Коррозия металлов и способы защиты от нее
Коррозия – это процесс разрушения металлов и металлических конструкций под воздействием различных факторов окружающей среды – кислорода, влаги, вредных примесей в воздухе. |
Коррозионная стойкость металла зависит от его природы, характера среды и температуры.
- Благородные металлы не подвергаются коррозии из-за химической инертности.
- Металлы Al, Ti, Zn, Cr, Ni имеют плотные газонепроницаемые оксидные плёнки, которые препятствуют коррозии.
- Металлы с рыхлой оксидной плёнкой – Fe, Cu и другие – коррозионно неустойчивы. Особенно сильно ржавеет железо.
Различают химическую и электрохимическую коррозию.
Химическая коррозия сопровождается химическими реакциями. Как правило, химическая коррозия металлов происходит при действии на металл сухих газов, её также называют газовой.![]() |
3Fe + 2O2 = Fe3O4
При химической коррозии также возможны процессы:
Fe + 2HCl → FeCl2 + H2
2Fe + 3Cl2 → 2FeCl3
Как правило, такие процессы протекают в аппаратах химических производств.
Электрохимическая коррозия – это процесс разрушения металла, который сопровождается электрохимическими процессами. Как правило, электрохимическая коррозия протекает в присутствии воды и кислорода, либо в растворах электролитов. |
В таких растворах на поверхности металла возникают процессы переноса электронов от металла к окислителю, которым является либо кислород, либо кислота, содержащаяся в растворе.
При этом электродами являются сам металл (например, железо) и содержащиеся в нем примеси (обычно менее активные металлы, например, олово).
В таком загрязнённом металле идёт перенос электронов от железа к олову, при этом железо (анод) растворяется, т.е. подвергается коррозии:
Fe –2e = Fe 2+
На поверхности олова (катод) идёт процесс восстановления водорода из воды или растворённого кислорода:
2H+ + 2e → H2
O2 + 2H2O + 4e → 4OH–
Например, при контакте железа с оловом в растворе соляной кислоты происходят процессы: |
Анод: Fe –2e → Fe 2+
Катод: 2H+ + 2e → H2
Суммарная реакция: Fe + 2H+ → H2 + Fe2+
Если реакция проходит
Анод: Fe –2e → Fe 2+
Катод: O2 + 2H2O + 4e → 4OH–
Суммарная реакция:
Fe 2+ + 2OH – → Fe(OH)2
4Fe(OH)2 + O2+ 2H2O → 4Fe(OH)3
При этом образуется ржавчина.
Защитные покрытия
Защитные покрытия предотвращают контакт поверхности металла с окислителями.
- Катодное покрытие – покрытие менее активным металлом (защищает металл только неповреждённое покрытие).
- Покрытие краской, лаками, смазками.
- Создание на поверхности некоторых металлов прочной оксидной плёнки химическим путём (анодирование алюминия, кипячение железа в фосфорной кислоте).
Создание сплавов, стойких к коррозии
Физические свойства сплавов могут существенно отличаться от свойств чистых металлов. Добавление некоторых металлов может приводить к повышению коррозионной стойкости сплава. Например, нержавеющая сталь, новые сплавы с большой коррозионной устойчивостью.
Изменение состава среды
Коррозия замедляется при добавлении в среду, окружающую металлическую конструкцию, ингибиторов коррозии. Ингибиторы коррозии — это вещества, подавляющие процессы коррозии.
Электрохимические методы защиты
Протекторная защита: при присоединении к металлической конструкции пластинок из более активного металла – протектора. В результате идёт разрушение протектора, а металлическая конструкция при этом не разрушается.
Понравилось это:
Нравится Загрузка…
Методы и способы защиты от коррозии металлов
Проблема изыскания новых и совершенствование старых способов защиты от коррозии актуальна, как для всей тяжёлой промышленности в целом, так и для автомобильной отрасли в частности.
Еще в XIX веке лучшие инженерные умы того времени волновала проблема защиты металлических конструкций от ржавления. Например, Александр Гюста́в Э́йфель, отец и создатель знаменитой «Tour de 300 mètres», говорил: «Трудно переоценить роль краски в сохранении металлического сооружения, и забота об этом – единственная гарантия его долголетия».
Портрет Александра Гюста́ва Э́йфель и его творение — Эйфелева башня
Кстати, вот уже 131 год эта достопримечательность Парижа противостоит воздействию неблагоприятных факторов окружающей среды именно благодаря краске. Интересный факт – для защиты 200.000 м2 наружной поверхности башни используется около 60 тонн специальной краски. Покраской занимается обслуживающая Эйфелеву башню специально созданная компания «SETE» («Société Nouvelle d’exploitation de la Tour Eiffel»). Весь процесс окраски занимает около 18 месяцев! Вначале, все детали конструкции тщательно осматриваются. Те, на которых слой антикоррозионного покрытия нарушен, – очищаются от старого и покрываются новым. Кроме того, вся поверхность сооружения перед окраской очищается паром высокого давления. Красят башню в два слоя.
Но, окрашивание защищаемой поверхности – всего лишь один из способов защиты металла от коррозии. Применительно к автомобилестроению, все методы защиты можно условно разделить на следующие виды:
2. Изменение характеристик коррозионной среды.
3. Легирование.
4. Электрохимическая защита
5. Рациональное конструирование.
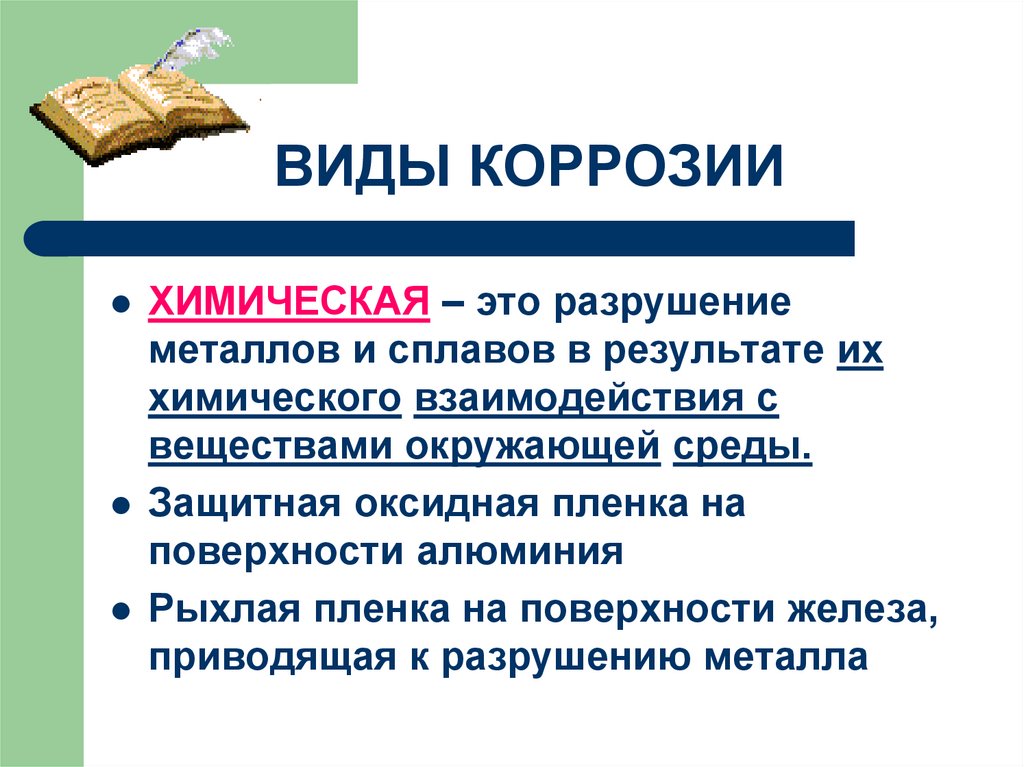
Нанесение защитных покрытий
Нанесение защитных покрытий – один из самых простых, а также исторических старых способов защиты металла от коррозии. Различают металлические и неметаллические покрытия. В свою очередь неметаллические покрытия делят на органические и неорганические.
Органические покрытия – это, привычные нам, лак и краска, а также разнообразные смолы. Сюда же относят полимерные плёнки и резину.
Неорганические покрытия включают в себя разнообразные эмали и грунты на основе соединений кремния, фосфора, цинка и хрома, а также оксидов металлов (например, оксид титана). Классическим примером использования неорганического покрытия в автомобилестроении является процесс фосфатирования автомобильных кузовов. Так, слоем фосфатов перед покраской покрывают кузова автомобилей на заводах Mercedes-Benz.
Металлические покрытия (анодные и катодные) представляют собой нанесённый на защищаемую поверхность слой металла (цинк, хром, кадмий, алюминий и др. ) или металлического сплава (олово, бронза, латунь и т.д.). У анодного покрытия электродный потенциал меньше электродного потенциала защищаемого металла. Поэтому, при повреждении анодного покрытия в первую очередь будет окисляться непосредственно оно само. В случае с катодным металлическим покрытием – наоборот: электродный потенциал покрытия выше потенциала защищаемого металла. Значит, при повреждении такого покрытия первой будет окисляться сама защищаемая поверхность.
Нанесение антикоррозийной защиты Krown
Применительно к автомобилестроению, классическим примером защиты с помощью металлического покрытия является оцинкованный автомобильный кузов. Этот способ получил очень широкое распространение и на сегодняшний день целый ряд автопроизводителей используют цинкование для защиты кузовных деталей. Но, первопроходцем в этом деле стала немецкая компания Audi, впервые применившая оцинковку для защиты кузовов своих автомобилей. Не остановившись на этом, инженеры Audi AG разработали и внедрили в производство двухстороннюю цинковую защиту не только кузовных деталей, но и их сварных соединений, а также и самих кузовов в целом. (Метод т.н. «горячего» цинкования погружением в ванну.) Первым серийным автомобилем с полностью оцинкованным кузовом стал Audi 80 B3, впервые сошедший с конвейера в уже далеком 1986 году.
Процесс цинкования
Изменение характеристик коррозионной среды – суть этого метода защиты заключается в том, что для снижения агрессивности среды в ней уменьшают количество опасных в коррозионном отношении компонентов или же применяют ингибиторы коррозии. (Это специальные вещества, замедляющие её скорость.) И вот, казалось бы, неразрешимая дилемма – как можно снизить количество опасных для стальных деталей автомобиля химических соединений в городской среде? Да очень просто – для начала перестать сыпать на дороги зимой активаторы коррозии, к примеру, тот же хлорид натрия.
Что касается ингибиторов коррозии, то их целесообразно использовать в замкнутых системах (где редко или мало обновляется циркулирующая жидкость). В автомобилестроении типичным примером таковой является система охлаждения двигателя. А все современные антифризы в обязательном порядке содержат в себе ингибиторы коррозии.
Легирование
Легирование (от немецкого legieren – «сплавлять» и от латинского ligare – «связывать») – один из самых эффективных и, одновременно, дорогих способов борьбы со ржавчиной. Суть этого метода заключается в том, что в состав стали добавляют т.н. «легирующие элементы». Таковыми являются некоторые металлы: хром, никель, марганец, ванадий, ниобий, вольфрам, молибден, титан, медь. Данные компоненты придают сплаву пассивность – т.е. при начале коррозии образуются плотные поверхностные продукты реакции, предохраняющие металл от дальнейшего коррозионного разрушения.
Легированные стали, устойчивые к коррозии в атмосфере и агрессивных средах, также называют «нержавеющими сталями», или же, в простонародье, «нержавейкой». Если говорить об её применении в машиностроении, то нужно сказать, что изготовить кузов автомобиля целиком из нержавеющего сплава, конечно же, возможно. Вот только никакой целесообразности в этом нет, ибо цена такой машины будет астрономической. Причина – изначально высокая стоимость коррозионно-стойкой стали. Тем не менее, в автомобилестроении она активно используется. Так, из неё изготавливают детали системы выпуска отработанных газов и термоотражающие экраны.
Электрохимическая защита
Электрохимическая защита автомобиля
Если говорить о методе электрохимической защиты, то, применительно к автомобилестроению, он является малоиспользуемым. Его суть заключается в торможении протекающих при электрохимической коррозии процессов (катодного / анодного). Например, к защищаемому элементу присоединяется деталь из более активного, нежели сам элемент, металла. В образовавшейся гальванической (коррозионной) паре в первую очередь будет разрушаться активный металл (протектор).
А вот метод рационального конструирования, в силу своей относительной простоты и малозатратности, наоборот, получил широкое распространение в машиностроении. Суть его заключается в том, что при проектировании узлов и агрегатов по возможности пытаются уменьшить площадь контакта с агрессивной средой опасных в коррозионном отношении участков деталей (сварных швов и металлических соединений). Если, в силу особенностей конструкции, сделать это не представляется возможным, предусматривают защиту данных узлов от коррозии различными вышеуказанными методами.
Способы защиты металлов от коррозии
Железо и сплавы на его основе подвержены коррозии – разрушению, которое происходит вследствие химического или электрохимического взаимодействия компонентов металлов и сплавов с различными веществами окружающей среды. В результате этих окислительно-восстановительных реакций металлы связываются в оксиды, что приводит к потере их эксплуатационных свойств. Первые проявления разрушительного процесса – образование на поверхности пятен рыжего цвета. Своевременные меры по предотвращению коррозии обеспечивают значительное продление срока службы металлических изделий и конструкций.
Виды коррозии металлов
Коррозионные процессы различаются по характеру разрушения, механизму протекания процесса, типу агрессивной среды, вызывающей коррозию.
Характер разрушения
По этому признаку выделяют следующие типы коррозии:
- Сплошная – равномерная или неравномерная. Затрагивает равномерно всю поверхность металлоизделия или конструкции.
- Местная. Поражаются отельные участки поверхности.
- Питтинг-коррозия (точечная). Поражения – отдельные, глубокие или сквозные.
- Межкристаллитная. Разрушающиеся области располагаются вдоль границ зерен.
Механизм протекания коррозии
Основные типы коррозии – химическая и электрохимическая. Химические коррозионные процессы протекают в результате химреакций, при которых разрушаются металлические связи, а образуются новые – между атомами металла и окислителя. Химическая коррозия возникает при контакте металлов и сплавов со средами, не проводящими электрический ток. Она может быть жидкостной и газовой.
- Газовая коррозия протекает в агрессивных газовых и паровых средах при отсутствии сконденсированной влаги на поверхности металлоизделия или металлоконструкции. Она может стать причиной полного разрушения железа и сплавов на его основе. На поверхности алюминия и алюминиевых сплавов в газовых средах образуется защитная пленка, защищающая их от коррозии. Примеры газов, которые становятся причиной возникновения химических коррозионных процессов: кислород, диоксид серы, сероводород.
- Жидкостная коррозия протекает при контакте металлической поверхности с жидкими неэлектролитами – нефтью и нефтепродуктами.
При наличии даже небольшого количества воды этот химический процесс легко превращается в электрохимический.
Электрохимическая коррозия возникает при контакте металлов и сплавов с жидкостями-электролитами вследствие протекания двух взаимосвязанных процессов:
- анодный – ионы металла переходят в раствор электролита;
- катодный – электроны, которые образовались на стадии анодного этапа, связываются частицами окислителя.
В зависимости от среды, в которой протекают электрохимические коррозионные процессы, различают следующие типы коррозии:
- Атмосферная. Самая распространенная. Протекает в условиях атмосферы или другого влажного газа.
- В растворах электролитов – кислотах, щелочах, солях, обычной воде.
- Почвенная. Скорость процесса зависит от состава грунта. Наименее агрессивны песчаные почвы, наиболее – кислые почвы.
- Аэрационная.
Ее вызывает неравномерный доступ воздушной среды к разным частям изделий и конструкций.
- Биологическая. Ее провоцируют микроорганизмы, которые в результате жизнедеятельности вырабатывают углекислый газ, сероводород и другие газы, вызывающие коррозионные процессы.
- Электрическая. Возникает из-за блуждающих токов, которые появляются при эксплуатации электротранспорта.
Общий вывод! Коррозионные процессы активнее всего развиваются на поверхностях, удобных для отложения пыли, осадков, плохо обдуваемых воздушными струями. Поэтому они подвержены застою воздуха, накоплению и длительному сохранению на поверхности влаги.
Способы защиты металла от коррозии
На стадии производства стали в ее состав могут вводиться легирующие добавки, которые предотвращают появление очагов всех (или некоторых) видов коррозии. Таким элементом является, хром, которого должно быть не менее 13 % от общего количества всех компонентов. Для предотвращения возникновения и развития коррозии в сталях без легирующих добавок используют следующие методы антикоррозионной защиты – конструктивные, пассивные, активные.
Конструктивные
Заключаются в защите поверхности металла с помощью нетонкослойных покрытий – панелей, резиновых прокладок, заслонов. Эти способы имеют мало преимуществ: их сложно, а иногда невозможно реализовать, материалы для конструктивной защиты стоят дорого и после монтажа занимают много места. Их применяют нечасто и только в местах, где они скрыты от глаз.
Пассивные
На металлическое изделие наносится тонкослойное покрытие, которое выполняет чисто барьерные характеристики, то есть процесс защиты заключается в предотвращении контакта металла с наружной средой. Для пассивного способа защиты используют неметаллические покрытия – грунтовки, лаки, краски, эмали. После высыхания они образуют прочную и твердую пленку, имеющую хорошее сцепление с основанием.
Преимущества пассивного способа: невысокая цена и удобное нанесение покрытий, большой ассортимент составов разных цветов и характеристик, создание надежного барьера между металлом и окружающей средой. Недостатки: невысокая устойчивость к механическим повреждениям, необходимость периодически обновлять барьерный слой.
Активные (электрохимические)
Самый распространенный способ создания активной защиты для стальной поверхности – цинкование (горячее, термодиффузионное, гальваническое, холодное). Первые три технологии осуществимы только в производственных условиях. Чаще всего используется горячее цинкование. Стальной листовой прокат цинкуют на непрерывных линиях. Преимущества такого процесса: возможность получать цинковый слой достаточной толщины, высокие автоматизация и производительность процесса. В бытовых условиях применяют только холодное цинкование – нанесение на стальную поверхность цинкнаполненного материала. Обычно холодное цинкование применяют для локального восстановления цинкового покрытия.
Принцип активного защитного действия цинка заключается в том, что он обладает меньшей скоростью коррозии в данной среде, что позволяет ему обеспечить электрохимическую катодную защиту стальной основы. При нанесении на сталь цинкового покрытия цинк с железом образуют гальваническую пару, в которой цинк является более активным металлом. При контакте с влагой и другими коррозионноопасными средами цинк-анод отдает электроны, которые принимает железо-катод, что позволяет ему сохранять свои технические характеристики. Защитный процесс длится до полного исчезновения цинкового слоя.
Плюсы цинкования – долговечность и возможность добавлять цинковый слой в процессе эксплуатации изделий и конструкций. Минусы – необходимость в тщательной подготовке поверхности, обязательное соблюдении технологических правил, сложность утилизации токсичных отходов.
Коррозия. Виды и способы защиты от коррозии
Коррозия – это процесс самопроизвольного разрушения металлов, сплавов и других материалов – бетонов, цементов в результате физико-химического взаимодействия с окружающей средой.
Среда, в которой происходит разрушение металлов, называется коррозионной. Химические соединения, образующиеся в результате коррозии, называются продуктами коррозии. Способность металлов сопротивляться коррозии воздушной среды называется коррозионной стойкостью.
Коррозия материалов является одной из важных мировых проблем. Практика показывает, что только прямые безвозвратные потери металла от коррозии составляют 10…12% всей производимой стали, при этом суммарный ущерб в промышленных странах достигает 4-5% от национального дохода. Ведь корродирует не только черный металл ( сталь, чугун, железо и некоторые его сплавы ), но и бетон, дерево, камень, даже полимеры.
Наиболее интенсивная коррозия наблюдается в зданиях и сооружениях химических производств, что объясняется действием различных газов, жидкостей и мелкодисперсных частиц непосредственно на строительные конструкции, оборудование и сооружения, а также проникновением этих агентов в грунты и действием их на фундаменты. Агрессивному воздействию подвержено до 75% строительного фонда. Коррозия металла приводит к ослаблению конструктива и, как следствие, снижению безопасности эксплуатации сооружений.
По характеру самого процесса коррозию разделяют на две основные группы: химическую и электрохимическую.
Химическая коррозия протекает в не электролитах – жидкостях, не проводящих электрического тока и в сухих газах при высокой температуре.
Электрохимическая коррозия происходит в электролитах и во влажных газах и характеризуется наличием двух параллельно идущих процессов: окислительного (растворение металлов) и восстановительного (выделение металла из раствора).
По внешнему виду коррозию различают: пятнами, язвами, точками, внутрикристаллитную, подповерхностную.
По характеру коррозионной среды различают следующие основные виды коррозии: газовую, атмосферную, жидкостную и почвенную.
Газовая коррозия происходит при отсутствии конденсации влаги на поверхности. На практике такой вид коррозии встречается при эксплуатации металлов при повышенных температурах.
Атмосферная коррозия относится к наиболее распространенному виду электрохимической коррозии, так как большинство металлических конструкций эксплуатируются в атмосферных условиях. Коррозия, протекающая в условиях любого влажного газа, также может быть отнесена к атмосферной коррозии.
Жидкостная коррозия в зависимости от жидкой среды бывает кислотная, щелочная, солевая, морская и речная. По условиям воздействия жидкости на поверхность металла эти виды коррозии получают добавочные характеристики : с полным и переменным погружением, капельная, струйная. Кроме того, по характеру разрушения различают коррозию равномерную и неравномерную.
По степени воздействия на металлы коррозионные среды делятся на неагрессивные, слабоагрессивные, среднеагрессивные и сильноагрессивные.
В атмосферных условиях железо и сталь подвергаются общей равномерной коррозии.
- коррозия в растворах электролитов – жидкостях, проводящих электрический ток;
- почвенная или подземная коррозия металлических сооружений, находящихся под землей;
- биологическая коррозия – это коррозия, протекающая под влиянием жизнедеятельности микроорганизмов.
По видам дополнительных воздействий различают следующие случаи коррозии:
- электрокоррозия под действием внешнего источника тока, т.
е. коррозия изделий, находящихся под землей, вызванная блуждающими токами;
- контактная коррозия металлов – разрушение металла в растворе электролита вследствие контакта с другим металлом, имеющим более положительный электродный потенциал, чем потенциал основного металла.
- радиационная коррозия – это процессы коррозии в условиях радиоактивного облучения;
- коррозия в условиях механического воздействия.
Наиболее типичными видами подобного разрушения являются коррозионные растрескивание, усталость, кавитация, эрозия и фреттинг-коррозия
Бетон и железобетон находят широкое применение в качестве конструкционного материала при строительстве зданий и сооружений химических производств. Но они не обладают достаточной химической стойкостью против действия кислых сред. Свойства бетона и его стойкость в первую очередь зависит от химического состава цемента из которого он изготовлен.
Наибольшее применение в конструкциях и оборудовании находят бетоны на портландцементе. Причиной пониженной химической стойкости бетона к действию минеральных и органических кислот является наличие свободной гидроокиси кальция (до 20%), трехкальциевого алюмината (3CaO×Al2O3) и других гидратированных соединений кальция.
Коррозия бетона происходит тем интенсивнее, чем выше концентрация водных растворов кислот. При повышенных температурах агрессивной среды коррозия бетонов ускоряется. Несколько более высокой кислотостойкостью обладает бетон, изготовленный на глиноземистом цементе, из-за пониженного содержания оксида кальция.
Кислотостойкость бетонов на цементах с повышенным содержанием оксида кальция в некоторой степени зависит от плотности бетона. При большей плотности бетона кислоты оказывают на него несколько меньшее воздействие из-за трудности проникновения агрессивной среды внутрь материала.
Щелочестойкость бетонов определяется главным образом химическим составом вяжущих, на которых они изготовлены, а также щелочестойкостью мелких и крупных заполнителей.
Увеличение срока службы строительных конструкций и оборудования достигается путем правильного выбора материала с учетом его стойкости к агрессивным средам, действующим в производственных условиях. Кроме того, необходимо принимать меры профилактического характера.
К таким мерам относятся:
- герметизация производственной аппаратуры и трубопроводов, хорошая вентиляция помещения, улавливание газообразных и пылевидных продуктов, выделяющихся в процессе производства;
- правильная эксплуатация различных сливных устройств, исключающая возможность проникновения в почву агрессивных веществ;
- применение гидроизолирующих устройств и др.
Непосредственная защита металлов от коррозии осуществляется нанесением на их поверхность неметаллических и металлических покрытий либо изменением химического состава металлов в поверхностных слоях:
- оксидированием,
- азотированием,
- фосфатированием.
Для защиты поверхностей от коррозии существуют разнообразные покрытия:
- лакокрасочные (антистатичные и армированные, полиуретановые, акриловые, порошковые эпоксидно – полиэфирные, органосиликатные и кремнийорганические),
- металлизационные с цинком, алюминием, медью и комбинациями этих металлов.
Это краски, лаки, эмали, тонкодисперсные порошки, пленки.
Лакокрасочные покрытия вследствие экономичности, удобства и простоты нанесения, хорошей стойкости к действию промышленных агрессивных газов нашли широкое применение для защиты металлических и железобетонных конструкций от коррозии.
Защитные свойства лакокрасочного покрытия в значительной степени обуславливаются механическими и химическими свойствами, сцеплением пленки с защищаемой поверхностью.
Лакокрасочные материалы в зависимости от назначения и условий эксплуатации делятся на десять групп:
- А – покрытия стойкие на открытом воздухе;
- АН – то же, под навесом;
- П – то же, в помещении;
- Х – химически стойкие;
- Т – термостойкие;
- М – маслостойкие;
- В – водостойкие;
- ХК – кислотостойкие;
- ХЩ – щелочестойкие;
- Б – бензостойкие.
Наиболее распространены в промышленности покрытия металлические, неметаллические (органического и неорганического происхождения), а также покрытия, образованные в результате химической и электрохимической обработки металла.
Выбор вида покрытия зависит от условий, в которых используется защищаемое изделие (перепад температур, повышенная влажность, морская или пресная вода, щелочь, кислота, соли металлов, радиация, электроток и огонь), и технологичность возможностей формирования покрытия.
Наиболее часто применяемые способы защиты металлов:
- легирование;
- электрохимическая защита;
- покрытие металлами;
- защитные пленки.
Легирование – это введение в металл на стадии его производства определенного количества специальных добавок, например – хрома или марганца. Это придает сталям особые свойства, необходимые для использования в сложных условиях. Для возведения современных зданий, особенно повышенной этажности, необходима высококачественная атмосферостойкая легированная сталь, например, погодоустойчивая марка COR-TEN. Такой материал позволяет решить проблемы эксплуатации сооружений даже в экстремальных климатических условиях.
Одними из самых популярных и относительно недорогих мер защиты от коррозии сегодня являются методы, изменяющие химический состав металла в поверхностных слоях. Как правило, это электрохимические способы нанесения покрытий на металл. Наиболее известный процесс называется оцинковкой, которая в зависимости от способа обработки металла делится на горячую и холодную.
В первом случае обрабатываемый материал погружается в специальную ванну. Затем под воздействием переменного тока осуществляется его обработка в растворе фосфата цинка при плотности тока 4 А/дм², напряжении 20 В и температуре 600-700ºС. В результате электрохимической реакции образуется ферроцинковый сплав. При применении второго способа на подготовленную поверхность стального листа наносится защитный слой из цинка. Оцинковка толщиной 0,3 мм позволяет обеспечить защиту обработанной поверхности металла более чем на 30 лет.
Итальянская фирма «Metalnastri» разработала метод, сочетающий в себе качество горячего и технологичность холодного цинкования. Это простая идея наклейки цинковой фольги на стальную поверхность. Высокую антикоррозийность создает сплошной цинковый слой, а токопроводящие клеевые композиции обеспечивают и электрохимическую защиту поверхности.
ЦНИИПСК им. А.П. Мельникова предложил метод термодиффузионного цинкования (ТДЦ) метизных и малогабаритных изделий из стали и чугуна. Метод заключается в нагреве металлоизделий в среде, содержащей порошок цинка. В результате на поверхности изделия образуется цинковое покрытие с хорошими защитными и декоративными свойствами.
Технологический процесс такого цинкования экологически чист и практически безотходен. В качестве сырья используются отечественные материалы, не требующие специальной обработки. ТДЦпокрытие обладает высокой адгезией и износостойкостью, обеспечиваемой в результате взаимной диффузии железа и цинка. Срок службы покрытия в 1,5-4 раза больше по сравнению с традиционными цинковыми покрытия.
Широкое распространение цинковых покрытий обусловлено их хорошими химическими свойствами. Для стали (катод) цинк является анодом, за счет этого образуется гальваническая пара, имеющая высокие защитные свойства, хорошо сохраняемые даже при малой толщине слоя. Скорость разрушения цинкового покрытия составляет примерно 1-10 мкм в год в зависимости от различных факторов. Оцинковка может осуществляться совместно с другими металлами – с добавлением алюминия (Al) или железа (Fe). В настоящее время в России широко используется сталь Galfan c цинкоалюминиевым покрытием и сталь Galvannealed с цинкожелезным покрытием.
При покрытии другими металлами в зависимости от вида коррозии покрывающий слой наносят различными способами. В качестве покрывающего материала часто используется хром или никель. Хромирование – электролитическое нанесение покрытия из хрома на поверхность металлического изделия. Никелирование, также нанесение на поверхность изделий никеля толщиной от 2 до 50 мкм.
На практике обычно применяются следующие методы:
- Погружение изделий в расплавленный металл (горячий способ). Заключается в том, что изделия погружают в ванну с расплавленным металлом или же нагретую поверхность деталей обволакивают расплавленным металлом.
- Метод термической диффузии. Основан на диффузии (проникновении) в поверхностные слои деталей присадок при высокой температуре.
Диффузионные покрытия наносятся при нагреве деталей в твердой (порошкообразной), жидкой или газообразной фазе металла.
- Металлизация. Заключается в нанесении (распылении) на поверхность деталей слоя присадок расплавленного металла с помощью пульверизаторов.
- Контактный метод осаждения металла. Осуществляется без применения внешнего источника тока за счет вытеснения менее благородными металлами более благородных из растворов их солей. Толщина таких покрытий невелика и защитные свойства их невысоки.
Следует отметить, что металлические покрытия достаточно хорошо защищают металл от коррозии. Однако при нарушении защитного слоя она может протекать даже более интенсивно, чем без покрытия. Поэтому в промышленности для улучшения свойств металлических поверхностей, обработанных электротехническим методом, используется способ нанесения защитных покрытий из полимерных материалов. Такие продукты получили широкое распространение в строительной индустрии.
Использование полимерных материалов для антикоррозионной защиты обусловлено их уникальными физико-химическими показателями. Полимеры имеют небольшой удельный вес, высокую стойкость к не механическим воздействиям (соприкосновение с водой, солями, щелочами или кислотами). Обладают пластичностью и светостойкостью. В настоящее время наибольшее распространение получили « трехслойные» продукты с двойным уровнем защиты.
Первый уровень – непосредственно оцинковка, второй – полимер. Благодаря такой структуре сталь становится стойкой к воздействию агрессивных сред, механическим повреждениям и ультрафиолетовому изучению. Срок их службы составляет порядка 50 лет, в зависимости от качества и толщины покрытия. Необходимо также учесть, что высокие эксплуатационные характеристики таких материалов напрямую зависят от качества оцинковки исходного металла, а потребительские качества – от применяемого в составе полимера.
Альтернативой полимерным материалам являются конструкционные пластмассы и стеклопластики, получаемые на основе различных синтетических смол и стекловолокнистых наполнителей. В настоящее время выпускается значительный ассортимент материалов, особое место среди них занимает полиэтилен. Он инертен во многих кислотах, щелочах и растворителях, а также имеет высокую теплостойкость.
Другим направлением использования полиэтилена в качестве химически стойкого материала является порошковое напыление. Применение полиэтиленовых покрытий объясняется их дешевизной и хорошими защитными свойствами. Покрытия легко наносятся на поверхность различными способами, в том числе пневматическим и электростатическим распылением.
Защитные пленки. Способ заключается в нанесении на металл защитной оболочки из различных компонентов в следующей последовательности: шпатлевка, грунтовка, краска, лак или эмаль.
Для противокоррозионной защиты конструкций зданий и сооружений (ферм, ригелей, балок, колонн, стеновых панелей), а также наружных и внутренних поверхностей емкостного технологического оборудования, трубопроводов, газоводов, воздуховодов вентиляционных систем, которые в процессе эксплуатации не подвергаются механическим воздействиям абразивных частиц, применяют лакокрасочные покрытия. Такие покрытия наиболее эффективны для защиты от атмосферной коррозии. Однако срок службы лакокрасочных покрытий невелик и составляет 4-5 лет. Для повышения коррозионной стойкости лакокрасочных покрытий используют различные противокоррозионные пигменты.
Следует назвать антикоррозионные пигменты фирмы SNCZ (Франция): фосфаты цинка; модифицированные фосфаты цинка; фосфаты, не содержащие цинк; полифосфаты; феррит кальция, а также тетраоксихромат цинка; хроматы стронция, цинка, бария.
Наиболее часто используются фосфаты цинка PZ 20 и PZ W2 в большинстве лакокрасочных систем: органоразбавляемых, водоразбавляемых, воздушной и горячей сушки.
Там, где нельзя использовать противокоррозионные пигменты, содержащие цинк (контакт с пищевыми продуктами), используются пигменты на основе щелочеземельных фосфатов Новинокс РАТ 30, Новинокс РАТ 15 и Новинокс РС01.
Металлоконструкции, подвергающиеся воздействию соляного тумана, могут быть защищены лакокрасочными материалами, содержащими фосфат щелочеземельных металлов. Фосфат щелочеземельных металлов – нетоксичный пигмент, что повышает экологичность лакокрасочного покрытия и увеличивает сферу его применения.
Тетраоксихромат цинка ТС 20, хромат стронция L203E и хромат цинка CZ20 – применяются в лакокрасочных материалах, использующихся в авиационных, судовых покрытиях, а также в составе адгезивов для легких сплавов.
Для защитных покрытий, эксплуатирующихся в условиях высоких температур (до 600ºС), используются хромат бария М 20 и феррит кальция FC 71. Применение феррита кальция для защитных покрытий – новое направление в лакокрасочных материалах. В табл. 1 представлена стойкость различных лакокрасочных материалов (ЛКМ) к агрессивным средам.
Таблица 1. Стойкость лакокрасочных материалов
ЛКМ, по типу связующего | Стойкость к агрессивным средам | |||||||
Вода | Водяной пар | Растворители | Разбавленные растворители | Кислоты | Разбавленные кислоты | Щелочи | Разбавленные щелочи | |
Винилхлоридные | + | ++ | ± | ± | ± | + | ± | + |
Хлоркаучуковые | + | ++ | ± | ± | ± | + | ± | + |
Акриловые | ± | ++ | ± | ± | ± | + | ± | + |
Алкидные | ± | + | ± | + | ± | ± | ± | ± |
Битумные | ++ | ++ | ± | ± | ± | ± | ± | + |
ПУ ароматические | ± | ++ | + | ++ | + | + | ± | ± |
ПУ алифатические | + | ++ | ± | + | ± | + | ± | ++ |
Эпоксиднополиуретановые | ++ | ++ | ± | ± | ± | + | + | ++ |
Эпоксидные | ++ | ++ | + | ++ | ± | + | ++ | ++ |
Цинк-силикатные | + | ++ | ++ | ++ | + | + | + | + |
Перхлорвиниловые | ++ | ++ | ± | ± | ± | ± | ± | + |
Примечания: ++ отлично, + хорошо, ± удовлетворитльно
Наиболее распространенным способом защиты от коррозии строительных конструкций, сооружений и оборудования является использование неметаллических химически стойких материалов: кислотоупорной керамики, жидких резиновых смесей, листовых и пленочных полимерных материалов (винипласта, поливинилхлорида, полиэтилена, резины), лакокрасочных материалов, синтетических смол и др.
Для правильного использования неметаллических химически стойких материалов необходимо знать не только их химическую стойкость, но и физико-химические свойства, обеспечивающие условия совместной работы покрытия и защищаемой поверхности. При использовании комбинированных защитных покрытий, состоящих из органического подслоя и футеровочного покрытия, важным является обеспечение на подслое температуры, не превышающей максимальной для данного вида подслоя.
Для листовых и пленочных полимерных материалов необходимо знать величину их адгезии с защищаемой поверхностью. Ряд неметаллических химически стойких материалов, широко используемых в противокоррозионной технике, содержит в своем составе агрессивные соединения, которые при непосредственном контакте с поверхностью металла или бетона могут вызвать образование побочных продуктов коррозии, что, в свою очередь, снизит величину их адгезии с защищаемой поверхностью. Эти особенности необходимо учитывать при использовании того или иного материала для создания надежного противокоррозионного покрытия.
Просмотров: 7 083
защита металла от коррозии, коррозия железа и стали, алюминия, чугуна, корозия метал
Обеспечение долговечности конструкций — понятие, включающее в себя как технологические, так и конструктивные требования.
Защита металла от коррозии — одна из главных проблем в решении этого вопроса. Под влиянием разрушительных атмосферных воздействий и агрессивных сред металлические конструкции постепенно утрачивают первоначальный внешний вид и теряют свои качества. В таких случаях очень остро встаёт вопрос о защите металла от коррозии.
Коррозия металла
Коррозией называется разрушение поверхности металлов под влиянием химического и электрохимического воздействия внешней среды. Коррозия разъедает металл, делая непригодным его дальнейшее использование и эксплуатацию. С течением времени это приводит к снижению прочности, а в ряде случаев и к разрушению металлических изделий.
Быстрота коррозионных процессов зависит от условий, в которых изготовляются и эксплуатируются изделия. Поскольку устранить атмосферное воздействие на металлические конструкции практически невозможно, то и коррозию следует признать вечным спутником металла. Процесс коррозии включает в себя четыре основных элемента. Это – катод (или электрод, на котором происходит катодная реакция), анод (или электрод, на котором происходит анодная реакция), проводник электронов (металл, проводящий электрический ток) и проводник ионов (проводящая электрический ток жидкость или электролит).
Электроды (катод и анод) являются электронными проводниками, которые соприкасаются с проводниками ионов. В проводнике ионов (электролит) возникает соответствующий электродный потенциал или электродное напряжение. Когда электроды соприкасаются между собой, то разность между электродными потенциалами действует как возбудитель коррозионной реакции. В результате образуется коррозионная пара, в которой один из электродов (анод) и разъедает металл. Все меры по защите металла от коррозии направлены на то, чтобы ослабить или не допустить образования коррозионных пар.
Важнейшим способом защиты металла от коррозии является покраска поверхности металлов специальными антикоррозионными составами.
Есть ли защита от коррозии?
Для любых металлических конструкций и условий их эксплуатации наиболее простым и доступным способом защиты от коррозии является применение специальных лакокрасочных материалов для металла.
Лакокрасочные покрытия имеют ряд преимуществ по сравнению с другими видами защитных покрытий:
• простота нанесения составов;
• возможность получения покрытия любого цвета;
• возможность обработки металлоконструкций больших габаритов и сложной конфигурации;
• дешевизна по сравнению с другими видами защитных покрытий.
Долговечность защиты металла от коррозии зависит от типа и вида применяемого лакокрасочного материала. Кроме этого, срок службы металла зависит от тщательности подготовки поверхности металла под окраску.
Защита металла от коррозии
Существует множество различных состояний поверхности металла, требующих защиты от коррозии. Возраст объекта и его расположение, качество поверхности, степень разрушения металла, количество дефектов, тип предыдущих и будущих агрессивных условий, свойства старого покрытия — все эти факторы влияют на подготовку поверхности и выбор системы защиты металла от коррозии.
Компания КрасКо предлагает целую серию лакокрасочных материалов, специально предназначенных для защиты металла от коррозии.
Нержамет — краска по ржавчине, антикоррозионная эмаль «три в одном». Эмаль наносится прямо на ржавчину. Предназначается для окраски как чистых, так и ржавых металлических поверхностей, ржавого металла.
Полимерон — износостойкая спецэмаль, антикоррозионное покрытие. Эмаль специально разработана для защиты металлических поверхностей в условиях тяжёлой промышленной атмосферы.
Сереброл — алюминиевая краска, серебристо-белая антикоррозионная эмаль. Применяется для окраски любых металлоконструкций, эксплуатирующихся во влажной атмосфере, в условиях морской и пресной воды.
Нержалюкс — антикоррозионная эмаль для цветных металлов. Применяется для окраски алюминиевых и оцинкованных поверхностей, любых других поверхностей из цветных металлов.
Цикроль — краска для крыш, краска по оцинковке. Краска применяется для окраски оцинкованной кровли, оцинкованного металла, кровельного железа, кровельной жести, металлочерепицы, водостоков, желобов, перил и других оцинкованных поверхностей.
Нержапласт — эмаль жидкая пластмасса. Образует на поверхности декоративное покрытие с эффектом пластика (жидкий пластик).
Молотекс — кузнечная краска, декоративная краска с рисунчато-молотковым эффектом.
Полиуретол — маслобензостойкая грунт-эмаль, полиуретановая двухкомпонентная эмаль.
Фосфогрунт — фосфатирование металла, антикоррозионный грунт для чёрных и цветных металлов.
Цинконол — цинконаполненный грунт, антикоррозионный грунт-протектор. Холодное цинкование металла.
Фосфомет — преобразователь ржавчины, фосфатирующий модификатор ржавчины.
Грункор — антикоррозионный быстросохнущий грунт по металлу (с фосфатом цинка).
Выбор системы защиты от коррозии
Выбор схемы защиты металла от коррозии (включая марку ЛКМ, количество наносимых слоёв и общую толщину покрытия) следует осуществлять с учётом климатических условий конкретного региона, характеристики среды эксплуатации металлической конструкции, а также с учётом условий при нанесении материала и технико-экономической эффективности данного ЛКМ. Декоративные свойства (внешний вид) системы антикоррозионной защиты определяется финишным (верхним) слоем.
Антикоррозионная защита металла и металлоконструкций — на сайте krasko.ru.
На сайте представлено множество разделов, посвященных защите металлов от коррозии (коррозия металла, коррозия железа и стали, коррозия чугуна и алюминия), которые помогут Вам осуществить правильный выбор системы защиты металла и антикоррозионного покрытия.
Специалисты Компании КрасКо внимательно выслушают все Ваши требования и подберут оптимальный вариант системы для защиты металла от коррозии на Вашем объекте.
Коррозия металлов и защита от коррозии
Коррозия металлов
Коррозия — это разрушение металла под действием окружающей среды.
По механизму протекания различают два типа коррозии — химическую и электрохимическую.
Химическая коррозия начинает влиять на металл сначала его происхождения. Окалина ее продукт. Взаимодействие металла и окружающей среды протекает постоянно, химические процессы, проходящие при этом взаимодействии можно назвать борьбой за выживание, наша задача свести потери металла в этой борьбе к минимуму.
По характеру агрессивной среды различают атмосферную коррозию, подземную и подводную.
Виды коррозионных разрушений разнообразны — равномерная коррозия, неравномерная, коррозия пятнами, коррозия язвами, подповерхностная коррозия, точечная или питтинговая, структурно-избирательная коррозия, межкристаллитная коррозия (этот самый опасный вид коррозии, обусловленный сложностью выявления). Последствия скрытно протекающих коррозионных процессов зачастую приводят к авариям, которых могло бы и не быть.
Химическая коррозия — это процесс разрушения металла под действием внешней среды, не сопровождаемая образованием электрического тока. Ее разновидность — газовая коррозия, представляет собой процесс взаимодействия газов при высокой температуре с металлом. При таком взаимодействии образуется оксидная пленка, на железе она рыхлая, легко отскакивает и не защищает от разрушения. В отличии от химической — электрохимическая коррозия протекает при контакте металла с раствором электролита. При этом электролитом может являться любая жидкость или газ. Примером электрохимической коррозии может быть атмосферная коррозия.
Электрохимическая коррозия, более трудно прогнозируемая, чем химическая, ввиду необходимости учёта множества факторов, зачастую изменяющихся в процессе эксплуатации ТУ. При этом скорость протекания процессов электрохимической коррозии на порядок больше чем при химической коррозии. В одних случаях на поверхности металла может образоваться плотная оксидная пленка, выполняющая роль защитного слоя. Образовавшаяся оксидная пленка предохраняет металл от разрушения. Это явление широко используется в современной технике, как способ защиты от коррозионных процессов.
Защита от коррозии
Существует немало способов защиты от коррозии. Самый лучший из них создание такого металла, который бы вообще не коррозировал. Один из путей создания коррозионностойкого металла — получение особых сплавов, в которые добавляют хром, никель, молибден, титан и другие компоненты. Так называемое легирование. Технология создания таких сплавов трудоемка, и связана с повышенными экономическими затратами. Цена таких материалов выше и не всегда целесообразно применение их в конкретных условиях.
Ингибирование — способ, при котором скорость коррозии снижается, если в агрессивную среду ввести соединения, значительно замедляющие коррозионный процесс. Одним из механизмов ингибирования является адсорбция ингибитора на поверхности защищаемого изделия. Ингибируемые бумаги и пленки применяются при долговременном хранении.
Различают металлические и неметаллические защитные покрытия, изолирующие металл от агрессивной среды. Большие детали или трубы защищают методом металлизации.
Плакирование — метод защиты металла от коррозии другим металлом, который устойчив к агрессивной среде. Трубы газо- и нефтепроводов защищаются комбинированным способом, мазутно-битумное покрытие, ингибированная бумага и одновременно с этим катодная защита.
Сущность электрозащиты состоит в том что, на катод, которым является сам трубопровод, накачиваются электроны от внешнего источника тока, и это тормозит коррозию. Анодом в этом случае может служить любой ненужный металл.
Так же широко сейчас применяются различные плёнки на основе полиэтилена, внутренняя поверхность так же защищается различными покрытиями на основе керамики.
Сварные стыки также защищаются от взаимодействия с перекачиваемой средой различными способами. При защите ТУ применяется метод протекторной защиты. Протектор — активный металл, с более отрицательным потенциалом, например цинк, который разрушаясь сам, защищает объект.
Надежным способом зашиты от коррозии, являются гальванические покрытия, которые получают электролизом в водных растворах.
Неметаллические покрытия — это покрытия лаками, красками, различными силикатными эмалями и полимерными материалами. Покрытие силикатными эмалями широко применяется в химической промышленности. Кислотостойкие эмали применяют для покрытия вакуумных аппаратов, резервуаров, реакторов. Затраты на защиту металла от коррозии оправданы и дают хороший экономический эффект, с учётом снижения затрат на замену непригодного ТУ. Где то, например подземные трубопроводы с агрессивной средой, она просто необходима для безопасной эксплуатации.
При проведении экспертизы промышленной безопасности технических устройств, применяемых на опасных производственных объектах, одной из важнейших задач является определение скорости коррозии и прогнозирование этой скорости на планируемый период эксплуатации. Мероприятия по антикоррозионной защите могут значительно увеличить срок эксплуатации и, как следствие, снизить затраты на замену ТУ.
Получение и свойства коррозионно-стойких покрытий из эпоксидной эмульсии, модифицированной полиуретаном на водной основе
Введение
Коррозия — это процесс, при котором материалы, особенно металлы (например, углеродистая сталь, оцинкованная сталь и чугун), изнашиваются электрохимическим и химические действия. Металлы имеют анодную и катодную области, а коррозия возникает в присутствии кислорода, воды и проводящей среды. Влияние коррозии металла на безопасность эксплуатации и надежность продукции может привести к потере ценных продуктов, крупным авариям, гибели персонала и остановке производства, поэтому последствия коррозии металлических конструкций огромны. Нанесение покрытий является наиболее широко используемым методом защиты от коррозии из-за желаемого преимущества замедления проникновения воды, ионов и других агрессивных сред через органическую пленку, а также простоты нанесения.
Большинство современных антикоррозионных покрытий представляют собой покрытия на основе растворителей. В последнее десятилетие водорастворимые покрытия привлекли внимание для защиты металлов, поскольку требования экологических стандартов устанавливают ограничения на удаление или контроль летучих органических соединений до минимально возможных уровней (Wang et al., 2013; Abdolahi et al., 2014; Yilmaz et al., 2014; Liu et al., 2016; Zhang et al., 2017).
Однако антикоррозионные свойства покрытий на водной основе значительно уступают покрытиям на основе растворителя, поскольку гидрофильные группы часто сохраняются в покрытии в процессе формирования пленки, что снижает способность защиты к диффузии пара и влагостойкость (Ai et al., 2014; Ван З. и др. , 2014; Рахман и др., 2015). Таким образом, добавление ингибиторов коррозии или наполнителей необходимо для повышения коррозионной стойкости покрытий на водной основе, а микро/нано неорганические частицы (т. е. неорганические добавки) часто применяются в качестве ингибиторов коррозии или наполнителей (Hao et al., 2012; Ma и др., 2012b; Чик и др., 2013; Лян и др., 2013; Сулейман и др., 2014; Дас и др., 2017).
Многие неорганические частицы, включающие графен (Mittal, 2014; Kausar et al., 2016; Qiu et al., 2017; Shahabadi et al., 2017; Zhu et al., 2017), Ni-Fe(Ti,W) Нанокомпозит C (Khorsand et al., 2018), нано-ZnO (Dhoke and Khanna, 2009; Rasool et al., 2018), SiO 2 (Khademian et al., 2015; Wang N. et al., 2016) , TiO 2 (Montesinos et al., 2015; Wang N. et al., 2016), Al (Deflorian et al., 2011), Al 2 O 3 (Chen et al., 2014), Исследователи исследовали Ag (Rahman, 2017), слюдяной оксид железа (Kakaei et al., 2013) и углеродные нанотрубки (Zhuo et al. , 2016), и результаты показывают, что коррозионная стойкость композитных покрытий значительно улучшилась. .
Композитное покрытие состоит из органических полимеров и неорганических добавок. Полимеры действуют как матрица и удерживают неорганические добавки. Полимеры на водной основе используются из-за их популярности в составах покрытий, включая акрил (Singh et al., 2017), полиуретан (PU) (Alagi et al., 2017), алкид (Pathan and Ahmad, 2013), эпоксидная смола (Cao et al., 2015), полиэстер (Kumar et al., 2017) и их комбинации из-за их дополнительных характеристик.
Водоразбавляемые органо-неорганические гибридные покрытия станут тенденцией развития в будущем (Boubakri et al., 2010; Huang et al., 2012). Однако из-за добавления неорганических добавок некоторые свойства (например, прозрачность и т. д.) композиционных покрытий явно снижаются, а применение покрытий ограничивается в некоторых специальных областях, требующих высокой прозрачности и демонстрирующих естественные цвета подложка, покрытая покрытиями. Поэтому необходимы исследования и разработка антикоррозионного покрытия без неорганических добавок.
Среди различных полимеров на водной основе, используемых в покрытиях, полиуретан известен своей превосходной долговечностью и устойчивостью, главным образом, к химическому и термическому разложению, ультрафиолетовому (УФ) излучению, царапинам и гидрофобности (Boubakri et al., 2010; Huang et al., 2012). ; Ма и др., 2013; Мохаммад и Хан, 2015; Каусар, 2016).
Эпоксидные смолы, благодаря своим превосходным химическим свойствам, коррозионной стойкости, выдающимся адгезионным свойствам, низкой усадке и низкой цене, широко используются в различных покрытиях. Кроме того, свойства отвержденного эпоксидного покрытия зависят от отвердителя и процесса отверждения, и эти свойства можно широко регулировать (Muhammad et al., 2014; Pradhan et al., 2016; Kumar et al., 2017). Однако из-за низкой стойкости эпоксидных смол на открытом воздухе, акриловые и полиуретановые гибриды находят все большее применение.
При воздействии агрессивных сред стабильность металла или сплава зависит от защитных свойств образующихся покрытий поверхности. Химический состав, электропроводность, адгезия, растворимость, гигроскопичность и морфологические характеристики определяют способность пленки работать в качестве антикоррозионного барьера (Stratmant et al., 1983). Если полиуретановые и эпоксидные сегменты синтезированы в молекуле полимера, свойства (то есть химический состав, адгезия, гигроскопичность и морфологические характеристики) смолы могут регулироваться в широких пределах. Следовательно, коррозионная стойкость полимера может быть улучшена.
В ходе этого исследования была приготовлена и охарактеризована водоразбавляемая эмульсия модифицированной полиуретаном эпоксидной смолы (WPUME), которая показала хорошие свойства коррозионной стойкости.
Материалы и методы
Материалы
Эпоксидная смола (Е-44) была приобретена у компании Lanxing Advanced Material Co. (Уси, Китай). Изофорондиизоцианат (IPDI), диметилолмасляная кислота (DMBA), триэтиламин (TEA), ацетон, бутанон и полиэтиленгликоль 2000 (PEG-2000) были приобретены у Kelong Co. (Чэнду, Китай). Катализатор с оловоорганическим (т.е. дилаурат дибутилолова) в качестве основного активного ингредиента, названный DY-20, был продуктом Deyin Chemical Co. (Шанхай, Китай). Отвердитель на водной основе с модифицированным первичным амином в качестве основного активного ингредиента, названный GCA 02, был приобретен у BASF Co. Активный водородный эквивалент GC 02 составляет 320. Все материалы были аналитической чистоты, кроме эпоксидной смолы, отвердителя и ДЯ-20. ИФДИ, ДМБА и ПЭГ-2000 высушивали в вакуумной печи (100°С) не менее 5 ч перед экспериментом, а остальные материалы наносили без дополнительной обработки.
Получение эпоксидной эмульсии, модифицированной полиуретаном
Эмульсию эпоксидной смолы, модифицированной полиуретаном, синтезировали реакцией с использованием IPDI, PEG, DMBA, эпоксидной смолы и TEA. В четырехгорлой круглодонной колбе растворяли 5 г ДМБА в 10 г ацетона, колбу снабжали термометром, мешалкой, вводом сухого азота, холодильником и нагревательной рубашкой. Затем медленно добавляли 15 г ИФДИ и 5 г ацетона при умеренном перемешивании (300 об/мин) и смеси давали реагировать при 70°С до тех пор, пока не было достигнуто теоретическое содержание NCO. Изменение содержания NCO в ходе реакции определяли стандартным методом обратного титрования дибутиламина (David and Staley, 19).69). После получения теоретического значения NCO реагент нагревали до 90°C, добавляли раствор (т.е. 41,8 г эпоксидной смолы, 37,1 г ПЭГ-2000, 0,3 г DY-20 и 40 г ацетона) и перемешивали при 300 об/мин в течение 2,5 ч при поддержании температуры 90°С. Затем реагент охлаждали до 40°С, медленно добавляли 3,5 г ТЭА и перемешивали в течение 30 мин, поддерживая температуру на уровне 40°С. По окончании реакции в колбу добавляли 120 г деионизированной воды при быстром перемешивании (800 об/мин) при комнатной температуре в течение 15 мин.
Наконец, ацетон удаляли в вакууме, чтобы получить эмульсию смолы WPUME. Молекула WPUME содержала гидрофильные группы (т. е. карбоксилатную группу и эфирную связь) и эпоксидную группу, поэтому она могла самоэмульгироваться (т. е. в зависимости от карбоксильной группы и эфирной связи) в воде с образованием стабильной эмульсии. Эмульсия отверждалась в стабильную пленку в зависимости от реакции между эпоксидной группой и аминогруппой в GC 02. Схема процесса приготовления ВЭМЭ показана на схеме 1, основные функциональные группы обведены кружками.
Схема 1 . Процесс приготовления молекулы WPUME. (A) Реакция между IPDI и DMBA. (B) Реакция между форполимером, эпоксидной смолой и ПЭГ-2000. (C) Взаимодействие карбоновой кислоты и ТЭА.
Приготовление отвержденной и чистой пленки WPUME
Около 100 г эмульсии WPUME хорошо перемешали с 7,5 г отвердителя (т. Процесс отверждения осуществляли при 120°С в течение 15 минут, а затем при 140°С в течение 15 минут для формирования пленки. Другая поверхность листа белой жести была отлита для формирования дополнительной литой пленки. Спиральным микрометром измеряли толщину полученных пленок 15–25 мкм. Реакция отверждения происходила между эпоксидной группой в молекуле WPUME и аминогруппой в GC 02, и реакция показана на схеме 2.
Схема 2 . Реакция отверждения между WPUME и отвердителем GC 02.
Поскольку была приготовлена исходная пленка, отвердитель в эмульсию не добавлялся, и все остальные процедуры были такими же, как и при приготовлении отвержденной пленки.
Водостойкость
Испытание на водонепроницаемость характеризовалось скоростью водопоглощения и определялось методом взвешивания следующим образом (Ma et al., 2012a). Образцы отвержденной пленки ВЭМЭ были разрезаны на кусочки размером 3 см × 3 см и высушены в вакуумной печи при 60°С в течение 24 ч для определения их сухой массы (W д ). Затем пленку погружали в дистиллированную воду на 72 ч, после чего стирали с поверхности воду кусочком фильтровальной бумаги для определения ее массы (W t ). Затем по формуле (1) рассчитывали степень водопоглощения (вес.%).
W(%)=Wt-WdWd×100 (1)
Стабильность эмульсии
Стабильность при хранении
Образец эмульсии помещали в закрытую стеклянную бутылку объемом 50 мл и помещали в печь на 20 ч при 50 ± 2°С. Затем бутылку вынимали из печи и помещали при комнатной температуре (т.е. 23 ± 2°С) на 3 часа. Если эмульсия не расслаивалась, стабильность была хорошей.
Стабильность при замораживании и оттаивании
Образец эмульсии замерзал при -10°C и помещался при комнатной температуре (т.е. 23 ± 2°C) на некоторое время, пока замороженная эмульсия не оттаивала. Если образец не расслаивался, процесс циклов замораживания-оттаивания продолжался до тех пор, пока не было проведено пять циклов для завершения теста на устойчивость к замораживанию-оттаиванию.
Стабильность при центрифугировании
Образец эмульсии центрифугировали при 5000 об/мин в течение 5 мин на центрифуге (TGK-16, Xiangyi Co. , Китай). Если эмульсия не расслаивалась, стабильность была хорошей.
Характеристика
FTIR
Инфракрасные Фурье-спектры исходного и отвержденного образца пленки регистрировали соответственно в диапазоне 400–4000 см −1 с использованием FTIR-спектрометра (VERTEX 70, BRUKER Co., Германия) ) на диске KBr при разрешении 4 см -1 за 32 скана.
Содержание твердых веществ
Образец эмульсии весом 2 г был взвешен точно для получения веса W 1 , а затем эмульсия была высушена до постоянного веса для получения веса W 2 , а содержание твердого вещества (sc%) рассчитывали по формуле (2).
sc(%)=W1-W2W1×100 (2)
Размер частиц и дисперсия эмульсии
Для определения размера частиц и дисперсии использовали оборудование для лазерного рассеяния (Autosizer, Melvern Co., UK). Образец сначала разбавляли дистиллированной водой до 0,5%, а затем обрабатывали ультразвуковой волной для гомогенизации эмульсии.
Микроскопическое исследование
Микроскопическое исследование проводили на просвечивающем электронном микроскопе (TEM, JEM-200CX, Japan Electronics Co., Япония), работающем при напряжении 120 кВ. Чтобы увидеть морфологию, первоначальную пленку смывали со слюдяных подложек в дистиллированную воду и собирали на сетках ПЭМ.
Термогравиметрический анализ
Термогравиметрический анализ (ТГА) проводили на термическом анализаторе (STA 449 F3, NETZSCH Co., Германия). Прибор ТГА калибровали оксалатом кальция от 30 до 500°С при скорости нагрева 10°С/мин в статической атмосфере азота.
Электрохимические измерения
Электрохимические измерения отвержденных и исходных пленок WPUME на жести (покрытие было отполировано наждачной бумагой перед нанесением пленки) проводили с использованием потенциостата ParStat 2273 (Ametec, Berwyn, PA, USA). Применялась классическая трехэлектродная система. Образцы, насыщенный каломельный электрод (НКЭ) и платиновая пластина, использовались в качестве рабочего электрода, электрода сравнения и вспомогательного электрода соответственно. Поляризационные кривые были получены на площади облучения 1 см 2 при постоянной скорости сканирования напряжения 0,5 мВ с −1 после начальной задержки 300 с. Испытание на погружение проводили согласно GB 10124-88 Китая (GB 10124-88, 2008). Электрохимические измерения проводились в растворе NaCl 3,5%.
Испытание на коррозию в солевом тумане
Испытание на коррозию в солевом тумане YW/R-150 (Тяньцзинь, Китай) проводили на листах белой жести с отвержденным образцом WPUME для имитации коррозии в окружающей среде в соответствии со стандартом ASTM B117-09.(испытание в естественном солевом тумане).
Испытание на гибкость
Эмульсию WPUME отверждали на белой жести, а гибкость образцов тестировали в соответствии со стандартом ASTM 4145-2010 (гибкость покрытия).
Результаты и обсуждение
Химическая характеристика
Исследование методом ИК-Фурье-спектроскопии было выполнено для структурного сравнения между отвержденными и исходными пленками, которые были приготовлены с помощью эмульсии WPUME (рис. 1). В целом, не было существенной структурной разницы между спектрами отвержденной и исходной пленки.
Рисунок 1 . Инфракрасные спектры с преобразованием Фурье исходной и отвержденной пленки, приготовленной с помощью эмульсии WPUME.
FTIR-спектр исходной пленки показал полосу поглощения при 3406 см -1 и пики поглощения при 1718 и 1250 см -1 , соответствующие характеристическому поглощению NH, C = O и CO в -NH -COO- соответственно. Не было обнаружено пика поглощения при 2270 см -1 (т.е. пик поглощения -NCO), что означает, что -NCO почти полностью реагирует с -ОН в реагенте. Анализ этих спектров выявляет пики поглощения при 1400 и 1107 см -1 , что можно отнести к характерному поглощению -ОН в первичной спиртовой и эфирной связи соответственно. Это означает, что ПЭГ индуцируется в сегменте полимерной цепи, и остается некоторое количество первичного спирта. Результаты характеристического пика при 955 см -1 относятся к поглощению -СООН, что означает, что ДМБА реагирует с другими материалами, и -СООН индуцируется в сегменте полимерной цепи. Гидрофильные группы (т.е. эфирная связь и карбоксильная группа) в молекуле WPUME обеспечивают хорошую стабильность эмульсии. Характерные пики поглощения эпоксидной группы при 913 и 830 см -1 легко обнаруживаются в исходном образце пленки, что означает, что эпоксидная группа сохраняется и позже может привести к реакции отверждения. Эти ИК-спектры показывают, что реакция синтеза ДМБА, ИФДИ, ПЭГ и эпоксидной смолы для синтеза ВПМЭ может происходить в соответствии со схемой 1.
Что касается спектра образца отвержденной пленки на рисунке 1, пик поглощения группа, первичный гидроксил и -COOH при 913, 1400 и 955 см -1 соответственно исчезают, и появляется новый банк поглощения третичной аминогруппы при 1125 см -1 , что означает, что отвердитель (т.е. модифицированный амин) может реагировать с кислородной группой, а эпоксидная группа может реагировать с активным амином, так что может образовываться аминогруппа. Исчезновение эпоксидной группы, первичного гидроксила и -COOH означает, что реакция отверждения проходит тщательно, и отвержденная пленка может обладать хорошими свойствами коррозионной стойкости, низкой скоростью водопоглощения и хорошей термостойкостью; поэтому свойства хорошо согласуются с результатами более поздних исследований.
Содержание сухого вещества
Содержание твердого вещества в эмульсии, приготовленной обычным способом, составляло 44,5%, что хорошо соответствует теоретическому значению (т.е. 46%). Разница может быть связана с улетучиванием материалов в реакции.
Водонепроницаемость
Все прозрачные образцы исходных и отвержденных пленок были погружены в дистиллированную воду для определения их водонепроницаемости. Прозрачная нетронутая пленка WPUME становилась белой, а затем непрозрачной после того, как ее погружали в дистиллированную воду примерно на 30 минут при комнатной температуре, и она постепенно распадалась на мелкие кусочки в течение примерно 2 часов. Однако отвержденная пленка ВПМЭ не претерпела видимых изменений даже после погружения ее в дистиллированную воду на 72 ч при комнатной температуре. Средняя скорость водопоглощения составила 2,8%, что было рассчитано по формуле (1). Низкий показатель водопоглощения свидетельствует о том, что отвержденная пленка не чувствительна к воде и обладает хорошей водостойкостью.
Размер частиц и дисперсия эмульсии
На рис. 2 показаны размер частиц и дисперсия WPUME. Видно, что средний размер частиц эмульсии составляет 102,82 нм, что хорошо согласуется с данными ПЭМ. Небольшой размер частиц эмульсии приводит к хорошей стабильности эмульсии.
Рисунок 2 . Размер частиц и дисперсность образца эмульсии.
Стабильность
Эмульсия WPUME демонстрирует хорошую стабильность (т.е. стабильность при хранении, стабильность при замораживании и оттаивании, стабильность при центрифугировании). Стабильность можно объяснить введением гидрофильных групп в полимерную цепь ВПМЭ и малым размером частиц эмульсии.
Микроскопическое наблюдение
Типичные ПЭМ-изображения частиц эмульсии ВЭМЭ представлены на рис. 3. Установлено, что частицы имеют правильную сферическую форму диаметром 100–200 нм и имеют некоторые регулярные границы. Морфология частиц представляет собой приблизительную структуру ядро-оболочка, в которой гидрофильные группы (т. е. карбоксильная группа и эфирная связь) составляют оболочку, а гидрофобный компонент составляет ядро. Инкапсулированный гидрофильной группой исходный гидрофобный сегмент полимерной цепи диспергирован в воде. Структура ядро-оболочка становится более заметной, когда частицы увеличиваются до больших размеров, как показано на рисунке 3b.
Рисунок 3 . ПЭМ-изображения образцов эмульсии с разным увеличением (т.е. 2500× в a и 5000× в b ).
Термический гравиметрический анализ
Результаты ТГА исходных и отвержденных образцов пленки WPUME показаны на рис. 4. Температуры соответствуют потерям веса 5, 10, 20, 50 и 80%, которые перечислены в таблице 1.
Рисунок 4 . ТГА отвердевает исходные и отвержденные пленки WPUME.
Таблица 1 . Данные о тепловых потерях для образцов WPUME.
Основная потеря массы образцов обусловлена термическим разложением сегмента молекулы полимера. При добавлении отвердителя отвержденный образец пленки WPUME демонстрирует лучшую термостойкость, чем нетронутый образец. Для типичных образцов температура, соответствующая 5%-ной потере веса исходной и отвержденной пленки, составляет 270 и 335°С соответственно, что на 65°С выше для образца отвержденной пленки, чем исходного. Отверждение и образование поперечных связей между полимерными цепями ограничивают свободное движение полимеров (Charles and Carraher, 2007), поэтому отвержденная пленка WPUME демонстрирует лучшую термостойкость. Лучшее термическое сопротивление указывает на то, что полимерные цепи образца WPUME сшиты и эффективно отверждены. Отвержденная пленка WPUME может обеспечить относительно более высокие свойства коррозионной стойкости, что подтверждается в следующем разделе.
Электрохимические измерения
Поляризационные кривые отвержденных и исходных пленок на полированных жести показаны на рис. 5. На рис. 5 видно, что скорость выделения водорода на катодной стороне и скорость растворения металла на анодной стороне уменьшаются. значительно, поскольку отвержденная пленка нанесена на подложку по сравнению с исходной пленкой. Кроме того, анодные стороны двух кривых также различны. Анодная сторона образца с нетронутой пленкой гораздо более гладкая, чем у отвержденного. На кривой отвержденного пленочного образца плотность тока коррозии (J) увеличивается значительно медленнее с ростом анодного потенциала в области пассивной тенденции. Плотность тока коррозии образца, покрытого отвержденной пленкой, составляет 0,002551 мкА·см -2 , что намного ниже, чем у образца, покрытого исходной пленкой (1,905 мкА см -2 ). Результат показывает, что белая жесть с отвержденной пленкой может значительно улучшить коррозионную стойкость подложки по сравнению с исходной.
Рисунок 5 . Поляризационные кривые отвержденных и исходных пленок, нанесенных на полированные белые жести.
Испытание в солевом тумане
На рис. 6 показаны фотографии образца WPUME, отвержденного на листах белой жести после разного времени воздействия (0, 30, 60 и 65 дней) в камере с нейтральным солевым туманом соответственно.
Рисунок 6 . Образцы подвергали испытанию на коррозию в солевом тумане через 0, 30, 60 и 65 дней.
До испытаний в солевом тумане коррозии не наблюдается. Изображения на рисунке 6 после 30, 60 и 65 дней воздействия показывают наличие коррозионной активности. Вблизи царапин на образцах наблюдается желтая ржавчина и вздутие покрытия, что свидетельствует о коррозионном поражении. Однако на изображении образца после 30 дней воздействия не видно образования пузырей, и нет признаков явного локального коррозионного воздействия. Возле царапин образца после 60 и 65 сут выдержки наблюдаются блистеры покрытия диаметром около 1 мм и более 1 мм, что свидетельствует о хороших антикоррозионных характеристиках ВЭМЭ покрытия, полученного в ходе исследования. Тем не менее, некоторые предыдущие покрытия на водной основе могут выдерживать испытание в нейтральном солевом тумане около 480 часов (Wang et al., 2014), 720 часов (Li et al., 2018), 600 часов (Wang N. et al., 2016) и 288 ч (Чжан и др. , 2019 г.).) и т. д. до появления локальной коррозии, которые все намного короче, чем образцы, приготовленные в этом исследовании.
Испытание на гибкость
Гибкость подготовленного покрытия изгибается до диаметра 2 мм, что является наивысшей гибкостью согласно ASTM 4145-2010.
Выводы
Эмульсия WPUME была успешно приготовлена с помощью реакции эпоксидной смолы (E-44), IPDI, DMBA, оловоорганического катализатора и PEG-2000, и отвердитель для образования коррозионно-стойкого покрытия мог отверждать эмульсию. Покрытие обладает хорошей гибкостью (т. е. может изгибаться до диаметра 2 мм) и свойствами коррозионной стойкости (т. е. может выдерживать испытание на коррозию в солевом тумане в течение примерно 60 дней на листах белой жести). Покрытие имеет множество потенциальных применений в некоторых специальных областях, требующих высокой гибкости и коррозионной стойкости.
Доступность данных
Необработанные данные, подтверждающие выводы этой рукописи, будут предоставлены авторами без неоправданных оговорок любому квалифицированному исследователю.
Вклад авторов
Все перечисленные авторы внесли существенный, непосредственный и интеллектуальный вклад в работу и одобрили ее для публикации.
Финансирование
Работа выполнена при финансовой поддержке Сычуаньской научно-технической программы (№ 2019JDTD0024 и № 2019).ZHCG0048), проект военной и гражданской интеграции провинции Сычуань (№ zyf-2018-089), Ибинская научно-техническая программа (№ 2018YG05 и № 2017YG02), проект Чунхуэй Министерства образования Китая (№ Z2017066), Научно-исследовательский фонд Департамента образования Сычуани, Китай (№ 18ZA0445), и Программа ученых Сихуа Университета Сихуа.
Заявление о конфликте интересов
JM работал в компании North Sichuan Nitrocellular Co., Ltd.
Остальные авторы заявляют, что исследование проводилось в отсутствие каких-либо коммерческих или финансовых отношений, которые могли бы быть истолкованы как потенциальный конфликт интересов.
Ссылки
Абдолахи Э., Ибрагим З. и Хашим С. (2014). Применение экологически чистых покрытий для подавления микробной коррозии (MIC) стали: обзор. Полим. Ред. 54, 702–745. doi: 10.1080/15583724.2014.946188
CrossRef Полный текст | Академия Google
Ай, Л., Лю, Ю., Чжан, X., Оуян, X., и Ге, З. (2014). Упрощенный и безтемплатный метод получения политиофеновых микросфер и их диспергирования для водоразбавляемых антикоррозионных покрытий. Синтез. Встретились. 191, 41–46. doi: 10.1016/j.synthmet.2014.02.004
CrossRef Полный текст | Google Scholar
Алаги П., Горпаде Р., Чой Ю., Патил У., Ким И., Байк Дж. и др. (2017). Полиолы на основе диоксида углерода как устойчивое сырье термопластичного полиуретана для антикоррозионного покрытия металлов. Поддержание ACS. хим. англ. 5, 3871–3881. doi: 10.1021/acssuschemeng.6b03046
Полный текст CrossRef | Google Scholar
Бубакри А., Гермази Н., Эллеуч К. и Айеди Х. (2010). Исследование УФ-старения термопластичного полиуретанового материала. Мат. науч. англ. А 527, 1649–1654. doi: 10.1016/j.msea.2010.01.014
CrossRef Полный текст | Google Scholar
Цао, М., Ван, Х., Цай, Р., Гэ, К., Цзян, С., Чжай, Л., и др. (2015). Приготовление и свойства эпоксидно-модифицированного тунгового масла изоляционного лака на водной основе. J. Appl. Полим. науч. 132:42755. doi: 10.1002/app.42755
Полный текст CrossRef | Google Scholar
Чарльз Э. и Каррахер Дж. (2007). Химия полимеров Сеймура/Каррахера . 7-е изд. Нью-Йорк, штат Нью-Йорк: Марсель Деккер Пресс.
Google Scholar
Чик Дж., Стил А., Байер И. и Лот Э. (2013). Устойчивость к подводному насыщению и электролитическая функциональность для супергидрофобных нанокомпозитов. Коллоидный полимер. науч. 291, 2013–2016 гг. дои: 10.1007/s00396-013-2933-x
Полнотекстовая перекрестная ссылка | Google Scholar
Чен X., Юань Дж., Хуан Дж., Рен К., Лю Ю., Лу С. и др. (2014). Крупномасштабное производство супергидрофобных покрытий из полиуретана/нано-Al2O3 методом суспензионного газопламенного напыления для защиты от коррозии. Заяв. Серф. науч. 311, 864–869. doi: 10.1016/j.apsusc.2014.05.186
CrossRef Полный текст | Google Scholar
Дас С., Панди П., Моханти С. и Наяк С. (2017). Взгляд на полиуретан и нанокомпозиты на основе касторового масла: последние тенденции и развитие. Полим. Пласт. Технол. 56, 1556–1585. doi: 10.1080/03602559.2017.1280685
CrossRef Full Text | Google Scholar
Дэвид, Д. Дж., и Стейли, Х. Б. (1969). «High Polymer Series», в Analytical Chemistry of Polyurethans , Vol. 16 (Нью-Йорк, штат Нью-Йорк: Wiley Interscience Press, 45–46.
Дефлориан, Ф., Росси, С., и Федель, М. (2011). Алюминиевые компоненты для морского применения, защищенные от коррозии циклами нанесения органических покрытий с низкой воздействие на окружающую среду Коррос. англ. науч. Технол. 46, 237–244. doi: 10.1179/147842209X12489567719545
CrossRef Full Text | Google Scholar
Дхок С. и Кханна А. (2009). Изучение электрохимического поведения алкидных покрытий на водной основе, модифицированных нано-ZnO. J. Appl. Полим. науч. 113, 2232–2237. doi: 10.1002/app.30276
Полный текст CrossRef | Google Scholar
GB 10124-88 (2008). Стандартная практика лабораторных испытаний металлов на коррозию погружением. Пекин: Управление по стандартизации Китайской Народной Республики.
Хао Ю., Лю Ф. и Хань Э. (2012). Механические и барьерные свойства композиционных покрытий на основе эпоксидной смолы/ультракоротких стеклянных волокон. Дж. Матер. науч. Технол. 28, 1077–1084. doi: 10.1016/S1005-0302(12)60176-5
CrossRef Full Text | Google Scholar
Хуан Т., Ван Ю., Се К. и Лин Дж. (2012). Дисперсия гибридов фосфазен-глина на молекулярном уровне в полиуретане и синергетическое влияние на термостойкость и устойчивость к ультрафиолетовому излучению. Полимер 53, 4060–4068. doi: 10.1016/j.polymer.2012.07.049
CrossRef Полный текст | Google Scholar
Какаи М., Данаи И. и Заарей Д. (2013). Исследование защиты от коррозии неорганическими антикоррозионными покрытиями, содержащими слюдистый оксид железа и цинковую пыль. Коррос. англ. науч. Технол. 48, 194–198. doi: 10.1179/1743278212Y.0000000060
CrossRef Full Text | Google Scholar
Каусар, А. (2016). Композитные пленки полиамид/фуллерен с полиуретановым покрытием на водной основе: механические, термические и воспламеняемые свойства. Междунар. Дж. Полим. Анальный. Характер. 21, 275–285. doi: 10.1080/1023666X.2016.1147729
CrossRef Полный текст | Google Scholar
Каусар А., Рафик И., Анвар З. и Мухаммад Б. (2016). Перспективы композита эпоксид/оксид графена: важные особенности и технические применения. Полим. Пласт. Технол. 55, 704–722. doi: 10.1080/03602559.2015.1098700
CrossRef Full Text | Google Scholar
Хадемян М., Эйсазаде Х., Шакери А. и Горбани М. (2015). Эффект ГПЦ-ПАНИ/SiO 2 Эмульсионный нанокомпозит в поли(винилацетате) для антикоррозионных покрытий. Полим. Пласт. Технол. 54, 1051–1056. doi: 10.1080/03602559.2014.986801
CrossRef Полный текст | Google Scholar
Хорсанд С. , Карбаси М., Сайедан Ф., Эшагян М. и Разави М. (2018). Разработка электроосаждаемых нанокомпозитных покрытий Ni-Fe (Ti, W) C. Прибой. англ. 34, 433–439. doi: 10.1080/02670844.2017.1370880
CrossRef Full Text | Академия Google
Кумар С., Кришнан С., Самал С., Моханти С. и Наяк С. (2017). Итаконовая кислота, используемая в качестве универсального строительного блока для синтеза смол и полиэфиров на основе возобновляемых ресурсов для будущих перспектив: обзор. Полим. Междунар. 66, 1349–1363. doi: 10.1002/pi.5399
CrossRef Full Text | Google Scholar
Li, J., Li, X., Zhu, K., Wang, H., and Fei, G. (2018). Влияние фосфорилированного оксида графена на антикоррозионные свойства водоразбавляемых акрилатно-эпоксидных покрытий. Дж. Макромоль. науч. А 55, 649–657. doi: 10.1080/10601325.2018.1504611
CrossRef Full Text | Google Scholar
Лян Ю., Лю Ф., Не М., Чжао С., Линь Дж. и Хань Э. (2013). Влияние концентратов нано-Al на коррозионную стойкость эпоксидных покрытий. Дж. Матер. науч. Технол. 29, 353–358. doi: 10.1016/j.jmst.2013.01.014
CrossRef Полный текст | Google Scholar
Лю С., Гу Л., Чжао Х., Чен Дж. и Ю Х. (2016). Коррозионная стойкость эпоксидных покрытий на водной основе, армированных графеном. Дж. Матер. науч. Технол. 32, 425–431. doi: 10.1016/j.jmst.2015.12.017
CrossRef Полный текст | Google Scholar
Ма, К., Сюй, Л., Сюй, В. и Чжан, Г. (2013). Разлагаемый полиуретан для защиты от биологического обрастания на море. Дж. Матер. хим. Б 1, 3099–3106. doi: 10.1039/c3tb20454e
CrossRef Полный текст | Google Scholar
Ма С., Сонг Г. и Фэн Н. (2012a). Получение и характеристика самоэмульгированной нитроцеллюлозы на водной основе. Углевод. Полим. 89, 36–40. doi: 10.1016/j.carbpol.2012.02.029
PubMed Abstract | Полный текст перекрестной ссылки | Google Scholar
Ма С., Сун Г., Фэн Н. и Чжао П. (2012b). Защита от коррозии низкоуглеродистой стали нановолокнистыми покрытиями на основе полианилина. J. Appl. Полим. науч. 125, 1601–1605. doi: 10.1002/app.35643
Полный текст CrossRef | Google Scholar
Миттал, В. (2014). Функциональные полимерные нанокомпозиты с графеном: обзор. Макромоль. Матер. англ. 299, 906–931. doi: 10.1002/mame.201300394
Полный текст CrossRef | Google Scholar
Мохаммад М. и Хан Д. (2015). Композит на водной основе полиуретан/масляная летучая зола: новый экологически безопасный материал покрытия. J. Прилипатели. науч. Технол. 29, 2709–2718. doi: 10.1080/01694243.2015.1087252
CrossRef Полный текст | Google Scholar
Монтесинос Р., Рейносо Р., Альварес Ф. и Васкес К. (2015). Оценка новых покрытий на водной основе, полученных из композитных латексных частиц и армированных TiO 2 нанотрубки. Полим. Пласт. Технол. 54, 730–740. doi: 10.1080/03602559.2014.974273
CrossRef Полный текст | Google Scholar
Мухаммад Р., Мохаммад Д. и Саидатул С. (2014). Разработка полимеров на основе растительных масел. J. Appl. Полим. науч. 131, 1–13. doi: 10.1002/app.40787
Полный текст CrossRef | Google Scholar
Патан С. и Ахмад С. (2013). Алкид на водной основе, модифицированный s-триазиновым кольцом: синтез, характеристика, антибактериальные и электрохимические исследования коррозии. Поддержание ACS. хим. англ. 1, 1246–1257. doi: 10.1021/sc4001077
Полный текст CrossRef | Google Scholar
Прадхан С., Панди П., Моханти С. и Наяк С. (2016). Взгляд на химию эпоксидной смолы и ее отверждение для нанесения покрытий: подробное исследование и перспективы на будущее. Полим. Пласт. Технол. 55, 862–877. doi: 10.1080/03602559.2015.1103269
CrossRef Full Text | Google Scholar
Цю С., Ли В., Чжэн В., Чжао Х. и Ван Л. (2017). Синергический эффект интеркалированного полипирролом графена для усиления защиты от коррозии водного покрытия в 3,5% растворе NaCl. Приложение ACS Матер. Интерфейсы 9, 34294–34304. doi: 10.1021/acsami.7b08325
PubMed Abstract | Полный текст перекрестной ссылки | Google Scholar
Рахман, М. (2017). Улучшение антимикробных и барьерных свойств водоразбавляемых полиуретанов, содержащих наночастицы гидроксиапатита и серебра. J. Прилипатели. науч. Технол. 31, 613–626. doi: 10.1080/01694243.2016.1228744
CrossRef Полный текст | Google Scholar
Рахман О., Кашиф М. и Ахмад С. (2015). Наноферритные дисперсные эпоксидно-акрилатные покрытия на водной основе: антикоррозионные нанокомпозитные покрытия. Прогр. Орг. Пальто. 80, 77–86. doi: 10.1016/j.porgcoat.2014.11.023
CrossRef Полный текст | Google Scholar
Расул К., Насралла Г., Юнес Н., Пандей Р., Рашид П. и Махмуд К. (2018). «Зеленые» наночастицы хитозана, связанные ZnO, для эффективного ингибирования сульфатредуцирующих бактерий в закачиваемой морской воде. ACS Sustain. хим. англ. 6, 3896–3906. doi: 10.1021/acssuschemeng.7b04248
Полный текст CrossRef | Google Scholar
Шахабади С., Конг Дж. и Лу Х. (2017). Только водный, зеленый путь к самовосстанавливающимся, устойчивым к ультрафиолетовому излучению и электропроводящим нанокомпозитным покрытиям из полиуретана/графена/лигнина. Поддержание ACS. хим. англ. 5, 3148–3157. doi: 10.1021/acssuschemeng.6b02941
Полный текст CrossRef | Google Scholar
Сингх А., Алам С. и Рани Н. (2017). Приготовление и характеристика водоразбавляемого акрило-полиуретанового покрытия на оцинкованной стали. Пер. Инст. Встретились. Заканчивать. 95, 165–172. doi: 10.1080/00202967.2017.1237759
CrossRef Полный текст | Google Scholar
Стратмант М., Боненкамп К. и Энгелл Х. Дж. (1983). Электрохимическое исследование фазовых переходов в слоях ржавчины. Коррос. науч. 23, 969–985. doi: 10.1016/0010-938X(83)
-0
CrossRef Full Text | Google Scholar
Сулейман Р., Халед М., Ван Х., Смит Т., Гиттенс Дж., Акид Р. и др. (2014). Сравнение выбранных систем золь-гелевых покрытий, легированных ингибиторами, для защиты низкоуглеродистой стали. Коррос. англ. науч. Технол. 49, 189–196. doi: 10.1179/1743278213Y.0000000113
CrossRef Full Text | Академия Google
Ван Н. , Фу В., Сунь М., Чжан Дж. и Фанг К. (2016). Влияние разноструктурных частиц TiO 2 на антикоррозионные свойства водоразбавляемых эпоксидных покрытий. Коррос. англ. науч. Технол. 51, 365–372. doi: 10.1080/1478422X.2015.1117267
CrossRef Full Text | Google Scholar
Ван Н., Ву Ю., Ченг К. и Чжан Дж. (2014). Исследование антикоррозионных свойств полианилин-мезопористого композита МС-41 в новом эпоксидном покрытии на водной основе. Матер. Коррос. 65, 968–976. doi: 10.1002/maco.201307458
CrossRef Полный текст | Google Scholar
Ван, X., Ван, Дж., Ли, К., и Ли, С. (2013). Синтез и характеристика водоразбавляемых эпоксидно-акриловых антикоррозионных покрытий. Дж. Макромоль. науч. В 52, 751–761. doi: 10.1080/00222348.2012.730351
CrossRef Полный текст | Google Scholar
Ван З., Хань Э., Лю Ф., Цянь З. и Чжу Л. (2014). Эпоксидные нанопокрытия на водной основе, модифицированные наноэмульсиями и наночастицами. Дж. Матер. науч. Технол. 30, 1036–1042. doi: 10.1016/j.jmst.2014.01.004
CrossRef Полный текст | Google Scholar
Йилмаз О., Каресоджа М., Адигузель К., Зенгин Г. и Тенху Х. (2014). Нанокомпозиты на основе сшитого полиакрилового латекса/наночастиц серебра для водоразбавляемых высокоэффективных антибактериальных покрытий. J. Appl. Полим. науч. А 52, 1435–1447. doi: 10.1002/pola.27130
Полный текст CrossRef | Google Scholar
Чжан Дж., Ли Ю., Ху К., Хуан В. и Су Л. (2019 г.). Антикоррозионные свойства покрытий полиуретан/поли(о-толуидин)–ZnO на водной основе в растворе NaCl. J. Прилипатели. науч. Технол. 33, 1047–1065. doi: 10.1080/01694243.2018.1529881
CrossRef Полный текст | Google Scholar
Чжан К., Хуанг К., Фанг К. и Лу К. (2017). Синтез самоэмульгируемого эпоксидного отвердителя на водной основе на основе глицидилтретного эфира карбоновой кислоты и характеристики его отверждения. J. Appl. Полим. науч. 134:44246. doi: 10.1002/app.44246
Полнотекстовая перекрестная ссылка | Google Scholar
Zhu, K., Li, X., Wang, H., Li, J. и Fei, G. (2017). Электрохимические и антикоррозионные свойства латексных композитов на основе алкидной смолы, модифицированной графеном/акриловой смолой, углеродистой стали. J. Appl. Полим. науч. 134:44445. doi: 10.1002/app.44445
Полный текст CrossRef | Google Scholar
Zhuo, Y., Liu, J., Li, Q., Qiu, B., and Xing, G. (2016). Получение и характеристика нанокомпозитов WPU/CNT/GO. Интегр. Ферроэлектр. 171, 52–58. doi: 10.1080/10584587.2016.1171662
CrossRef Полный текст | Google Scholar
Защита от коррозии — Защита от ржавчины
Коррозия, в том числе ржавчина, является глобальной проблемой, которой уделяется все больше внимания. В условиях устаревающей инфраструктуры риск возрастает и угрожает жизни и имуществу. Слишком часто проблемы игнорируются до тех пор, пока не становится слишком поздно.
Коррозия имеет два аспекта: предотвращение и ремонт. Важным фактором является то, что коррозия необратима… она всегда приводит к ослаблению конструкции. В то время как профилактика работает в будущем, ремонт является наиболее насущной проблемой.
Как ArmorThane предотвращает коррозию
Коррозия — это повреждение поверхностей и конструкций, вызванное реакцией на ряд элементов и условий. Напыляемые покрытия ArmorThane образуют защитный барьер, который блокирует эти вредные среды, поэтому коррозия не может начаться:
- Вода, дождь, влага
- Морская вода, соленый воздух
- Химические вещества, кислоты, газы
- Истирание и эрозия
- Высокоскоростной поток
- Напряжение, давление
- Микроорганизмы
- Ухудшение возраста
- Электролиз, Электрический дисбаланс
Коррозионностойкие сплавы и материалы с ингибиторами замедляют повреждение, но недолговечны. По мере того как защитные поверхности стираются в результате износа или физического повреждения, обнажаются лежащие под ними металлы.
Ржавчина является наиболее распространенным результатом и относится к коррозии железа и его сплавов, таких как сталь. Со временем в присутствии кислорода и воды прочные железные конструкции полностью разрушатся. По мере того, как металлическая поверхность стирается и ржавеет, обнажается новый металл; цикл повторяется, оставляя слои только хлопьев. Единственным решением является блокировка этих элементов путем покрытия полимерами ArmorThane до того, как начнется коррозия.
Почему ArmorThane лучше защищает
Краски и лаки обычно используются для покрытия поверхностей, но они обладают очень ограниченными защитными свойствами и со временем ухудшаются без регулярного ухода. Эти тонкие пленки плохо стареют и могут легко трескаться и отслаиваться, оставляя открытые поверхности.
Стандарты толщины поверхностных покрытий устанавливаются поставщиками и спецификациями клиентов, но краски и грунтовки обычно тестируются при толщине 10 мил или меньше. Напыляемые полимеры, естественно, толще, что в двадцать раз превышает толщину промышленных красок, в зависимости от проекта.
Чистые и гибридные полимочевины и полиуретаны ArmorThane были разработаны, чтобы противостоять истиранию, сильным ударам, экстремальным температурам, химическим веществам, воде и многим другим средам для широкого спектра применений. Эти полимеры выдерживают давление и растяжение, не трескаясь, даже при смещении или вибрации основной конструкции. Непроницаемая природа этих материалов создает бесшовный, герметичный барьер. В качестве бонуса аэрозольное покрытие покрывает сложные формы и легко транспортируется на рабочие площадки. Эти факторы делают долгосрочную ожидаемую продолжительность жизни очень рентабельной.
Действия по устранению ржавчины
Существуют разногласия по поводу удаления ржавчины. Одна школа говорит, что ржавчина может быть лишена кислорода и влаги, чтобы остановить ржавчину. Другая мысль заключается в том, что это практически невозможно сделать. Противники указывают на следующие проблемы:
- Ржавчина занимает больше объема, чем исходный металл, вызывая расширение, особенно в окружающем бетоне.
Известно, что это состояние вызывает раздвигание соседних суставов. Результатом являются трещины, которые способствуют более быстрому износу и повреждению.
- Многие из методов, направленных на ремонт или предотвращение ржавчины, часто дают сбой в швах, отверстиях и стыках, где есть пробелы в обработке. Они обеспечивают защиту в течение ограниченного времени.
- Если поверхности не полностью герметизированы или повреждены, такие элементы, как кислород и влага, проникают внутрь.
Согласитесь, что маскировка не работает для ремонта. Простое покрытие ржавчиной может улучшить внешний вид и замедлить износ, но все, что питает ржавчину, будет продолжать разъедать, часто незамеченным. Ослабленное состояние может привести к коллапсу.
Как минимум необходимо удалить рыхлую ржавчину. Существует несколько способов сделать это с помощью абразивно-струйной обработки/шлифовки, кислот, электролиза, преобразователей ржавчины и других методов борьбы с ржавчиной.
Далее необходимо подготовить поверхность. Если покрытие не держится, зазоры вызовут проблемы. Металл должен быть чистым и обезжиренным. Также может потребоваться грунтовка или шероховатость поверхности. Тщательное покрытие полимером ArmorThane — лучший способ создать бесшовный барьер для предотвращения проникновения кислорода и влаги.
Выбор наилучшего полимера
Все продукты ArmorThane прочны и создают герметичный барьер. Тем не менее, были разработаны различные полимеры для повышения защитных свойств в зависимости от поверхности, на которую наносится покрытие, и окружающей среды, такой как атмосферные и промышленные загрязнения, стресс и т. д.
Отрасли, получающие выгоду от полимерных покрытий затраты на коррозию составляют 2,2 триллиона долларов и 3% или более мирового ВВП. Ключевые отрасли, затронутые проблемой, включают:
- Трубопроводы для газа и жидкости
- Переработка нефти
- Автомобильные мосты
- Транспорт
- Морской, судоходный
- Питьевая вода
- Канализационные системы
- Производство, Производство
- Пищевая промышленность
- Химические производства
- Хранилище отходов
- Коммунальные услуги
Примеры защиты от коррозии и окисления
Суда и морская техника.
Транспортные контейнеры, подвергающиеся воздействию суровых условий.
Стальные мосты и другая открытая инфраструктура.
Кровля из алюминия и металла.
Защита от коррозии — SteelConstruction.info
Экономичная защита стальных конструкций от коррозии не вызовет затруднений при обычном применении и окружающей среде, если с самого начала будут определены факторы, влияющие на долговечность.
Многие стальные конструкции успешно эксплуатируются в течение многих лет даже в неблагоприятных условиях. Первое крупное железное сооружение, мост в Коулбрукдейле, Великобритания, просуществовало более 200 лет, в то время как о железнодорожном мосту Форт, которому более 100 лет, ходят легенды. Сегодня доступны современные долговечные защитные покрытия, которые при правильном использовании позволяют увеличить интервалы обслуживания и повысить производительность.
Ключ к успеху заключается в распознавании коррозионной активности среды, которой будет подвергаться конструкция, и в определении четких и подходящих спецификаций покрытия. Там, где сталь находится в сухом отапливаемом помещении, риск коррозии незначителен, и защитное покрытие не требуется. И наоборот, стальная конструкция, подвергающаяся воздействию агрессивной среды, должна быть защищена высокоэффективной обработкой и, возможно, должна быть спроектирована с учетом технического обслуживания, если требуется продление срока службы.
Оптимальная защитная обработка, которая сочетает в себе соответствующую подготовку поверхности, подходящие материалы покрытия, требуемую долговечность и минимальную стоимость, достижима с использованием современной технологии обработки поверхности.
Содержание
- 1 Коррозия конструкционной стали
- 2 Влияние конструкции на коррозию
- 3 Подготовка поверхности
- 4 Лакокрасочные покрытия
- 5 Металлические покрытия
- 5.1 Горячее цинкование
- 5.2 Металлические покрытия, полученные термическим напылением
- 6 Соответствующие спецификации
- 7 Инспекция и контроль качества
- 8 Каталожные номера
- 9 Ресурсы
- 10 Дальнейшее чтение
- 11 См.
также
- 12 Внешние ссылки
- 13 CPD
[вверх]Коррозия конструкционной стали
Основная статья: Коррозия конструкционной стали
Схематическое изображение механизма коррозии стали
Коррозия конструкционной стали представляет собой электрохимический процесс, требующий одновременного присутствия влаги и кислорода. При отсутствии того и другого коррозия не возникает. По сути, железо в стали окисляется с образованием ржавчины, которая занимает примерно в 6 раз больше объема исходного материала, потребляемого в процессе. Здесь показан общий процесс коррозии.
Наряду с общей коррозией могут возникать различные виды локальной коррозии; биметаллическая коррозия, точечная коррозия и щелевая коррозия. Однако они, как правило, не имеют существенного значения для металлоконструкций.
Скорость, с которой развивается процесс коррозии, зависит от ряда факторов, связанных с «микроклиматом», непосредственно окружающим конструкцию, в основном от времени увлажнения и уровня загрязнения атмосферы. Из-за изменений в атмосферных условиях данные о скорости коррозии не могут быть обобщены. Тем не менее, среды можно классифицировать в широком смысле, и соответствующие измеренные скорости коррозии стали дают полезный показатель вероятной скорости коррозии. Дополнительную информацию можно найти в BS EN ISO 129.44-2 [1] и BS EN ISO 9223 [2] .
Категория коррозионной активности | Низкоуглеродистая сталь Потеря толщины (мкм) a | Примеры типичных сред (только для справки) | |
---|---|---|---|
Внешний вид | Интерьер | ||
C1 очень низкий | ≤ 1,3 | — | Отапливаемые здания с чистой атмосферой, напр. офисы, магазины, школы, гостиницы |
C2 низкий | > 1,3 до 25 | Атмосферы с низким уровнем загрязнения: преимущественно сельские районы | Неотапливаемые здания, в которых может образовываться конденсат, напр.![]() |
C3 средний | > 25 до 50 | Городская и промышленная атмосфера, умеренное загрязнение двуокисью серы; прибрежная зона с низкой соленостью | Производственные помещения с повышенной влажностью и некоторым загрязнением воздуха, напр. предприятия пищевой промышленности, прачечные, пивоварни, молокозаводы |
C4 высокий | > от 50 до 80 | Промышленные районы и прибрежные районы с умеренным засолением | Химические заводы, плавательные бассейны, прибрежные суда и верфи |
C5 очень высокий | > 80 до 200 | Промышленные зоны с повышенной влажностью и агрессивной атмосферой и прибрежные зоны с повышенной соленостью | Здания или зоны с почти постоянной конденсацией и высоким уровнем загрязнения |
CX экстремальный | > 200 до 700 | Морские районы с высокой соленостью и промышленные районы с повышенной влажностью и агрессивной атмосферой, субтропической и тропической атмосферой | Промышленные зоны с повышенной влажностью и агрессивной атмосферой |
Примечания:
- 1 мкм (1 микрон) = 0,001 мм
- a Значения потери толщины приведены после первого года воздействия.
Убытки могут уменьшиться в последующие годы.
- Значения потерь, используемые для категорий коррозионной активности, идентичны значениям, указанным в BS EN ISO 9223 [2] .
[вверх]Влияние конструкции на коррозию
Основная статья: Влияние конструкции на коррозию
Конструкция и детали конструкции могут влиять на долговечность любого нанесенного на нее защитного покрытия. Конструкции, спроектированные с большим количеством мелких конструктивных элементов и крепежных элементов, труднее защитить, чем конструкции с большими плоскими поверхностями. Ключевые вопросы, которые необходимо рассмотреть, включают:
- Доступ для нанесения покрытия и обслуживания
- Избегание ловушек для влаги и мусора
- Предотвращение или герметизация щелей
- Дренаж и вентиляция для минимизации времени увлажнения
- Тщательное управление контактом с другими материалами
Общие рекомендации по предотвращению коррозии за счет надлежащей детализации конструкции можно найти в BS EN ISO 12944-3 [3] , а также некоторые типичные рекомендации и запреты для стальных каркасов. здания показаны ниже.
Примеры детализации зданий
[вверх]Подготовка поверхности
Основная статья: Подготовка поверхности
Стальная балка, выходящая из установки автоматической пескоструйной очистки
Подготовка поверхности — это обязательный первый этап обработки стальной подложки перед нанесением любого покрытия, который обычно считается наиболее важным фактором, влияющим на общий успех защиты от коррозии система.
Характеристики покрытия в значительной степени зависят от его способности должным образом прилипать к материалу подложки. Исходное состояние поверхности стали может варьироваться в зависимости от количества остаточной прокатной окалины и степени начальной ржавчины. Однако, как правило, это неудовлетворительная основа для нанесения современных высокоэффективных защитных покрытий. Существует ряд методов подготовки и степеней чистоты, но, безусловно, наиболее важным и важным методом, используемым для тщательной очистки поверхностей от прокатной окалины и ржавчины, является абразивоструйная очистка. Стандартные степени чистоты для абразивоструйной очистки в соответствии с ISO 8501-1 [4] являются:
- Sa 1 – Легкая пескоструйная очистка
- Sa 2 – Тщательная пескоструйная очистка
- Sa 2½ – Очень тщательная пескоструйная очистка
- Sa 3 – Дробеструйная очистка до визуально чистой стали
Ручная пескоструйная очистка
(Видео предоставлено Corrodere/MPI)
Процесс подготовки поверхности не только очищает сталь, но также обеспечивает подходящий профиль и амплитуду поверхности для нанесения защитного покрытия. Толстослойные лакокрасочные покрытия и металлические покрытия, полученные термическим напылением, требуют грубого угловатого профиля поверхности для обеспечения механического ключа. Это достигается за счет использования абразивных материалов. Дробеструйные абразивы используются для тонкопленочных лакокрасочных покрытий, таких как заводские грунтовки. Разница между дробью и дробью и соответствующими профилями поверхности показана ниже на трехмерных диаграммах, полученных с помощью оборудования для бесконтактной характеристики поверхности.
Абразивная дробь
Зернистый абразив
После абразивоструйной очистки можно проверить дефекты поверхности и изменения поверхности, возникшие в процессе изготовления, например, сварка. Некоторые поверхностные дефекты, появившиеся во время первоначальной обработки стали, могут не оказывать отрицательного влияния на характеристики покрытия в процессе эксплуатации, особенно для конструкций в категориях окружающей среды с относительно низким уровнем риска. Однако, в зависимости от конкретных требований к конструкции, может потребоваться дополнительная обработка поверхности для удаления поверхностных дефектов на сварных швах и кромках срезов, а также растворимых солей для обеспечения приемлемого состояния поверхности для окраски.
[вверх]Лакокрасочные покрытия
Основная статья: Лакокрасочные покрытия
Поперечное сечение многослойной системы окраски
Лакокрасочные покрытия для стальных конструкций разрабатывались на протяжении многих лет в соответствии с промышленным законодательством по охране окружающей среды и в ответ на требования владельцев мостов и сооружений о повышении долговечности. Краска состоит из пигмента, диспергированного в связующем и растворенного в растворителе. Наиболее распространены методы классификации красок либо по их пигментации, либо по типу связующего вещества.
Современная система окраски обычно включает последовательное нанесение красок или, альтернативно, красок, наносимых на металлические покрытия для образования «дуплексной» системы покрытия. Защитные лакокрасочные системы обычно состоят из грунтовки, промежуточных/сборочных слоев и финишных слоев. Каждый «слой» покрытия в любой защитной системе выполняет определенную функцию, и различные типы наносятся в определенной последовательности: грунтовка, промежуточные/сборочные слои в цеху и, наконец, финишное покрытие (или верхнее покрытие) либо в цехе. или на месте.
Предварительные грунтовки используются на стальных конструкциях сразу после пескоструйной очистки, чтобы сохранить реактивно очищенную поверхность в состоянии отсутствия ржавчины в процессе изготовления до тех пор, пока не будет проведена окончательная покраска. Эти типы грунтовки не используются перед нанесением термического напыления покрытий.
Способ нанесения систем окраски и условия нанесения оказывают существенное влияние на качество и долговечность покрытия. Стандартные методы, используемые для нанесения красок на стальные конструкции, включают нанесение кистью, валиком, обычным воздушным распылением и безвоздушным распылением/электростатическим безвоздушным распылением.
Безвоздушное распыление стало наиболее часто используемым методом нанесения лакокрасочных покрытий на стальные конструкции в контролируемых заводских условиях. нанесение кистью и валиком чаще используется для нанесения на месте, хотя также используются методы распыления. Покрытия «полосатые», наносимые на кромки и острые углы, обычно наносятся кистью.
- Безвоздушное распыление на стальные балки мостов
Основными условиями, влияющими на нанесение лакокрасочных покрытий, являются температура стали и окружающей среды, а также влажность. Их легче контролировать в условиях магазина, чем на месте. С появлением современных высокоэффективных покрытий правильное нанесение становится все более важным для достижения намеченных характеристик. Промышленность признала это и ввела схему обучения и сертификации специалистов по нанесению красок (ICATS — Схема обучения специалистов по нанесению покрытий). Регистрация ICATS (или эквивалентная схема, например, Trainthepainter) впоследствии стала обязательным требованием для работы на мостах Highways England и сооружениях Network Rail.
Безвоздушное распыление краски
(Видео предоставлено Corrodere/MPI)
[вверх]Металлические покрытия
Основная статья: Металлические покрытия
Существует четыре широко используемых метода нанесения металлического покрытия на стальные поверхности. Это горячее цинкование, термическое напыление, гальваническое покрытие и шерардизация. Последние два процесса не используются для металлоконструкций, но используются для фитингов, крепежных изделий и других мелких предметов. В целом защита от коррозии, обеспечиваемая металлическими покрытиями, в значительной степени зависит от выбора металла покрытия и его толщины и не сильно зависит от способа нанесения.
[вверх]Горячее цинкование
Стальные элементы, извлекаемые из обычной ванны для горячего цинкования
Горячее цинкование — это процесс, который включает погружение стального компонента, подлежащего покрытию, в ванну с расплавленным цинком (при температуре около 450 °C) после травления и флюсования, а затем отзыв его. Погруженные поверхности равномерно покрыты цинковым сплавом и слоями цинка, образующими металлургическую связь с подложкой. Полученное покрытие является прочным, прочным, устойчивым к истиранию и обеспечивает катодную (жертвенную) защиту любых небольших поврежденных участков на стальной основе. Типичная минимальная средняя толщина покрытия для стальных конструкций составляет 85 мкм.
Поперечное сечение горячеоцинкованного покрытия
[top]Термическое напыление металлических покрытий
Поперечное сечение термически напыленного алюминиевого покрытия
Термически напыляемые покрытия из цинка, алюминия и цинко-алюминиевых сплавов могут обеспечить долговременную защиту от коррозии стальных конструкций, подвергающихся воздействию агрессивных сред. Металл в виде порошка или проволоки подается через специальный пистолет-распылитель, содержащий источник тепла, которым может быть кислородное пламя или электрическая дуга. Капли расплавленного металла выдуваются струей сжатого воздуха на предварительно очищенную пескоструйным методом стальную поверхность. Легирования не происходит, покрытие состоит из перекрывающихся пластин металла и является пористым. Затем поры герметизируются путем нанесения тонкого органического покрытия, проникающего вглубь поверхности. Важно, чтобы герметик полностью заполнил все поры в металлическом покрытии.
Адгезия напыленных металлических покрытий к стальным поверхностям считается в основном механической по своей природе. Поэтому необходимо наносить покрытие на чистую шероховатую поверхность, и обычно рекомендуется пескоструйная очистка крупнозернистым абразивом.
Дуговое напыление
(Видео предоставлено Metallisation)
[наверх]Подходящие спецификации
Основная статья: Подходящие спецификации
Общий успех схемы защитного покрытия начинается с хорошо подготовленной спецификации. Это важный документ, предназначенный для предоставления подрядчику четких и точных инструкций о том, что и как следует делать. Спецификация должна быть составлена кем-то с соответствующими техническими знаниями, и в ней должно быть ясно, что требуется, а что является практичным и достижимым. Он должен быть написан в логической последовательности, начиная с подготовки поверхности, проходя через каждую наносимую краску или металлическое покрытие и, наконец, касаясь конкретных областей, например. сварные швы. Он также должен быть максимально кратким, согласующимся с предоставлением всей необходимой информации. Наиболее важными элементами спецификации являются следующие:
- Металлическая обработка для удаления острых краев, выступов и т. д., а также стальных загрязнений.
- Метод подготовки поверхности и требуемый стандарт.
- Максимальный интервал между подготовкой поверхности и последующим грунтованием или металлическим покрытием.
- Типы используемых красок или металлических покрытий, поддерживаемые соответствующими стандартами.
- Используемый(е) метод(ы) применения.
- Количество наносимых слоев и интервал между слоями.
- Толщина влажной и сухой пленки для каждого слоя.
- Место нанесения каждого слоя (т.
е. магазины или строительная площадка) и требуемые условия нанесения с точки зрения температуры, влажности и т. д.
- Детали для обработки сварных швов, болтовых соединений и т. д.
- Процедуры устранения повреждений и т. д.
Большинство стальных мостов защищены в соответствии с требованиями Highways England и стандартными спецификациями Network Rail. Для других мостов могут быть указаны альтернативные системы и методы покрытия, но должны применяться те же стандарты и принципы надлежащей практики покрытия.
[наверх]Инспекция и контроль качества
Основная статья: Инспекция и контроль качества
Ассортимент инструментов для испытаний и контроля
Контроль является неотъемлемой частью контроля качества. Его целью является проверка соблюдения требований спецификации и предоставление клиенту отчета с надлежащими записями. Одним из самых больших преимуществ для инспектора по покрытиям является четкая письменная спецификация, на которую можно без сомнений ссылаться.
Назначение стороннего инспектора с соответствующей квалификацией следует рассматривать как инвестиции в качество, а не просто как дополнительные расходы. Проверка процессов, процедур и материалов, необходимых для нанесения защитного покрытия на стальные конструкции, имеет жизненно важное значение, поскольку серьезную ошибку даже в одной операции нельзя легко обнаружить после выполнения следующей операции, и, если ее не исправить немедленно, это может значительно снизить ожидаемые срок службы до первого технического обслуживания.
[наверх]Ссылки
- ↑ 1.0 1.1 BS EN ISO 12944-2: 2017, Краски и лаки. Защита стальных конструкций от коррозии защитными системами окраски. Часть 2. Классификация сред, BSI
- ↑ 2.0 2.1 BS EN ISO 9223: 2012, Коррозия металлов и сплавов. Коррозионная активность атмосферы. Классификация, определение и оценка BSI
- ↑ BS EN ISO 12944-3: 2017, Краски и лаки. Защита стальных конструкций от коррозии защитными системами окраски.
Часть 3. Вопросы проектирования, BSI
- ↑ BS EN ISO 8501-1: 2007 Подготовка стальных поверхностей перед нанесением красок и сопутствующих продуктов. Визуальная оценка чистоты поверхности. Степени ржавчины и степени подготовки стальных поверхностей без покрытия и поверхностей после полного удаления предыдущих покрытий, ISO
Ресурсы
- Хенди, Ч.Р.; Айлс, округ Колумбия (2015) Группа стальных мостов: Руководящие указания по передовой практике строительства стальных мостов (6-й выпуск). (стр. 185). SCI
- Руководство 8.01 Подготовка к эффективной защите от коррозии
- Руководство 8.02 Защитная обработка крепежных изделий
- Руководство 8.03 Горячее цинкование погружением
- Руководство 8.04 Металлические покрытия, полученные термическим напылением
- Руководство 8.05 Высокоэффективные лакокрасочные покрытия
- Руководство 8.06 Проверка подготовки поверхности и обработки покрытий
- Стальные здания, 2003 г.
, Британская ассоциация строительных металлоконструкций, ООО.
- Глава 12 – Защита от коррозии
[наверх]Дополнительная литература
- D.Deacon & R.Hudson (2012 г.), Руководство по проектированию металлоконструкций (7-е издание), Глава 36. Коррозия и предотвращение коррозии, Институт стальных конструкций.
- Д.А. Bayliss & DHDeacon (2002), Steelwork Corrosion Control (2-е издание), Spon Press
[вверху] См. также
- Коррозия конструкционной стали
- Влияние конструкции на коррозию
- Подготовка поверхности
- Лакокрасочные покрытия
- Стандартные системы защиты зданий от коррозии
- Металлические покрытия
- Соответствующие спецификации
- Инспекция и контроль качества
[наверх]Внешние ссылки
- Британская федерация покрытий
- Ассоциация гальванистов
- Ассоциация исследования красок
- Ассоциация термического напыления и обработки поверхностей
- ИКАТС
- Корродор
- Защита от коррозии
Защита от коррозии — Ингибисферы
Краски являются одним из наиболее часто используемых методов предотвращения коррозии металлических поверхностей; Обеспечивает экономичную и практичную альтернативу другим методам, таким как гальванопокрытие, покрытие и эмалирование, и в то же время дает возможность персонализировать внешний вид поверхности. Как правило, антикоррозионная краска состоит из двух слоев: грунтовка содержит антикоррозионный агент и прилипает непосредственно к основанию. Большинство антикоррозионных пигментов имеют тенденцию придавать грунтовке матовый вид из-за их формы, размера и показателя преломления. Это означает, что, как правило, верхний слой требуется для обеспечения эстетических качеств краски, обеспечения блеска и гладкости. Покрытия, нанесенные непосредственно на металл (DTM), также могут использоваться для защиты металлов от коррозии, при этом пигмент, защищающий от коррозии, наносится с использованием системы с одним слоем. В то время как большинство антикоррозионных пигментов могут уменьшать глянец покрытия, что приводит к компромиссу между защитой от коррозии и внешним видом, Inhibispheres® могут быть включены в DTM без ухудшения характеристик поверхности и в то же время обеспечивают эффективную и долговечную работу. защита от коррозии.
В зависимости от среды, которой подвергается металлическая поверхность, скорость коррозии будет разной. Воздействие влаги, хлоридов и загрязнения воздуха могут увеличить коррозионную активность окружающей среды, классифицированную в ISO 12944-2, как показано ниже:
Класс окружающей среды | Уровень коррозии | Внутренняя среда | Внешняя среда |
---|---|---|---|
С1 | Очень низкий | Отапливаемое здание с низкой относительной влажностью, напр. магазины, офисы | Сухие или холодные зоны, очень низкий уровень загрязнения и очень кратковременная влажность, обычно не встречающиеся за пределами центральных арктических/антарктических районов |
С2 | Низкий | Неотапливаемые здания с непостоянной температурой и относительной влажностью, напр. спортивные залы, складские помещения | Умеренная зона с низким уровнем загрязнения, напр. сельская местность |
С3 | Умеренный | Производственные площади с умеренным загрязнением воздуха и высокой влажностью, напр.![]() | Умеренная зона, средние уровни загрязнения SO2, напр. городские районы, прибрежная зона с низким уровнем содержания хлоридов |
С4 | Высокий | Промышленные зоны с высокой конденсацией и промышленным загрязнением, напр. бассейны | Умеренная зона, высокий уровень загрязнения SO2 или высокая соленость, |
С5-I | Очень высокая – Промышленность | Здания или зоны с очень высокой частотой образования конденсата и высоким уровнем загрязнения, напр. шахты, промышленные раскопки | Умеренные и субтропические зоны, промышленные районы с очень высокой влажностью или прибрежные районы с высокой соленостью. Очень сильное загрязнение или хлориды, т.е. прибрежные районы, морские районы. |
С5-М | Очень высокий – Морской |
В зависимости от классификации коррозии среды, воздействию которой подвергается подложка, рекомендуются различные краски. Чистые барьерные покрытия считаются подходящими для классов коррозии C1-C3, в то время как добавление ингибитора, такого как Inhibispheres®, может улучшить защиту покрытия от коррозии, делая его пригодным для сред C1-C5.
Краски для защиты от коррозии могут быть классифицированы как активные, расходуемые или пассивные в зависимости от способа их действия. Краски, которые предотвращают коррозию исключительно за счет барьерной защиты, известны как пассивная защита от коррозии, поскольку они не изменяют поведение коррозионного агента и не изменяют склонность основания к коррозии. В этих красках также могут использоваться слои металлических или силикатных чешуек, чтобы обеспечить извилистый путь, что затрудняет попадание воды, пробившей поверхность краски, на подложку. Однако, если пленка краски повреждена, коррозия произойдет очень быстро из-за отсутствия защиты от окружающей среды. Некоторые из широко используемых пассивных антикоррозионных красок включают алкидные, акриловые, аминовые эпоксидные смолы, полиамидные эпоксидные смолы, уретановые и полиуретановые.
Эти краски также используются как для временной защиты, так и для активной защиты от коррозии. Жертвенные покрытия используют как барьерную защиту, так и катодную защиту для защиты подложки, при этом катодная защита используется при разрушении пленки краски (например, царапина, скол). В этих покрытиях используется присутствие металлов, которые являются более активными и будут корродировать преимущественно на подложке, помогая предотвратить коррозию нижнего слоя. Типичные расходуемые коррозионные пигменты включают фосфат цинка (ZnPO4), цинковую пыль или соединения хромата 6+ (CrVI). Существует ряд проблем с использованием этих соединений в антикоррозионных красках, связанных с серьезными проблемами со здоровьем и окружающей средой, возникающими в результате использования как цинковых, так и хроматных соединений. Это привело к ограничению использования шестивалентного хрома в Европе и других странах, при этом европейским компаниям требуется специальное и очень ограниченное разрешение REACH на использование этих соединений. Во всем мире настоятельно рекомендуется отказаться от использования этих типов материалов в антикоррозионных покрытиях. Краски с активной защитой от коррозии содержат добавку, которая может влиять на коррозионные реакции, вызванные воздействием агрессивных элементов, нарушая химические реакции коррозии. Они часто используются в праймерах.
Inhibispheres® обеспечивают активную защиту от коррозии при включении в традиционную систему барьерной окраски и способствуют самовосстановлению пленки краски при повреждении, предотвращая возникновение коррозии. Благодаря их однородному распределению по всему покрытию Inhibispheres® обеспечивает защиту независимо от того, где покрытие повреждено, распространяясь к месту коррозии, чтобы быстро предотвратить дальнейшую коррозию. Разработанный со специально подобранными ингибиторами коррозии, Inhibispheres® можно использовать как на стальных, так и на алюминиевых поверхностях, как в системах окраски на водной основе, так и на основе растворителей, а пролонгированное действие Inhibispheres® означает, что покрытие обеспечит длительную защиту от коррозии.
Коррозионная стойкость и антикоррозионные покрытия: типы и методы испытаний
- Коррозия – обзор
- Типы коррозии металлов
- Антикоррозионные покрытия – механизм и типы
- Ингибиторы коррозии и антикоррозионные пигменты
- Испытание на коррозионную стойкость – популярные методы
Коррозия – обзор
Термин « Коррозия » означает разрушение материала, вызванное химической или электрохимической реакцией с окружающей средой. Материал обычно относится к металлам, но может также включать неметаллические материалы, такие как керамика, полимер и пластик.
Коррозия не только влияет на прочность и долговечность материала, но и обходится дорого. Это приводит к повреждению оборудования и утечке продукции, что особенно важно в химической промышленности, тем самым создавая угрозу для окружающей среды .
Эксплуатационные характеристики и срок службы металлов или любой другой подложки можно улучшить за счет нанесения антикоррозионных покрытий. Покрытие действует как расходуемый материал и служит «барьерным слоем » для поверхности материала при коррозии. К преимуществам использования покрытий для защиты от коррозии в основном относятся:
- Повышение эффективности металлов или других компонентов
- Производство поверхностей из новых материалов с улучшенными функциональными характеристиками и свойствами
- Промышленные операции по переработке
- Снижение стоимости обслуживания и замены
- Экономия дефицитных природных ресурсов
- Сокращение выбросов загрязняющих веществ
Давайте подробно рассмотрим распространенные типы коррозии металлов и то, как они возникают…
Типы коррозии металлов
Чтобы сделать правильный выбор покрытий, необходимо определить тип коррозии. Пять распространенных типов коррозии включают:
Другими распространенными типами коррозии являются нитевидная коррозия, отслоение, растрескивание под воздействием окружающей среды, кавитация и т. д.
Антикоррозионные покрытия – механизм и типы
Сегодня для защиты от коррозии широко используются антикоррозийные покрытия. Механизм, который позволяет покрытиям защищать материальные подложки от коррозии, в основном включает:
- Снижение скорости окисления или снижение полуреакций коррозии, происходящих на поверхности материала.
- Улучшение электрического сопротивления на границе материала с электролитом.
- Представляет собой физический барьер против O 2 ,H 2 O и ионов коррозии, таких как Cl — и SO 4 -2 .
Кинетика, термодинамика и природа являются ключевыми факторами, влияющими на окружающую среду, и для понимания коррозионной стойкости необходимо обладать всесторонними научными знаниями и изучать факторы, связанные с этим, как описано здесь.
Внешние факторы | Состав / на основе композиции |
|
|
Типы покрытий, используемых для защиты от коррозии
Покрытия, используемые для защиты от коррозии, в основном бывают трех типов: металлические, органические и неорганические. Давайте подробно обсудим каждый из них:
- Металлические покрытия : Нанесение металлических покрытий включает электроосаждение, газопламенное напыление, плакирование, горячее погружение и осаждение из паровой фазы.
- Неорганические покрытия : Нанесение неорганических покрытий включает распыление, диффузию и химическое преобразование.
- Органические покрытия : Нанесение включает создание барьера между материалом подложки и окружающей средой. Покрытия, такие как краски, лаки и лаки, более эффективно защищают металл.
Органические ингибиторы коррозии могут использоваться отдельно или в сочетании с неорганическими ингибиторами коррозии, обеспечивая двойное защитное действие и повышая антикоррозионные свойства покрытия.
Другие распространенные типы антикоррозионных покрытий включают:
Керамические покрытия. Эти покрытия улучшают коррозионную стойкость системы, создавая защитный барьер между деталью и агрессивной средой. В таких отраслях, как полупроводниковая промышленность, производство топливных элементов и коррозионно-активных сред, таких как газотурбинные двигатели, теплообменники и двигатели внутреннего сгорания, используются керамические покрытия с высокой эрозионной стойкостью, такие как TiN, CrN.
Другие интересные разработки в области антикоррозионных покрытий включают гибридные покрытия , умные покрытия , наноматериалы , биоматериалы и биомиметики.
Особенности антикоррозионных покрытий
Значение грунтовки и финишного покрытия
Для любых многослойных систем покрытий грунтовка и верхнее покрытие являются ключевыми слоями, отвечающими за защиту металла от коррозии. Если грунтовка не имеет хорошей адгезии к основанию или несовместима с верхним покрытием, существует вероятность преждевременного выхода из строя.
- Нарушение адгезии подложки обычно происходит между слоем покрытия (грунтовка) и адгезивом (подложкой).
Узнайте об основах адгезии и факторах, влияющих на это свойство покрытий.
- Нарушение межслойной адгезии происходит, когда связь между верхним слоем и грунтовкой не соединяется. Двумя основными причинами этого отказа являются недостаточно отвержденный верхний слой и нанесенный толстый слой грунтовки.
Грунтовка создает высокоактивную основу, таким образом обеспечивая стабильную поверхность, на которой могут фиксироваться последующие слои краски. Он обеспечивает катодную защиту и помогает ингибировать или замедлять коррозию защищаемой металлической поверхности. Верхний слой наносится поверх грунтовки или существующей отделки для защиты или украшения.
При использовании в качестве антикоррозионной краски основными компонентами грунтовки являются ингибиторы коррозии/антикоррозионные пигменты .
В поисках более экологичных коррозионно-стойких систем – будьте бдительны, эксперты!
Ускорьте разработку долговечной, экологически чистой и коррозионно-стойкой системы покрытий , применяя лучшие альтернативы хроматным технологиям, чтобы опередить конкурентов. Зарегистрируйтесь сейчас, чтобы пройти курс под названием «Стратегии составления защитных покрытий для более экологичных коррозионно-стойких систем» » Dr. Ing. Patricia Geelen .
Ингибиторы коррозии и антикоррозионные пигменты
Нанесение покрытий, состоящих из антикоррозионных пигментов или ингибиторов коррозии , является наиболее распространенным методом коррозионной стойкости. Антикоррозийные пигменты обеспечивают защиту от коррозии металлических подложек, в основном цинка, стали и алюминия.
Эти пигменты или добавки обладают физическим защитным действием, и их механизм работает на создание барьерного эффекта, просто увеличивая диффузионное расстояние между поверхностью покрытия и поверхностью металла. Основные преимущества антикоррозионных пигментов включают:
- Обеспечение физического барьера для прохождения воды и кислорода
- Жертвенно уничтожается в качестве анода, таким образом защищая анодные участки, которые стали изъеденными
- Обеспечение растворимыми пассивирующими ионами для защиты металла
- Образует нерастворимую пленку, предотвращающую активную коррозию, и
- Улучшение адгезии покрытия к подложке и защита связующего вещества от фотохимического разрушения в результате отражения и/или поглощения УФ-излучения
Классификация антикоррозионных пигментов
Антикоррозионные пигменты можно классифицировать по их химической природе:
- Неорганические пигменты, такие как свинец, хроматфосфаты, молибдаты, силикаты и ферриты
- Органические пигменты, такие как углеродные цепи и углеродные кольца, и органические полимерные материалы
- Металлические пигменты, такие как цинк, алюминий и сплавы
на основе свинца — два оксида свинца, используемые в качестве антикоррозионных агентов, — это глет (PbO) и красный свинец (Pb 9). 0011 3 О 4 ). Плохо растворимы (растворимость < 0,001%). Свинцовые пигменты фактически не являются прямыми ингибиторами. Они могут реагировать с некоторыми системами смол, льняным маслом или другими маслами с образованием металлических мыл, которые являются активными ингибиторами и, по-видимому, являются механизмом, посредством которого свинцовые пигменты подавляют коррозию.
Хроматные пигменты . Как правило, шестивалентный (Cr 6+ ) хром (сильный окислитель) и трехвалентный (Cr 3+ ) ионы хрома обеспечивают высокую коррозионную стойкость хроматных покрытий. При коррозионном воздействии шестивалентный хром подвергается активной защите от коррозии и восстанавливается с образованием трехвалентного хрома. Затем нерастворимый трехвалентный хром может положить конец атаке.
Хотя свинцовые и хромовые пигменты обладают отличной коррозионной стойкостью, они очень токсичны по своей природе. Со временем их применение в рецептурах покрытий сократилось из-за их вредного воздействия на окружающую среду.
В последние годы было проведено значительное количество исследований и разработок, направленных на поиск замены свинцовым и хроматным пигментам в антикоррозионных покрытиях. Доступны некоторые дополнительные пигменты и технологии, которые обеспечивают защиту от коррозии без вредного воздействия на здоровье и окружающую среду, включая:
Фосфаты (ортофосфаты, полифосфаты) – Это нетоксичный и антикоррозионный пигмент, часто используемый в красках. Эти пигменты проявляют повышенную антикоррозионную эффективность при использовании в высокой концентрации. Пигменты на основе фосфатов почти полностью заменили свинцово-хроматные пигменты в высокотехнологичных областях применения, таких как покрытия для рулонных материалов и грунтовки для самолетов.
- Ортофосфаты являются экономически эффективными антикоррозионными средствами, совместимыми с широким спектром типов смол и обеспечивающими улучшенную долговременную защиту.
- Полифосфаты – продукты на основе кислого триполифосфата алюминия, модифицированного соединениями цинка, стронция и кальция.
Эти соединения обладают высокой электрохимической эффективностью благодаря измененной конструкции химической структуры.
Дигидрат ортофосфата цинка – Обладает превосходными свойствами коррозионной стойкости и имеет ряд преимуществ, таких как повышенная износостойкость и отличная адгезия между слоями. Другими предлагаемыми фосфатными пигментами являются фосфат алюминия, фосфаты кальция, магния, фосфаты бария, фосфаты алюминия, цинка и фосфат молибдена.
Другие материалы, замедляющие коррозию, включают:
Молибдаты кальция, стронция и цинка — эти пигменты белого цвета, их можно использовать в качестве грунтовки в красках, смешивая с любым другим цветом. Их использование значительно расширилось в последние годы из-за их более благоприятных физиологических свойств.
Оксид цинка — Порошкообразный оксид цинка используется в качестве ингибитора и антикоррозионного пигмента. Способствует успешной антикоррозионной защите металлических конструкций, подвергающихся воздействию морской атмосферы.
Силикаты . Силикаты, такие как боросиликат кальция, фосфосиликат кальция-бария, фосфосиликат кальция-стронция и фосфосиликат кальция-стронция-цинка, также обладают антикоррозионными свойствами при использовании в составе краски.
Титанаты — Титанат кальция со структурой перовскита — высокоэффективный антикоррозионный пигмент для красок.
Ферриты — Ферриты относятся к пигментам, состоящим из Fe 2 O 3 и другой металл, обычно магний, кальций, стронций, барий, цинк или марганец. Эти пигменты способствуют защите от коррозии, образуя щелочную среду на границе между покрытием и подложкой. Эта щелочная среда способствует пассивации металла.
» Читайте также: Советы экспертов по выбору метода обработки поверхности и антикоррозионных добавок
Проверка коррозионной стойкости – популярные методы
Существует несколько методов испытаний для оценки коррозионной стойкости поверхности красок. Здесь перечислены популярные методы испытаний на коррозионную стойкость:
ASTM D2803 – Стандартное руководство по тестированию стойкости органических покрытий к нитевидной коррозии на металле
Некоторые органические покрытия, нанесенные на металлические подложки, проявляют нитевидную коррозию при разрыве пленки покрытия и относительной влажности в диапазоне от 70 до 95 %. Это руководство можно использовать для определения подверженности металлических подложек с органическим покрытием образованию нитевидной коррозии.
ASTM D7893 — Стандартное руководство по подготовке панелей для испытаний на коррозию, испытаниям и оценке строительных изделий с рулонным покрытием
Металлы с рулонным покрытием подвергаются широкому спектру воздействий окружающей среды. Коррозия на обрезанных кромках, в местах повреждений и на обработанных участках может привести к преждевременному выходу из строя.
Эта статья относится к подготовке, испытаниям и оценке испытательных панелей с линейным и лабораторным покрытием с целью сравнения и ранжирования панелей по коррозионной стойкости и другим связанным свойствам.
ASTM D1654 — Стандартный метод испытаний для оценки окрашенных образцов или образцов с покрытием, подвергнутых воздействию агрессивных сред
Этот метод испытаний распространяется на обработку предварительно окрашенных или покрытых образцов для испытаний на ускоренное воздействие и воздействие атмосферных условий и их последующую оценку в отношении:
- Коррозия
- Образование пузырей, связанное с коррозией
- Потеря адгезии в месте разметки или
- Другие кинопровалы
» Подробнее о циклическом и статическом методе испытаний на коррозию!
Таким образом, адгезия покрытия к основе также является важным фактором в отношении антикоррозионных свойств. Если 9Покрытие 0738 плохо прилипает к подложке, покрытие может легко отслаиваться, увеличивая открытую поверхность подложки.
Ингибиторы коррозии для красок, покрытий и чернил
Ознакомьтесь с полным ассортиментом ингибиторов коррозии, доступных сегодня, проанализируйте технические характеристики каждого продукта, получите техническую поддержку или запросите образцы.
Защита стали от коррозии | Американская ассоциация гальванистов
Дом » Горячее цинкование (HDG) » Почему именно цинкование? » Защита от коррозии для стали
Экстремальная коррозия Сталь— распространенный и эффективный строительный материал, дающий разработчикам свободу проектирования. Однако для проектов, подверженных воздействию атмосферы и других агрессивных сред, очень важно нанести на сталь покрытие для защиты от коррозии. Часто крупные строительные проекты рассчитаны на расчетный срок службы 50-100 лет, что подчеркивает необходимость надежной и долговечной защиты от коррозии. Существует бесчисленное множество примеров, демонстрирующих проверенную защиту горячего цинкования в самых суровых условиях.
Причиной широкого применения горячего цинкования (HDG) является тройной защитный характер покрытия. В качестве барьерного покрытия он обеспечивает прочное металлургически связанное цинковое покрытие, которое полностью покрывает стальную поверхность и изолирует сталь от коррозионного воздействия окружающей среды. Кроме того, жертвенное поведение цинка защищает сталь даже в случае повреждения или незначительного разрыва покрытия. Наконец, естественное выветривание покрытия приводит к образованию на поверхности дополнительного защитного слоя.
Барьерная защита
Барьерная защита, пожалуй, самый старый и наиболее широко используемый метод защиты от коррозии. Он действует путем изоляции основного металла от окружающей среды. Как и краски, покрытие методом горячего цинкования обеспечивает барьерную защиту стали. Пока барьер не поврежден, сталь защищена и коррозии не произойдет. Однако если барьер будет нарушен, начнется коррозия.
Поскольку для обеспечения коррозионной стойкости барьер должен оставаться неповрежденным, двумя важными свойствами барьерной защиты являются адгезия к основному металлу и стойкость к истиранию. Плотно связанная, непроницаемая природа цинка делает цинкование очень хорошим барьерным покрытием. гораздо более толстая стальная деталь. Покрытия, такие как краска с точечными отверстиями, восприимчивы к проникновению элементов, вызывающих быстрое распространение коррозии под пленкой.
Катодная защита
Гальваническая серия металлов (справа) перечисляет металлы и сплавы в порядке убывания электрической активностиКатодная защита является более эффективным методом защиты от коррозии. Это требует замены элемента коррозионной цепи путем введения нового коррозионного элемента, таким образом гарантируя, что основной металл станет катодным элементом цепи.
Горячее цинкование обеспечивает катодную защиту стали аналогично методу расходуемого анода. В основном, металл (цинк), анодированный по отношению к основному металлу (стали), помещается в цепь для коррозии вместо основного металла. Гальваническая серия металлов представляет собой список металлов, расположенных в порядке электрохимической активности в морской воде (электролите). Такое расположение металлов определяет, какой металл будет анодом и катодом, когда они будут помещены в электролитическую ячейку. Металлы выше в списке являются анодными по отношению к металлам ниже, что означает, что они обеспечивают катодную или жертвенную защиту, когда они соединены.
Из списка видно, что в случае горячего цинкования цинк предпочтительнее защищает от коррозии основную стальную основу. Фактически, катодная защита HDG гарантирует, что даже если покрытие повреждено до такой степени, что обнажается голая сталь (до ¼ дюйма в диаметре), коррозия не начнется до тех пор, пока не будет израсходован весь окружающий цинк.
Цинк горячеоцинкованного покрытия будет жертвовать собой, чтобы защитить основную стальную основу до тех пор, пока весь окружающий цинк не будет израсходован.Цинковая патина
В отличие от барьерной и катодной защиты, которые препятствуют коррозии самой стали, цинковая патина защищает цинковое покрытие. Цинк, как и все металлы, начинает подвергаться коррозии при воздействии атмосферы. Таким образом, свежеоцинкованная сталь проходит процесс естественного выветривания при воздействии влажных и сухих циклов в окружающей среде.
Когда гальванизированные покрытия подвергаются воздействию свободного потока воздуха, образование цинковой патины начинается с тонкого слоя оксидов цинка. Затем, когда деталь подвергается воздействию влаги (дождь, роса, сырость), частицы оксида цинка реагируют с водой, образуя пористый студенистый гидроксид цинка. Затем во время циклов сушки углекислый газ вступает в реакцию с гидроксидом цинка и превращается в тонкий, компактный и плотно прилегающий слой карбоната цинка. Скорость образования патины варьируется в зависимости от условий окружающей среды, но обычно для ее полного развития требуется примерно 6–12 месяцев.
Полностью проявленная патина представляет собой пассивную, стабильную пленку, которая прилипает к цинковой поверхности и не растворяется в воде, поэтому не смывается дождем или снегом. Из-за этого патина цинка подвергается коррозии очень медленно и защищает оцинкованное покрытие под ним, замедляя скорость коррозии примерно до 1/30 скорости коррозии стали в той же среде. По мере образования цинковой патины оцинкованное покрытие приобретает матово-серый цвет.
Образование цинковой патины имеет решающее значение для долговременной коррозионной стойкости при горячем цинковании.