Технология производства экструзионного пенополистирола
На сегодняшний день образовался довольно большой спрос на эсктрузионный вспененный полистирол в связи с развитием строительства как частного, так и коммерческого. Вспененный полистирол обладает лучшими потребительскими свойствами по сравнению с обычным пенопластом, обладает практически нулевым влагопоглощением, повышенной жесткостью.
В зависимости от технологии производства вспененный полистирол бывает следующих типов:
- прессовый пенополистирол
- EPS — безпрессовый пенополистирол ПСБ
- XPS — экструзионный пенополистирол
От этого зависит и цена на пенополистирол.
Производить вспененный экструзионный полистирол стали довольно давно, поначалу вспенивание производилось с помощью жестких фреонов, затем применяли смесь жестких и мягких фреонов, затем перешли к применению только мягких фреонов. После того как было доказано что фреоны способствуют разрушению озонового слоя вместо фреонов стали применять вспенивание с помощью CO

Для вспенивания применяются смеси полистирола общего назначения и впс (вспенивающийся полистирол), также добавляют пигменты или красители, нуклеаторы, антипирены. Применяемые добавки зависят от необходимых требований к готовому изделию.
Вспенивание происходит методом свободного вспенивания через плоскощевую фильеру, затем полученное полотно проходит через безвакуумный калибратор состоящий из двух охлаждаемых пластин или через охлаждаемые формующие валки. При применении охлаждаемых пластин на них крепится тонкий лист фторопласта для уменьшения трения между вспенивающимся листом и металлом пластин. Калибратор стали применять относительно недавно, а раньше применялись охлаждаемые формующие валки. После предварительного охлаждения и формовки полотно проходит через тянущее устройство.
После тянущего устройства для полотна даётся пространство для окончательного воздушного охлаждения, обычно это растояние составляет от 10м до 20м, за время прохождения этого расстояния полотно практически полностью остывает и завершается процесс вспенивания, изделие стабилизируется и готово для обработки поверхностей.
Поверхность полотна обрезается, как с боков, так и сверху-снизу, т.е полотно получается правильной геометрической формы, после чего оно нарезается на листы заданной длины.
Обрезанные кромки дробятся, гранулируются и заново перерабатываются в изделие.
При высокой производительности линии применяется дополнительное устройство для охлаждения листов перед упаковкой. Это устройство представляет собой автоматический укладчик карусельного типа, который берет листы с одного конвейера и перекладывает их на другой конвейер, за время перекладывания листа, он успевает почти полностью остыть и стабилизироваться и соответствено лист становится готовым к упаковке. Время нахождения листа на устройстве дополнительного охлаждения составляет от 60сек.
Далее листы складываются в стопы и упаковываются в пленку стретч или стретч-худ.
При экструзии используются два одношнековых экструдера, первый используется для расплавления и перемешивания сырья, а второй как насос расплава, также во втором экструдере происходит полное разложение вспенивающих добавок входящих в состав впс. Также возможны варианты применения шестеренчатых насосов расплава, но они как правило применяются на линиях малой производительности.
ПОЛУЧЕНИЕ ТЕПЛОИЗОЛЯЦИОННЫХ МАТЕРИАЛОВ Н4 ОСНОВЕ ПОЛИСТИРОЛА МЕТОДОМ ЭКСТРУЗИИ
Высокая сорбционная способность полистирола к предельным углеводородам и их галогенпроизводным (фреонам) явилась основой для развития технологии пеноизделий. По сравнению с другими крупнотоннажными пластмассами полистирол относительно легко перерабатывается методом экструзии, так как требует меньших энергозатрат и обладает более широким интервалом температур при переработке по сравнению, например, с полиолефинами. Инертность фреонов по сравнению с пентанами с точки зрения пожарной безопасности также способствовала их внедрению в производство.
Первые производства пенополистирольных плит методом экструзии были созданы фирмой «Ооу СЬет.» в конце 1950-х гг. В качестве пеноаген гов использовалась смесь фреонов 11 и 12. Однако экологические проолемы, связанные с нарушением озонового слоя из-за широкого использования этих фреонов, привели к необходимости их замены на озонобезоиасные соединения, к которым можно отнести:
1) неполностью галогенировачные углеводороды: фреоны 142в, 22,134а и 152а;
2) нейтральные газы: азот и углекислый газ:
3) предельные углеводороды: бутан, пентан, изопентан.
Применение дешевых инертных газов — азота и углекислого
Газа в качестве пеноагентов ограничивается их низкой Генри растворимостью в полистироле. Так, для достижения растворимости азота более 10 см3/г требуется давление свыше 200 кгс/см2 (см. рис. 5.3), что технически трудно обеспечить в экструзионном оборудовании. В связи с этим азот используется в качестве пено — агента только при получении из полистирола экструзионных вспененных пленок толщиной до 500 мкм.
Углекислый газ, в отличие от азота, характеризуется удовлетворительной Генри растворимостью в полистироле (=15 см3/г при
давлении 80 кгг./см2). Однако низкий коэффициент диффузии С02 (см. табл. 5.2) снижает скорость его десорбции при формировании пеноизделий на заключительных стадиях экструзии и приводит к получению повышенной плотности изделий (более 40 кг/м8).
Углекислый газ применяют при производстве из полистирола методом экструзии листов толщиной 1-5 мм, а также как добавку к фреону при выпуске пенополистирольных плит толщиной 20 мм и более с целью повышения их плотности и соответственно прочности.
Высокое значение Генри растворимости углеводородов С4-С5 в полистироле приводит к тому, что при формовании пеноизделий часть пор становится открытыми. Это снижает теплоизоляционные свойства пеноплит и их влагостойкость.
Использование предельных углеводородов С4-С5, обладающих высокими сорбцией и диффузией по отношению к полистиролу, затруднено практически, так как связано с необходимостью обеспечения условий взрывобезопасности экструзионного оборудования, производственных помещений, включая склады хранения готовых пеноизделий.
С точки зрения теплоизоляционных свойств пеноплит, полученных на основе различных пеноагентов, существенными преимуществами обладают плиты, полученные на основе фреонов (рис. 5.8), так как фреоны обладают наименьшим коэффициентом теплопроводности среди рассмотренных пеноагентов.
Таким образом, использование галогенпроизводных углеводородов в качестве пеноагентов при получении теплоизоляционных пеноплит является оптимальным, ибо в процессе экструзии обеспечивается получение пеноплит закрытой ячеистой структуры, в которой длительное время сохраняется определенная доля фреона. Низкая теплопроводность фреона обеспечивает пониженную теплопроводность пенополистирольных плит (ЭПС), получаемых на его основе методом экструзии. Пеноплиты (ВПС) на основе смеси пентана с изопентаном уступают им по этому показателю.
Наиболее широко распространенным пеноаген — том, используемые в производстве пенополистирольных плит, получаемых экструзионным методом, является
Рис. 5.8. Диаграмма влияния пеноагентов на теплопроводность пенополистирольных плит
Фреон фреон С02 °оздух 142в, 22 152а, 134а
Смесь фреонов 142в (СН3СС№2) и 22 (СНС1Р2) состава 60 : 40. Эта смесь обеспечивает низкую теплопроводность пеноплит в течение длительного времени (более 20 лет), благодаря низкой скорости диффузии фреона 142в. 1
В качестве альтернативы смеси фреонов 142в и 22 представляет интерес смесь Фреонов 152а и 134а в соотношении -70 : 30, обладающая меньшим парниковым эффектом.
Основные характеристики указанных смесей фреонов и углекислого газа приведены в табл. -5.3.
Таблица 5.3 Характеристики агентов вспенивания при получении пенополистирольных плит экструзионным методом
|
Смесь фреонов 152а и 134а по сравнению с фреонами 142а и 22 обладает в 2 раза меньшей проницаемостью по отношению к полистиролу и повышенным коэффициентом теплопроводности.
С целью повышения раствооимости в полистироле смеси фреонов 152а и 134а в качестве добавк I, способствующей повышению сорбции пеноагента полистиролом, используются спирты или кето — ны, например этиловый спирт [7-9]. Анализ патентов показывает, что смесь фреонов 152а и 134а може ‘- быть эффективным агентом вспенивания при получении пенополистирольных плит методом экструзии, при этом увеличение теплопроводности плит не превышает 10 % и остается существенно ниже, чем для члит, получаемых с использованием в качестве пеноагента воздуха или пентанов.
Использование углекислого газа в качестве пеноагента не может быть альтернативной заменой смеси фреонов 142в и 22, так как высокое давление газа приводит к образованию значительного количества открытых пор, что, наряду с повышением теплопроводности, приведет к потере теплоизоляционных характеристик пеноплит, получаемых экструзионным методом.
Аппаратурно-технологическое оформление процесса получения пенополистирольных плит методом экструзии можно разделить на две основные группы, схематически изображенные на рис. 5.9:
1. Установки тандемного типа, состоящие из двух последовательных экструдеров (рис. 5.9, а, б). Первый экструдер предназначен для плавления исходного полистирола и смешения его с добавками. На выходе из первого экструдера происходит смешение расплава полистирола с пеноагентами, подаваемыми под давлением специальными насосами. В качестве первого экструдера плавления первоначально использовался одношнековый экструдер (рис. 5.9, а). По мере развития производств он был заменен двухшнековым экструдером (рис. 5.9, б). Второй (одношнековый) экструдер предназначен для охлаждения расплава, его тщательного перемешивания с целью обеспечения однородной прочности расплава и подготовки его к процессу формирования плит.
А
Двухшнековый экструдер плавления и смешения с добавками |
| |
| |
| |
Экструдер охлаждения и гомогенизации расплава
Экструдер охлаждения и гомогенизации расплава
Зона плавления |
Статический Теплообменник |
| |
| |
Рис. 5.9. Схематическое изображение типов экструзионных линий, используемых для получения полистирольных пеноплит:
А, б — тандемные установки из двух экструдеров. Охладитель расплава — динамический в виде второго одношнекового экструдера специальной конструкции; в, г — моноэкструзионные установки (б — двухшнековый экструдер, совмещенный с динамическим охладителем расплава; г — двухшнековый экструдер для плавления. Охладитель расплава статического типа)
Рис. 5.10. Влияние температуры и содержанья фреона на вязкость полистирола:
105 100 120 140 160 180 200 Г, ”С |
I — полистирол оез фреона; — о — 2 — полистирол с 5 % фреона; — Д — 3 — полистирол с 20 % фреона
2. Моноэкструзионные установки с испотьзоъанием двухшнековых экструдеров (рис. 5.9, в, г) и статических смесителей для стабилизации и охлаждения расплава.
Первоначально в производстве пеноплит появились именно тандемные установки. Наличие независимого экструдера плавления позволяет осуществлять смешение исходного полистирола в расплаве с индивидуальными добавками: антипиренами, красителем, тальком, который играет роль физического зародышеобра — зователя, способствующего образованию пор.
Смешение расплава полистирола с адсорбционно активными средами, например с фреоном, приводит к снижению поверхност ного натяжения на границе раздела расплав полимера — фреон и, следовательно, к существенному снижению вязкости расплава (рис. 5.10). Это позволяет обеспечивать транспортировку расплава уже при температуре 110-140 °С вместо 180—190 °С, т. е. стабилизация смеси полимера с пеноагентом происходит при высокоэластическом состоянии полимера.
Создание и развитие производств двухшнековых экструдеров явилось технической базой для организации моноэкструзионных установок получения пенополистирольных плит (рис. 5.9, в, г). В этом случае экструзионная линия состоит из одного двухшнекового экструдера, в котором первые зоны являются зонами плавления полистирола и его смешения с добавками, затем после зоны сжатия происходит охлаждение расплава, сопровождаемое подачей вспенивающего агента.
Наличие эффективных зон смешения расплава полимера с агентом вспенивания в двухшнековом экструдере обеспечивает однородность расплава и его надежную транспортировку при температуре 120-140 °С.
Концентрация добавляемого агента вспенивания зависит от толщины получаемых экструзионных изделий. Так, при производстве вспененных пленок и листов толщиной до 3-4 мм содержание фреона находится на уровне =10 % (мае.). При получении пеноплит толщиной более 20 мм содержание фреона увеличивается до 16-18 % (мае.).
Первоначально в моноэкструзионных установках получения пеноизделий охлаждение расплава производилось ь динамических теплообменных устройствах (рис. 5.9, в), совмещенных со шнеками основного двухшнекового экструдера. Разработка эффективных устройств смешения расплава в статических условиях позволила в экструзионных линия? получения пеноплит на основе двухшнеко — вого экструдера (рис. 5.9, г) использовать для охлаждения расплава статические смесители вместо динамических. Использование статических смесителей для охлаждения и гомогенизации смеси расплава полимера с агентом вспенивания максимально снижает турбулентность расплава и повышает его однородность по сравнению с использованием экструдера для охлаждения расплава на тандемных установках. Статические смесители специальной конструкции, предназначенные для охлаждения и гомогенизации, непосредственно прифланцовываются к двухшнековому экструдеру.
На стадии гомогенизации под действием напряжения, создаваемого экструдером, начинает развиваться процесс жидкого крей — зинга в полимере под воздействием пеноагентов, играющих роль ААС. Наличие направленногс воздействия на полимер, создаваемого во втором экструдере тандемных установок (рис. 5 9, а, б), вызывает нарушение ламинарности потока и может приводить к зарождению неоднородной структуры на начальном процессе жидкого крейзинга.
После гомогенизации смесь поступает в фильеру. На этой стадии начинается процесс формирования пеноиздетшй. Тип получаемого пеноизделия определяется конструктивными особенностями фильеры:
— плоская фильера предназначена для получения пеноплит толщиной 20-150 мм;
— кольцевая фильера — для производства пленок и листог толщиной 0,3-0,4 мм;
— профильная фильера — для изготовления декоративных профилей;
— стренговая фильера — для изготовления гранул диаметром до 4 мм.
Приобретение опыта по созданию производств концентратов позволило отказаться от использования индивидуальных добавок в производстве пеноизделий и перейти к применению их в виде 40-50 % — х концентратов на основе полистирола.
Использование добавок в виде концентратов с экологической точки зрения обладает рядом преимуществ: снижается образование пыли, повышается точность дозировки добавок, исключается стадия предварительного смешения добавок с исходным полистиролом. В установках тандемного типа, имеющих одношнековый экструдер плавления, использование концентратов для смешения с расплавом полистирола невозможно, так как одношнековые экструдеры не обеспечивают однородного смешения.
Моноэкструзионные установки на базе двухшнекового экструдера, снабженного статическим охладителем и гомогенизатором расплава, являются более прогрессивными по сравнению с установками тандемного типа. Одним из основных производителей мо — ноэкструзионных установок является фирма «LMP» (Италия), ко торая выпускает установки производительностью до 600 кг/ч.
Технологическая схема моноэкструзионной установки производства пенополистирольных плит методом экструзии представлена на рис. 5.11.
Технологический процесс получения пеноплит на моноэкстру- зионных установках на основе двухшнекового экструдера состоит из следующих основных стадий и узлов:
1. Хранение исходного сырья, добавок и отходов.
2. Предварительное смешение концентратов различных добавок.
3. Дозирование исходного сырья и смеси добавок в основной двухшнековый экструдер.
4. Плавление исходного полистирола и добавок в двухшнековом экструдере и смешение расплава с пеноагентом.
5. Охлаждение расплава в теплообменнике статического типа.
6. Гомогенизация расплава в гомогенизаторе статического типа.
7. Подготовка расплава к формированию пеноплит в фильере.
8. Формирование пеноплит в кали&раторах.
9. Разрезание и обработка краев пеноплит.
10. Сбор, грануляция отходов и их возврат ь основной процесс.
Хранение исходного полистирола в виде гранул осуществляется в специальных цилиндрических емкостных силосах, снабженных сигнализаторами верхнего и нижнего уровня и циклонами для улав — яивания пыли. Хранение отходов, образующихся при обработке пеноплит и утилизации некачественных изделий, получаемых при пуске установки, также производится в силосах аналогичного типа. В нижней конической части силосы оборудованы специальными камерами всас ывания, через которые с помощью вакуума осуществляется подача гранул в питающие бункеры основного производства.
Все добавки, необходимые для получения пеноплит, вводятся в основное производство в виде 10-40 %-х гранулированных концентратов с полистиролом.
Гранулы исходного полистирола, возвратного полистирола и концентратов должны иметь цилиндрическую форму с размерами: диаметр (2-3) мм, длина (3-5) мм. Возвратный полистирол может иметь вид щепы.
Рис. 5.11 Принципиа пьная технологическая схема получения пеноплит экструзионным методом в двухшнеко — вом экструдере со статическим теплообменником |
Хранение концентратов добавок осуществляется на складе в мешках
Агенты вспенивания или их смеси хранятся в специальных емкостях при повышенном давлении (до 12 кгс/см2), которые снабжены манометром, предохранительным клапаном и уровнемером. Емкости хранения пеьоагента имеют циркуляционный контур, с помощью которого обеспечивается поддержание постоянного давления при хранении и подаче пеноагентов в основное производство.
Концентраты добавок в определенном заданном количестве вручную загружаются из мешков в вертикальный предварительный смеситель, снабженный мешалкой шнекового типа с импеллером в нижней части. После кратковременного смешения смесь концентратов добавок перегружается в промежуточный бункер для смеси добавок (см рис. 5.11).
Как правило, прл получении пенополистирольных плит используются концентраты талька, красителя и антипирена.
Дозирование исходного полистирола, возвратного полистирола и смеси концен гратов в питающую воронку основного экстру дера из питающих бункеров производится с помощью непрерывных весовых дозаторов шнекового типа. На входе в основной экструдер вмонтирован металлоискатель для удаления посторонних металлических примесей. Система подачи твердых компонентов должна быть сконструирована таким образом, чтобы исключить образование пыли при транспортировке гранул. Наличие пытга в исходном сырье нарушает работу непрерывных весовых дозаторов.
Дозирование агента вспенивания в зону смешения основного экструдера производится специальным высоконапорным 3-х сту пенчатым дозировочным насосом диафрагменного типа, создаю щим давление до 100 кгс/см2. Непосредственная подача агента вспенивания в зону смешения экструдера, находящегося под давлением 50-70 кгс/см2, производится игольчатым клапаном, открытие которого происходит автоматически — при достижении на нем давления 100 кгс/см2.
Основной экструдер получения пеноплит представляет собой двухшнековый экструдер с отношением длина : диаметр = 32, который имеет 8 зон регулирования температуры. Шнеки экструдера вращаются двигателем постоянного тока в одном направлении.
Шнеки состоят из наборных элементов различной конструкции по каждой из зон. Внутри шнека каждой зоны имеются спе — циа льные проточки, предназначенные для циркуляции теплоносителя, обеспечивающего регулирование температуры по зонам экструдера.
Непосредственно к экструдеру прифланцован теплообменник, представляющий собой многозаходный статический смеситель специальной конструкции, предназначенный для удаления избы точной тепловой энергии из полимера и стабилизации температуры полимера. К теплообменнику примыкает гомогенизатор, являющийся также статическим смесителем простейшей конструкции, 3 гомогенизаторе происходит окончательная стабилизация температуры расплава до величины, характерной для перехода полимера в высокоэластическое состояние, и обеспечивается однородность реакционной массы. После гомогенизатора расположена щелевидная фильера, имеющая три зоны (корпус, головка и губы) регулирования температуры. Температура на губах фильеры поддерживается на 10-15 °С ниже температуры размягчения полистирола, так как на этой стадии начинается формирование пено — плит
Регулирование температуры по зонам экструдера, в теплообменнике, гомогенизаторе и фильере осуществляется с помощью специальных контуров охлаждения. В первом контуре в качестве теплоносителя используется обессоленная вода, а в двух других — высокотемпературный органический теплоноситель (ВОТ). Теплоносители в контурах охлаждения находятся в замкнутых циклах. Поддержание температуры теплоносителя в каждом контуре обеспечивается за счет циркуляции захоложенной воды через теплообменные устройства, вмонтированные в эти контуры.
Первый контур охлаждения, работающий на обессоленной воде и обладающий наиболее высокой теплопередачей, предназначен для регулирования температуры в зонах смешения расплава полимера с агентом вспенивания (зоны 4, 5 экструдера), а также на губах фильеры.
Второй контур, работающий на ВОТ с высокой температурой, обеспечивает регулирование температуры в зоне п, [авления полимера и подачи пеноагента (зоны 2, 3 экструдера), а также в транспортирующих зонах экструдера (6-8).
Третий контур регулирует температуру в теплообменнике, гомогенизаторе, корпусе и на головке фильеры.
В основном экструдере происходит ряд сложных сЬизико-хи- мических процессов, необходимых для последующего формирования пеноплит.
В первой зоне экструдера при температуре 200-210 °С происходит плавление полистирола с добавками с целью перевода полимера в вязко-текучее состояние. Во второй зоне экструдера (зона сжатия), где поддерживается температура 220-230 °С, происходит смешение в расплаве полистирола с добавками, возвратным полимером и создается давление, необходимое для транспортировки
Расплава полимера с добавками. В конце второй зоны экструдера на шнеках имеются специальные сегменты, предотвращающие появление обратных потоков и попадание во вторую зону экструдера агента вспенивания.
В третьей зоне экструдера (зона сжатия) при температуре 215- 220 °С под давлением осуществляется ввод агентов вспенивания.
В четвертой и пятой зонах экструдера температура расплава снижается до 85 -95 °С для предотвращения роста давления и начинается процесс смешения расплава полимера с агентом вспенивания. Растворимость пеноагента в расплаве полимера зависит от температуры и давления, а также от природы агента вспенивании и молекулярной массы исходного полимера. Введение 15-20 % фреона, являющегося агентом вспенивания, снижает вязкость расплава полимера (см. рис. 5.10) так, что ее величина при 120-130 ПС становится равной вязкости расплава полистирола при 180-190 °С. Это обеспечивает надежную транспортировку полимера вблизи его температуры размягчения, т. е. в высокоэластическом состоянии. Наличие частиц талька в расплаве полимера обеспечивает появление неплотностей или «дырок» в вязкой жидкости, способствующих проникновению агента вспенивания и повышению его Генри растворимости.
В зонах 6-8 экструдера при постепенном снижении температуры от 140 до 100-105 °С происходит динамическое смешение раси пава с пениагеятом и его одновременное охлаждение.
Окончательное охлаждение реакционной массы завершается в теплообменнике — многозаходном статическом смесителе, в котором поддерживается температура 85-95 °С. В данных условиях агент вспенивания в виде жидкости на этой стадии уже начинает играть роль адсорбционно активной среды (ААС), способствующей проявлению процесса жидкого крейзинга. Можно предположить, что именно на этой стадии начинается процесс инициирования крейз.
В гомогенизаторе при температуре 110-120 °С достигается стабилизация структуры и состава расплава с целью повышения его однородности и прочности. Возможно, на этой стадии происходит рост крейз, инициированных ААС После гомогенизатора полимер, находящийся в высокоэластическом состоянии, продавливается через фильеру, в головке и корпусе которой поддерживается температура =120 и 100 °С соответственно. Пребывание полимера в гомогенизаторе и фильере в высокоэластическом состоянии способствует не только повышению прочности расплав?, но и увеличивает сорбционную способность по иистирола, повышая Генри растворимость фреона в микронеоднородных структурных зонах полимера.
Важным фактором для обеспечения однородности расплава на этих стадиях является приближение течения полимера к ньютоновскому. Повышение однородности полимера по молекулярной массе (сужение ММР) способствует его текучести как ньютоновской жидкости. Стабильность давления, действующего на полимер в гомогенизаторе и фильере, является важным фактором, позволяющим исключить турбулентность при течении. В этом отношении процесс охлаждения расплава полистирола в статических условиях обладает реальными преимуществами по сравнению с динамическим охлаждением в установках тандемного типа.
Использование двухшнекового экструдера в моноэкстоузион- ных установках для получения пеноплит обеспечивает лучшее смешение расплава полистирола с добавками и агентом вспенивания по сравнению с одношнековым экструдером.
Стабилизированный при температуре 100-120 °С вязкий «раствор» полистирола после фильеры п подавливается через ее губы при температуре 75-85 °С. На этой стадии начинается формирование пеноплиты, так как при выходе из фильеры агент вспенивания мгновенно вскипает, что способствует охлаждению полимера и его одновременному вспениванию. Температура губ фильеры поддерживается несколько ниже температуры стеклования полимера для предотвращения его перехода в хрупкое состояние при мгновенном охлаждении при вспенивании. Для предотвращения налипания расплава губы фильеры имеют тефлоновое покрытие, которое обновляется через 15-20 сут непрерывной работы линии.
С физико-химической точки зрения на выходе расплава полимера из губ фильеры под действием растягива: )щего напряжения, создаваемого тянущими устройствами (волочильнями), завершается процесс жидкого крейзинга. На этой стадии крейзинга происходит коллапс крейз, приводящий к образованию микро — пор, в которых капсулируется агент вспенивания.
Образование микропор при однородности расплава и его повышенной пбочности протекает стабильно. Сужение ММР полимера и повышение его молекулярной массы способствуют получению пор, однородных по размеру, с одновременным повышением прочности их стенок.
После выхода с фильеры первоначально сформированная плита под действием напряжения, создаваемого волочильнями, проходит первую стадию созревания через систему трех калибрационных плит, нагретых до температуры, соответствующей хрупкости полимера (75- 80 °С).
При калибрации протекает процесс дальнейшего образования микрочор с одновременной десорбцией агента вспенивания. Поверхность первого калибратора также имеет тефлоновое покрытие для исключения налипания полимера. При калибрации на поверхности пеноплит образуется тонкая пленка гомополимера, что обеспечивает повышение прочности пеноплит.
После калибрации полученная пеноплита охлаждается при транспортировке ее по роликовому каландру. Затем в специальных камс рах происходит разрезание плит по длине и обработка их краев для обеспечения максимального удобства использования полученных изделий в качестве эффективной теплоизоляции.
При получении пеноплит на тандемных установках в качестве исходного полистирола используется полимер с более низкой молекулярной массой, чем на моноэкструзионных установках. Это обусловлено тем, что в одношнековых экструдерах не обеспечивается однородное смешение высокомолекулярного полистирола с добавками.
Под действием сдвиговых напряжений, создаваемых в экструдере охлаждения на тандемных линиях, нарушается ламинарное течение полимера. Это способствует появлению неоднородностей в микроструктуре не только полимера в высокоэластическом состоянии при его транспортировке по экструдеру, но и при формировании пли гы. При этих условиях в плитах увеличивается число слабых мест, а снижение молекулярной массы используемо*ю полистирола снижает прочность полимерных стенок, образующих поры. В результате процесс созревания пеноплит, полученных на тандемных установках, протекает более длительно, чем на моноэкструзионных установках, а прочностные показатели пеноплит будут ниже.
Отходы, образующиеся при обработке краев пеноплит, собираются пневмотранспортом в емкости для отходов и поступаю™ в воронку специального экструдера для переработки отходов. После предварительного уплотнения измельченные отходы расплавляются в зоне плавления экструдера. Экструдер для переработки отходов также имеет зону дегазации, в которой происходит удаление агентов вспенивания. После этого расплав сжимается и через стренговую фильеру производится его грануляция. Гранулированный возвратный полимер, содержащий твердые добавки (тальк, краситель, антипирен и др ), поступает в силос хранения отходов возвратного полимера и добавляется к исходному полистиролу при получении пеноплит
При обработке полимера в основном экструдере и при переработке отходов происходит механическая деструкция полимера, в результате которой показатель текучести расплава возвратного полимера увеличивается в 2-2,5 раза. С целью снижения деструкции целесообразно добавлять при получении пеноплит термостабилизаторы, наличие которых снижает разрушение полимера под термическим и механическим воздействием.
Рис. 5.12. Влияние структурных характеристик талька на распределение микро — г. ор в пенополистирольнь’х плитах. Содержание талька 2,3 %:
1 — размер микрочастиц талька 120-140 мкм; — О — 2 — иазмер микрочастиц талька 30- 80 мкм; — Л — 3 — тальк с бимодальным размером микрочастиц: 30-80 и 120-140 мкм
Анализ показывает, что на установках тандемного типа меха но-химическая деструкция полистирола протекает в большей степени, о чем свидетельствует увеличение показателя текучести расплава возвратного полистирола в 3-3,5 раза.
Изучение влияния особенностей получения пенополистироль- ных плит на формирование их структуры позволяет выявить наличие корреляции между размерами микрочастиц талька и распределением по размеру микропор, образующихся в плитах (рис. 5.12). Наличие этой зависимости свидетельствует о том, что тальк является физическим нуклезатором и способствует образованию дефектов в расплаве полимера. В этих микродефектных зонах концентрируется агент вспенивания. При переходе расплава полимера в состояние высокоэластичности (на стадии охлаждения и гомогенизации) возникшие микрообласти, содержащие агент вспенивания, превращаются в зоны развития жидкого крейзинга. Анализ концентрации талька в полимере при получении плит показывает, что каждая микрочастица талька размером 140 мкм образует в полимере до 104 пор аналогичного размера. Снижение размера микрочастиц талька до 20- 30 мкм уменьшает размер пор и увеличивает количество пор, образующихся в полимере, больше чем на порядок. Улучшение микроструктуры пеноплит и снижение размера микропор при одновременном повышении их однородности обеспечивают повышение прочностных показателей пеноплит [10]. Установлено, что снижение размера микрочастиц талька до 20-30 мкм обеспечивает получение пеноплит с прочностью при 10 %-м сжатии до 0,5-0,6 МПа при плотности 40-42 кг/м3. Использование талька с размером микрочастиц 120-140 мкм позволяет получать плиты с прочностью не более 0,4 МПа. Использование в качестве промоторов веществ, обладающих высокой пористостью и соответственно сорбционной способностью, налример у-окиси алюминия в минимальных количествах (0,1 %) (рис.
5.13), повышает однородность распределения микропор в пеноплитах. Увеличение
Рис. 5.13. Влияние добавки промотора порообразования у — окиси алюминия на распределение микропор в пенопо лигтролыдах плитах при содержании талька 2,3 %:
20 40 60 80 100 120 140 160 |
1 -тальк без промотора; — о — 2
— тальк с промотором (у-окись алюминия 0,1 %)
Содержания талька при получении пеноплит способствует оптимизации распределения микропор в пеноплитах (рис. 5.14).
Вещества, обладающие сорбционной активностью, например у-окись алюминия, оказывают большее влияние на повышение однородности микропор в плитах, чем тальк. Так, добавка 0,1 % у-окиси алюминия по эффективности воздействия на микроструктуру плит аналогична увеличению содержания талька с 2,3 до 2,7 %. Увеличение концентрации талька выше некоторой критической величины недопустимо, так как происходит нарушение стабильности расплава.
При получении пеноплит на моноэкструзионных установках существенное влияние на их качество оказывает температура в гомогенизаторе, которую необходимо поддерживать на 10-15 °С выше температуры размягчения полистирола. Эта темпера-урэ зависит от показателя текучести расплава полистирола. Плотность получаемых пеноплит при этом уменьшается, так как повышается прочность стенок и снижается количество дефектных пор, разрушающихся при созревании плит (рис. 5.15).
Стабильность ьязкотекучего и высокоэлас! ичегкого состояний полимера при получении пеноплит являются решающими параметрами для получения плит высокого качества. Об этом свидетельствует снижение плотности получаемых плит при повышении скорости вращения экструдера (рис. 5.16) при сохранении неизменным его литания. Это явление объясняется тем, что с увеличением скорости вращения шнеков
Рис. 5.14. Влияние концентрации талька на распределение микропор в пенополисти- польных плитах:
1 — содержание талька 2,3 %;
-О — 2 — содгржапие талька 2,7 %
Н Рис. 5.15. Зависимость те. лпера-
О туры в гомогенизаторе и плотно-
Н сти плит от показателя текуче-
£ сти расплава (ПТР) исходного
Полистирола:
1 — температура в гомогенизаторе; — О — 2 — плотность плит
Основного экструдера повышается и стабилизируется давление перед теплообменником. Прочность получаемых при этом пено — плит несколько повышается и стабилизируется. Одновременно происходит снижение плотности пеноплит.
Обобщение технологических особенностей получения пенопо- листирольных плит показывает, что использование статических смесителей для охлаждения полимера и стабилизации его однородности на стадии высокоэластического состояния имеет решающее значение для оптимизации производства пеноплит. Анализ патентных данных [11] показывает, что использование статических смесителей в производстве пеноизделий является наиболее перспективным. Так, фирма «Зульцер» [11] запатентовала процесс смешения расплава полистирола с физическими нуклезаторами и последующего насыщения расплава предельными углеводородами в статических смесителях специальной конструкции. Грануляция под давлением такого расплава полистирола с пеноагентом позволит получать полистирол для вспенивания в виде гранул, а в перспективе — совместить процесс получения полистирола и пеноплит в едином технологическом потоке.
Рис. 5.16. Зависимость плотности плит «Пеноплэкс-45» (1) и производительности их выпуска (2) от скорости вращения шнека основного экс — трудеоа со:
1 — плотность, кг/м3;
-о — 2 — производительность, м3/ч
(О, об/мин
Сопоставление тандемных и моноэкструзионных установок при получении пенополистиролиных плит методом экструзии свидетельствует о наличии ряда технологических преимуществ моноэкструзионных установок на базе двухшнекового экструдера со статическими смесителями на стадиях охлаждения и гомогенизации:
— смешение полистирола с нуклезаторами и другими добавками в двухшнековом экструдере характеризуется более высокой эффективностью по сравнению с одношнековым экструдером;
— степень механо-химического воздействия на расплав полистирола снижается, так как зоны плавления в двухшнековом экструдере существенно меньше по длине;
— использование статических смесителей вместо экструдера на стадии охлаждения расплава и обеспечения его однородности перед формированием плиты позволяет исключить турбулентность расплава и способствует повышению однородности микроструктуры пеноплит;
— снижение теплосодержания в расплаве полимера перед формированием плиты за счет использования статических смесителей вместо второго экструдера охлаждения в тандемных установках сокращает время созревания пеноиаделий;
— прочностные показатели пеноизделий могут быть увеличены путем использования полистирола с повышенной молекулярной массой (низким значением ПТР).
В установках тандемного типа верхнее значение молекулярной массы полимера ограничено не только условиями его смешения с добавками в одношнековых экструдерах, но и повышением механо-химической деструкции полимера.
admin Основы технологии полистирольных пластиков
Экструзия полистирола — Справочник химика 21
Освоение технологии производства пенопластов экструзией полистирола общего назначения с вводом порообразователя в экструдер является одной из важных задач в производстве полистирольных пластиков на десятую пятилетку. [c.68] Следует помнить, что полипропилен обладает значительно более высокой жесткостью, чем полиэтилен, и затвердевает значительно быстрее последнего. Это значит, что наружный слой толстостенного изделия при быстром охлаждении становится настолько твердым, что он не оседает, когда внутренний слой охлаждается и дает усадку. При экструзии полистирола и полиметил-метакрилата усадка вызывает образование пустот в изделии. Во избежание этого необходимо, чтобы изделия, получаемые методом экструзии, охлаждались постепенно. Рекомендуется метод, при котором изделие пропускают сначала через ванну с нагретой водой, а затем постепенно через охлажденную воду. Для охлаждения некоторых видов изделий целесообразно применять воздушное охлаждение или использовать контакт с охлаждаемыми металлическими направляющими иЛи пластинами. [c.135]
Таким образом были получены соединения с новыми свойствами, Так, к полиэтилену были привиты боковые ветви полистирола. Для проведения блокполимеризации молекулы двух различных полимеров разрываются на короткие цепи (например, при вальцевании, экструзии), затем полученные блоки связываются , образуя полимер, в котором чередуются куски или блоки первого А и второго В соединений. Так, например, при взаимодействии каучука с эпоксидными смолами получается полимер, обладающий исключительной стойкостью к истиранию.
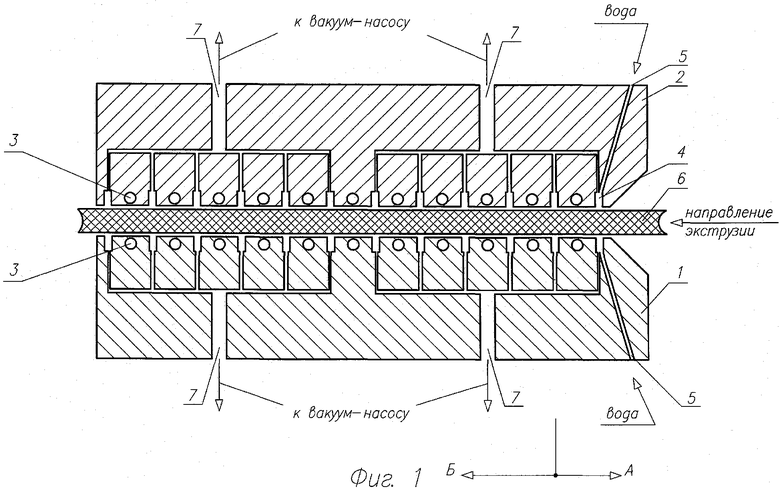
Экструзия полистирола производится при 180—190° С. Материал должен быть равномерно нагрет и состоять из частиц одинакового размера, иначе поверхность изделий из-за неравномерной усадки получается неровной и шероховатой. Толстостенные изделия могут растрескиваться в толще стенок возможно образование внутренних пустот или пузырей. Наружные слои могут затвердеть, тогда как внутренние остаются мягкими и теплыми. Это приводит к неравномерной усадке, а следовательно, к возникновению внутренних напряжений, вызывающих трещины. [c.121]
Охлаждение. Охлаждающая ванна обычно заполняется теплой водой. При экструзии полистирола температуру жидкости в охлаждающей ванне желательно поддерживать несколько выше 100° С, и поэтому иногда вместо воды применяют этиленгликоль или глицерин. Однако после прохождения такой ванны на волокнах остается часть жидкости, что приводит к дополнительным расходам, связанным с ее удалением. Поэтому иногда волокна из полистирола подвергают ориентации, минуя стадию охлаждения в жидкости. [c.180]
В охлаждающей ванне волокна должны охлаждаться до температуры, при которой их можно подвергать дальнейшей обработке. Температура волокна, выходящего из ванны, не должна быть слишком высокой, так как в этом случае при прохождении системы устройств технологической линии оно может деформироваться. Если же температура слишком низкая, падает прочность волокон. Для полипропилена и полиэтилена высокой плотности температура воды в охлаждающей ванне около 52° считается оптимальной. При экструзии полистирола требуется более высокая температура (107—135° и по крайней мере не менее 93°), и поэтому иногда в качестве охлаждающей среды применяют другие жидкости. [c.187]
Полистирол. Полистирол — продукт полимеризации стирола. Положительными свойствами его является отличная стабильность размеров, практически полная водостойкость, высокая химическая стойкость и способность перерабатывания в изделия методом литья под давлением и экструзией. Полистирол легко обрабатывается пилится, сверлится и склеивается. Изделия из полистирола сваривают горячим воздухом при температуре 220—250 С. [c.36]
Полистирольные пластмассы легко перерабатываются литьем под давлением, экструзией, вакуум- и пневмоформованием. Они легко окрашиваются в различные цвета и оттенки. Полистирол некоторых марок обладает хорошими санитарно-гигиеническими свойствами и используется для изготовления изделий, контактирующих с пищевыми продуктами. [c.82]
Ниже показано изменение молекулярной массы по длине цилиндра при экструзии полистирола при 200 °С [832] [c.358]
Листы из полипропилена, полистирола и полиэтилена обычно изготавливают методом экструзии. Листы и пленки из жесткого и пластифицированного ПВХ, так же как листы из резины, обычно изготавливают методом каландрования, так как при каландровании существенно уменьшается опасность термодеструкции. [c.20]
Полистирол перерабатывают в изделия методом литья под давлением или экструзии, реже прессованием. Изделия из полистирола обладают высокой стойкостью к растворам кислот, щелочей, солей. Литьем под давлением можно готовить из полистирола мелкие детали сложной конфигурации с многочисленной тонкой армировкой. Изготовление крупногабаритных изделий затруднительно вследствие возникновения внутри изделия усадочных раковин и растрескивания его в результате значительных внутренних напряжений. [c.806]
Б. с. получают также экструзией высоконаполненных полимеров, напр, полиолефинов, полистирола. Это самая дешевая Б. с. Применяется для печати массовых изданий на полиграфич. оборудовании, включающем устройство для обработки поверхности Б.с. коронным разрядом. Последнее необходимо для восприятия и удержания краски поверхностью пленки. [c.324]
Аналогичные изделия м. б. получены также экструзией расплава полистирола, насыщенного хладоном (т. кип. от [c.458]
Строго говоря, это деление в значительной степени условно стереорегулярные каучуки (НК, СКИ, СКД), бутилкаучук, поли-хлоропрен, способные частично (до 15—20%) кристаллизоваться [5—8], органические стекла (полистирол, поливинилхлорид, полиакрилаты) могут быть сильно ориентированы и получены в виде пленок и волокон, а такие волокнообразующие полимеры, как нейлон или капрон, могут использоваться для получения массивных изделий путем экструзии и литья под давлением [9—13]. [c.9]
Вследствие высокой текучести полистирола при повышенных температурах удобнее всего перерабатывать его методом литья-под давлением, хотя пригодны также прессование, экструзия и выдувание. Известное применение нашла механическая обработка блоков и пластин из полистирола в производстве линз и электротехнических деталей. Пленки, полученные путем выдувания, непрочны, но если этот процесс сопровождается продольной вытяжкой (ориентация), прочность негибкость их резко возрастают. Полистирольные волокна, уступая полиолефиновым, например по-эластичности, обладают другими ценными свойствами (упругость, прозрачность), что позволило применять их в волоконной оптике, электротехнике и производстве армированных пластиков. [c.287]
Получение ударопрочного полистирола суспензионным методом осуществляется по полунепрерывной схеме и включает следующие основные стадии растворение каучука в стироле, форполимеризацию до 25—30%-ной конверсии с перемешиванием, суспензионную полимеризацию (периодические стадии), далее промывку, отжим, сушку, смешение с красителями, стабилизаторами и другими добавками, экструзию, грануляцию и упаковку (непрерывные стадии). [c.90]
Ударопрочный полистирол перерабатывается в изделия обычными для термопластов методами, и в первую очередь экструзией и литьем под давлением. Из ударопрочного полистирола можно получать листы, которые затем перерабатываются в крупногабаритные изделия вакуум- и пневмоформованием. Листовые материалы могут перерабатываться горячей штамповкой. [c.93]
Допустим, что лист из полистирола получают методом экструзии в водяную ванну. Затем из листа вырубают изделия, причем требования к точности размеров этих изделий таковы, что максимально допустимая величина изменения линейных размеров за счет усадки не должна превышать 0,33%. [c.80]
ДЕСТРУКЦИЯ ВЫСОКОМОЛЕКУЛЯРНОГО ПОЛИСТИРОЛА ПРИ ЭКСТРУЗИИ [c.191]
Деструкция полистирола при экструзии [c.193]
Грессли с сотр. [22] установил, что при экструзии полистирола со скоростью 1—3 мм/с при 160—180 °С степень ВЭВ DIDq на расстоянии 0,1 см от выхода из капилляра составляет 90 % от максимальной. Остальные 10 % ВЭВ развиваются на расстоянии 3 см от выхода из капилляра. Что же представляет собой обратимая деформация на участке длиной 0,1 см [c.474]
Ранее в лаборатории авторов были выполнены исследования il] деструкции при экструзии полистирола со средневесовым молекулярным весом М , 6,7-10 и узким молекулярновесовым распределением (МВР). Опыты проводили с помощью капиллярного реометра Instron , который использовался в качестве приспособления для создания высоких скоростей сдвига, моделирующих реальный процесс переработки полимера в изделие. Для оценки МВР образцов после экструзии использовали метод гель-проникающей хроматографии. Эту же методику использовали и в настоящей работе при исследовании высокомолекулярного образца полистирола с 1,8-10 . При этом варьировали различные параметры процесса, что позволило получить некоторые результаты, отличные от описанных ранее. [c.191]
Наиболее современным и прогрессивным является метод плоскощелевой экструзии полистирола с последующей двухсторонней вытяжкой пленки-заготовки. Аппаратурное оформление этого процесса аналогично процессу получения двухосноориентированной полипропиленовой пленки. Этим методом достигается одинаковый ориентационный эффект в обоих направлениях, ширина полотна увеличивается до l500 мм при толщине 0,02—0,5 мм. [c.51]
Наши опыты охватывали сравнительно узкую область скоростей сдвига (до 10 сек ). Такие значения скоростей сдвига наблюдаются при экструзии полистирола. В условиях же литья под давлением реализуются гораздо более высокие скорости сдвига. Кроме того, процесс литья под давлением проходит в неизотер- [c.35]
Отделение химии и химической технологии Заведующий S. otson Направление научных исследований изучение строения веществ с помощью рентгеновской дифракции гомогенные реакции в газовой фазе химия соединений олова и серы химия сиднонов окисление метанола кинетика реакций поликонденсации влияние пластификаторов на поливинилхлорид экструзия полистирола неорганические полимеры. [c.252]
Пластмассы могут быть термопластичными и термореактивными. Термопластичные пластмассы при нагревании становятся пластичными, а при охлаждении снова затвердевают. Размягчение и отверждение можно проводить многократно. К таким пластмассам относятся полиэтилен, полипропилен, полистирол, полиметилметакрилат, полиамиды, фторопласты и др. Изделия из них получают литьем под давлением, экструзией, штампозание. м. [c.319]
Рабочая температура выбирается внутри диапазона, ограниченного минимально и максимально допустимыми значениями температуры. Низкие температуры термоформования более выгодны, поскольку они позволяют сократить периоды нагрева и охлаждения в цикле формования. Кроме того, чем ниже температура, тем выше уровень двухосной ориентации, а значит, выше ударная вязкость изделия. С другой стороны, более высокая температура позволяет увеличить воспроизводимость и точность размеров изделий. Обычно для термоформования используют экструзионные листы. Щелевая экструзия приводит к возникновению неизотропной молекулярной ориентации. Так, в случае экструзионного листа из ударопрочного полистирола толщиной 1,52 мм Шмидт и Карли [24] наблюдали 31 %-ную усадку в направлении экструзии и очень сдабую усадку [c.574]
Поскольку критерий Флори зависит от термодинамических и механических поправок, можно ожидать, что в определенных условиях течения сравнительно малые градиенты скорости у компенсируются большими термодинамическими поправками . По-видимому, впервые прямым образом это было показано Келлером , который при экструзии промышленного блоксополимера кратон , содержащего два концевых полистирольных блока, сочлененных полибутадиеновым (полная мольная доля полистирола 25% блок-сополимер практически гомодисперсен), получал макроскопические, размерами в несколько кубических миллиметров, суперкристаллы с правильной гексагональной упаковкой практически бесконечных полистирольных цилиндров диаметром порядка 15 нм в полибутадиеновой матрице. [c.223]
ПЛЕНКИ ПОЛИМЕРНЫЕ, имеют толщину от неск. мкм до 0,25 мм. В зависимости от метода и условий получения м. б. неориентированными (изотропными) и ориентированными. Получ. след, способами 1) экструзией расплавов полимеров (полистирола, полиэтилена, полипропилена, хлориров. полиолефинов и других полимеров, не подвергаюптхся деструкции при переходе в вязкотекучее состояние) через фильеры со щелевыми или кольцевыми отверстиями при этом в первом случае из фильеры выходит изотропная лента бесконечной длины, к-рую вытягивают в продольном и (или) поперечном направлениях, во втором — рукав, к-рый раздувают сжатым воздухом (плоскостная ориентация) 2) из р-ров полимеров (напр. , эфиров целлюлозы, гл. обр. ацетатов), к-рые через фильеру наносят на движущуюся ленту или барабан (сухое формование) либо направляют в осадит, ванну (мокрое формование) структуру и св-ва пленок регулируют скоростью испарения р-рителя, составом и т-рой ванны сформованную пленку часто пластифицируют, а затем высушивают 3) каландрованием пластифицированных полимеров (главным образом поливинилхлорида). [c.448]
Сочетание разл. методов. Напр., экструзией и ка-ландрованием получают толстые П. п. (0,2-2,5 мм) из ударопрочного полистирола, АБС-пластика, полипропилена, к-рые подвергают глубокой вытяжке, и П.п. из нек-рых термостойких термопластов. [c.572]
Основным методом изготовления выдувной тары из полиэтилена высокой и низкой плотности, попипропилена, полистирола, твердого и мягкого (пластифицированного) поливинилхлорида, ацетата целлюлозы, полиамида и различных сополимеров является экструзия с раздувом, т.е, выдувное формование. Данный способ основан на раздуве нагретой заготовки кз термопласта, помешенной в форму определенного объема и конфигурации. Раздув разогретых заготовок производится обычно сжатым воздухом, после раздува отформованные изделия охлаждают. [c.167]
Интересным методом регулирования структуры является метод введения в расплав полимера искусственных зародышей, которые становятся центрами кристаллизации. Ими могут быть разли шые органические вещества, нерастворимые в полимере, плавящиеся при более высоких температурах, чем сам полимер, и химически ие взаимодействующие с ним, например иидиго. ализарин и т. д. При Этом можно получить разнообразные надмолекулярные структуры одного и того же полимера, так как они зависят от формы введенных кристалликоп. Так, введение 1% тоикодисперсного индиго в расплав полипропилена при экструзии приводит к образованию пленок с однородной мелкосферолитной структурой. Пленки, полученные при тех же условиях в отсутствие искусственных зародышей, состоят из крупных сферолитов с четкими границами раздела. Первые обладают вынужденной эластичностью, вторые разрушаются Хрупко. Аналогичные данные получены для изотактиче-ского полистирола н гуттаперчи. [c.239]
Самозатухакцций слоистый пластик на основе фено-ло-форм альдегидных смол То же на основе эпоксидных смол Сополимер винилхлорида Дисперсии ПВА Полистирол для экструзии Ненасыщенные полиэфирные смолы Пленка нз ПВХ Шпатлевка иа основе ПВА [c.286]
Рациональное применение полимеров в конструкциях значительно увеличивает долговечность этих конструкций. Рассмотрим характерные примеры использования термопластов в химической и иефтехимической промышленности [50, 151]. Наиболее широкое распространение в этих отраслях получили напорные трубы из полиэтилена, полипропилена, винипласта и фторлона. Весьма перспективны также трубы из полиамидов, полистирола, поликарбоната, полиформальдегида и т. д. Оболочки и емкости больших размеров с толщиной стенок до 25 мм получают методом экструзии, центробежного литья и спиральной намотки [202]. [c.13]
Полистирол марок ПВФГ и ПОГ имеет с одной стороны глянцевую поверхность, Листы изготовляют непрерывной экструзией из гранулированного ударопрочного полистирола, выпускаемого по ТУ 6-05-1604—72. Размеры листов должны удовлетворять требованиям, приведенным в таблице на стр. 95. [c.93]
Биориентированная пленка (полифлекс, стирофлекс). Этот продукт был разработан с целью уменьшения хрупкости полистирола при его использовании в виде тонких пластин. Изготавливаются такие пленки экструзией тонкого листа или трубки полистирола, находящихся под натяжением в пластическом состоянии и затем также под натяжением охлаждаемых. [c.155]
Зависимость механич. свойств смеси от размера частиц изучена слабо. Установлено только, что прочность смеси мало изменяется при изменении размера частиц в пределах от 1 до 50 мкм. По-разному влияет на свойства смесей и анизометричность частиц дисперсной фазы. Обычно в смеси полимеров, снятой с вальцев или с экструдера, прочность в направлении ориентации иа 20—100% выше, чем в перпендикулярном направлении. Анизометричные частицы каучука в смесях с поливинилхлоридом обеспечивают более высокую ударную прочность, чем сферические. Однако существуют и др. двухфазные системы, напр, ударопрочный полистирол, в к-рых ударная вязкость после экструзии в результате ориентации частиц каучука снижается. [c.219]
Способ получения экструзионного пенополистирола
Изобретение относится к технологии переработки пластмасс, к способу получения пенополистирола методом экструзии, широко применяющегося в качестве теплоизоляционного материала в промышленном и гражданском строительстве, строительстве автомобильных и железных дорог. При изготовлении экструзионного пенополистирола в качестве регулятора пор использут перлит вспученный молотый в количестве 0,7 — 1,5 мас.ч. на 100 мас.ч. гранул полистирола с содержанием 3,5 — 7,0 мас.% смеси предельных углеводородов C5 или их изомеров в качестве вспенивающего агента. Изобретение позволяет получать профилированные изделия из пенополистирола с мелкоячеистой однородной структурой, высокой формоустойчивостью и стабильными физико-механическими и теплофизическими свойствами. 1 табл.
Изобретение относится к способу получения пенополистирола и может быть использовано в промышленности строительных материалов и в холодильной технике.
Пенопласты на основе полистирола и изделия из них широко применяются в качестве теплоизоляционных материалов в строительстве гражданских и промышленных зданий и сооружений, в рефрижераторах, промышленных холодильниках, для защиты от промерзания и вспучивания автомобильных и железных дорог. Теплоизоляционные материалы и изделия из пенополистирола со стабильными теплофизическими и физико-механическими свойствами получают методом экструзии вспенивающейся композиции, которая кроме полистирола содержит вспенивающие агенты и нуклеирующие добавки. Экструзионный метод переработки включает следующие основные стадии: добавление к полистиролу вспенивающих агентов и нуклеирующих добавок; плавление, гомогенизация в экструдере смеси расплавленного полистирола со вспенивающими агентами и добавками; вспенивание расплавленной полимерной композиции, основанное на быстром снятии давления при экструдировании в зону более низкого давления; охлаждение полученного вспененного материала или изделия.
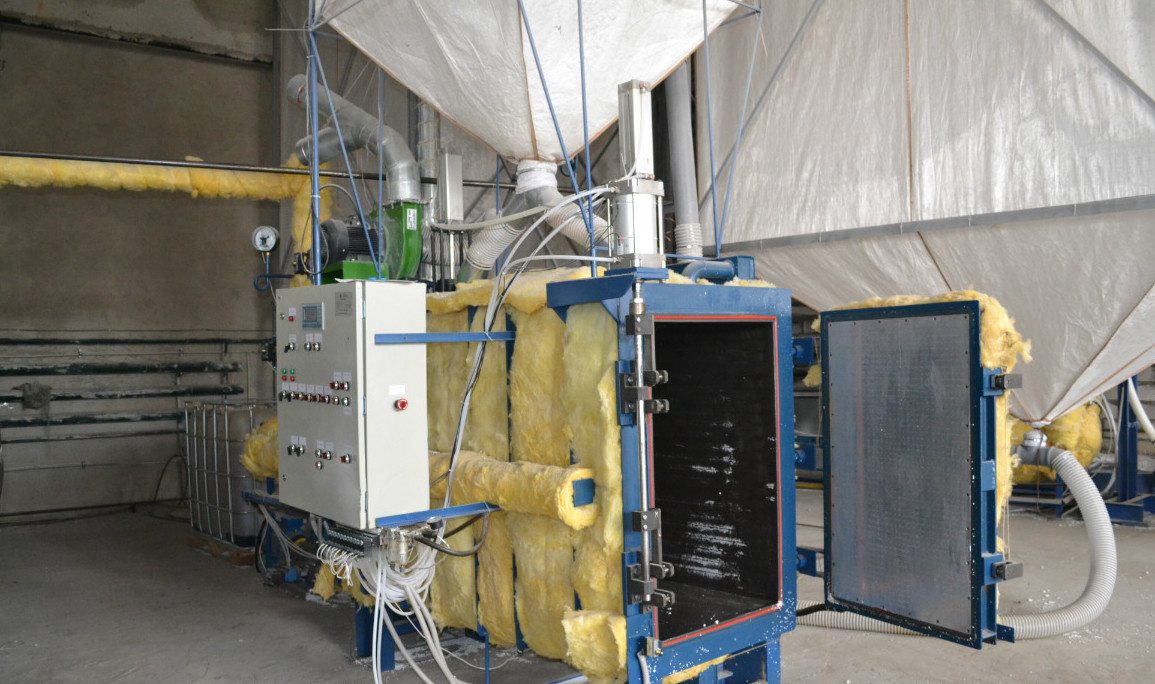

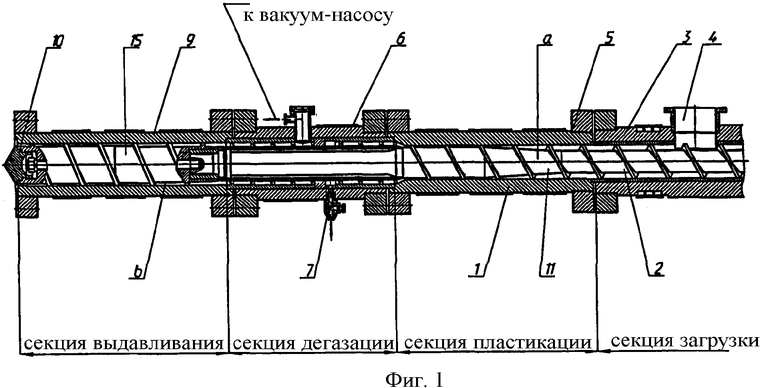
Гранулы полистирола, содержащие 3,5 — 7,0 мас.% предельных углеводородов C5 или их изомеров — 100,0
Натрий бикарбонат — 1,0
Лимонная кислота или ее моногидрат — 0,8
Молотый перлит вспученный — 0,7 — 1,5
Мелкодисперсные кристаллические частицы перлита имеют неправильную форму и обладают большой удельной поверхностью за счет большого количества внутренних пор, что увеличивает количество центров зародышеобразования газовых пузырьков при вспенивании полимерной композиции. В композицию могут быть введены традиционные смазки и антипирены. Помимо известного экономического преимущества, технические достоинства предлагаемого способа, вытекающие из свойств перлита, иллюстрируются следующими примерами. Пример 1. Для экструдирования готовят вспенивающуюся композицию следующего состава: 100,0 мас.ч. полистирола вспенивающегося, содержащего 3,5-7% пентана или изопентана или их смеси, смешивают с 1 мас.ч. перлита молотого, 1 мас. ч. бикарбоната натрия, 0,8 мас.
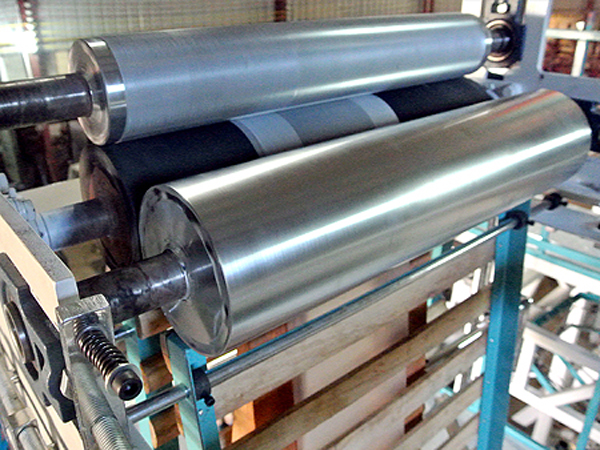

Формула изобретения
Гранулы полистирола, содержащие 3,5 — 7,0 мас.% предельных углеводородов C5 или их изомеров — 100,0
Натрий бикарбонат — 1,0
Лимонная кислота или ее моногидрат — 0,8
Молотый перлит вспученный — 0,7 — 1,5
РИСУНКИ
Рисунок 1Технология производства экструдированного пенополистирола: изготовление
Экструдированный пенополистирол – однородный синтетический материал. В его прочной микроструктуре распределена масса ячеек, составляющих единое тело.
Экструдированный пенополистирол является однородным материалом-утеплителем, который состоит из нескольких пористых ячеек.
Диаметр ячеек очень мал – примерно одна десятая миллиметра, внутри они полые и абсолютно герметичные, то есть имеют капиллярность, приближенную к нулю. Именно это и делает полистирол уникальным материалом с идеальными характеристиками, такими, как:
Схема пенополистирола в качестве утеплителя.
- Низкая теплопроводность пенополистирола.
- Прочность.
- Легкость.
- Влагостойкость, которая обеспечивается очень низкой степенью водопоглащения.
- Сохранение своих свойств под воздействием очень низких температур.
- Отличные звукоизоляционные показатели пенополистирола.
- Долговечность.
- Высокие гигиенические свойства, которые обеспечиваются стойкостью к образованию плесени, росту и размножению бактерий на поверхности пенополистирола.
Все эти свойства пенополистирола делают его идеальным утеплителем. В этом качестве он и используется уже более 70 лет, являясь лидером продаж в этой сфере строительного рынка. В странах Европы и Соединенных Штатах он уже давно вытеснил применение пенопласта.
В нашей стране пенополистирол также набирает популярность благодаря своим эксплуатационным характеристикам и относительно небольшой цене.
Спрос на экструдированный полистирол в России каждый год увеличивается приблизительно на тридцать процентов. Нашел свое широкое применение экструдированный полистирол и в пищевой промышленности для производства тары для упаковки пищевой продукции. Не сложная технология производства полистирола делает возможным его изготовление на небольших производственных линиях.
Технология производства экструдированного пенополистирола
Производство экструдированного пенополистирола – его вспенивание посредством фреонов.
Поначалу технология производства экструдированного пенополистирола представляла собой его вспенивание посредством фреонов. После многочисленных протестов экологов и проведения исследований, установивших, что фреоны входят в список веществ, применение которых участвует в разрушении озонового слоя Земли, в производстве пенополистирола стали использовать углекислый газ СО² как вспенивающий агент.
В общих чертах процесс изготовления выглядит так:
- В сырье (суспензионный полистирол) вводятся необходимые добавки для обеспечения противопожарных свойств (антипирены), для обеспечения лучшего распределения осветлителя (нуклеаторы), а так же красители или пигменты. Далее производится процесс загрузки.
- Производится предварительное вспенивание и вылеживание вспененных гранул.
- Спекание и формовка.
- Обработка в тянущем устройстве.
- Полотно охлаждается естественным путем, при этом происходит окончательное вспенивание. Иногда на мощных производственных линиях применяется принудительное охлаждение методом перекладывания.
- Процесс стабилизации.
- Обработка поверхности до достижения гладкости поверхностей.
- Процесс нарезки и упаковки пенополистирола.
Вернуться к оглавлению
Поэтапное описание технологии и особенностей производства экструдированного полистирола
Вернуться к оглавлению
Загрузка сырья в бункер вспенивающего устройства
Суспензионный полистирол является сырьем для пенополистирола.
Сырьем для производства пенополистирола является суспензионный полистирол, вес при насыпке которого приблизительно равен 500 г на кубический м объема (после вспенивания увеличивается до 15-100 кг). Каждая партия сырья имеет свое время, необходимое для вспенивания, которое должно строго выдерживаться. При превышении временных границ происходит разрушение гранул. В технологии производства вспененного полистирола учитывается качество сырья.
Сырье поступает на склады производства обычно упакованным в мешки по 25 кг или в так называемых биг-багах – мягких контейнерах большого размера и грузоподъемности, имеющих стропы петли для погрузки. Условия хранения сырья должны быть строго соблюдены. Оно должно храниться на поддонах при температуре от 20-25ºC. Сырье не предназначено для длительного хранения, так как со временем могут меняться временные показатели вспенивания. Технология хранения обычно указывается на упаковке.
Перед загрузкой сырья производится механическое перемешивание гранул полимера с добавками-модификаторами. Каждая из них выполняет свою функцию. Помимо уже перечисленных выше для улучшения однородности и мелкой структуры пор добавляют стабилизаторы-нуклезиаты, антипиреновые добавки для повышения огнестойкости, термостабилизаторы и антиоксиданты для защиты от термоокислительной диструкции, абиотические добавки для исключения плесневения. Возможно введение антистатических и синергических добавок. Технология введения добавок подбирается с учетом марки экструдированного пенополистирола.
Вернуться к оглавлению
Приспособления для загрузки
Гибкие шнеки состоят из мягкой трубы и стальной спирали.
Все современные линии оснащены обеспечивающими высокую пропускную способность приспособлениями для загрузки. Более того, производители предусматривают резервные возможности, если будет необходимо увеличение объемов производства пенополистирола. К устройствам подачи предъявляются высокие требования по надежности и способности транспортировки сырья без его повреждения. Более надежными считаются механические подающие устройства.
- Шнеки жесткие определенного диаметра, к которым подсоединена загружающая воронка. Главные преимуществом шнека считается возможность обеспечения при необходимости транспортировки сырья на большие расстояния (до 10 м). Именно жесткий шнек способен обеспечить максимальную сохранность сырья от механического повреждения.
- Гибкие шнеки. Состоят из мягкой трубы и проталкивающего устройства – стальной спирали. Главное достоинство – способность обеспечить как вертикальную, так и горизонтальную подачи. Работают в прерывистом режиме из-за невозможности синхронизации подачи сырья и наполнения бункера предварительного вспенивания.
- Инжектор для подачи сырья, который вставляется непосредственно в бункер.
Оснащен всасывающей трубкой, которая заканчивается штуцером. Для сокращения количества всасываемого с материалом воздуха оснащается регулирующими устройствами. Обеспечивает высокую скорость подачи сырья. Однако это скорее недостаток, чем достоинство, так как повышается вероятность повреждения гранул сырья, а так же из-за попадания воздуха снижается производительность и рентабельность производства.
- Вакуумная подача. Производится посредством воздуходувки, работающей при низком давлении, которое автоматически захлопывает клапан загрузки. Воздух выкачивается через фильтр. Работает по прерывистой схеме. Несмотря на малые диаметры подающего устройства, подача сырья происходит в очень высоком скоростном режиме, так что степень повреждения загружаемого материала очень велика.
Вернуться к оглавлению
Процесс предварительного вспенивание и вылеживание сырья
Процесс вспенивания гранул пенополистирола.
Свободное или предварительное вспенивание гранул происходит в предвспенивателе при температуре от 100-110°С и давлении 16-0,22 кг/см². Он состоит из емкости с отверстиями для подачи пара в днище и активатора для размешивания. В процессе вспенивания при обработке паром сырье увеличивается приблизительно в 30-50 раз. Целостность и замкнутость ячеек при этом не нарушается. Далее гранулы сырья под давлением поднимаются вверх и в окно выгрузки выдавливаются в промежуточный бункер, из которого транспортируются пневмотранспортом (система труб и вентиляторов) в бункер вылеживания. Здесь происходит стабилизация давления в расширившихся при вспенивании гранул. Здесь же происходит частичное замещение вспенивающего агента на воздух. Вспенивающий агент вытесняется, а частицы воздуха занимают их место.Технология контроля над процессом осуществляется вручную при помощи весов и мерных емкостей.
Вернуться к оглавлению
Процесс вторичного вспенивания
После выдержки в бункере вылеживания вспененные гранулы сырья вновь подвергаются термической обработке, еще раз увеличиваются в объеме, а так как этот процесс происходит в замкнутом пространстве, то увеличивающиеся в объеме сферические частицы вынуждены «спекаться», деформируясь в многогранники. Для технологии производства полистиролов имеются сводные таблицы по нормам загрузки и времени вспенивания.
Обработка поверхности, нарезка и упаковка экструдированного полистирола
Виды обработанной поверхности экструдированного полистирола.
Далее происходит выравнивание листов пенополистирола для достижения ровной поверхности. Полотно обрезается с боков, сверху и снизу. Получив правильные геометрические линии, его разрезают на листы необходимых размеров. Технология выравнивания и нарезки пенополистирола на современных линиях автоматизирована.
Производится дробление и гранулирование обрезки, после чего она снова поступает в производство.
Для больших производств рентабельным является применение устройства для дополнительного охлаждения листов, которое позволяет сократить время охлаждения путем перекладывания листов пенополистирола устройством карусельного типа. Лист охлаждается очень быстро, приблизительно за минуту.
Упаковываются листы пенополистирола, уложенные стопами, специальной упаковочной пленкой стретч-худ.
Вернуться к оглавлению
Типы установок для производства экструдированного полистирола
Процесс производства экструдированного полистирола.
Можно выделить три типа экструзионных установок, которые используется для изготовления экструдированного пенополистирола:
- Установки с одночервячным единичным агрегатом.
- Установки с двухчервячным двойным агрегатом.
- Тандемные установки с парой последовательно установленных агрегатов.
Экструдер представляет собой закрытую линию с поэтапным нагревом и охлаждением.
Шнеки устройства загружают и перемешивают гранулы сырья. Одночервячные экструдеры и двухчервячные экструдеры имеют сходный принцип действия, однако двухчервячные при своей компактности способны создавать более высокое давление в бункерах, что позволяет снижать температуру, что, в свою очередь, приводит к сокращению времени производственного цикла. Поэтому они более экономичны и рентабельны. Оба вида экструдеров лучше применять в небольших производствах.
Но самыми выгодными для производителя являются тандемные установки. Они наиболее рентабельны на больших, многотоннажных производствах пенополистирола, так как процесс разделен между двумя агрегатами. В одном происходит плавление и насыщение паром, во втором происходит гомогенизация, охлаждение формовка.
Технология производства пенопласта и экструдированного пенополистирола
Оглавление:- Этапы производства пенополистирола
- Вспенивание гранул полистирола
- Сушка и вылеживание вспененных гранул
- Производство блоков и их резка
- Экструдированный пенополистирол
Для изготовления пенополистирола (пенопласта) необходим суспензионный полистирол. Гранулы этого материала могут быть различного размера от 0,4 до 3,2 мм (в зависимости от марки сырья). В состав гранул входит легкокипящий компонент пентан, способствующий их увеличению в несколько раз при определенных условиях. Именно на этом свойстве материала основывается технология производства пенополистирола.
Схема наружного утепления с помощью пенополистирола.
Этапы производства пенополистирола
Заключается технология изготовления пенопласта во вспенивании суспензионного полистирола. Чтобы получить необходимый результат, применяют пар. Далее происходит спекание гранул. Затем формируется крупногабаритный блок, который впоследствии режется на листы. Но, прежде чем загрузить сырье в бункер, выполняется механическое перемешивание гранул с различными добавками-модификаторами.
Чтобы готовый материал был более огнестойким, в его состав добавляются антипиреновые добавки. Для защиты пенопласта от воздействия тепла и кислорода применяют антиоксиданты и термостабилизаторы, для предотвращения плесневения абиотические компоненты. При производстве экструдированного пенополистирола вводятся стабилизаторы-нуклезиаты, которые способствуют получению более однородной и мелкой структуры пор.
Вспенивание гранул полистирола
Технологическая схема производства листового пенополистирола.
Вспенивание суспензионного полистирола происходит в два этапа. Причем для каждой партии сырья определяется оптимальное время на прохождение данной стадии. Оно зависит от качества сырья. Этот период должен строго соблюдаться, так как если происходит увеличение временных интервалов, то гранулы могут разрушаться.
Первый этап обработки материала проходит в предвспенивателе. Этот агрегат емкость с отверстиями в днище, через которые происходит подача пара. Также он оснащен активатором для размешивания гранул. Во время вспенивания (около 5 минут) в емкости поддерживается температура около 100-110° С.
Процесс вспенивания происходит следующим образом. Благодаря действию водяного пара активизируется пентан, который входит в состав гранул суспензионного полистирола. Они размягчаются и вырастают в объеме, при этом количество материала может увеличиться в 30-50 раз. Целостность и герметичность ячеек сохраняются.
Чтобы процесс вспенивания происходил с ускорением, гранулы перемешиваются при помощи механического активатора. В конце этого цикла материал под давлением поднимается. Через окно выгрузки выталкивается в промежуточную емкость, а затем при помощи пневмотранспорта перемещается в бункер для вылеживания.
Сушка и вылеживание вспененных гранул
Схема пенополистирола в качестве утеплителя.
В гранулах полистирола, которые были вспенены, заключается около 10-15% влажности. Внутри них присутствует разрежение, так как происходила конденсация остатков пентана и пара. В результате под воздействием этих факторов может произойти сжатие гранул, что повлечет снижение объема материала и увеличение насыпной плотности. Именно по этой причине технология производства пенопласта предусматривает этап высыхания.
Цель данной стадии:
- укрепление наружных стенок гранул,
- восстановление внутреннего давления.
Благодаря тому, что теплый воздух (около 35° С) проникает в ячейки материала, полистирол приобретает нужные параметры сопротивления сжатию. Причем чем ниже у материала насыпная плотность, тем быстрее будет поглощаться воздух.
Процесс сушки занимает около 5 минут. В некоторых случаях он совмещается с этапом транспортировки. Во время перемещения материала влажность может быть снижена до 6-3%. Кроме потери влажности, сушка способствует значительному увеличению текучести материала.
Схема основных видов пенополистирола.
Это, в свою очередь, позволяет заполнять бункера для вылеживания более эффективно. Эти специальные устройства представляют собой металлическую основу с фиксированным мешком из воздухопроницаемой ткани. В них хранят гранулы при температуре, не превышающей 22-28° С. Продолжительность может составлять от 6 часов до суток. Зависит это время от объемного насыпного веса гранул: при снижении веса срок увеличивается, но он не должен превышать 14 суток, так как за такой период изопентан улетучивается и гранулы теряют способность к вспениванию.
Между тем способов вылеживания существует несколько. Чтобы сократить время выдержки, применяется метод перекачивания гранул при помощи воздушного потока из бункера в бункер. При таком подходе достаточно 2-3 часов для приобретения материалом необходимых показателей водопоглощения и прочности.
Производство блоков и их резка
Производство или выпекание блоков проводится в специальной блок-форме. Это устройство из стали в виде прямоугольника имеет двойные стенки, причем внутренняя часть перфорированная (это необходимо для подачи пара).
Схема панели из пенополистирола.
После прогревания формы в нее засыпаются гранулы, и она герметично закрывается. Повторное вспенивание проводится также под воздействием водяного пара под давлением.
На качество пенополистирола влияет своевременное прекращение процесса формирования. Если он прерван раньше необходимого срока, то недостаточно вспененные гранулы плохо сплавятся. Если же материал передержан, то ячейки разрушаются и появляются усадочные явления. В обоих случаях качество изделия значительно ухудшается.
После этого следует процесс охлаждения. Полученные блоки размещаются в цехе, где могут находиться от 12 до 720 часов. За это время материал теряет излишнюю влажность. Именно ее избыток не позволяет производить резку сразу же после охлаждения. Чтобы получить плиты нужной толщины, используется автоматический станок. А в качестве режущего элемента применяются разогретые нихромовые струны. На заключительном этапе листы помещают на станок с вертикальной резкой и торцуют.
Экструдированный пенополистирол
Процесс производства экструдированного пенополистирола несколько отличается от изготовления пенопласта, хотя по химическому составу эти материалы довольно схожи. Экструзия это своеобразный технологический процесс, который заключается в выдавливании материала, имеющего высокую вязкость. Пропускается такое сырье через экструзионную головку особенное формующее приспособление, которое позволяет получить изделие, имеющее поперечное сечение нужной формы.
Исходным материалом для экструдированного пенополистирола служит полистирол общего назначения.
Таблица характеристик экструдированного пенополистирола.
Гранулы вспенивают, но не при помощи водяного пара, а с использованием специального агента.
Ранее в качестве вспенивающих материалов для получения экструдированного пенополистирола использовались различные фреоны (жесткие, мягкие и их смеси). Сейчас применяют безфреоновые компоненты на основе СО2.
Для изготовления экструдированного пенополистирола создаются определенные условия, которые запускают процесс преобразования полистирола. Как и при производстве пенопласта, гранулы вспенивают, и получается вязкотекучая масса. Согласно технологии идет обработка не отдельных гранул, а жидкообразного вещества.
Готовый материал состоит из массы закрытых ячеек, которые наполнены воздухом, и обладает цельной микроструктурой. Размеры ячеек составляют 0,1-0,2 мм.
По окончании производства остатки вспенивателя, как правило, на протяжении суток вытесняются окружающим воздухом. В готовом материале между ячейками отсутствуют микропоры.
При точном соблюдении технологии производства как обычного пенопласта, так и экструдированного пенополистирола, получается легкий и прочный материал, обладающий низкой теплопроводностью и паропроницаемостью, а также устойчивый к водопоглощению.
Экструзионный пенополистирол
Экструзионный пенополистирол (экструзия, XPS)
Экструзионный пенополистирол, также как и обычный пенополистирол, состоит из пенополистирола, но отличается технологией создания гранул. Обычный пенополистирол создается путем «пропаривания» микрогранул водяным паром их гиперувеличения под воздействием температуры пары пока не будет заполнена пеной пенополистирола вся форма. Экструзионный пенополистирол производится методом экструзии. Экструзионный пенополистирол получают путём смешивания гранул полистирола при повышенной температуре и давлении с введением вспенивающего агента и последующим выдавливанием из экструдера. Внутри самого экструдера созданы специфичные условия для начала активации процесса преобразования полистирола. Экструзия заставляет полимер преобразовываться по другим механизмам и задает ему иные свойства и строение структуры. В частности, сначала происходит плавление гранул, и образуется однородная вязкая масса – сырье из твердого состояния переходит в вязко-текучее. Таким образом, дальнейшему преобразованию подвергаются уже не отдельные «тела»-гранулы, как при получении пенополистирола, а единое жидкофазное вещество, с неразрывными межмолекулярными связями.
Экструдированный пенополистирол имеет прочную, цельную микроструктуру, представляющую собой массу закрытых ячеек, заполненных молекулами газа. Экструзионый пенополистирол — это единое химическое вещество, с межмолекулярными химическими связями, которые на порядок прочнее, чем в пенополистироле. Ячейки экструдированного пенополистрола непроницаемы, потому что, в отличие от пенополистирола, не имеют микропор, следовательно, проникновение газа и воды из одной ячейки в другую невозможно. Стенки ячеек — это сплошная масса вещества. Доступ веществ окружающей среды возможен только в открытые ячейки, находящиеся на боковых поверхностях и срезах куска экструзионного пенополистирола. Т.е. весь кусок материала не поглощает влагу, пар, и т.п. извне. Качественный экструзионный пенополистирол обладает равномерной, закрытопористой структурой, с диаметром ячеек 0,1-0,2 мм.
Этот тип материала, обладающий плотностью 28 — 45 кг/м³ и высокой прочностью на сжатие, применяется при строительстве взлётных полос, автомобильных и железных дорог. Высокая прочность экструзионного пенополистирола является его главным преимуществом и позволяет его использовать не только как утеплитель, но и как строительный материал выполняющий иногда даже функции вспомогательных или несущих конструкций.
Экструзионный пенополистирол обладает низкой теплопроводностью (0,029-0,034), минимальным водопоглощением (0,2-0,4%), малым удельным весом (25 — 45 кг/м³). По показателям теплоизоляции и легкости экструзионный пенополистирол несколько превосходит обычный пенополистирол низкой плотности, который имеет теплопроводность 0. 038 Вт/(м*С), но теплопроводность EPS может ухудшадся во влажных условиях эксплуатации (например, грунтовые воды при утеплении фундамента) из-за более высокого водопоглощения. И в таком случае экструдированный пенополистирол будет уже значительно превосходить обычный пенополистирол.
Сфера применения XPS весьма широка: теплоизоляция фундаментов и цоколей, слоистой кладки и штукатурного фасада, кровли (инверсионные, традиционные, эксплуатируемые и др), полов, в том числе «тёплых». Также именно экструзионный пенополистирол применяется при строительстве автомобильных и железных дорог, снижая риск промерзания грунтов земляного полотна и последующего промерзания и вспучивания (морозное пучение грунта) Материал решает задачи теплоизоляции спортивных площадок, холодильных установок и ледовых арен.
Срок службы материала сопоставим со сроком службы всего здания, у качественных производителей он составляет более 40 лет.
Недостатки XPS (по сравнению с EPS)
К недостаткам экструзионного пенополистирола относится в 5 раз более худшая паропроницаемость 0. 013 Мг/(м*ч*Па) чем у традиционного пенопласта, что повышает требования к вентиляции дома утепленного экструзионным пенополистиролом.
Так-же существенный недостаток экструзионного пенополистирола — его высокая горючесть (класс Г3-Г4), в то время как многие производители обычного пенополистирола за счет специальных добавок добились фактически негорючих характеристик по классам Г1 и В1. Тем не менее, согласно СНиП 21-01-97 «Пожарная безопасность зданий и сооружений» и Федеральному закону №123 (Российскому) экструзионные плиты высокой степени горючести (Г3-Г4) могут использоваться в конструкциях. При повышенных требованиях к пожарной безопасности используют экструзионный пенополистирол группы горючести Г3. Однако, существуют современные ЭПС, в характеристиках которых по заявлению газеты класс горючести Г1 (слабогорючий материал)! Реализуется это за счёт новейших добавок из графитовых нано-частиц. … Эм, проверка этой информации показала, что производитель такого всё-же не заявляет, и класс горючести любого экструдированного пенополистирола Г3 либо Г4. Не верьте никому! И даже мне=)
Также следует отметить, что согласно новому Федеральному законодательству РФ (ФЗ №123) для горючих теплоизоляционных материалов регламентируется определение показателя токсичности продуктов горения, для качественных пенополистиролов она составляет не более Т2 — умеренноопасные. Кстати, показатель Т2 также присущ и материалам из дерева, например паркетам.
Что такое экструдированный полистирол (XPS)?
ПенопластXPS — это жесткий термопластический материал, изготовленный из полистирола. Полистирол — это синтетический углеводородный полимер, полученный из бензола и этилена, двух нефтепродуктов.
ПенопластXPS часто используется для теплоизоляции над уровнем земли, например, стен, потолков, чердаков и крыш, а также для элементов ниже уровня, например фундаментов и подвалов. При использовании более высокого класса он может уменьшить тепловые мосты и повысить энергоэффективность.
Как производится пенопласт XPS?Процесс производства изделий из пенополистирола (XPS) аналогичен процессу производства изделий из пенополистирола (EPS). Оба начинаются с одного и того же основного сырья. Но в случае экструдированного полистирола шарики или гранулы полистирольной смолы загружаются в экструдер, где они нагреваются при очень высоких температурах до расплавления. В этот момент к расплавленной смеси добавляют различные добавки.Одной из таких добавок может быть краситель. Пенопласт XPS обычно окрашивается в различные цвета, чтобы идентифицировать его как конкретную марку. Например, пенопласт Owens Corning XPS обычно розового цвета, а пенопласт Dow XPS — синего цвета. Также добавляется вспенивающий агент, чтобы продукт расширялся после процесса экструзии. Используя тщательно контролируемые нагрев и давление, пластиковая смесь продавливается через фильеру (экструдируется), затем ей дают остыть и расширяться до желаемой формы. Затем полученный пенопласт обрезается до размеров конечного продукта.Поскольку пенопласт скорее экструдируется, чем заливается в формы, такие как пенопластовый картон EPS, толщина изделия XPS ограничена.
Тепловые свойстваR-value — это показатель сопротивления материала теплопередаче. Это зависит от толщины и плотности строительного материала. Чем выше значение R, тем выше способность материала противостоять кондуктивной теплопередаче и тем лучше его характеристики в качестве изоляционного материала. Пенопласт XPS имеет равномерно распределенную структуру с закрытыми ячейками, что позволяет достичь начального значения R около R-5 на один дюйм (25 мм).По данным Министерства энергетики США, пенопласт XPS обеспечивает в два раза большее тепловое сопротивление, чем большинство других изоляционных материалов той же толщины,
.Непрерывный процесс экструзии, используемый для производства пенопласта XPS, обеспечивает однородное поперечное сечение с закрытыми ячейками, при этом каждая ячейка полностью закрыта стенками из полистирола, не оставляя пустот. Это помогает R-value пенопласта XPS сохранять однородный и надежный термический рейтинг R-5 в течение длительного времени, независимо от его плотности.
Однако элементы XPS содержат изолирующие газы или пенообразователи в дополнение к воздуху, который в конечном итоге диффундирует из ячеек. Этот процесс называется «старением». Фактически, процесс старения может со временем ухудшить изоляционные свойства пенопласта XPS, в результате чего его долгосрочное термическое сопротивление будет меньше заявленного начального значения R.
Благодаря своим высоким тепловым свойствам использование пенопласта XPS в строительстве может помочь снизить количество энергии, необходимой для обогрева и охлаждения здания.Изоляция из жестких плит, таких как пенопласт XPS, потенциально может помочь домовладельцам сэкономить до 40 БТЕ энергии на каждую БТЕ энергии, потребляемой системами отопления и охлаждения дома. В старых домах это может повысить энергоэффективность дома до 70%.
Сопротивление влагопоглощениюПроницаемость или «проницаемость» — это стандартная мера проницаемости для водяного пара материала. В отличие от значения R, в котором чем выше число, тем лучше, материал с более низким рейтингом проницаемости лучше задерживает движение водяного пара.Устойчивость к влагопоглощению важна, потому что вода является отличным проводником тепла.
Очень мало воды может проникнуть через структуру пенопласта XPS с закрытыми порами, что позволяет пенопласту XPS обеспечивать довольно постоянное тепловое сопротивление. Как правило, пенопласт XPS обладает достаточной водостойкостью, чтобы справляться с нормальным уровнем влажности подвала и фундамента, если дом не расположен в зоне затопления.
Необлицованный пенопласт XPS толщиной один дюйм имеет рейтинг проницаемости около 1.0, что делает его полупроницаемым замедлителем пара Класса II. Но настоящим испытанием изоляции является ее способность не только противостоять влаге, но и легко выделять любую влагу, которую она действительно поглощает, что называется «высыхающим потенциалом». Потенциал высыхания теплоизоляции имеет решающее значение для поддержания теплового сопротивления конструкции. Некоторые тесты показали, что с течением времени пенопласт XPS может впитывать больше влаги при работе с низкокачественными материалами и удерживать эту влагу в течение более длительных периодов времени, чем пенополистирол.Потенциал удержания влаги может со временем ухудшить начальное значение R пенопласта XPS, снижая его долгосрочное значение R и эффективность в качестве изоляционного материала.
Другая недвижимостьПрочность на сжатие. Пенопласт XPS — это жесткий материал с очень высокой прочностью на сжатие. Однородное поперечное сечение продукта с закрытыми ячейками, без пустот и каждая ячейка полностью закрыта стенками из полистирола, способствует его впечатляющей прочности.Доступны продукты с различной прочностью на сжатие для различных областей применения. Пенопласт XPS может изготавливаться с давлением до 100 фунтов на квадратный дюйм и более.
Способность подавлять рост биологических загрязнителей воздуха. Влага способствует росту многих организмов, таких как плесень, грибок и другие бактерии. Пенопласт XPS является водостойким и может препятствовать росту этих организмов.
Прочность . Поскольку пенопласт XPS является термопластичным материалом, он не гниет и не разлагается со временем.Он также устойчив к микроорганизмам в почве. К тому же он непривлекателен для крыс и других паразитов в качестве источника пищи. Срок службы до 50 лет.
Химическая инертность. Пенопласт XPS считается химически довольно инертным материалом. Он устойчив к большинству кислот, щелочей и водных растворов солей и щелочей. Однако многие органические растворители, такие как ацетон, хлорированные растворители и ароматические углеводородные растворители, могут разрушать пену и вызывать ее растворение.
Размер и плотность. Пенопласт XPS может изготавливаться как с пластиковым покрытием, так и без него. Из-за ограничений экструдированного производственного процесса он чаще всего доступен только в стандартных размерах и в форме листа (доски), при этом пенопласт обычно изготавливается в виде листов размером 4 на 8 футов. Пенопласт XPS довольно плотный — в среднем 2,18 фунта на кубический фут. Это делает его очень прочным.
Стоимость. Пенопласт XPS — один из наиболее экономичных вариантов жесткого пенопласта на рынке.Пенопласт XPS толщиной в один дюйм стоит около 0,47 доллара за квадратный фут.
Энергоэффективность. Пенопласт XPS — это энергоэффективный строительный материал. В течение всего срока службы здания, изолированного пенопластом XPS, экономится гораздо больше энергии, чем в процессе производства продукта. Исследование, проведенное Franklin Associates, показало это в течение 50-летнего срока службы дома, в котором использовалась изоляция из пенополистирола XPS.
Стабильность размеров. Пенопласт XPS значительно расширяется и коробится при более высоких температурах.
Устойчивое развитие. Было доказано, что пенопласт XPS, используемый в качестве изоляции для дома или здания, снижает количество энергии, необходимое для поддержания его обогрева и охлаждения, тем самым снижая потребление наших и без того истощенных природных ресурсов. И, поскольку полистирольная смола, термопластический материал, используется в производстве пенопласта XPS, пенопласт можно расплавить и повторно использовать для производства новой изоляции XPS. Что еще более важно, сегодня это обычная практика. По данным Ассоциации по производству экструдированного полистирола, заводы по производству XPS не создают «лома» или отходов, потому что 100% промышленных отходов вспененные плиты XPS восстанавливаются, разлагаются на полимерный материал и повторно используются в процессе производства пенополистирола.
Воздействие на окружающую средуКак мы видели, пенопласт XPS является экологически чистым продуктом, который можно переплавить и повторно использовать для производства большего количества продукции. Это также энергоэффективный продукт, позволяющий экономить гораздо больше энергии, чем было использовано при его производстве. И, с начальным значением R 5 на дюйм, использование пенопласта XPS может значительно снизить количество энергии, необходимой для обогрева и охлаждения здания. Это помогает сохранить наши природные ресурсы. Фактически, пенопласт XPS получил квалификацию Energy Star®.
ПенопластXPS обладает большинством основных атрибутов «зеленого» строительного материала. Он энергоэффективен, экологичен, обладает хорошей термостойкостью и устойчивостью к водопоглощению, а также долговечен и долговечен — до 50 лет. А поскольку это искусственный материал, он сокращает использование природных ресурсов.
Но не все аспекты изделий из пенопласта XPS столь же экологичны. Во-первых, пена XPS обычно содержит красители, которые окрашивают продукт, чтобы дифференцировать его по марке.В зависимости от типа используемого красителя он потенциально может нанести вред окружающей среде.
Вспенивающие агенты, используемые в процессе производства экструдированных материалов, также могут разрушать озоновый слой и способствовать глобальному потеплению. Пенопласт XPS часто использует гидрохлорфторуглероды (ГХФУ) в качестве вспенивателя. Вспенивающий агент проникает в ячейки XPS во время производственного процесса. В конце концов, в процессе, называемом «старением», вспениватель диффундирует из клеток в окружающую среду. Некоторые производители начинают использовать вспениватели, не наносящие вреда окружающей среде, но это еще не стандартная практика.
(PDF) Полевое обучение по производству вспененного и экструдированного пенополистирола и общее управление качеством
41
Ссылки
1. [1] ДОСТУПНО В; (HTTP://WWW.CHEMA-FOAM.COM)
2. [2] КАТРИН СИВЕРЦЕН, «ПОЛИМЕРНАЯ ПЕНА», 3.063 ПОЛИМЕРНАЯ ФИЗИКА, ВЕСНА
2007.
3. [3] ВОСТОЧНОЕ ПОЛУШАРИЕ, ЧАРЛЬЗ Э. КАРРАХЕР, МЛАДШИЙ, «ПОЛИМЕР
ХИМИЯ», ШЕСТОЕ ИЗДАНИЕ, 2003 г., БЕЗ СТРАНИЦЫ.
4. [4] CRC PRESS TAYLOR & FRANCIS GROUP, HEINZ HEINEMANN, JAMES G. SPEIGHT,
UTTAM RAY CHAUDHURI, «ФУНДАМЕНТАЛЫ НЕФТЕХИМИЧЕСКОЙ И НЕФТЕХИМИЧЕСКОЙ ПРОМЫШЛЕННОСТИ
ENGINEERING, 2011, ПРОМЫШЛЕННАЯ ПРОМЫШЛЕННОСТЬ 115, ХИМИЧЕСКОЕ ИЗДАНИЕ, 115
И 116.
5. [5] ПЛАСТИКОВЫЕ МАТЕРИАЛЫ И ОБРАБОТКИ КОНКУРЕНТАЯ ЭНЦИКЛОПЕДИЯ »ДЛЯ
ЧАРЛЬЗ А. ХАРПЕР И ЭДВАРД М. ПЕТРИ
6. [6] AHMED FOUAD ELRAGI AND 9000 PROECTEDTIESINEER, 9000 PROECTEDTIESINEER ПРИМЕНЕНИЕ EPS GEO FOAM », 2016, НОМЕР СТРАНИЦЫ
7.[7] ЧАРЛЬЗ Э. ТОМАС, «ТЕХНОЛОГИЧЕСКОЕ ОБОРУДОВАНИЕ И СИСТЕМЫ»,
ТРЕТЬЕ ИЗДАНИЕ, 2011, СТР. 215 216.
8. [8] ИНЖЕНЕРНЫЙ КОРПУС АРМИИ США, «ОБРАБОТКА КОТЕЛЬНОЙ ВОДЫ: УРОКИ
ИЗВЛЕЧЕНЫ», 10 НОЯБРЯ 1999, СТРАНИЦА 1.
9. [9] ДОСТУПНО В; (HTTP://WWW.LWEPS.COM/EPS-MACHINE/EPS-PRE-
EXPANDER / TOP-PERFORMANCE-MULTIFUNCTIONAL-PRE-EXPANDER.HTML)
10. [10] AR CHIVESOF FOU NDRYE NGI NE ER I NG МЕТОД РАСШИРЕНИЯ
— ПРОЦЕСС ПРЕДВАРИТЕЛЬНОГО РАСШИРЕНИЯ ”ФОРТ.ПАЦЫНЯК, Р. КАЧОРОВСКИЙ, Я. ГРОМ, М.
БЕЙГЕР, Б. МАЙЧРЗАК.
11. [11] T.PACYNIAK, R.KACZOROWSKI, J.GROM, M.BEJGER, B.MAJCHRZAK, AR CH
IVESOF FOU NDRYE NGI NEERI NG МЕТОД УТЕРЯ ПЕНЫ — ПРОЦЕСС ПРЕДВАРИТЕЛЬНОГО РАСШИРЕНИЯ
9 , ТОМ 10, 2010, СТР. 90.12. [12] В НАЛИЧИИ; (HTTP://WWW.EBRUZEN.COM.TR/EN/PORTFOLIO/EPS-
AGING-SILO-FABRIC /)
13. [13] A JOHN WILEY & SONS, INC., ПУБЛИКАЦИЯ, ЧАРЛЬЗ А.ХАРПЕР И
ЭДВАРД М. ПЕТРИ, «ПЛАСТИКОВЫЕ МАТЕРИАЛЫ И ПРОЦЕССЫ КОНКУРЕНТАЯ
ЭНЦИКЛОПЕДИЯ», 2003 г., СТРАНИЦА 174.
14. [14] Р.К. Синнотт, «ХИМИЧЕСКИЙ ИНЖЕНЕРНЫЙ ДИЗАЙН, ТОМ 6, 9000» 1993, 1996, 1999, 2005, СТРАНИЦА 912
15. [15] FORD MOTOR COMPANY, FORD DESIGN INSTITUTE, «СПРАВОЧНИК FMEA
ВЕРСИЯ 4.1″, ФЕВРАЛЬ 2004, СТР. 2-3, 2-5 И 2-12
Экструдированный полистирол XPS
Экструдированный пенополистирол, известный как XPS, представляет собой теплоизоляционный материал, который был создан в США в 1941 году.
XPS имеет очень широкую область применения — теплоизоляция зданий, фундаментов, цоколей, фасада, кровли, полов, применяется при строительстве автомобильных и железных дорог. Это приводит к уменьшению расширения и сжатия грунта в результате изменения температуры грунта. Используется в качестве теплоизоляции на спортивных площадках, в холодильных установках, на ледовых аренах.
XPS производится из полистирола общего назначения (GPPS). Состав пенополистирола, применяемого для производства полистирола и полистирола общего назначения, одинаков, он отличается технологией производства самих гранул.
Обычная пена получается пропариванием гранул. В водяном паре под действием температуры происходит гиперувеличение гранул и форма заполняется пенополистиролом.
XPS производится методом экструзии. Гранулы полистирола смешивают в экструдере при повышенном давлении и температуре. Добавляют вспенивающий агент, тщательно перемешивают и выдавливают через головку экструдера. EPS имеет однородную структуру с закрытыми порами, диаметр ячеек 0.1 — 0,2 мм.
При строительстве взлетно-посадочных полос, автомобильных и железных дорог используется особый вид изоляции с высокой прочностью на сжатие, плотностью 38–45 кг / м3.
Высокопрочный экструдированный пенополистирол является одним из основных достоинств и позволяет использовать его в качестве материала, выполняющего функции вспомогательных или даже несущих конструкций.
XPS имеет очень низкую теплопроводность, минимальное водопоглощение и низкий удельный вес.
Срок службы данного вида утеплителя от качественных производителей достигает 40-50 лет и сопоставим со сроком эксплуатации всего здания.
Ведущими производителями XPS являются Owens Corning, Ravago, URSA, Dow и др.
Пенополистирол (EPS)
EPS
EPS — это жесткий вспененный термопластический материал с закрытыми порами. Он изготовлен из твердых бусин полистирола. Расширение достигается за счет небольшого количества газа, содержащегося в шарике полистирола.При подаче тепла в виде пара газ расширяется, образуя закрытые ячейки EPS. Эти ячейки занимают примерно в 40 раз больше объема исходного шарика полистирола. Бусины из больших блоков EPS могут быть изготовлены в соответствии со спецификацией для формирования индивидуальных форм.
ПРИЛОЖЕНИЯ
EPS имеет множество применений, включая защиту небольших электрических компонентов, крупных предметов, таких как холодильники с морозильной камерой, и множество применений, защищающих продукты питания от повреждений на различных этапах производства и отгрузки.Он используется в рыбной промышленности для упаковки охлажденных продуктов и в сельскохозяйственном секторе для лотков с семенами и упаковки фруктов и овощей.
НЕДВИЖИМОСТЬ
Легкий вес: EPS на 98% состоит из воздуха, что делает его одним из самых легких упаковочных материалов. Это очень мало увеличивает вес упаковки, поэтому транспортные расходы и выбросы топлива сведены к минимуму.
Прочность: ячеистая матрица из 2% полистирола обеспечивает исключительную ударопрочность.Превосходная амортизация упаковки из пенополистирола гарантирует защиту продукции.
Изоляция: теплоизоляционные свойства пенополистирола помогают сохранять пищу свежей и предотвращают образование конденсата по всей цепочке распределения. EPS имеет пониженную теплопроводность, с плотностью около 28-45 кг / м3. Поэтому он действует как изолятор, сохраняя продукты холодными или теплыми в зависимости от области применения.
Универсальность и простота маркировки: EPS может иметь индивидуальную форму для защиты мельчайших электрических компонентов или самого большого холодильника с морозильной камерой.Это уменьшает количество необходимой упаковки, что приводит к экономии места, расходов на распространение и повреждение товаров. Он может быть четко обозначен содержимым или логотипом компании, а этикетка может быть прикреплена непосредственно к упаковке.
Гигиенично и безопасно: EPS нетоксичен и химически инертен. На нем не могут расти грибы и бактерии.
Водонепроницаемость: EPS нерастворим и негигроскопичен.
Низкое воздействие углерода: Чистые производственные технологии означают минимальные затраты энергии и воды без производственных отходов.
Экономичность: Высокоэффективное производство и локализованные производственные подразделения означают, что это недорогое, проверенное решение.
ЭКОЛОГИЧЕСКИЕ ФАКТЫ
Защитные характеристики EPS помогают снизить потери, вызванные поломкой или повреждением товаров в цепочке поставок. Это экономит ресурсы энергии, материалов и транспорта.
Использование EPS помогает предотвратить порчу пищевых продуктов. Благодаря своей вспененной природе, он защищает пищевые продукты и предотвращает повреждение на различных этапах производства и транспортировки от фермы к вилке, обеспечивая доставку множества различных продуктов к продавцу или потребителю в идеальном состоянии.
EPS не содержит ГФУ, ХФУ и ГХФУ, а в качестве вспенивающего агента используется пентан. Пентан имеет низкий потенциал глобального потепления * (ПГП) менее пяти. (ЕС не регистрирует пентан как вещество, опасное для здоровья человека или окружающей среды.)
EPS чрезвычайно легкий. Это помогает снизить расход топлива при транспортировке товаров по сравнению с другими более тяжелыми упаковочными материалами.
Стирол, используемый при производстве пенополистирола, естественным образом встречается во многих обычных продуктах, включая клубнику, бобы, орехи, пиво, вино, кофейные зерна и корицу.
Производство EPS — это процесс с низким уровнем загрязнения. Пар — ключевой ингредиент, и вода используется много раз. В этом процессе нет отходов, так как все обрезки или браки используются повторно.
Только 0,1% от общего потребления масла используется для производства EPS.
Углеродный след EPS ниже, чем у многих других упаковочных материалов, используемых сегодня.
КОНЕЦ ЖИЗНИ
EPS может быть успешно восстановлен и переработан там, где есть оборудование.Однако из-за того, что он чрезвычайно легкий, в настоящее время он не перерабатывается в мировом масштабе.
Там, где в настоящее время нет инфраструктуры для рециркуляции, это идеальный кандидат для использования энергии из схем утилизации отходов из-за ее высокой теплотворной способности.
EPS, полученный из отходов упаковки, является идеальным исходным материалом для схем EfW. Сегодня они составляют всего 0,1% твердых бытовых отходов (ТБО), хотя многие считают, что их намного больше из-за их громоздкости!
Ключевым преимуществом использования EPS для EfW является то, что он имеет высокую теплотворную способность (46 000 кДж / кг), аналогичную природному газу — 48 000 кДж / кг.
отходов EPS, помещенных в мусорные ведра одного домохозяйства в Великобритании в течение одного года, содержат достаточно энергии, чтобы нагреть воду для 500 ванн или поддерживать телевизор включенным в течение 5000 часов.
При этом методе обращения с отходами EPS также отсутствуют токсичные выбросы, поскольку он сжигается на современных заводах при очень высоких температурах. Таким образом, побочными продуктами являются только пар, двуокись углерода и очень низкий уровень нетоксичной золы. Эти выбросы менее опасны, чем типичный походный костер, и на самом деле нет достоверных доказательств того, что схемы EfW имеют какое-либо влияние на здоровье населения.
ВыбросыEfW строго контролируются, и «Стратегия правительства Великобритании по утилизации отходов для Англии 2007» не предусматривает «убедительных доказательств неблагоприятных последствий для здоровья» от выбросов EfW.
BPF настоятельно рекомендует в тех случаях, когда переработка упаковочного продукта невозможна, его следует отправлять на завод EfW, где рекуперированная энергия будет обеспечивать столь необходимую электроэнергию местного производства.
EPS
EPS используется во многих аспектах строительных работ, включая большие конструкции, такие как дороги, мосты, железнодорожные пути, общественные здания или даже небольшие семейные дома.
Характеристики EPS делают его идеальным для использования в качестве легкого наполнителя, утеплителя, в качестве элемента для украшения или творческих штрихов, в качестве легкого заполняющего материала на дорогах, для облегчения дренажа земель и т. Д.
Мы можем посетить любую строительную или строительную площадку и найти изделия из пенополистирола, выполняющие разнообразные и важные функции.
Для этих приложений важны следующие свойства:
Низкая теплопроводность
Благодаря закрытой, заполненной воздухом ячеистой структуре, препятствующей прохождению тепла или холода, достигается высокая теплоизоляционная способность.
Малый вес
Плотность от 10 до 35 кг / м2 позволяет проводить легкие и безопасные строительные работы
Механическое сопротивление
EPS обладает превосходными механическими свойствами, что делает его хорошим выбором для изоляции несущих крыш, полов с основанием тротуара, строительства дорог, в качестве несущей изоляции и т. Д.
Низкое водопоглощение
EPS не впитывает влагу, а на его термические и механические свойства не влияет сырость, влажность или влажность.
Простота обращения и установки
С материалом можно обращаться обычным способом. Вам гарантирован идеальный результат. Малый вес EPS упрощает обращение с ним и его транспортировку на строительную площадку.
Химическая стойкость
EPS полностью совместим с другими материалами, используемыми в строительстве, включая цемент, штукатурку, соль, пресную воду и так далее.
Универсальность
EPSможно разрезать по форме или размеру, которые требуются для строительного проекта.
Стойкость к старению
Все перечисленные выше свойства сохраняются в течение всего срока службы материала и сохраняются на протяжении всего срока службы самого здания. EPS не изменяется под воздействием внешних факторов, таких как грибки или паразиты, поскольку они не находят в материале питательной ценности
.
Преимущества изоляции оболочки из экструдированного пенополистирола
Обшивка из экструдированного пенополистирола — от производства до установки
Наиболее распространенные компоненты ограждающих конструкций здания выполняют важные функции, но не всегда раскрывают свой истинный потенциал.С этой целью различные типы пластиковых материалов могут помочь владельцам зданий достичь требуемой эффективности. Например, изоляционная оболочка из вспененного экструдированного полистирола (XPS) предлагает множество преимуществ благодаря способу изготовления этого продукта. Энергоэффективная, простая в установке, легкая и узнаваемая по синему, розовому или зеленому цвету, оболочка из экструдированного пенополистирола может позволить использовать один продукт для создания непрерывного слоя тепловой и влагозащиты на здании. стены, тем самым способствуя энергоэффективности.
Создание экструдированного полистирола
Экструдированный пенополистирол начинается с твердых гранул полистирольной смолы. Пластиковые гранулы загружаются в экструдер, где они плавятся и смешиваются с важными добавками с образованием вязкой жидкости. Затем вводится пенообразователь, чтобы пластиковый продукт расширился. В тщательно контролируемых условиях нагрева и давления пластиковая смесь продавливается через матрицу в желаемую форму. Затем жесткий пенопласт обрезается до размеров конечного продукта и обычно распознается как доски.
Этот непрерывный процесс дает структуру с закрытыми ячейками, которая выглядит как масса однородных пузырьков с общими стенками между ними. Также образуется сплошная гладкая пленка сверху и снизу.
Структура экструдированного пенополистирола (XPS) с закрытыми порами придает превосходную долговечность и долговечность. (См. «Сообщение от APC» на стр. 4 для получения дополнительной информации о пенопластах.) Доступны продукты с различными значениями прочности на сжатие, чтобы удовлетворить различные потребности применения. Благодаря своим физическим свойствам эта прочность не зависит от использования облицовочных материалов или ламинатов, которые иногда могут быть нарушены во время установки.Тем не менее, облицовочные изделия из экструдированного полистирола (XPS) доступны для добавления дополнительной прочности, если это указано для конкретного применения. Экструдированный пенополистирол также бывает самых разных размеров и имеет толщину до 102 мм (4 дюйма), что позволяет использовать его во многих областях.
XPS Энергоэффективность
Обшивка из пенополистирола (XPS) может иметь положительное влияние на энергию и выбросы в атмосферу при использовании в жилых зданиях. Исследование, проведенное в 2000 году компанией Franklin Associates, показывает, что в течение 50-летнего срока службы дома при правильном использовании пенопласта XPS экономится гораздо больше энергии, чем при производстве изоляции. 1 Другое исследование, представленное на форуме Earth Tech 2004 года, показывает, что менее чем через три года удается избежать выбросов парниковых газов из-за потребления энергии на нагрев / охлаждение, чем при производстве изоляционной оболочки из экструдированного пенополистирола. 2
Правильно установленная пена из экструдированного полистирола (XPS) также может повысить энергоэффективность здания, обеспечивая полный слой изоляции на стене. Это уменьшает движение воздуха через стену, которое может отбирать энергию.Изоляция между стойками не обязательно обеспечивает полную изоляцию, поскольку деревянные стойки и другие элементы каркаса не изолированы. (См. «Пластик требует улучшения стены» на странице 5.) Это явление называется тепловым мостиком и может значительно снизить тепловые характеристики здания.
Поскольку жилые деревянные каркасы обычно составляют около 25 процентов площади стены (с учетом оконных и дверных рам), четверть стены остается неизолированной, если используется только изоляция полости.Таким образом, оболочка из пенополистирола (XPS) может обеспечить изоляционные свойства всей площади стены. Помимо присущих им изоляционных свойств, обшивка из пенополистирола (XPS) при правильной установке и герметизации швов также может значительно снизить утечку воздуха через стены, что может повысить энергоэффективность и комфорт.
Важным атрибутом экологичных строительных изделий, особенно изоляционных, является способность правильно функционировать в течение всего срока службы без ухудшения физических свойств.Фактически, для правильного проектирования систем отопления и кондиционирования воздуха необходимы хорошие долгосрочные изоляционные свойства.
Экструдированный пенополистирол также может иметь преимущества, связанные с его способностью управлять влажностью, сопротивляться как водопоглощению, так и циклам замораживания / оттаивания. Когда традиционная изоляция впитывает воду, ее тепловые характеристики со временем могут ухудшиться.
Уменьшение, повторное использование, переработка
Три строгих экологических принципа: сокращение, повторное использование и переработка. 3 Поскольку изоляционная оболочка из пенополистирола (XPS) может снизить потери энергии в зданиях, она может снизить (т.е. уменьшить) количество энергии (газовой и электрической), необходимой для поддержания комфортных условий жизни.
Чем шире используется изоляционная оболочка из вспененного экструдированного полистирола (XPS), тем сильнее его влияние на снижение потребления природных ресурсов, таких как уголь, нефть и газ.
Полистирол — это термопластический материал, что означает, что его можно расплавить и повторно вставить (т.е.е. повторно используется) в производство новой изоляции из пенополистирола (XPS). Заводы по производству экструдированного полистирола практически не образуют лома или отходов, потому что почти 100% регенерируется, измельчается и повторно гранулируется для производственной системы (т.е. перерабатывается). Некоторые компании даже ищут внешние источники лома полистирольной пластмассы для повторного использования.
Кроме того, экструдированный пенополистирол (XPS) может быть изготовлен из материала бытового назначения. Однако в настоящее время в Соединенных Штатах нет инфраструктуры, которая делает экономически выгодным сбор строительных материалов, загрязненных гвоздями, клеем и т. Д.Если ситуация изменится, экструдированный пенополистирол (XPS) может быть легко переработан после удаления загрязняющих веществ из продукта. 3
Другой вариант уменьшения количества постобработанных материалов — сжигание, которое не так широко используется в Соединенных Штатах. Тем не менее, вспененный экструдированный полистирол (XPS) может быть сырьем для этой технологии, если она получит поддержку. В любом случае, поскольку пенопласт из экструдированного полистирола (XPS) используется в конструкциях со сроком службы от 15 до 50 лет, его влияние на свалки, как правило, невелико по сравнению с традиционными материалами, которые могут потребовать более частой замены.
Инструкции по монтажу экструдированного пенополистирола
По мере появления большего количества вариантов изоляционной оболочки строители постоянно ищут более простые и лучшие методы установки. Традиционно следуя текущим тенденциям в установке систем жилых зданий, изменения в местных правилах и внедрении новых продуктов заставляют строителей возводить дома более высокого качества, которые обладают большей устойчивостью к влаге
и повышенной энергоэффективностью.
Правильно установленная изоляционная оболочка из вспененного экструдированного полистирола (XPS) может обеспечить отличные влагостойкие и изоляционные свойства.Как уже упоминалось, изделия из экструдированного полистирола легки, универсальны и легко устанавливаются на стены жилых домов, как показано в следующем пошаговом руководстве:
- Первым шагом является маркировка изоляционных панелей из экструдированного пенополистирола (XPS) путем перетаскивания крючка измерительной ленты по поверхности пластиковой изоляционной панели, удерживая другой конец ленты на нужном расстоянии. Это создает небольшую отметку, по которой можно следить при резке.
- Затем пластиковую изоляционную плиту следует положить на плоскую прочную поверхность для облегчения резки и безопасности.Для работы по пояс обычно достаточно пары козлов. По отметке, оставленной краем ленты, следует сделать глубокий отпечаток, прижав нож к доске (не прорезая). Как только вся измеренная линия будет надрезана, кусок просто защелкнется над краем рабочей поверхности. . Лучше всего использовать универсальный нож и прямую кромку, чтобы обрезать изоляционную плиту из экструдированного пенополистирола (XPS), чтобы она соответствовала неровным углам стены, выступам или поверхностям стен меньше ширины или высоты плиты.
- Затем устанавливаются угловые распорки, соответствующие требованиям Кодекса (например, диагональная металлическая обвязка, пропущенная древесина или деревянная конструкционная обшивка). Если деревянная обшивка используется в качестве конструктивного элемента, здание может быть покрыто изоляционными плитами из вспененного экструдированного полистирола (XPS), чтобы обеспечить полную изоляцию стен.
- Изоляционные плиты из пенополистирола (XPS) шириной 1,2 м (4 фута) следует устанавливать вертикально с длинными стыками, плотно стыкованными вместе и опирающимися непосредственно на элементы каркаса.Горизонтальные стыки между досками должны быть минимизированы, если стыки не располагаются непосредственно над горизонтальным элементом каркаса. Заклеивание швов изоляционных плит из вспененного экструдированного полистирола (XPS) изолирует их от проникновения воздуха для повышения энергоэффективности.
- Желательно закрепить изоляционные панели из пенополистирола (XPS) с помощью пластиковых колпачковых гвоздей с головкой 25,4 мм (1 дюйм), достаточной длины для проникновения в каркас размером не менее 19 мм (0,75 дюйма). Другой вариант — использовать 9,5 мм (0.375 дюймов) оцинкованные с головкой кровельные гвозди достаточной длины для проникновения в каркас минимум на 19 мм. Кроме того, можно использовать коронку диаметром 25,4 мм и проволочные скобы 16 калибра, достаточные для проникновения в каркас, минимум 12,7 мм (0,5 дюйма). Не допускайте чрезмерного забивания шляпок гвоздей или скоб. Затем область экструдированного пенополистирола (XPS) закрепляется на 406 мм (16 дюймов) по центру (oc) и по периметру на 305 мм (12 дюймов) oc, или в соответствии с требованиями органов строительного надзора. имеющий юрисдикцию.
В конструкции из палочек следует рассмотреть возможность использования 1.Изоляционные плиты из экструдированного пенополистирола (XPS) размером 2 x 2,7 м (4 x 9 футов) для эффективного покрытия подоконников, стыков пола и потолка, ленточных коробов и коллекторов в одном приложении с меньшим количеством горизонтальных стыков. Обшивка из кирпича, дерева, ДВП, алюминия или винила крепится к конструкции деревянного каркаса через изоляцию в соответствии с инструкциями производителя сайдинга. Шатки или битумную черепицу также можно нанести, установив планки обрешетки или фанерный гвоздь поверх изоляции и прикрепив тряпки или битумную черепицу.Следует проконсультироваться с производителем о наиболее подходящих методах.
Изоляционные материалы из вспененного экструдированного полистирола (XPS) доступны в вариантах с жестким картоном или фальцованными листами. Свойства вспененного картона из экструдированного полистирола (XPS) описаны в стандарте ASTM International C 578 «Стандартные технические условия на жесткую теплоизоляцию из ячеистого полистирола». Они доступны в исполнениях по стандарту ASTM IV, V, VI, VII и X с обработкой кромок под квадрат, внахлест или гребень и паз для минимизации утечки воздуха через соединения.Другие варианты вспененных плит из экструдированного полистирола (XPS) включают кромки с прорезями и панели с пластиковыми, светоотражающими или перфорированными облицовочными материалами. 4
Пенополистирол EPS — Coperion
- Пластмассы
- Пенополистирол EPS
Пенополистирол (EPS) — это жесткий и прочный пенопласт.EPS часто используется для упаковки пищевых продуктов, строительной изоляции и упаковочного материала в виде твердых блоков, предназначенных для размещения защищаемого объекта, или в виде гранул с сыпучим наполнением, смягчающих хрупкие предметы внутри коробок.
Проверенная временем первоклассная технология Coperion и Coperion K-Tron оптимально подходит для одностадийного производства пенополистирола. Чрезвычайно надежные гравиметрические дозаторы Coperion K-Tron обеспечивают высокую точность подачи при добавлении в процесс GPPS, EPS, наполнителей, антипиренов, зародышеобразователей, цветных пигментов или пенообразователей.Благодаря интенсивному перемешиванию и очень бережному обращению с продуктом двухшнековые экструдеры ZSK обеспечивают оптимальное диспергирование всех ингредиентов. Микропеллеты создаются с помощью подводного гранулятора, а затем расширяются или формуются.
Читать далее Читать меньше
Ключевые преимущества:
- Компактная установка системы
- Гибкое производство по рецептуре
- Регулируемый размер гранул
- Повышение качества продукции за счет двухшнекового компаундирования
- Высокоточная подача основных ингредиентов
- Доступна полная конструкция ATEX
- Доступна полностью защищенная от коррозии технологическая секция
Типовая установка для одностадийного производства пенополистирола (EPS)
Полный ассортимент
Компаундирующие машины и экструдеры
Coperion предлагает двухшнековые экструдеры ZSK и STS, вращающиеся в одном направлении.Обе экструдерные линии обеспечивают плавное взаимодействие этапов процесса и бережное обращение с продуктом с максимальной производительностью.
Оборудование для кормления
ПитателиCoperion K-Tron обеспечивают непрерывную равномерную подачу с очень высокой кратковременной точностью и воспроизводимостью.В зависимости от сырья и требований процесса доступны различные модели и конфигурации питателей. Вибрационные питатели, одношнековые питатели или насосы для сыпучих продуктов для сыпучих материалов, таких как грануляты и пеллеты, двухшнековые питатели для сложных порошков, таких как наполнители, антипирены, пигменты или другие добавки, а также питатели для жидкостей и другие специальные питатели — это лишь некоторые из технологий, позволяющих разработать правильное решение для каждого приложения.
Подъемно-транспортное оборудование
Coperion и Coperion K-Tron разработали широкий спектр решений по транспортировке материалов для производства пенополистирола.Наши проекты включают полный спектр решений: компоненты для хранения и разгрузки материалов, пневматические и механические системы транспортировки, системы взвешивания и подачи, а также полные системы управления технологическим процессом. В транспортных решениях может использоваться давление или вакуум, обедненная или плотная фаза, в зависимости от характеристик материала и свойств применения. Разгрузка материалов может осуществляться от грузовиков, силосов, BBU (разгрузчиков биг-бэгов) до станций опрокидывания мешков (маленькие мешки) и перчаточных ящиков для токсичных или опасных материалов.Исходя из свойств материала и требований, мы с радостью интегрируем в наши системы другие функции, такие как удаление осадка, просеивание или другое оборудование, зависящее от вашего процесса.
Заводы и системы
Coperion предлагает системы из одного источника, включая весь наш опыт работы с материалами, подачи, компаундирования и экструзии.При планировании и установке компаундного завода у вас будет только одно контактное лицо, и вы получите выгоду от четко определенной ответственности за проект.
Глобальная служба
Наша сервисная структура состоит из более чем 350 сервисных инженеров и техников по всему миру, которые не только заботятся о ваших машинах и системах, но и о вашем бизнесе.Они видят себя партнерами, которые обеспечивают ваше будущее.
Загрузки
Посмотреть больше загрузок Увидеть меньше загрузок