Как делают фанеру и все про изготовление фанеры
В России очень много лесов, которые идут под производство фанеры и других строительных материалов. И если оцилиндровка бревен, распиловка и другие наиболее часто используемые способы обработки древесины не вызывают вопросов, то изготовление фанеры может быть достаточно интересным процессом.
На деревообрабатывающем заводе материалы для производства фанеры проходят несколько стадий. И начинается все с березовых бревен, которые сюда привозят. По сути, перед началом производства бревна не проходят никакой специальной подготовки. Их просто спиливают и привозят на завод.
Первым этапом производства является подготовка бревен. Их специально размачивают в теплой воде, чтобы они впитали как можно больше влаги и стали готовыми для использования. После этого их достают и разрезают по длине на необходимый размер.
Разрез бревен производится в специальных станках, которые распиливают бревна по спирали на очень тонкие пластины. Конечно, реальных пластин на этом этапе не получается, на выходе получается что-то вроде деревянной тонкой спирали, которую после этого растягивают в один лист и разрезают на пластины. В качестве отходов на этом этапе остаются сердцевины от бревен, которые затем используют как вторичное сырье для производства других типов строительных материалов.
После получения деревянных листов полученный материал тщательно сортируется. После этого несколько пластин складывается воедино и склеивается между собой. При этом каждая последующая пластина в слое укладывается так, чтобы было чередование исходя из направления волокон: вдоль и поперек по очереди. Такие чередования пластин при укладке обязательны, потому как делают фанеру более прочной.
Если толщина каждого листа дерева составляет порядка миллиметра, то требуется примерно пять или шесть слоев, чтобы получилась фанера толщиной в пять миллиметров. Для склейки используется специальный клеящий материал, который сушится несколько дней после проклейки. Так высыхает непосредственно сам клей, а также каждый слой фанеры.
После просушки фанера разрезается на пластины заданного размера. В зависимости от полученных пластин, фанера сортируется по размеру, толщине, проверяется ее качество.
В зависимости от типа фанеры пропитка может производиться не только водой, но и специальными средствами. Кроме этого, после пропитки водой фанеру могут пропитывать средствами для приобретения ею определенных свойств, например, для придания большей долговечности, теплостойкости или огнестойкости.
Также полученные листы фанеры могут подвергать внешней обработке, например, шлифованию, покраске, и так далее.
Советуем почитать
Укладка фанеры на пол
Фанеру можно назвать одним из наиболее универсальных материалов, которые придумал человек. Повсеместно применяется это сырье в строительной отрасли. В соотношении цена-качество фанере нет конкурентов. Чаще всего она используется для настила и ремонте пола. Однако высокая функциональность этого материала обуславливает и большое число методик работы с ним, поэтому нужно детально рассмотреть все нюансы.
25 февраля
Фанера для пола
Фанера – это материал, который отлично подходит для создания и ремонта разных напольных покрытий. Ее использование распахивает для строителей значительные перспективы в обустройстве не только финишного перекрытия, но и крепежа чернового пола. В этой статье мы попытаемся разобраться в том, какую фанеру нужно купить для пола и на чем нужно акцентировать внимание во время покупки этого материала?
24 февраля
Производство фанеры — виды, материалы, технологии
Содержание
- Что такое фанера?
- Размеры
- Виды
- Состав
- Подробнее
Что такое фанера?
Для изготовления фанеры можно использовать множество пород дерева, но лучше всего для технологии производства фанеры подходит берёза. Такая древесина имеет равномерную плотность и высокую прочность, что очень важно для получения качественного шпона. Из хвойных пород дерева чаще всего выбирают сосну и лиственницу. Вообще, хвою редко используют для производства, так как содержащиеся там смолы затрудняют изготовление шпона.
Технология производства фанеры состоит из нескольких этапов. Сначала древесину вымачивают для того, чтобы уровнять влажность дерева. Затем производят лущение и нарезку на листы. Полученный шпон сушат, после чего наносят на них клей и прессуют. Полученный материал шлифуют и ламинируют.
Размеры
Материал фанеры обладает малым весом и устойчивостью к механическим воздействиям, благодаря чему её легко обрабатывать и монтировать. Толщина варьируется от 3 до 30мм. Количество слоёв шпона обычно нечётное (от 3 до 21). Она экологичнее, прочнее и обладает лучшими теплоизоляционными свойствами, чем МДФ и ДСП. Кроме того, ламинированная обладает большей прочностью и устойчивостью к влаге.
Виды
Обычно разделяют на два самых популярных вида фанеры: ФК (влагостойкая) и ФСФ (повышенной влагостойкости). Они отличаются друг от друга используемым клеящим составом.
Для производства влагостойкой — используют карбамидную смолу. ФК используется при внутренней отделке помещений, теплоизоляции и изготовлении мебели.
Состав
С повышенной влагостойкости — самый популярный вид фанеры. ФСФ производится с использованием фенолформальдегидной смолы, благодаря которым материал фанеры имеет большую устойчивость к механическим воздействиям и влаге. Благодаря этому ФСФ применяются в строительстве и кровельных работах.
Подробнее
ФБС — самая прочная и водостойкая. Это обуславливается тем, что каждый лист шпона перед проклеиванием обрабатывается специальным бакелитовым лаком. Благодаря его выдающимся свойствам, материал фанеры применяется в строительстве самолётов и кораблей.
Также, в зависимости от количества дефектов наружного слоя шпона, листы делят на пять категорий, от E (элита) до четвёртой.
Как производится фанера?
В блоге Plyco, посвященном фанере и шпону, содержится информация о продуктах, практические советы и идеи для реализации проектов в стиле «сделай сам», архитектурных и профессиональных проектов. Мастер-классы по изготовлению фанеры и обновления каталога помогут вам завершить проект в кратчайшие сроки.
Подробнее
Категории
Все сообщения
Этот пост является частью руководства Plyco по фанере.
Почти все слышали о фанере, но знаете ли вы, как она делается? Конечно, вы, возможно, знаете, что фанера состоит из трех или более тонких слоев дерева, соединенных клеем, но что на самом деле нужно для изготовления Plyco Decoply? Какие процессы используются при создании нашей березовой фанеры премиум-класса? Как именно мы можем оказаться с морской фанерой на нашем пороге? Здесь, в Plyco, мы одержимы всем, что связано с Ply, от ДСП до фанерных панелей, поэтому мы подумали, что было бы интересно подробно рассказать о том, что происходит за кулисами.
Доверьтесь процессу Plyco
Все начинается с деревьев. Деревья, используемые для производства фанеры, как правило, меньше, чем деревья, используемые для других видов древесины, таких как пиломатериалы, в то время как фанера может быть изготовлена как из твердых пород дерева, таких как клен, тополь и береза, так и из хвойных деревьев, таких как сосна лучистая, сосна обручная и лауан. .
Деревья происходят из плантации, за которой тщательно ухаживают. Сначала выбранные деревья маркируются, чтобы знать, какие из них готовы к вырубке. Это делается с помощью бензопил или валочных машин — больших гидравлических ножниц, которые крепятся к передней части автомобиля.
Ты крутишь меня прямо
После того, как эти могучие деревья были срублены, их перетаскивают на погрузочную площадку с помощью удобных транспортных средств, известных как трелевочные тележки. Здесь бревна нарезаются по размеру и загружаются на грузовики в виде длинной кучи, называемой бревенчатым настилом. После резки и загрузки древесина готова начать свое увлекательное путешествие на фанерный завод.
По прибытии в новый дом бревна подбираются погрузчиками по мере необходимости и помещаются на цепной конвейер, который доставляет их к окорочному станку — что-то вроде кассы в местном супермаркете, только немного больше. Окорочный станок удаляет кору с помощью шлифовальных кругов с острыми зубьями или струй воды под высоким давлением при вращении бревна. Затем эти бревна перемещаются на другую конвейерную ленту, где циркулярная пила разрезает их на секции, подходящие для изготовления стандартных фанерных листов. Вы часто будете слышать, как их называют блоками-пилерами.
Итак, шпон, но пока
Следующий шаг в этом волшебном процессе требует изготовления деревянного шпона. Однако, прежде чем мы слишком увлечемся, блоки для очистки должны быть нагреты и замочены, чтобы смягчить древесину, путем их пропаривания или погружения в горячую воду в процессе, который занимает 12-20 часов в зависимости от типа древесины и множества других. характеристики. После нагрева блоки транспортируются на токарно-винторезный станок, где они подаются по одному. Токарный станок быстро вращает блок, и лезвие ножа снимает с поверхности непрерывный лист шпона.
Здесь становится жарко
Теперь, когда у нас есть наш лист шпона, вы можете сразу его обработать, хранить в многоуровневом лотке или намотать на рулон. Отсюда следующий шаг требует резки шпона на полезную ширину. На этом этапе оптические сканеры ищут участки с недопустимыми дефектами и вырезают их. Похож на Терминатора, но из фанеры. Затем виниры будут укладываться в соответствии с классом, что можно сделать вручную или с помощью нашей технологии Terminator. Наконец, отсортированные секции сушат для удаления влаги.
Шпон у нас есть, так что пора начинать веселье. Сейчас идет процесс укладки и склеивания деталей, который должен выполняться вручную или полуавтоматически с помощью машин. В случае трехслойного листа задний шпон укладывается ровно и проходит через шпатель, нанося клей на верхнюю поверхность. Короткие отрезки основного шпона укладываются поперек, и весь лист проходит через раскладчик во второй раз. Затем лицевой шпон укладывается поверх клееного сердечника.
Ситуация накаляется, поскольку мы подошли к насущной стадии процесса. Листы загружаются в горячий пресс, который может обрабатывать невероятные 20-40 листов за раз! Когда все листы загружены, пресс сжимает их вместе с огромным давлением и нагревает примерно до 110-157 градусов по Цельсию. Примечательно, что прессование завершается уже через 2-7 минут.
На финишной прямой
После разгрузки листы пропускаются через пилы, обрезая их до окончательной длины и ширины. Затем лицевые стороны фанерной плиты будут отшлифованы с помощью ленточных шлифовальных машин или вручную точечно отшлифованы в зависимости от сорта.
Красивое конечное изделие из фанеры
Наконец, листы оцениваются, а затем отправляются к нам в Plyco, где по прибытии им устраивают аплодисменты. Самый последний шаг процесса фанеры происходит, когда наши замечательные клиенты покупают лист, который доставляется нашим парком грузовиков из наших офисов в Морнингтоне и Мельбурне или через перевозчиков и курьерские компании для межгосударственных и региональных поставок. В качестве альтернативы, если у вас есть средства, вы можете прийти к нам лично и забрать свою новую блестящую фанеру домой.
- Нет предложений, так как поле поиска пусто.
Популярные сообщения
Подписаться на последние новости
Похожие сообщения
Производственный процесс — ООО «Китроник» Подвести итоги производственного процесса; бревна очищают от шпона, шпон намазывают клеем, укладывают так, чтобы направление волокон каждого шпона было перпендикулярно соседнему шпону, спрессовывают вместе, обрезают и шлифуют.
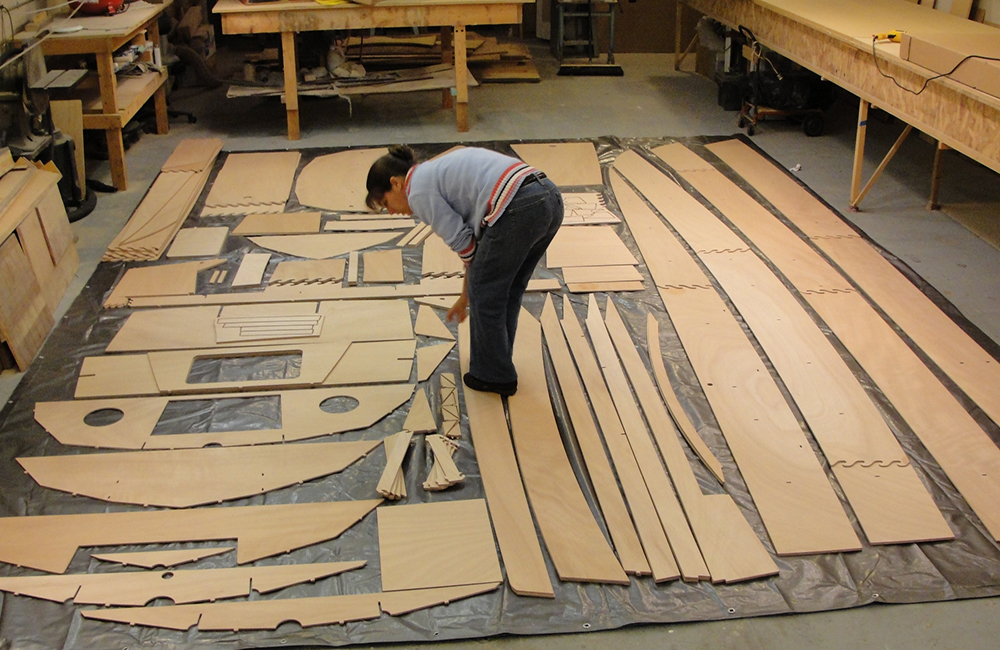
Но в производственном процессе есть нечто большее, чем просто…
Этап 1: Лес
Для нас важно, чтобы все необработанные бревна, используемые в нашей фанере, поступали из законных и устойчивых лесных концессий. Для обеспечения этого мы используем только заводы, которые придерживаются Политики ответственных закупок Федерации торговли лесоматериалами.
Как только деревья достигают приемлемого уровня зрелости, их вырубают обученные сборщики урожая. В зависимости от работы мельницы, транспортные средства, подобные тем, что на изображении выше, могут использоваться для выбора и валки деревьев с использованием спутниковых изображений.
Этап 2: Транспортировка на заводБревна вывозятся из лесхоза на лесопилку для переработки.
Транспорт в некоторых случаях сопряжен с собственными экологическими проблемами, поскольку лесные массивы вырубаются, чтобы освободить место для дорог, и поэтому новые деревья не могут расти.
По прибытии на завод бревна хранятся на складе бревен. Заводы будут использовать различные методы для удержания влаги в бревнах, многие из которых выбирают спринклерные системы. Затем бревна в конечном итоге доберутся до бревенчатого пруда. Бревна погружают в воду на длительный период времени, чтобы их было легче распилить по размеру и легче чистить. На некоторых заводах в более холодном климате есть пруды с подогревом бревен, поскольку тепло также улучшает качество лущения; они называют это гидротермальной обработкой.
Этап 4. Окорка бревен
Перед распиловкой и лущением бревен необходимо удалить кору. Заводы используют такие промышленные машины для окорки бревен по мере их продвижения по производственной линии.
Этап 5. Резка бревен Затем необработанные бревна распиливаются по размеру.
Бревна лупят с помощью токарно-карусельного станка. Это очищает бревно аналогично точилке для карандашей, за исключением того, что лезвие полностью параллельно бревну во время резки. Вы можете увидеть этот процесс в действии на видео выше и увидеть, как они выходят из задней части машины для очистки прямо на конвейер в видео ниже.
Этап 7: Калибровка и классификация После очистки полученные листы подаются на следующий этап конвейера, как показано на изображении ниже.
После лущения шпон длинными потоками перемещается по производственной линии. Их нужно обрезать по размеру и пройти первоначальный процесс сортировки. Сортировка особенно важна в отношении березовой фанеры (лазерной печати), поэтому большинство заводов используют технологию сканирования для проверки дефектов шпона, резки до необходимых размеров, а затем отделения потенциального лицевого шпона от основного шпона.
В отличие от заводов из Восточной Европы и Прибалтики, такие страны, как Китай, будут лущить шпон на более мелкие квадраты, а затем сшивать их до соответствующего размера, что является более экономичным (но снижающим качество) методом.
Этап 8. Сушка виниров
На данный момент шпон еще влажный из-за замачивания в бревенчатом пруду. Виниры должны быть высушены по целому ряду причин; от защиты древесины от грибкового распада до повышения механических свойств готовой доски. На большинстве заводов используются большие промышленные сушилки, которые часто соединяются с машиной для очистки бревен через ленточный конвейер; однако можно использовать и более экономичные методы. Например, некоторые очистители бревен в Китае оставляют фанеру на открытом воздухе для просушки в течение дня.
После высыхания виниры необходимо отремонтировать там, где есть дефекты. В случае с березовой фанерой, например, открытые сучки (там, где раньше были ветки) можно «заткнуть». Трещины в шпоне на фанере также можно заполнить, а шпон неподходящего размера можно срастить вместе (см. выше) . На некоторых фабриках есть машина, которая сканирует шпон и автоматически затыкает открытые отверстия или сучки. (См. ниже).
Этап 10: Нанесение клея и укладкаВиниры проходят через машину для склеивания, которая, по сути, наносит клей на лицевую и обратную стороны шпона. Затем их укладывают поверх неклееного шпона так, чтобы стопка чередовалась; Склеенный, не склеенный, склеенный, не склеенный и так далее.
Этап 11. Холодное прессование
Холодное прессование происходит после нанесения клея для подготовки виниров к горячему прессованию. Это помогает выровнять шпон и обеспечить равномерное распределение клея по шпону.
Шаг 12: Горячее прессование (Daylight Press) На этом этапе производственного процесса собственно панели начинают обретать форму. Несколько панелей загружаются в пресс дневного света. Затем Daylight Press сжимает и поддерживает нагретое давление на доски в течение длительного периода времени. Это создает и поддерживает необходимый контакт между клеем и винирами. Это также уменьшает натяжение клеевого шва и толщину слоя клея.
После горячего прессования плиту оставляют для стабилизации и охлаждения перед дальнейшей обработкой. Затем нужно обрезать излишки шпона, чтобы у доски были прямые края, затем доски чаще всего шлифуют с помощью большой промышленной шлифовальной машины.
Этап 14: Контроль качества Конечный продукт должен быть оценен по качеству, но было бы не очень эффективно просто ждать окончания процесса, чтобы обнаружить большую проблему с производством. По этой причине фабрики контролируют свое производство, проводя ряд тестов на различных этапах производственного процесса, например.