ХиМиК.ru — ПОЛИКАРБОНАТЫ — Химическая энциклопедия
А Б В Г Д Е Ж З И К Л М Н О П Р С Т У Ф Х Ц Ч Ш Щ Э Ю Я
ПОЛИКАРБОНАТЫ, сложные
полиэфиры угольной к-ты и дигидроксисоединений общей ф-лы [—ORO—C(O)—]n,
где R-ароматич. или алифатич. остаток. Наибольшее пром. значение имеют ароматические
поликарбонаты (макролон, лексан, юпи-лон, пенлайт, синвет, поликарбонат): гомополимер ф-лы
I на основе 2,2-бис-(4-гидроксифенил)пропана (бисфенола А) и смешанные
поликарбонаты на основе бисфенола А и его замещенных-3,3′,5,5′-тетрабром- или 3,3′,5,5′,-тетраметилбисфено-лов
А (ф-ла II; R = Br или CH3 соотв.).
Свойства. Поликарбонаты на основе
бисфенола А (гомополикарбо-нат) — аморфный бесцв.
Физ.-мех. св-ва поликарбонатов зависят
от величины мол. массы. Поликарбонаты, мол.м. к-рых менее 20 тыс.,-хрупкие полимеры с низкими
прочностными св-вами, поликарбонаты, мол. м. к-рых 25
тыс., обладают высокой мех. прочностью и эластичностью. Для поликарбонатов характерны высокое
разрушающее напряжение при изгибе и прочность при действии ударных нагрузок
(образцы поликарбонатов без надреза не разрушаются), высокая стабильность размеров. При
действии растягивающего напряжения 220 кг/см2 в течение года не обнаружено
пластич.
Плотн. (при 25 |
1,20 |
||
|
1,5850 |
||
T. |
150 |
||
T. размягч., 0C |
220-230 |
||
, МПа |
65-70 |
||
, МПа |
95 |
||
Ударная вязкость
по Шарпи (с надрезом), кДж/м2 |
25-50 |
||
, кДж/(кг·К) |
1,17-1,2 |
||
Теплопроводность,
Вт/ (м·K) |
0,20 |
||
Коэф. |
(5-6)· 10 -5 |
||
Теплостойкость
по Вика, 0C |
150-155 |
||
e (при 10-108
Гц) |
2,9-3,0 |
||
Электрич. |
20-35 |
||
|
|||
при 1 МГц |
0,011 |
||
при 50 Га |
0,0007-0,0009 |
||
Равновесное влагосодержание
(200C, 50%-ная относит. |
0,2 |
||
Макс. поглощение
воды при 25 0C, % по массе |
0,36 |
||
Поликарбонаты характеризуются невысокой
горючестью. Кислородный индекс гомополикарбоната составляет 24-26%. Полимер
биологически инертен. Изделия из него можно эксплуатировать в интервале т-р
от — 100 до 135
Для снижения горючести
и получения материала с величиной кислородного индекса 36-38% синтезируют смешанные
поликарбонаты (сополимеры) на основе смеси бисфенола А и 3,3′,5,5′-тетрабромбисфенола А;
при содержании последнего в макромолекулах до 15% по массе прочностные и оптич.
св-ва гомополимера не изменяются. Менее горючие сополимеры, имеющие также более
низкое дымовыделение при горении, чем у гомополикарбоната, получены из смеси
бисфенола А и 2,2-бис-(4-гидроксифенил)-1.1 -дихлорэтилена.
Оптически прозрачные поликарбонаты,
обладающие пониж. горючестью, получены при введений в гомополикарбонат (в кол-ве
менее 1%) солей щелочных или щел.-зем. металлов ароматич. или алифатич. сульфокислот.
Напр., при содержании в гомополикарбонате 0,1-0,25% По массе дикалиевой соли
дифенилсульфон-3,3′-дисульфокислоты кислородный индекс возрастает до 38-40%.
Т-ру стеклования, устойчивость
к гидролизу и атмосферо-стойкость поликарбонатов на основе бисфенола А повышают введением
в его макромолекулы эфирных фрагментов; последние образуются при взаимод. бисфенола
А с дикарбоновыми к-тами, напр. изо- или терефталевой, с их смесями, на стадии
синтеза полимера. Полученные таким образом полиэфир-карбонаты имеют т. стекл.
до 1820C и такие же высокие оптич.
св-ва и мех. прочность, как у гомополикарбоната. Устойчивые к гидролизу поликарбонаты получают
на основе бисфенола А и 3,3′,5,5′-тетраметилбисфенола А.
Прочностные св-ва гомополикарбоната
возрастают при наполнении стекловолокном (30% по массе): 100 МПа,
160 МПа, модуль упругости при растяжении 8000 МПа.
Получение. В пром-сти
поликарбонаты получают тремя методами. 1) Переэтерификация дифенилкарбоната бисфенолом
А в вакууме в присут. оснований (напр., метилата Na) при ступенчатом повышении
т-ры от 150 до 300 0C и постоянном удалении из зоны р-ции выделяющегося
фенола:
Процесс проводят в расплаве
(см. Поликонденсация в расплаве)по периодич. схеме. Получаемый вязкий
расплав удаляют из реактора, охлаждают и гранулируют.
Достоинство метода — отсутствие
р-рителя; осн. недостатки — невысокое качество поликарбонатов вследствие наличия в нем остатков
катализатора и продуктов деструкции бисфенола А, а также невозможность получения
поликарбонатов с мол. м. более 50000.
2) Fосгенирование
бисфенола А в р-ре в присут. пиридина при т-ре
25 0C (см. Поликонденсация в растворе). Пиридин, служащий
одновременно катализатором и акцептором выделяющегося в р-ции HCl, берут в большом
избытке (не менее 2 молей на 1 моль фосгена). Р-рителями служат безводные хлорорг.
соединения (обычно метиленхло-рид), регуляторами мол. массы — одноатомные фенолы.
Из полученного реакц. р-ра
удаляют гидрохлорид пиридина, оставшийся вязкий р-р поликарбонатов отмывают от остатков
пиридина соляной к-той. Выделяют поликарбонаты из р-ра с помощью осадителя (напр., ацетона)
в виде тонкодисперсного белого осадка, к-рый отфильтровывают, а затем сушат,
экструди-руют и гранулируют. Достоинство метода — низкая т-ра процесса, протекающего
в гомог. жидкой фазе; недостатки-использование дорогостоящего пиридина и невозможность
удаления из поликарбонатов примесей бисфенола А.
3) Межфазная поликонденсация
бисфенола А с фосгеном в среде водной щелочи и орг. р-рителя, напр. метиленхлорида
или смеси хлорсодержащих р-рителей (см. Межфазная поликонденсация):
Условно процесс можно разделить
на две стадии, первая -фосгенирование динатриевой соли бисфенола А с образованием
олигомеров, содержащих реакционноспособные хлор-формиатные и гидроксильные концевые
группы, вторая -поликонденсация олигомеров (кат.-триэтиламин или четвертичные
аммониевые основания) с образованием полимера. В реактор, снабженный перемешивающим
устройством, загружают водный р-р смеси динатриевой соли бисфенола А и фенола,
метиленхлорид и водный р-р NaOH; при непрерывном
перемешивании и охлаждении (оптим. т-ра 20-250C) вводят газообразный
фосген. После достижения полной конверсии бисфенола А с образованием олигокарбо-ната,
в к-ром молярное соотношение концевых групп COCl и ОН должно быть больше 1 (иначе
поликонденсация не пойдет), подачу фосгена прекращают. В реактор добавляют триэтиламин
и водный р-р NaOH и при перемешивании осуществляют поликонденсацию олигокарбоната
до исчезновения хлорформиатных групп. Полученную реакц. массу разделяют на две
фазы: водный р-р солей, отправляемый на утилизацию, и р-р поликарбонатов в метиленхлориде.
Последний отмывают от орг. и неорг. примесей (последовательно 1-2%-ным водным
р-ром NaOH, 1-2%-ным водным р-ром H3PO4 и водой), концентрируют,
удаляя метиленхлорид, и выделяют поликарбонаты осаждением или посредством перевода из р-ра
в расплав с помощью высококипящего р-рителя, напр. хлорбензола.
Достоинства метода — низкая
т-ра р-ции, применение одного орг. р-рителя, возможность получения поликарбонатов высокой
мол. массы; недостатки — большой расход воды для промывки полимера и, следовательно,
большой объем сточных вод, применение сложных смесителей.
Метод межфазной поликонденсации
получил наиб. широкое распространение в пром-сти.
Переработка и применение.
Поликарбонаты перерабатывают всеми известными для термопластов способами, однако гл.
обр. — экструзией и литьем под давлением (см. Полимерных материалов переработка)при 230-3100C. Выбор т-ры переработки определяется вязкостью
материала, конструкцией изделия и выбранным циклом литья. Давление при литье
100-140 МПа, литьевую форму подогревают до 90-1200C. Для предотвращения
деструкции при т-рах переработки поликарбонаты предварительно сушат в вакууме при 115
50C до содержания влаги не более 0,02%.
Поликарбонаты широко применяют как
конструкц. материалы в автомобилестроении, электронной и электротехн. пром-сти,
в бытовой и мед. технике, приборо- и самолетостроении, пром. и гражданском стр-ве.
Из поликарбонатов изготовляют прецизионные детали (шестерни, втулки и др.), осветит. арматуру,
фары автомобилей, защитные очки, оптич. линзы, защитные шлемы и каски, кухонную
утварь и т. п. В мед. технике из поликарбонатов формуют чашки Петри, фильтры для крови,
разл. хирургич. инструменты, глазные линзы. Листы из поликарбонатов применяют для остекления
зданий и спортивных сооружении, теплиц, для произ-ва высокопрочных многослойных
стекол — триплексов.
Мировое произ-во поликарбонатов в 1980
составило 300 тыс. т/год, произ-во в СССР-3,5 тыс. т/год (1986).
Лит.: Шнелл Г.,
Химия и физика поликарбонатов, пер. с англ., M., 1967; Смирнова О. В., Ерофеева
С. Б., Поликарбонаты, M., 1975; Sharma C. P. [а. о.], «Polymer Plastics»,
1984, v. 23, № 2, p. 119 23; Factor A., Or Undo Ch. M., «J. Polymer
Sci. , Polymer Chem. Ed.», 1980, v. 18, № 2, p. 579-92; Rathmann D., «Kunststoffe»,
1987, Bd 77, № 10, S. 1027 31. В. В. Америк.
А Б В Г Д Е Ж З И К Л М Н О П Р С Т У Ф Х Ц Ч Ш Щ Э Ю Я
Как производят поликарбонат
Автор На чтение 6 мин Просмотров 1.1к. Опубликовано
Благодаря универсальным техническим характеристикам, таким как легкость, прочность, коррозийная стойкость, поликарбонаты являются очень востребованным материалом в различных отраслях промышленности: в производстве автомобилей, электротехнической, электронной промышленности, в производстве предметов бытового потребления и т.д. Составляя серьезную конкуренцию металлу и стеклу, за счет увеличения потребления конструкционных материалов доля литого и сотового поликарбонатов на мировом рынке с каждым годом завоевывает все новые позиции.
Производство поликарбоната — сложный технологический процесс, в основе которого лежит использование двухатомного фенола и угольной кислоты.
Поликарбонат является линейным полиэфиром этих двух составляющих компонентов. В зависимости от природы, поликарбонаты разделяются на алифатические, жирноароматические и ароматические. Практическое значение имеет лишь ароматический поликарбонат. Поликарбонаты относятся к разряду аморфных, инженерных пластиков, а изготовленные на их основе композиции — к специальным полимерам.
Содержание
- Достоинства поликарбоната
- Современные технологии изготовления поликарбоната
- Изготовление сотового поликарбоната
Достоинства поликарбоната
Схема структур сотового поликарбоната.Широкий диапазон использования литого и сотового поликарбоната обусловлен универсальными термическими, оптическими и механическими свойствами данного материала. Так, поликарбонат обладает высокой прочностью и жесткостью в сочетании с довольно высокой стойкостью к различным ударным воздействиям, в том числе и при повышенной или пониженной температуре.
Поликарбонат — морозостойкий, оптически прозрачный материал, способный выдерживать кратковременный нагрев до 153ºС и циклические перепады температур от +100ºС до -253ºС. Поликарбонат устойчив к агрессивному воздействию окислителей, растворов солей, кислот, но не обладает устойчивостью к действию щелочей, органических растворителей и концентрированных кислот.
Читайте также:
Поликарбонат: размеры листов и другие характеристики.
Инструкция по монтажу поликарбоната на металлический каркас своими руками.
О том, какой поликарбонат выбрать для навеса, читайте здесь.
Вернуться к оглавлению
Современные технологии изготовления поликарбоната
Процесс создания поликарбоната базируется на использовании одной из следующих технологий: поликонденсации, переэтерификации или межфазной поликонденсации.
Поликонденсация — это метод синтеза полимеров, базирующийся на реакциях замещения мономеров и/или олигомеров, которые, взаимодействуя между собой, образовывают побочные низкомолекулярные соединения.
Переэтерификация диарилкарбонатов проводится с ароматическими диоксисоединениями (так называемый нефосгенный способ). В качестве диоксисоединения выступает 2,2-бис-(4-оксифенил) пропан (диан, бисфенол А).
В промышленном производстве поликарбоната в настоящее время используется способ, базирующийся на межфазной поликонденсации. Согласно данному методу производится взаимодействие динатриевой соли бисфенола А с фосгеном в присутствии оснований. Протекающие при взаимодействии процессы практически необратимы. Данная технология используется для производства 80% поликарбоната в мире.
Наша отечественная технология также применяет метод межфазной поликонденсации фосгена с бисфенолом А. Очевидными недостатками данного метода является высокая токсичность реагента, склонность к образованию побочных продуктов и необходимость последующей очистки образующегося полимера от изначально применяемых реагентов и побочных компонентов.
Производство полимеров на основе новейших технологий ориентировано на нефосгенный метод выпуска, который базируется на процессах взаимодействия диметилового эфира угольной кислоты (ДМУК) и дифенилолпропана. Подобное решение позволяет перевести технологическую процедуру получения ПК из фазы жидкого состояния в расплав, исключить экологически опасный фосген и существенно увеличить объемы производства.
Бесфосгенный метод по всем параметрам, кроме энергетических расходов, превосходит традиционные технологии. Но пока и он не лишен некоторых недостатков, в число которых входит побочное выделение анизола, не имеющего на данном этапе полезного применения в том объеме, который образуется в ходе нефосгенной реакции. Мировое потребление анизола в настоящее время составляет до 7 тыс. тонн, поэтому излишки материала отправляются на сжигание. Еще одним существенным минусом нефосгенной технологии является невозможность получения ряда марок поликарбоната — высокомолекулярного поликарбоната и сополимеров на основе поликарбоната.
Поликарбонатный гранулят, как известно, является основой для производства листов поликарбоната, в число которых входит и сотовый поликарбонат. Этот материал представляет собой листы ячеистой структуры, выполненные из полимера в виде сот, которые состоят из двух слоев, соединенных посредством внутренних ребер жесткости между собой. Сотовый поликарбонат — легкий, устойчивый к коррозийным процессам, ударопрочный материал с хорошими теплоизоляционными и светопрозрачными свойствами.
На рынке, помимо обычного сотового поликарбоната, можно встретить и более долговечный его аналог — полимер, покрытый специальным защитным слоем, устойчивым к ультрафиолетовому излучению. Благодаря своим универсальным свойствам сотовый поликарбонат очень востребован в строительстве и сельском хозяйстве. В зависимости от толщины, он выступает в качестве прекрасного материала для оборудования навесов, арок, крыш, витрин, перегородок, бассейнов, теплиц, балконов, автобусных остановок, вокзалов, стадионов и т. д., поэтому в число целевых потребителей материала входят автостоянки, муниципалитет, рекламные и дизайнерские компании, АЗС, подрядчики, тепличные хозяйства и сельскохозяйственные предприятия.
http://polikarbonatstroy.ru/youtu.be/YF3Cii8-Ssk
Вернуться к оглавлению
Изготовление сотового поликарбоната
Для производства сотового поликарбоната используются поликарбонатные гранулы. Изготовление материала включает в себя прохождение гранулами цикла определенных технологических процессов. Производство сотового поликарбоната предполагает наличие:
Схема воздействия солнечных лучей на поликарбонат.- гранул поликарбоната;
- специализированного оборудования;
- специальных химических добавок.
Вначале закупается поликарбонатный гранулят. Стоит учитывать, что, в зависимости от цвета гранул (которые могут быть белыми, цветными и прозрачными), в конечном итоге получится материал определенной цветовой гаммы. Поэтому при покупке стоит обращать внимание на цвет сырья.
После взвешивания, сортировки, очистки от пыли для производства листов гранулы поступают на плавление.
В камере плавления гранулы переходят из твердого состояния в жидкое, к ним добавляются специальные компоненты, способствующие улучшению характеристики будущего материала. В конечном итоге образуется однородная смешанная масса.
Далее начинается процесс экструзии, в ходе которого бесформенная масса преобразуется в нужную структуру, монолитную или сотовую. Помимо основного процесса экструзии, поликарбонатная масса одновременно подвергается соэкструзии тонкой пленкой, поглощающей ультрафиолетовое излучение, что способствует сохранению превосходной прочности материала.
На следующем этапе прозрачный или цветной сотовый поликарбонат в виде тонких пластин, скрепленных между собой прочными ребрами жесткости, подается на конвейер.
http://polikarbonatstroy.ru/youtu.be/rLFh_d8Y1h8
После остывания пластины поликарбоната нарезаются на нужные размеры, складируются и в многослойных, защищенных от проникновения влаги мешках поступают на хранение.
Производство поликарбонатов
На этой странице мы собираемся делать поликарбонаты. Прежде чем мы это сделаем, давайте взглянем на наш состав персонажей. Две наши ведущие молекулы бисфенол А и фосген. Вы можете увидеть их ниже в обычном порядке мы рисуем молекулы или видим их в 3D ниже.
Модель слева внизу представляет собой изображение модели BPA pdb, которую вы можете просмотреть, щелкнув здесь, или вы можете просто щелкнуть само изображение. На втором изображении мономер хлорангидрида фосген. В любом случае, обязательно закройте новые окна, которые открываются с 3D-моделью, когда будете готовы вернуться сюда.
Сейчас мы будем беспокоиться только о бисфеноле А. мы доберемся до
фосген позже. Первым этапом изготовления поликарбоната является обработка
бисфенол А с NaOH. Гидроксильная группа будет делать какие основания
сделать и унести протон от бисфенола А. Когда это произойдет
гидроксильная группа становится молекулой воды, а бисфенол А,
спирт, окажется в виде его натриевой соли. Затем то же самое
реакция происходит снова на другой спиртовой группе бисфенола А.
кликните сюда чтобы увидеть фильм этого шага реакции.
Теперь, когда бисфенол А представляет собой соль, он может работать с фосгеном. (Помните фосген?) Вы видите, что кислород в соли бисфенола А теперь отрицательный заряд на нем. Это означает, что он может отдать пару электронов атому углерода в фосгене. Помните, что углерод не хватает электронной плотности, потому что он находится рядом с этим электроотрицательным кислород. Когда этот углерод получает новую пару электронов от соль бисфенола А, она освобождается от одной из пар, которые она разделяла. неравномерно с карбонильным кислородом. Эта пара держится на том, что кислород, придающий ему отрицательный заряд.
Но не думайте, что он хотел бы остаться таким. Отнюдь не.
электроны на этом кислороде сместятся обратно к углероду, реформируя
двойная связь углерод-кислород. Конечно, мы знаем, что углерод не может
разделяют десять электронов, поэтому он должен избавиться от двух. Два электрона на
получить ботинок — это пара, которую углерод поделился с одним из
атомы хлора. Таким образом, хлор и его электроны выбрасываются из
молекула. Оставшаяся молекула называется 9.0032 хлорформиат .
Что касается выброшенного иона хлора, то он объединится с этим
ион натрия, который тихо слонялся вокруг во время всей этой суматохи, чтобы
образуют NaCl.
кликните сюда чтобы увидеть фильм этого шага реакции.
Этот хлорформиат может быть атакован другой молекулой бисфенол А, как и фосген. Вторая молекула бисфенола А может атаковать так же, как и первый.
И он проходит через подобное промежуточное звено и аналогичную игру
электронные музыкальные стулья, чтобы показать виды, содержащие карбонаты.
кликните сюда чтобы увидеть фильм этого шага реакции.
После того, как это произойдет, солевые группы на большой новой молекуле могут сформироваться. реагировать с большим количеством фосгена, и таким образом молекула растет, пока мы бери поликарбонат.
Если вы хотите посмотреть фильм всего процесса, нажмите здесь.
Теперь немного веселья: на самом деле сделать поликарбонат самостоятельно. Проблема в том, что это довольно опасно, а это значит, что это следует делать только в вытяжном шкафу с хорошей вентиляцией и под наблюдением опытного ученого-синтетика.
И я просто слышу, как вы говорите: «Что ты имеешь в виду под «опасно»?? Я действительно могу пораниться?»
Вот сенсация: реагент, который запускает синтез, называется «фосген», обманчиво простое и безобидно звучащее название, верно? НЕПРАВИЛЬНЫЙ!! На самом деле фосген — это то, что называют «военным газом», настолько ядовитым, что, когда он применялся в Первой мировой войне во время так называемой «окопной войны» в Европе, он убил сотни, а может быть, и тысячи солдат. И это не просто не просто «бам, бах, ты мертв!» способ. Нет, фосген обладает восхитительным свойством, общим для всех хлорангидридов карбоновых кислот: он гидролизуется в воде с образованием HCl, одной из самых сильных известных кислот. Таким образом, когда фосген вдыхается после того, как он оседает в вашем бункере или траншее (он тяжелее воздуха), он превращается в концентрированную HCl в ваших легких. Это не убивает вас сразу. Вместо этого он медленно разъедает легочную ткань, заставляя ваше тело наполнять легкие водой, что, в свою очередь, заставляет вас тонуть, даже если вы не находитесь под водой. Ужасный путь. Итак, безопасность прежде всего: достаточно ли сказано?
Все еще хотите попробовать?
Если вы все еще хотите попробовать это и обещаете быть предельно осторожными, щелкните здесь, чтобы просмотреть процедуру, и здесь, чтобы загрузить копию.
И вам нужно ЗНАТЬ, что вы действительно сделали полимер, верно? Лучший способ — получить спектр ЯМР или два выделенного продукта. Перейдите сюда, чтобы просмотреть спектр 1 H, и здесь, чтобы увидеть спектр 13 C.
Хорошая новость заключается в том, что существует альтернативный, гораздо более безопасный способ производства поликарбоната, в котором не используется фосген. Мы поговорим об этом подробнее в следующем разделе, так что следите за обновлениями…
Вернуться на страницу поликарбонатов |
Вернуться в каталог четвертого уровня |
Вернуться к Справочник Макрогалереи |
Поликарбонат The Division 2 — выращивание поликарбоната, где быстро достать поликарбонат полезное снаряжение на каждом этапе, вам нужно будет обновить свой верстак. Для этого требуется множество различных материалов для крафта, некоторые труднее найти, чем другие. Одним из самых редких является поликарбонат, который необходимо использовать для повышения с мирового уровня 4 до 5.
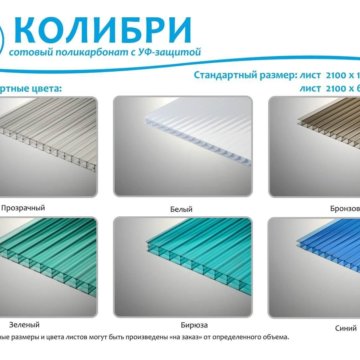
- Дивизион 2 Поликарбонат
- The Division 2: как получить поликарбонат
- The Division 2 Поликарбонатное сельское хозяйство
- Поликарбонат можно найти в канализации
- Разберите броню, чтобы получить поликарбонат
- Набор стандартных материалов The Division 2 — купить поликарбонат в магазине
Поликарбонат — это редкий ресурс, который можно найти разными способами в The Division 2. Он понадобится вам для изготовления снаряжения и улучшения вашего верстака. Когда вы достигнете мирового уровня 5 и вам нужно будет обновить свою скамейку, вам нужно будет накопить 200 поликарбонатов, что немаловажно, если только вы не активно искали его с самого начала. Однако есть несколько способов быстро получить его, поэтому давайте посмотрим.
The Division 2: Как получить поликарбонат
В The Division 2 есть несколько способов получить поликарбонат, но обычно он не выпадает из врагов. Вам нужно будет разграбить окружающую среду, чтобы получить большую ее часть, чему способствует пополнение контрольных точек на карте. Вы также можете получить его за разборку определенных доспехов, хотя это, безусловно, не лучший способ получить его.
Выращивание поликарбоната в Дивизионе 2
Лучший способ получить поликарбонат в Дивизионе 2 — делать контрольные точки. В частности, вы захотите сделать контрольные точки, контролируемые гиеной. Лучший из тех, что мы нашли, называется Солнечная ферма и находится в юго-восточной части карты. Мы включили экран ниже.
Что вам нужно сделать, так это захватить контрольную точку, а затем отправиться к офицеру контрольной точки. Жертвуйте ресурсы, пока не активируете перк осведомленности. Это подсветит добычу в районе, коих здесь тонна. Нам удалось получить около 90 поликарбонатов, разграбив эту точку, а затем область к востоку. Эти акции также обновляются каждые 24 часа, так что продолжайте расти, и у вас будет все, что вам нужно, в кратчайшие сроки.
Поликарбонат можно найти в канализации
Еще один отличный способ получить поликарбонат — спуститься в подземелье. Здесь много добычи и большой потенциал для получения поликарбоната. Мы рекомендуем связать это во время поиска ключей. Двух зайцев одним выстрелом, так сказать.
Разобрать броню, чтобы получить поликарбонат
Наконец, вы можете разобрать нагрудник, чтобы получить поликарбонат. В любом случае это не самый прибыльный метод, но если у вас есть запас снаряжения, обязательно разберите его как можно больше. В частности, из легендарного нагрудника выпадает много поликарбоната.
Набор стандартных материалов The Division 2 — купите поликарбонат в магазине
Если ваша учетная запись uPlay связана с The Division 2, вы можете потратить 20 кредитов, чтобы получить 30 единиц поликарбоната в составе набора стандартных материалов.