я использовал для его изготовления, — это базовое домашнее оборудование — 10-дюймовая гибридная настольная пила, 6-дюймовый фуганок и 12-дюймовый рубанок. И мне не нужна была скамья, чтобы построить свою скамью. Сначала я сделал верх, а затем поместил его на пару лошадей.
Одноразовый малярный валик быстро наносит ровный слой желтого клея. Нанесите клей только на одну сторону ламината. Выполнение обеих сторон тратит время и клей.
Лучшая причина для сборки верхней части скамейки в первую очередь состоит в том, что когда она будет завершена, ее можно будет приступить к изготовлению и сборке всех остальных частей. Это почти так же хорошо, как иметь место, где можно сесть, когда вы на полпути к сборке стула.
Я начал с грубых пиломатериалов из ясеня 8/4 и выбрал самые прямые куски, чтобы использовать их для верха. Пропустив один край через фуганок, я разорвал каждый кусок до грубой ширины 3¼ дюйма. Затем я приклеил одну сторону каждой детали к фуганку. Когда у меня было готово 14 деталей, я перешел к рубанку.
Я хотел, чтобы заготовка была толщиной не менее 1 7/8 дюйма, но перестала фрезеровать, когда у меня были две чистые грани. Каждая половина топа состоит из шести частей, склеенных лицом к лицу, и, оставив части максимально толстыми, я смог максимально увеличить ширину. Если бы запас оказался тоньше, чем планировалось, я бы добавил седьмой кусок. Цель заключалась в том, чтобы половинки верхней части были шириной не менее 11½ дюймов, но менее 12 дюймов.
Длина скамьи также была переменной. Я хотел минимальную длину 84″, но смог получить чистую длину 90″ из грубого материала длиной 8 футов. После того, как все детали были отфрезерованы, я оставил их на выходные, чтобы убедиться, что древесина не сдвинется и не деформируется.
Я начал ламинировать верхние доски парами, склеенными лицом к лицу. Чтобы они оставались плоскими, я скрепил их вместе на самой прочной и прямой поверхности: двутавровой балке из фанеры толщиной 3/4 дюйма. Я даю каждой паре посидеть в зажимах не менее четырех часов и оставляю их все на 24 часа, чтобы клей высох.
Назад к фрезерованию, затем серьезному склеиванию Эта скамья была разработана с учетом имеющегося оборудования. После очистки одной поверхности рубанком противоположная поверхность строгается на переносном станке.
Края каждой склеенной пары я провела по фуганку, чтобы получить ровный квадратный край каждого ламината. Затем я пропустил доски кромкой через рубанок. И снова я остановился, когда у меня было две чистые поверхности, вместо того, чтобы доводить доски до определенной толщины.
Толщина очищенных пар немного превышала мою запланированную толщину 3″, но мне все равно нужно было удалить часть материала после склеивания каждой верхней секции. Сколько нужно удалить, будет зависеть от того, насколько хорошо эти части сочетаются друг с другом.
Я поставил две длинные доски между лошадьми и положил поперек них квадратные доски на расстоянии около фута друг от друга. Это дало мне хорошую ровную поверхность для работы и предоставило возможность дотянуться вокруг, над или под вершинами, когда я устанавливал зажимы. Пробная укладка трех пар досок дала мне уверенность, что я смогу склеить каждую половинку за один раз.
Имея почти все зажимы в магазине, я намазал желтый клей на одну сторону двух деталей с помощью малярного валика шириной 3 дюйма. Нанеся ровный слой клея, я повернул детали 90˚ и начинаем затягивать зажимы, работая от центра к концам.
Обрезка верхних половин до конечной длины находится в пределах возможностей этой 12-дюймовой торцовочной пилы с подвижным составом.
Деревянные шурупы на концах клеевых соединений предотвращали соскальзывание деталей. Я удалил остатки клея мокрой тряпкой и скребком и оставил кусочки в зажимах на ночь.
Поскольку перед склеиванием я тщательно фрезеровал детали и аккуратно приклеивал их на плоскую поверхность, верхние части выходили из зажимов в хорошем состоянии. Я сбил выступы рубанком, чтобы получить плоскую поверхность, и пропустил собранные вершины через переносной рейсмусовый станок.
Ширина верхних половин менее 12 дюймов позволила мне использовать эту маленькую машину для наплавки. В какой-то момент в будущем мне может понадобиться отполировать верхнюю часть, и маленький рубанок всегда будет вариантом. Эта стратегия также позволила мне отрезать каждую верхнюю половину по длине с помощью торцовочной пилы с подвижным составом.
Профиль
Столярные изделия на скамейке отличаются по масштабу от столярных изделий для мебели. Детали больше, и акцент делается больше на функциональности и прочности, чем на внешнем виде. Ножки состоят из двух частей, склеенных лицом к лицу, и каждая пара ножек соединена с верхним и нижним подрамниками врезными соединениями.
После разметки мест расположения шипов на подрамниках переносятся линии для обозначения соответствующих пазов на внутренних частях ножек.
Ножки и носилки собраны в блоки, а два конца соединены рельсами, идущими по всей длине скамьи. Крупный размер компонентов позволил найти стыки для разборных соединений на наружных половинах ножек, и эти стыки были вырезаны до ламинирования ножек.
В мебели я использую сквозные шипы, чтобы покрасоваться, но в этой скамье я использовал их, чтобы облегчить жизнь. Врезки вырезаются только во внутренней половине каждой ножки. После разметки соединений я удалил большую часть отходов на сверлильном станке с помощью сверла Форстнера диаметром ¾ дюйма.
Работая над своими новыми столешницами, установленными на коньках, я воспользовался долотом, чтобы выровнять пазы по линиям разметки. Затем я вырезал шипы, чтобы они соответствовали пазам. Я вырезал большую часть плеч вручную, но также вырезал некоторые на настольной пиле, чтобы сравнить методы. Вырезанные вручную плечи были немного аккуратнее, и их изготовление не заняло много времени. После обрезки плеч я удалил отходы вокруг шипов на настольной пиле, используя угловой упор, чтобы направлять доски по набору стопки-дадо.
Небольшая работа долотом очищает пазы до линий макета сверху и снизу. Расширение сторон обеспечивает более легкую посадку и более прочное соединение с добавлением клиньев.
С помощью плечевого рубанка и рашпиля я отрегулировал посадку суставов. После настройки пары до идеальной подгонки, я понял, что могу сделать шипы узкими по ширине, расширить внешнюю часть пазов с помощью быстрого резания долотом, а затем закрепить соединения снаружи клиньями.
Это сэкономило время и укрепило суставы. С заклиненными шипами они не могут вытащить из пазов. Дав клею высохнуть, я обрезал клинья плоскорезной пилой, а затем рубанком.
Большой большой ласточкин хвостЯ думаю, что быстрее вырезать плечи вручную и не настраивать на станке. Это просто вопрос сокращения строк.
Легко представить, что ласточкины хвосты служат декоративным соединением, но есть много практических причин использовать это соединение для соединения концов скамейки вместе. Большая часть нагрузки на скамейку при использовании приходится на край, а клиновидная форма соединений рельса и ноги не может быть разорвана. На самом деле, если вы нажмете на основание этой скамьи с конца, суставы скорее затянутся, чем ослабнут.
Ласточкин хвост также служит для точного размещения и выравнивания деталей во время окончательной сборки. Когда суставы собираются вместе, они подходят туда, где они подходят; невозможно поставить их вместе в неправильном месте.
После изготовления охватываемой части соединения прямо из готовой детали выкладывается раструб. Просто положите рейку на место, выровняйте верхнюю часть и нож по наклонной линии.
И верхнее, и нижнее соединения типа «ласточкин хвост» наполовину заходят внахлест на наружную часть ножки. Нижнее соединение находится на внутренней стороне ноги и представляет собой полуласточкин хвост; другая половина сустава представляет собой съемный клин. Верхний шарнир находится на внешней стороне ноги и закреплен стяжным болтом.
После ручной обрезки плеч я удалил отходы с помощью стопки пазов на настольной пиле и использовал роликовую подставку для поддержки длинных заготовок. Срезы под углом были сделаны электролобзиком.
После установки ласточкина хвоста для нижней направляющей вырезается и устанавливается соответствующий клин. Благодаря работе только с половиной ноги этот процесс полностью виден.
С помощью стамески, плечевого рубанка и рашпиля я зачистил отходы, оставленные пазорезами, затем отметил места расположения гнезд на внешних ножках прямо от хвостовиков. Я обрезал угловые концы раструбов обратной пилой и удалил большую часть отходов между ними на настольной пиле.
Ласточкины хвосты на концах горизонтальных направляющих наполовину перекрыты. Я удалил большую часть материала с помощью стопорной планки, установленной на настольной пиле. Регулируемая роликовая стойка поддерживает другой конец длинных деталей.
Оставшиеся отходы удаляются долотом, а затем плечевым рубанком. Затем я использовал плоскую терку, чтобы добиться плоского дна на этих соединениях. Верхние стыки должны быть одинаковой толщины, чтобы внешние поверхности ножек и поручней были заподлицо при сборке скамейки.
План
Внизу у нижней направляющей конец должен быть тоньше гнезда, чтобы конец направляющей легко проходил через гнездо в стойке. Гнездо также должно быть достаточно широким, чтобы квадратный конец рейки мог войти в узкую часть соединения, а затем опуститься на место.
Деталь ноги
Это требует некоторых усилий, но поскольку внешняя половина ноги на этом этапе ослаблена, легко увидеть, что происходит, при регулировке шарнира. После подгонки нижней части хвоста я вырезал и вставил съемные клинья.
Фасад
Завершив столярные работы, я намазал клей на внутреннюю поверхность и приклеил внешние ножки к ранее собранным внутренним ножкам и подрамникам, следя за тем, чтобы детали были выровнены. После того, как клей высох на ночь, мне не терпелось увидеть готовую скамейку.
Винты, клинья и Отверстие ИсторияНожки прочно собраны путем склеивания. Разумное размещение клея, чтобы он не попал в соединение, и зажим на дне, чтобы детали не скользили, делают процесс безболезненным.
Я поставил готовые концевые блоки на пол и вставил две нижние перекладины в один конец, вбил клинья и вставил перекладины в другой конец. Верхние перекладины были забиты на место, и, отметив центры хвостовиков, я сделал зенковку диаметром ¾ дюйма, достаточно глубокую, чтобы оставить головку стягивающего винта примерно на 1⁄8 дюйма ниже поверхности. Затем я просверлил пилотное отверстие и вкрутил стяжной винт ¼” x 2″. Я установил верхние части на собранное основание так, чтобы края были на одном уровне с внешней стороной ножек и на постоянном расстоянии между ними.
Я просверлил сквозные отверстия диаметром 3⁄8 дюйма в верхних подрамниках и направляющие отверстия диаметром ¼ дюйма в нижней поверхности крышек. Четыре шурупа 5⁄16” x 3 1⁄2” крепят каждую верхнюю секцию к основанию. Полюбовавшись на сборку некоторое время, я положил скамейку на бок, а стыки прижали друг к другу.
Короткая поездка. После сборки реек и верхних половинок скамью переворачивают на бок, чтобы выровнять передние поверхности.
Передняя часть скамейки на самом деле является рабочей опорной поверхностью, поэтому я позаботился о том, чтобы все части находились в одной плоскости. Пока я был на этом, я использовал свой рубанок, чтобы совместить концы хвостов с краями ног.
Установив скамейку на ножки, я наметил расположение тисков, а также отверстия диаметром ¾ дюйма в верхней части, передних направляющих и передних ножках. Двухвинтовые тиски Veritas охватывают левую переднюю ногу, а небольшие быстросъемные тиски находятся в положении хвостовых тисков. Я сделал углубление в конце столешницы для хвостовых тисков и приклеил к основанию два блока толщиной 2 дюйма и шириной 4 ¼ дюйма, чтобы удерживать винты для больших двухвинтовых тисков.
Болты с запаздыванием, крепящие верхние направляющие, раззенкованы для удержания головок глубоко под поверхностью. Торцы реек выполнены заподлицо с ножками.
В верхней части имеется ряд отверстий, центр которых находится в месте упора в концевых тисках. Я начертил линию по всей длине скамьи на этом расстоянии, затем отметил отверстие, чтобы не задеть правую ногу с каждой стороны. Я установил пару разделителей на этом расстоянии и отступил от межцентровых меток для этой линии отверстий.
Я перенес эти метки на передние поручни с помощью угольника. Отверстия в нижней направляющей центрированы по вертикали, а отверстия в верхней направляющей чередуются вверху и внизу, на расстоянии 1¾ дюйма от краев. Отверстия в направляющих не обязательно должны совпадать с отверстиями в верхней части, но это казалось разумным расстоянием. Легче было перенести существующую планировку, чем думать о новой. Отверстия в передней части будут использоваться с поверхностным зажимом или простой собачкой для поддержки работы снизу.
Верхние половинки тяжелые, но с помощью подставки их можно подвести к сверлильному станку для растачивания упорных и крепежных отверстий.
На внутреннем крае верхней части я отметил места для крепежных отверстий по центру 12 дюймов, в 3 дюймах от заднего края передней половины. На задней половине находится еще один ряд отверстий для крепления, также на 12-дюймовых центрах. Я хотел, чтобы они располагались примерно посередине верхней части, но не хотели просверливать линию склеивания, поэтому я расположил их по центру доски за центром задней верхней части.
В передней губке тисков имеется пять отверстий, совпадающих с отверстиями в верхней части, примерно в центре и рядом с каждым концом губки. Каждая из передних ножек также имеет отверстия, два слева, на равном расстоянии между верхней и нижней перекладинами. Отверстия в правой ножке совпадают с дополнительным отверстием в пространстве между верхней направляющей и столешницей.
Поскольку части верстака являются относительно управляемыми компонентами, я разобрал верстак и просверлил все отверстия на сверлильном станке с помощью сверла диаметром 3/4″ на низкой скорости, около 500 об/мин. Я использовал роликовую подставку для поддержки длинных деталей, свисающих со стола сверлильного станка.
Где будут спать хомяки?Между двумя нижними перекладинами находится полка, поддерживаемая планками шириной 2″, прибитыми к нижней части перекладин. Полочные доски произвольной ширины из материала 4/4 с противоположными шпунтами на длинных краях. Доски на каждом конце имеют шпунт только на одном крае и упираются в стык с внутренним краем нижних подрамников.
Полочные доски и планки были оставлены максимально толстыми, а планки также были прибиты к нижней стороне каждого внутреннего края верхних секций для поддержки съемных лотков для инструментов. Лотки представляют собой ящики с открытым верхом, изготовленные из массива дерева толщиной ¾ дюйма. Углы скрепляются простыми шпунтовыми соединениями. Дно имеет шпунт, чтобы соответствовать канавке шириной ¼ дюйма, при этом поверхность дна находится на одном уровне с нижними краями боковых сторон коробки.
Лотки для инструментов при желании можно перевернуть вверх дном, чтобы весь стол или его части превратились в одну широкую плоскую поверхность. Или их можно снять, чтобы можно было прикрепить их к середине столешницы. Их также можно легко носить с собой, чтобы вернуть инструменты домой или в мусорное ведро, чтобы удалить неизбежное скопление стружки и другого мусора.
Я не думаю, что скамья нуждается в чистовой отделке. Выровняв все поверхности, я срезал острые углы кромок и нанес слой датского масла. С помощью нескольких фиксаторов и фиксаторов, а также нескольких зажимов F-типа я могу надежно удерживать работу практически в любом положении. Вот для чего нужна хорошая скамейка. Это инструмент, который делает работу всех других инструментов проще и эффективнее. ШИМ
21-го века Список вырезания Workbench
Нет. ❏ 4 Внутренние опоры 1 15⁄16 x 3 x 31 ОТВЕТЧИК* для золы*, минимум 1¾”
❏ 4 Внешние опоры 1 15⁄16 x 3¾ x 31 Отвод для золы*, 1¾” минимум
❏ 4 Верхние подрамники 1 15 ⁄16 x 2¼ x 31 ЗОЛОПРОВОДНИК *, минимум 1¾”
❏ 4 Нижние носилки 1 15⁄16 x 3¼ x 31 ЗОЛОПРОВОД*, минимум 1¾”
❏ 2 Верхние направляющие 1 15⁄16 x 6 x 65 ЗУ*, минимум 1¾”
❏ 2 Нижние направляющие 1 15⁄16 x 3¾ x 72½ Золорезки*, 1¾” минимум
❏ 4 Клинья 7 ⁄8 x 1 3⁄8 x 8 5⁄8 Ясеневый метчик*, 1¾” минимум
❏ 4 Планки 1 3⁄16 x 2 x 90 Ясень Отрезанный, чтобы поместиться между концами
❏ 8 Стороны ящика ¾ x 3 x 22 ½ Ясень
❏ 8 Торцевые части ящика ¾ x 3 x 6 ¾ Ясень
❏ 4 Дно ящика ¾ x 6 ¾ x 20 ½ Ясень
❏ 1 Полка ¾ x 22 3⁄8 x 58 Ясень Произвольная ширина досок внахлест3
20002 ❏ 1 Блоки для торцевых тисков 2 x 4 ¼ x 30 Ясень Общая длина, отделка для каждой стороны ноги
❏ 1 Торцевые тиски для нарезки 2 ¼ x 7¼ x 30 Ясень Ламинированные из 3-х частей
❏ 1 Хвостовые тиски для нарезки 1 ½ x 3 x 11 5⁄8 Ясень
*TAP=По возможности толстый
Рекомендации по продуктам
Вот некоторые расходные материалы и инструменты, которые необходимы нам в повседневной работе в магазине.
Комплект Kreg Top Trak
48-дюймовый стержневой зажим
Двусторонняя лента
Верстак 21-го века, Избранная статья, Октябрь 2018 г. № 241, Магазинные проекты, Верстак, Верстак
Построить деревообрабатывающий верстак | Jays Custom Creations
Как и большинство других, кто делает проекты из дерева, я много лет хотел прочный, прочный верстак. В моем последнем магазине у меня просто не было места, а в моем нынешнем магазине я несколько раз откладывал его, так как появлялись другие проекты, и я не мог найти достаточно времени, чтобы посвятить его сборке.
Любой может построить этот верстак. Не имеет значения, используете ли вы только ручные инструменты или у вас есть доступ к электроинструментам, чтобы ускорить работу. И материалы вполне доступны. Весь верстак я спроектировал из сосновых досок 2×10. Я использую для этого южную желтую сосну, но на самом деле можно использовать любые породы. Древесина для этого верстака обошлась мне примерно в 110 долларов. Я включил в дизайн три разных тиска, а также шкаф с четырьмя ящиками, но не буду их здесь описывать. В итоге я сделал 20-минутное видео только о самом верстаке, поэтому добавление тисков и шкафа сделало бы его немного длиннее. Я расскажу о них в следующем видео. А пока давайте займемся верстаком.
Для тех, кому интересно, у меня есть 25-страничный подробный набор планов в метрических и имперских единицах внизу этой статьи.
Первое, что нужно построить для верстака, это верх. Верхняя поверхность — единственная поверхность, на которой я хочу убедиться, что она остается без узлов и дефектов… или как можно ближе к этому. Чтобы убедиться, что это произошло, я отсортировал свои доски по краям. Поскольку доски склеены, чтобы сформировать верхнюю часть, края будут видны. Я убедился, что там было по крайней мере полдюйма или около того прозрачного материала, прежде чем увидеть какие-либо узлы. Таким образом, я мог бы сгладить вершину позже, и узел не просвечивал.
Я разработал план так, чтобы почти каждую доску можно было разорвать пополам. Это означает много надрезов не только для верхней части, но и для остальных частей.
Сосна является относительно гибким материалом в зажимах. Так что я был в порядке, просто пропустив строгание всех моих частей, чтобы получить красивые и гладкие поверхности клея. Идеально ровной не было необходимости, поэтому я пропустил фуганок.
Верхняя сборка в конечном итоге будет иметь ширину около 24 дюймов, что на самом деле шире, чем мой рубанок и фуганок вместе взятые, поэтому я решил сделать верхнюю сборку из трех меньших секций. Зажать их и оставить сидеть в конечном итоге заняло больше всего времени.
После того, как все три верхних секции высохли, я воспользовался фуганком, чтобы выровнять поверхность, которая в конечном итоге станет верхом. Я знаю, что не у всех есть фуганок с электроприводом, но то же самое можно сделать с помощью ручного рубанка и небольшого пота.
Я также соединил обе короткие грани под углом 90 градусов относительно уже сплющенной широкой грани. Как правило, вы не будете соединять обе короткие грани, так как вы действительно не сможете держать их параллельно таким образом. Тем не менее, эти короткие лица уже были чертовски плоскими и параллельными, поэтому, если я и убрал их из параллельности, это было ненамного и, конечно, недостаточно, чтобы изменить ситуацию в этом проекте.
Строгальный станок использовался для получения одинаковой толщины трех секций. Я строгал только нижнюю сторону каждой из этих секций, поэтому, если какой-либо строгальный бекас будет очевиден, он будет виден только на нижней поверхности, а не на верхней. На самом деле я был очень доволен тем, как мало бекаса оказалось внизу этих разделов.
Обычно верхнюю часть верстака нужно обрезать после того, как она будет склеена. Я решил отрезать верхние секции по длине перед окончательным склеиванием верха, используя
Далее нужно склеить верхние части в одну сплошную вершину. Если у вас есть столярка для печенья, сейчас самое время ею воспользоваться. Использование печенья будет держать секции выровненными во время склеивания и предотвратит неровную верхнюю поверхность. У меня нет столярного станка для печенья, поэтому я использовал плавающие шипы так же, как и печенье. Затем верх приклеил, зажал зажимами и оставил на ночь.
Закончив верх, я приступил к ногам. Это тот же процесс фрезерования, который начинается с строгания скипов.
Приклеивая ножки, я вспомнил, что у меня есть малярный валик, который, наверное, быстрее нанесет клей. Хотел бы я использовать это для верхних разделов.
После того, как ноги застыли в зажимах, пришло время фрезеровать ноги в обычном режиме. Начните с фуганка, чтобы две стороны были плоскими и перпендикулярными друг другу. Затем рубанок, чтобы выровнять две другие стороны.
Опять же, торцовочная пила используется для обрезки ножек до их окончательной длины.
Ножки крепятся к верхней части с помощью сквозного паза и шипа. Однако шип на конце каждой ножки представляет собой не что иное, как соединение внахлестку. Я хотел сделать свои окончательные разрезы с помощью настольной пилы и пильного диска, но подумал, что на настольной пиле, а также в системе сбора пыли будет проще сначала удалить большую часть разреза на ленточной пиле.
Затем с помощью настольной пилы можно выполнить окончательные проходы, чтобы получить аккуратные и безупречные разрезы.
Разметка пазов довольно проста, если вы начинаете с одного и того же угла как на верхней, так и на нижней поверхности. Для разметки пазов измерения не требуются. С помощью ножки можно получить все необходимые размеры.
Удаление основной части паза можно выполнить с помощью множества различных инструментов. Я выбрал погружной фрезер, так как он довольно быстрый и собирает пыль. Гораздо чище, чем с помощью дрели и сверла Форстнера. Если бы я делал это снаружи на паре козлов, я бы, вероятно, выбрал дрель и сверло Форстнера, так как это, вероятно, было бы быстрее.
После удаления большей части материала с обеих сторон у меня остался очень грубый сквозной паз. Я снял материал свободной рукой, стараясь не приближаться к линиям. Хотя в паре моментов я был довольно близок.
Длинные грани паза можно аккуратно и гладко вырезать с помощью моего погружного фрезера и универсальной направляющей для кромок .
После набора второго длинного торца на погружном фрезере, шипы на ножках плотно прилегают.
Однако торцевые стороны паза нужно было обрезать вручную. Острым зубилом это сделать довольно просто.
На данный момент все ножки подошли идеально. Я подточил короткие грани шипов ножек, чтобы они идеально входили в пазы. Прежде чем зайти слишком далеко, я просверлил отверстие для ножных тисков.
Еще одна склейка. На этот раз носилки. Тот же процесс фрезерования, что и раньше. Пропустить планируют только перед склеиванием.
И снова подрамники обрезаются до необходимой длины на станции торцовочной пилы.
Перед тем, как разрезать соединения внахлест, которые будут связывать все вместе, я правильно отметил начальную линию каждого соединения внахлест, а также сторону удаления линии начала. Я бы не хотел закручивать ноги так далеко.
Сначала полукруги начинаются на носилках.
Я позаботился о том, чтобы полукруги немного укоротились и подкрались, чтобы между ногами была правильная посадка.
Пару раз приходилось подкрадываться к разрезу. Я, конечно, не хотел перебраться и случайно удалить слишком много материала.
Обрезка половин внахлест на ногах — это почти тот же процесс, но требуется немного больше осторожности, чтобы случайно не разрезать не тот сустав на другой стороне ноги.
После того, как была подобрана необходимая ширина для плотного прилегания половины нахлеста, можно было обрезать остальные суставы ног.
У меня нет достаточно длинных хомутов, чтобы должным образом зафиксировать соединения внахлест в продольном направлении верстака, поэтому я решил предварительно просверлить отверстия и использовать винты в качестве зажимов, чтобы удерживать соединения в закрытом состоянии, пока клей высыхает. В видео я сказал, что вернусь позже и заменю винты дубовыми дюбелями, но я думаю, что это совершенно не обязательно.
С основанием всухую с винтами и ножками, сидящими в верхней части, я перевернул верстак на его постоянное место. Ну… во всяком случае, пока навсегда.
Я оставил основание в собранном виде и смог поднять и снять верхнюю часть с шипов ножек, подняв одну сторону и ударив молотком по шипам, повторяя это взад и вперед с обеих сторон. С верхней частью, сидящей поверх шипов ножек, я покрыл внутреннюю часть каждого паза очень большим количеством клея.
Затем снова наденьте верхнюю часть на шипы ножек, пока каждая ножка не войдет в пазы. Затем нужно поднять и опустить каждую сторону, используя гравитацию и вес верхней части, чтобы полностью усадить шипы так, чтобы плечи плотно прилегали к нижней части верхней части верстака.
Я вырезал несколько клиньев на ленточной пиле, чтобы вставить стороны шипов на место. Клей и один клин с каждой стороны каждого шипа действительно фиксируют все.
Следующими были носилки. Эта часть была легкой частью склейки. Просто откручивайте по одной доске, наносите клей и снова прикручивайте.
После того, как клей высохнет на всех стыках, можно использовать торцовочную пилу для зачистки всех длинных полунахлестов, а также сквозных шипов и клиньев в верхней части.