Печи металлические для бани. Печи для русской бани, сделанные своими руками
Содержание
- Печи металлические для бани. Печи для русской бани, сделанные своими руками
- Безопасная печь для бани. Режим работы печи
- Печь для дачной бани. Обзор 10 лучших видов печей для бани
- Как выбрать печь для бани
- Лучшая печь для бани с баком для воды
- Лучшая печь для бани с теплообменником
- Лучшая печь для бани из чугуна
- Самодельные печи для бани из металла: чертежи. Чертежи печи для бани из металла
- Этапы изготовления
- Бак для воды и место для камней
- Дымоход
- Виды печей для бани. Виды кирпичных печей для бани
- Видео металлическая печь для бани своими руками.
Печи металлические для бани. Печи для русской бани, сделанные своими руками
Самое главное при изготавливании по чертежам металлических печей для бани своими руками – это учесть, что невозможно при разогретых металлических стенках поддерживать нужную температуру в пределах 60-65 ºС (прочитайте: “Чертежи банной печи из металла – строим печь своими руками”). Обязательно придется перетапливать, что сопровождается излучением сильных ИК волн, при котором довольно тяжело находиться рядом с печью.
Решить эту проблему можно двумя методами:
- Произвести футеровку топки . Процесс заключается в обкладывании топки изнутри огнеупорным кирпичом. Достаточно укладки на ребро, при этом толщина футеровки составит 6 см, хотя встречается и узкий шамот, толщиной 3 см. Как бы то ни было, нагрев стальных стенок является незначительным, больше всего прогревается каменка. Поэтому сразу следует спроектировать топку, чтобы она была увеличенных размеров, потому как большая часть ее объема отводится на футеровку. Недостатком такого способа считается то, что в результате вырабатывается горячий дым, что понижает пожаробезопасность. Лучше всего провести его охлаждение путем установки бака или каменки на трубу. Немного сложнее – установить отопительный щиток, проходя через который, дым остывает до 80-120 ºС.
- Установить кирпичный экран вокруг печи из железа для бани.
Его собирают из керамического кирпича, при этом в стенке оставляют окошки для монтирования дверок, которые позволят в будущем контролировать уровень прогрева воздуха. Можно сделать вывод, что такой вариант является лучшим из-за возможности регулирования температуры, однако он менее практичен, так как задняя стенка очень сильно перегревается, поэтому приходится в конструкцию включать жаропрочную сталь. В таком случае получается, что для более продолжительного срока службы железной банной печи, нужно выбирать довольно толстый металл. Его, как показывает практика, лучше устанавливать в верхней и нижней части топки.
Источник: https://milyj-dom.ru-land.com/stati/pechi-metallicheskie-dlya-bani-metallicheskie-pechi-dlya-bani-kak-izgotovit-i-ustanovit-kakie
Безопасная печь для бани. Режим работы печи
Следующий шаг в решении проблемы, как выбрать печь для бани – это определение режима эксплуатации отопительного агрегата.
Чтобы понять, какая модель лучше, следует ознакомиться с принципом работы таких агрегатов. Многообразие моделей может привести к замешательству и неправильному выбору. Сначала четко представьте себе, какую бы вы хотели иметь печь, как должна производиться топка печи. По режиму работы их можно разделить на два класса:
- Непрерывного действия . Здесь огнем производится нагрев ящика, произведенного из металла или чугуна, в котором помещаются камни (служат для аккумуляции тепла в себе). Эти печи хороши тем, что есть возможность начинать париться практически сразу при нагреве камней. Такие печи безопасны, невозможно попадание угарного газа в парилку т.к. вода попадает на камни. Они имеют небольшую толщину стенок и малые объемы засыпки греющих элементов. Здесь железная плита отделяет камни из дымовых газов, температура нагрева поверхности каменки составляет до 350ºС . Отсутствует сажа на камнях. Есть возможность протапливать печь многократно, даже во время проведения банных процедур. В таких печах используется больше топлива, но в парилке можно находиться любое количество времени.
Такую печь требуется топить постоянно в связи с небольшой теплоемкостью. В результате — небольшой КПД, уходит много топочного материала. Зато в парной отсутствует образование копоти и угарного газа.
- Печи периодического действия . Здесь производится прямой нагрев камней каменки . По такому принципу работают общественные бани, в которых топка производится газом всю ночь, прогревая чугунные плиты, чтобы они отдавали тепло в течение следующего дня. Такую конструкцию требуется несколько часов протапливать, чтобы прогреть массив камней. Камни прогреваются открытым пламенем, температура может достигать до 1000ºС . При более низкой температуре нагретые элементы покрываются сажей, которая вместе с паром поднимается в воздух, если камни облить водой. Это простая конструкция печи. Большим минусом является невозможность париться до полного прогрева камней и парилки . При открытии заслонки с камней сразу начнет попадать угарный газ в помещение. После полного прогрева закрывается задвижка в трубе, и накопившееся тепло прогревает помещение, а не вылетает в трубу.
КПД таких печей значительно выше, чем с постоянным действием. И затраты топлива ниже. Но зато, поддавая пар, ценители могут уловить приятный аромат дымка. Их безопасность ниже, чем у предыдущей конструкции.
Печь для дачной бани. Обзор 10 лучших видов печей для бани
Печи для бани отличаются внешним видом, внутренней системой функционирования и характеристиками. Несмотря на то, что модели разные, цель у них одна – обогревать баню, способствуя созданию нужного микроклимата.
Как выбрать печь для бани
- Тепловая мощность. Главный критерий выбора. Она должна быть достаточной для обогрева парилки и смежных помещений в летнее время за полчаса, в зимний период при морозах за 2 часа. Для умеренной по возможностям печи средняя цифра приближена к 10 кВт.
- Емкость аккумулятора тепла. Пар не должен быть прозрачным. Для нормального режима достаточно 100 г воды на 1 м3. Температура не должна падать ниже 100˚С, иначе пар получится на выходе тяжелым и сырым.
- Материал. Хромистая сталь – оптимальный вариант. Риск сжигания кислорода отсутствует. Есть также модели из чугуна, обычной стали.
- Длительность работы. Печь должна работать как минимум 3-4 часа, долго сохранять тепло. Быстро остывающие модели каждый раз придется заново разжигать.
Важные параметры:
- Вид топлива. Дрова, газ и электричество. Экземпляр на дровах – традиционный. Он гарантирует быстрый, равномерный обогрев и благоприятный микроклимат. Идет с дымоходом и без него. В его отсутствие гарь уходит через отдушник.
Электрический – современный способ. Отличается точным контролем температурного режима. Для нормальной работы нужна стабильная подача электричества.
Газовая модель подразумевает полную самостоятельность. Она поддается автоматизации. Подойдет тем, у кого в регионе низкие тарифы на газ.
- Тип каменки. При открытой системе воздух прогревается раскаленными камнями. Такая печь быстро обогревает парилку, подходит для часто посещаемых бань.
Закрытая увеличивает время прогрева помещения.
- Наличие теплообменника. Позволяет экономить дрова и поддерживать высокую температуру в бане.
- Дизайн. Печь может быть любого размера, оттенка и формы.
- Цена. Стоимость на умеренную по мощности модель не превышает 20 000 р.
Второстепенные параметры:
Лучшая печь для бани с баком для воды
Термофор Калина Карбон удобна в пользовании, компактна и не уступает вариантам премиум-класса по возможностям и качеству сборки.
У нее логичное и удобное расположение элементов управления, все части плотно пригнаны друг к другу, корпус черного цвета с матовой текстурой из конструкционной стали – материала, устойчивого к коррозии и царапинам.
Панорамное стекло для релаксации, внутренняя загрузка камней до 95 кг при помощи выдвижного отдела для длительного сохранения тепла.
Лабиринт дымохода для увеличения КПД печи и встроенный теплообменник для подогрева воды в баке.
Характеристики:
- Объем – 30 м3.
- Мощность – 15 кВт.
- Вес – 96 кг.
Плюсы:
- Высокая мощность. Обогреет большую площадь сауны.
- Встроенный теплообменник. Для улучшения показателей микроклимата.
Минусы:
- Ограничения. Не подойдет для маленькой бани, только для большой, за счет габаритов.
- Экономный материал. Проигрывает моделям из стали с хромом.
Лучшая печь для бани с теплообменником
Ермак 12 относится к линейке эконом-класса, однако это не указывает на плохое качество. Материал – нержавеющая сталь с содержанием хрома. Он устойчив в коррозии. Печь имеет стандартные размеры для своего класса: 425×520×690 мм. Вес – 52 кг.
Масса закладываемых камней составляет 40 кг. Такой показатель требует более длительного подогрева сырья. Выносной бак и теплообменник идут в комплектации.
Характеристики:
- Мощность – 12 кВт.
- Рабочая площадь – 14 м3.
- Зона для камней – на 40 кг.
- Длина дров – до 450 мм.
Плюсы:
- Богатая комплектация.
- Умеренный микроклимат. Вода в печи горячая, но не закипает.
- Стоимость. Невысокая цена.
Минусы:
- Камни медленно нагреваются.
Лучшая печь для бани из чугуна
Актуальность Гефест ПБ-01 объясняется высокой мощностью. Она способна обогреть большое помещение объемом до 45 м3. Толстые стенки конструкции быстро передают тепло.
Самый высокий КПД (87%) среди банных печей – ключевая особенность. Печь выдерживает большие тепловые нагрузки – до 750 ̊С. Турбулентные ребра дают возможность снизить теплоотдачу в дымоходе до 300˚С.
Характеристики:
- Мощность – 18 кВт.
- Масса камней – 70 кг.
Самодельные печи для бани из металла: чертежи. Чертежи печи для бани из металла
Что самое главное в бане — конечно же печь. Существует множество готовых решений печей, которые можно купить в магазине, но в этой статье мы рассмотрим чертежи для самостоятельного изготовления печей из металла.
Печь для бани из металла своими руками
Этапы изготовления
Чертежей печи для бани достаточно много и каждый из них имеет свою функциональность. Начнем с топки для печи.
- Топка — первое что нужно сделать. Размеры топки вы определяете самостоятельно, исходя из размеров вашей парной.
Главное помнить, что ширина и высота топки должны быть одинаковы. - На некоторых чертежах печей из металла вы можете увидеть готовые решения, которые можно купить в магазине ,а не вырезать и варить самостоятельно. Например, дверцы, решетки, ручки и так далее. Вы сэкономите массу времени, если приобретете их в магазине.
- Почти на всех чертежах топка состоит из 2 частей. В одной части горят дрова, а другая предназначена для сбора золы и также выполняет функцию поддувала.
- Если на верхнюю часть топки будут ложиться камни, то ее следует сделать из решетки. Можно сделать декоративную решетку для красоты.
Важно! Если Вы решили сварить печь для бани самостоятельно — отнеситесь с особым вниманием к толщине металла. Металл должен быть не менее 5 мм, чтобы при нагревании его не повело.
Подробный чертеж печи для бани из металла
Бак для воды и место для камней
- Сразу над топкой делается емкость для засыпки камней.
- На некоторых чертежах емкость является открытой и вода поливается на камни сверху.
- На других чертежах печей можно встретить емкость для камней с дверцей, которую необходимо открывать для полива воды на камни. Так камни быстрее прогреваются в закрытой емкости и дольше сохраняют тепло.
- В каменке используются специальные камни для бани. Можно конечно использовать обычные речные, но эффект будет не тот.
- Над каменкой устанавливается бак с водой. Через него также должна проходить труба, которая будет подогревать воду.
- В бак с водой можно вмонтировать кран для набора горячей воды.
Также не забудьте про то, что через каменку должен проходить дымоход.
Печь с открытой каменкой
Чертеж печи из металла с каменкой и баком для воды
Трубу также необходимо изготавливать из трубы с большой толщиной металла.
Печь для бани с трубой, проходящей через каменку и водяной бак
Дымоход
Также на чертеже печи для бани необходимо указать место, где дымоход будет проходить через крышу. Это место необходимо тщательно изолировать, так как воздух, проходящий через трубу очень горячий.
Дымоход для бани
Для изоляции дымохода от крыши лучше приобрести готовые решения, которые продаются в специализированных магазинах для бани.
Таким образом сделать печь для бани по чертежам самому не так уж и сложно. К тому же в магазинах продается много готовых решений (решетки, дверцы, баки, трубы, дымоходы, изоляция дымохода), применяя которые соорудить печь будет еще проще.
Виды печей для бани. Виды кирпичных печей для бани
Интересная тема, обширная. Конструкций, образующих разные виды кирпичных печей для бани полно. Одни попроще, другие посложнее. В одних предусмотрены регистры для нагрева воды , в других – место для бака . Есть колпаковые печи и канальные , есть более привычные типы каменок – глухие и проточные . Помимо этого есть разные системы дымооборотов канальных печей – вертикальные и горизонтальные.
Итак, понятно, что регистры и баки – это дополнительные приспособления, а нам для начала надо уяснить необходимые элементы. К ним относятся:
- поддувало;
- колосник;
- топка;
- каменка;
- дымооборот.
Первое крупное разделение можно провести по каменкам . В одних печах камни отделены от огня только решеткой , которая никак не препятствует их контакту, в других для камней оборудован герметичный ящик , дно которого разделяет камни и пламя, являясь посредником в передаче тепла.
Первая каменка называется « проточной ». Это наследница печей «по-черному». Сегодня они называются «печами периодического действия». В самом деле – как в такую каменку лить воду и не залить огонь? Невозможно. Поэтому надо ждать, пока дрова совсем прогорят. Вот тогда и можно открывать дверцу и поддавать воду для получения пара.
Плюс проточной каменки в том, что камни нагреваются быстрее и до более высокой температуры. Минус – это плохо сказывается на их сроке жизни в каменке.
Закрытая или глухая каменка позволяет лить воду прямо во время топки печи , что делает такие агрегаты популярными. Потому что это независимые процессы. За такое удобство приходится платить тем, что камни нагреваются медленнее, не такие горячие, как в проточной, но все же их температуры достаточно для получения хорошего пара.
Другой способ деления печей такой: они бывают канальные и колпаковые. Из последних широкую известность обрела печь Кузнецова . Различие между ними в том, что именно является «двигателем» продуктов сгорания внутри печи: канальная печь работает исключительно на тяге . А в колпаковой продукты сгорания движутся свободно, но при этом новоприбывающие теснят предшественников по ходам, предготовленным для них инженером.
На заметку! Разновидностей как канальных, так и колпаковых печей очень много. Окончательный выбор подходящего для вашего случая варианта обычно зависит от печника, а точнее, от того, как много разных печей он сложил за свою жизнь.
Смысл разных конструкций в том, чтобы увеличить теплоотдачу печных газов. Чем больше отдадут, тем выше КПД печки. У Кузнецова КПД 94% – просто отличный показатель. Это достигается за счет встраивания нескольких колпаков.
Кстати! Второй колпак часто используется для встраивания дополнительных приспособлений – теплообменника или бака для нагрева воды , печам данных видов посвящены отдельные статьи.
Вернемся к канальным печам. Совокупность каналов представляет собой дымооборот. Классифицировать кирпичные банные печи можно и по тому, как расположены каналы:
- вертикально;
- горизонтально.
Специфика каждого из этих вариантов в полной мере понимается тогда, когда приходит время чистки.
Совет! Поэтому и тут (хотя бы поначалу) стоит воспользоваться услугами профессионала.
Немного о баках . Кирпичные печи для бани на дровах с баком для воды могут располагать его как вверху, так и внизу печной конструкции. Достаточно распространен вариант, когда бак находится позади топки, то есть вода нагревается максимально быстро. Но надо принимать во внимание, что .
Да и еще. Вариативно расположение топки, однако у нее не будет выносного топливного канала – сама печка расположится так, что ее стенка с топкой будет находиться в предбаннике, например. При этом убиваются сразу два зайца: обогрев идет на соседние с парилкой помещения, в самой парилке чистота и порядок.
По поводу разновидностей печей есть один любопытный момент. Не вникая в детали, люди часто формулируют свои желания следующим образом: «хочу самую простую печь для бани из кирпича» или «мне нужна маленькая печка для бани из кирпича». Что ж, почему бы и нет, давайте и их рассмотрим как возможные разновидности.
Видео металлическая печь для бани своими руками.
Самодельные металлические печи для бани и сауны и их чертежи
Хорошая печка является главным атрибутом русской бани или сауны. На сегодняшний день существует множество видов печек для бани. Все они делятся на два больших вида: из кирпичной кладки и металлические.
Кирпичная печка является более красивой и удобной, однако на ее строительство нужно достаточно много недешевого материала. Плюс ко всему, кладка — не такой уж и легкий процесс, поэтому приходится звать на помощь опытных специалистов, что обуславливает дополнительные затраты. А вот железные печи для бани вполне под силу каждому. Сделать ее не так уж и сложно, да и дорогой материал для этого совершенно не нужен.
Сейчас есть несколько разных вариантов того, как сделать печь для бани из металла или же на основе уже готовой печи.
Поэтому целесообразно рассмотреть более подробно, что собой представляют такие самодельные железные печи, а также вникнуть в их чертежи и описание.
Содержание
- Вертикальные и горизонтальные каменки
- Печь для бани из листового металла
- Каменка, совмещенная с варочной печью
- Печи для бани с разным расположением водяного бака
- Каменка с двойными стенками
Вертикальные и горизонтальные каменки
Рисунок 1.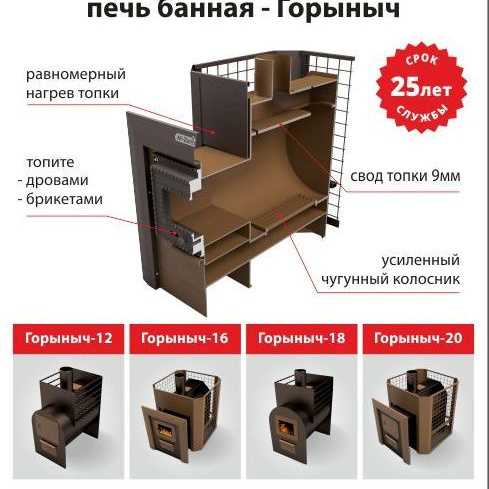
Первая группа металлических печек для бани — на основе трубы. Топливом здесь являются исключительно дрова, при этом не нужно никакой дополнительной энергии для работы данного устройства.
Есть два вида печей из этой группы: вертикальные и горизонтальные. Все зависит лишь от расположения трубы-основы относительно пола, где она устанавливается. Что касается вертикальных металлических устройств, то они изготавливаются из прочной железной трубы большого диаметра (не менее 50 см).
Толщина стенок трубы должна быть как минимум 5 мм. Эти печи удобны тем, что не занимают слишком много горизонтального пространства в помещении. При этом все отделения (емкость для воды, каменка, топка и зольник) располагаются по вертикали друг над другом. Дымоходная труба такой печи выходит на крышу. А за счет величины печи по вертикали труба для дымохода не требуется слишком высокая. Данная печка выглядит примерно так, как на схеме (Рисунок 1).
Горизонтальные самодельные металлические печи для бани могут быть изготовлены как из трубы, так и из железной бочки. Их особенность состоит в том, что они располагаются по горизонтали параллельно поверхности пола. Они занимают немного больше места, чем вертикальные, но чаще всего такого вида печь может держать температуру в бане несколько дольше. Схема устройства простейшей печи представленного типа показана на Рисунке 2.
Удобство ее состоит в том, что ее основные элементы могут располагаться в разных местах, где вам будет удобнее. При этом до каждого элемента довольно легко добраться. Единственное, дымоход, как правило, в этом случае нужен длинный, чтобы провести его на крышу. Но в данном варианте можно еще вывести дымоход через стену по горизонтали.
Но при этом следует помнить о том, что максимально допустимая длина горизонтального колена трубы от бочки до выхода не должна превышать 25 см. В противном же случае дым будет выходить слабо.
Вернуться к оглавлению
Печь для бани из листового металла
Рисунок 2. Горизонтальная самодельная металлическая печь.Но помимо представленных простейших двух видов печек существуют еще и металлические печи для бани и сауны, которые сделаны не из бочек и труб, а из металлических отходов или же просто кусков прочного металла с толстыми стенками, сваренными между собой.
Делать их немного дольше за счет дополнительно вводимого процесса сварки отдельных деталей, но по себестоимости в большинстве случаев обходятся они несколько дешевле.
Итак, различают четыре основных вида печек для бани данного типа. Это каменка с боковым баком для жидкости, каменка с двойными стенами, каменка с фронтальным размещением водяного бака, а также совмещенная с кухонной варочной печью каменка. Каждая из печей хороша по-своему, поэтому рассмотрим кратко устройство каждой.
Вернуться к оглавлению
Каменка, совмещенная с варочной печью
Рисунок 3. Чертеж печи каменки, совмещенной с кухней: 1 – кухонная печь; 2 – топочная дверка кухонной печи; трубы с каменной засыпкой; 4 – печь-каменка; 5 – дверка топливника каменки.Каменка, которая одновременно совмещается с кухонной печкой, очень удобна. Ведь при нахождении в бане вы сможете сразу же приготовить себе поесть или нагреть чай. Устройство печи состоит в том, что топочная часть кухонной стороны совмещается с зольником каменки, поэтому можно как одновременно париться и готовить пищу, так и производить все по отдельности и даже в разное время. Схему устройства печи наглядно представляет чертеж (Рисунок 3).
Интересно то, что сделать такого плана совмещенную каменку можно на основе уже существующей варочной железной печи, дополнительно приварив к ней некоторые элементы, которые характерны для банной установки, и совместив отделения. Наиболее целесообразно устройство такого типа конструкции в тех саунах и банях, где есть рядом дополнительная комнатка для отдыха. Приготовив пищу, можно перевести дыхание в этой комнате, в то время как другие могут париться в банной части постройки.
Вернуться к оглавлению
Печи для бани с разным расположением водяного бака
Рисунок 4. Каменка с одинарными стенками и фронтальным расположением бака для воды.Каменки с боковым или фронтальным расположением бака являются на сегодняшний день довольно популярными. Ведь вы имеете уникальную возможность расположить устройство для воды там, где вам это удобно.
Отличительной особенностью данной печи являются и ее одинарные стенки. За счет этого она может быстро остывать. Но эта проблема легко решается, если обложить такую печь сначала листами огнеупорного листового металла, а потом через небольшой зазор осуществить кирпичную кладку из огнеупорного кирпича.
Каменка, в которой бак с водой находится в передней части (Рисунок 4), может быть очень даже удачно расположена прямо посередине банной комнаты. Тогда отделение с водой, а заодно и отделение для камней будут смотреть прямо в центр помещения и давать больше жара.
Каменка с боковым устройством отделения для воды лучше всего будет смотреться около стены другим боком, чтобы рабочая часть смотрела в центр помещения. Топка, зольник и колосник располагаться будут перпендикулярно, что не даст дыму и золе попадать непосредственно в рабочую часть помещения бани.
Вернуться к оглавлению
Каменка с двойными стенками
Еще один вариант каменки для бани — печь железная с двойными стенками. Понятно, что такая установка не требует обкладки огнеупорным кирпичом, так как она достаточно хорошо сохраняет тепло и сама по себе. Железные печи для бани такого типа хороши в любом случае.
https://1popechi.ru/youtu.be/f2kPfaiW3A4
Выполняется данная металлическая печь для бани из того же листового металла путем крепкого сваривания листов друг с другом. Печь может служить одновременно как в качестве чисто банной установки, так и для обогрева помещения. Единственное, что можно в ней доработать, — установить вокруг печи стеночки из огнеупорного металла, чтобы избежать ожогов при случайном соприкосновении с печкой. Какую печь выбрать — определяться только вам самим!
Заявка на патент США для печи для расплавленного металла. Заявка на патент (заявка № 20130249149, выданная 26 сентября 2013 г.)
ПЕРЕКРЕСТНАЯ ССЫЛКА НА РОДСТВЕННЫЕ ЗАЯВКИ № 61/506,121.
ОБЛАСТЬ ИЗОБРЕТЕНИЯ
Настоящее изобретение относится к нагревательным и/или плавильным печам с прямым пламенем, таким как алюминиевые печи, и к снижению подводимой тепловой энергии для эффективного плавления нагретого продукта при одновременном обеспечении инертной атмосферы внутри печи. печь, которая сводит к минимуму или предотвращает возникновение нежелательных реакций с нагретым продуктом.
ПРЕДПОСЫЛКИ СОЗДАНИЯ ИЗОБРЕТЕНИЯ
Типичная установка для производства расплавленного металла включает печь с одним или несколькими насосами для перемещения расплавленного металла. Во время обработки расплавленных металлов, таких как алюминий, расплавленный металл обычно непрерывно циркулирует через печь с помощью центробежного крыльчатого насоса, т. е. циркуляционного насоса, для выравнивания температуры ванны расплава. Типичная печь включает в себя насосный колодец, расположенный между нагревательной камерой или подом и загрузочным колодцем (где сырье загружается в печь). Эти три основные секции типичной печи сообщаются по текучей среде с циркуляционным насосом, в результате чего расплавленный металл циркулирует из насосного колодца в загрузочный колодец, в горну и обратно в насосный колодец.
В обычных нагревательных или плавильных печах с прямым (топливным) нагревом газовые горелки создают пламя и/или продукты сгорания непосредственно над расплавом или загрузкой. Тепло передается непосредственно от пламени и/или продуктов сгорания к расплаву за счет комбинации излучения и конвекции.
Проблема этого метода плавки в том, что он очень неэффективен. Чтобы предотвратить контакт отработанных газов/топлива горелок с расплавом, горелки обычно устанавливаются внутри печи на высоте не менее четырех футов над верхней поверхностью расплавленного металла (металлопровод). Из-за этого расстояния и несмотря на то, что алюминий плавится при температуре чуть выше 1200°F, обычные печи работают при температуре приблизительно 2100°F, чтобы обеспечить достаточную тепловую нагрузку на металл для его полного расплавления (т. е. на пол печи). . При этом методе нагрева большое количество тепла/энергии теряется, поскольку они истощаются вверх по дымовой трубе.
Кроме того, в этих алюминиевых плавильных печах кислород, водород и двуокись углерода в окружающем воздухе вступают в реакцию с алюминием с образованием оксида алюминия или окалины. Образование окалины (т. е. окисление алюминия) нежелательно, поскольку снижает выход алюминия. В зависимости от типа расплавляемого шихтового материала может окисляться примерно от 5 до 10 % загружаемого алюминия. Это увеличивает эксплуатационные расходы из-за потерь невосстановленного алюминия, затрат труда и времени на удаление шлака из печи, а также потерь энергии при нагреве шлака в печи. То есть оксид алюминия имеет характерно низкую теплопроводность и, следовательно, сильно препятствует передаче тепла к расплавленному алюминию, поскольку слой шлака действует как изолятор на поверхности расплава, тем самым снижая эффективность передачи тепла от горелки к алюминию.
По вышеуказанным причинам обычные печи работают с КПД 20-30%, поскольку теплопередача к расплаву в первом контуре печи происходит за счет излучения верхних газовых горелок к расплаву через значительный зазор и изолирующего эффекта, обеспечиваемого образующимся окалиной. над расплавленным металлом.
Таким образом, существует потребность в печи, которая снижает тепловую энергию, необходимую для эффективного плавления нагретого продукта, и значительно снижает образование шлака в расплавленном металле.
СУЩНОСТЬ ИЗОБРЕТЕНИЯ
Вышеупомянутые и другие недостатки печей предшествующего уровня техники преодолеваются настоящим изобретением усовершенствованной печи типа, имеющей буферную плиту, которая полностью отделяет горелки печи от ванны с расплавленным металлом. Усовершенствование изобретения включает буферную пластину, изготовленную из жаропрочного сплава на основе никеля, которую устанавливают в печи с расплавленным металлом над линией металла и под горелками печи.
Азот представляет собой инертный газ, который, как правило, практически не реагирует или не реагирует с загружаемым материалом, таким как алюминий, по сравнению с кислородом и другими дымовыми газами, присутствующими в печи.
В настоящем документе описаны системы и соответствующие способы, которые обеспечивают камеру горелки печи, которая отделена от металлического изделия или загрузки буферной пластиной из суперсплава, которая получает тепловую энергию от горелок и передает эту энергию с небольшими тепловыми потерями металлическому изделию или нагрузка.
В настоящем документе описаны системы и соответствующие способы, которые обеспечивают герметичную камеру для расплавленного металла, заполненную эффективным количеством инертного газа, над поверхностью металлического изделия или загрузки в нагревательной и/или плавильной печи.
В настоящем документе описаны системы и соответствующие способы, которые обеспечивают печь, имеющую буферную пластину из суперсплава, которая предпочтительно устанавливается менее чем на один фут ниже горелки (горелок) печи и находится на расстоянии менее восьми дюймов от металлического изделия или загрузки. Буферная плита, уплотняющая горелки, из металлического изделия. В алюминиевой печи меньший зазор между горелкой и загрузкой позволяет снизить температуру горелки до 1640°F по сравнению с 2100°F в обычной печи.
Как описано в данном документе, система включает печь, сконфигурированную для приема продукта, подлежащего термической обработке, в печи, где печь включает по меньшей мере одну горелку, которая обеспечивает нагрев продукта, находящегося в печи. Печь включает в себя увеличенную буферную пластину или лист из суперсплава на основе никеля, который герметизирует и отделяет горелки печи от нагреваемого продукта. Содержание никеля в суперсплаве достаточно для образования слоя черного оксида никеля, в результате чего суперсплав имеет коэффициент теплового излучения приблизительно 0,9.6 до 0,98.
Как далее описано в данном документе, буферная пластина герметизирует камеру продукта и позволяет подавать инертный газ в печь под буферной пластиной, чтобы защитить поверхность продукта и свести к минимуму или предотвратить химическую реакцию продукта с любыми другими газов внутри печи. Кроме того, инертный газ будет пропитывать любую пористость огнеупорного материала стенок печи, существенно уменьшая эрозию огнеупорного материала и образование других нежелательных побочных продуктов, таких как шпинель.
Преимуществом настоящего изобретения является создание усовершенствованной печи для расплавленного металла, включающей: резервуар для расплавленного металла, приспособленный для удержания ванны с расплавленным металлом; нагреватель вблизи резервуара, при этом нагреватель окружен атмосферой, содержащей воздух и выхлопные газы нагревателя; и буферную пластину, расположенную между ванной с расплавленным металлом и по меньшей мере одним нагревателем, при этом буферная пластина герметизирует и отделяет ванну с расплавленным металлом от атмосферы нагревателя.
Еще одним преимуществом настоящего изобретения является создание наклонных проходов печи, которые перенаправляют более горячий расплавленный металл, поступающий из верхних областей пода, вниз к насосу, и перенаправляют относительно более холодный расплавленный металл из загрузочного колодца к более горячему расплавленному металлу. внутри очага.
Еще одним преимуществом настоящего изобретения является футеровка наклонных проходов печи прочной керамической футеровкой для предотвращения эрозии огнеупорных стенок печи, содержащих эти проходы.
Здесь также предусмотрен способ защиты продукта, нагреваемого в печи. Способ включает подачу источника кислорода и источника топлива на основе углерода по меньшей мере к одной горелке печи для генерирования дымовых газов, обеспечение буферной плиты между по меньшей мере одной горелкой и нагреваемым продуктом для образования верхней камеры горелки и нижняя продуктовая камера, доставляющая дымовые газы в печи к буферной пластине, тем самым передавая тепловую энергию буферной пластине, доставляя тепловую энергию внутри буферной пластины к продукту и подавая инертный газ в продуктовую камеру для предотвращения продукта. от химической реакции с другими газами внутри печи.
Вышеупомянутые и дополнительные цели, особенности и преимущества систем и способов, описанных в настоящем документе, станут очевидными при рассмотрении следующего подробного описания конкретных вариантов их осуществления, особенно если рассматривать их вместе с прилагаемыми чертежами, на которых одинаковые ссылочные позиции обозначают одинаковые компоненты. Эти и другие цели, признаки и преимущества настоящего изобретения станут очевидными из следующего описания при рассмотрении в соответствии с прилагаемыми чертежами.
КРАТКОЕ ОПИСАНИЕ ЧЕРТЕЖЕЙРИС. 1 представляет собой схематический вид сверху известной печи для расплавленного металла;
РИС. 2 представляет собой схематический вид сбоку печи предшествующего уровня техники, показанной на фиг. 1;
РИС. 3 представляет собой схематический вид сбоку одного варианта осуществления настоящего изобретения;
РИС. 4 представляет собой увеличенный вид сбоку в разрезе интерфейса между буферной плитой и стенками печи варианта осуществления, показанного на фиг. 3;
РИС. 5 представляет собой вид сверху части резервуара по настоящему изобретению;
РИС. 6 представляет собой вид сбоку в разрезе по линии 6 — 6 на фиг. 5;
РИС. 7 представляет собой вид сбоку в разрезе по линии 7 — 7 на фиг. 5;
РИС. 8 представляет собой схематический вид сбоку другого варианта осуществления настоящего изобретения в открытом положении или положении для чистки;
РИС. 9 представляет собой схематический вид сбоку варианта осуществления, показанного на фиг. 8, показывающая печь, закрытую буферной плитой; и
РИС. 10 представляет собой частичный схематический вид сбоку варианта осуществления, показанного на ФИГ. 8 и 9показано механическое соединение буферной плиты с печью.
ПОДРОБНОЕ ОПИСАНИЕ ИЗОБРЕТЕНИЯ
Обращаясь теперь к фиг., в известных печах, таких как показанная на фиг. 1 и 2 показана печь 10 , которая обычно имеет форму кожуха, удерживающего текучую среду. Это ограждение включает в себя зону нагрева или топку 12 , насосный колодец 14 , в котором находится насос для расплавленного металла 16 , и загрузочный колодец 9.0003 18 . Ванна 20 расплавленного металла находится внутри печи. Ряд арок 21 a , 21 b и 21 c по текучей среде соединяют под, насосную и загрузочную скважины, позволяя расплавленному металлу течь через печь.
При нормальной работе ванна 20 нагревается в очаге с помощью ряда горелок 22 , работающих от источника кислорода и углеродсодержащего топлива. Баня 20 втягивается в насосный колодец насосом 16 и ускоряется из насоса в загрузочный колодец 18 для циркуляции расплавленного алюминия 20 через печь. Как показано, расстояние 23 от горелок 22 до расплава 20 обычно составляет от трех до четырех футов из-за присутствия кислорода, который образует шлак, и поскольку температура поверхности алюминия должна оставаться ниже 1400°F.
Дополнительно горелки 22 должен работать при температуре примерно от 2100° до 2200°F из-за низкого коэффициента излучения расплавленного алюминия (от 0,09 до 0,18). Выхлопные газы и выход тепла через крышную дымовую трубу или дымовую трубу 25 .
Из-за вышеуказанных ограничений, а также из-за большого градиента температуры расплавленного алюминия глубина ванны 20 обычно составляет менее тридцати дюймов. Эта относительно неглубокая ванна 20 требует, чтобы насос 16 быть большими и работать на низких скоростях из-за отсутствия положительного напора на всасывании. Полученный в результате низкоскоростной поток из насоса требует более длительного времени рециркуляции и более длительного и менее эффективного времени впрыска газа (например, впрыск газообразного хлора).
Насос 16 обычно представляет собой насос с центробежным рабочим колесом, предназначенный для погружения в расплавленный металл. Насос 16 вращает крыльчатку для всасывания и выталкивания формовочной ванны расплавленного металла 20 . Следует понимать, что пока насос 16 описывается как насос с центробежным рабочим колесом, это может быть практически насос любого типа, подходящий для использования в среде с расплавленным металлом.
Обращаясь теперь более конкретно к ФИГ. 3 и 4 показана усовершенствованная печь 50 для плавки расплавленного металла. Печь 50 выполнена со стенками из огнеупорного материала 52 . Подобно печи 10 , описанной выше, печь 50 по настоящему изобретению включает под, насосный колодец 14 , и хорошо зарядить 18 . Печь 50 , однако, включает в себя увеличенную буферную пластину или экран 54 , который разделяет печь на верхнюю камеру сгорания 56 и нижнюю камеру продукта (алюминиевую камеру) 58 , которая содержит ванну 20 из расплавленный металл.
В одном предпочтительном варианте буферная пластина 54 изготовлена из суперсплава на основе никеля, такого как Super 22H®, доступного в Duraloy Technologies, Inc, или из моих предыдущих составов суперсплава, таких как мой суперсплав JAM-003. Важно отметить, что материал из суперсплава должен иметь достаточное содержание никеля (например, не менее 15% Ni) для образования слоя оксида никеля на его внешней поверхности. Этот черный слой оксида никеля обуславливает коэффициент теплового излучения буферной пластины 9.0003 54 приблизительно до 0,96-0,98, что позволяет по существу любой тепловой энергии проходить в пластину и излучать ее с небольшими тепловыми потерями. В других неограничивающих вариантах осуществления пластина 54 может быть практически из любого материала, способного выдерживать температуры до 2000°F, сохраняя при этом подходящий предел текучести, чтобы поддерживать себя, и образует слой оксида никеля (т. 30% никеля).
В одном неограничивающем варианте осуществления буферная пластина 54 имеет толщину примерно один дюйм и может включать дополнительные опоры, такие как соединенные между собой перемычки или фланцы, позволяющие плите 54 охватывать всю длину и ширину печи 50 .
Важно отметить, что благодаря физическому отделению горелок 22 от ванны расплава 20 буферная пластина 54 позволяет переместить горелки гораздо ближе к нагреваемому продукту. Таким образом, тепловая энергия от горелок может передаваться более эффективно (т.е. как конвекцией, так и излучением, а не только излучением, как в предшествующем уровне техники). В предпочтительном варианте горелки 22 можно перемещать примерно на один фут от верхней части пластины 54 . Следует понимать, что потери тепловой энергии обратно пропорциональны квадрату расстояния между горелками и нагреваемым объектом. За счет опускания горелок до фута от плиты вместо трех футов печь 50 примерно в девять раз эффективнее, чем печь предшествующего уровня техники. Расстояние 60 между нагретым изделием 20 и плитой 54 желательно как можно ближе. Например, от четырех до восьми дюймов. Точно так же расстояние 61 между нижней частью пластины 54 и ванной с расплавленным металлом также должно быть как можно меньше, например, от трех до шести дюймов.
Эта эффективность демонстрируется необходимостью запускать горелки 22 только при температуре всего 1640°F для поддержания/плавления расплавленного алюминия на обычной глубине в тридцать дюймов.
Как лучше всего показано на РИС. 4, печь 50 включает наружную окружающую стену 52 с плоским уступом 62 , который проходит вокруг внутренней части печи. Буферная пластина 54 поддерживается вертикально на выступе 62 . Камера продукта 58 предпочтительно отделена от камеры горелки 56 добавлением соответствующего прокладочного материала 64 , такого как Fiberfrax® от Unifrax, LLC, который помещается между плитой 54 и выступом 9.0003 62 . В показанном варианте осуществления прокладочный материал 64 расположен внутри углубленного канала 66 , образованного внутри выступа 62 .
Для дальнейшего ограничения образования нежелательных побочных продуктов в нагретом продукте 20 (например, окалины в алюминиевой ванне) печь 50 дополнительно включает средства для подачи инертного газа 70 в камеру продукта 58 . Этот инертный газ впрыскивается в камеру продукта 9.0003 58 через трубопровод 72 и сконфигурирован таким образом, что газ 70 может быть введен для создания локальной атмосферы или слоя инертного газа на поверхности расплавленного металла 20 . Состав газа 70 в основном состоит из азота (например, предпочтительно по существу или почти 100% по объему) в продуктовой камере 58 . Герметичный инертизирующий слой азота защищает нагретую поверхность изделия от остатков печной атмосферы и дымовых газов.
Кроме того, инертный газ 70 также проникает и пропитывает пористость огнеупорного материала 52 стенки печи внутри продуктовой камеры 58 . Эти стены, пропитанные азотом, уменьшают проникновение расплавленного алюминия в огнеупорный материал, значительно снижая эрозию огнеупора и увеличивая срок службы стен печи/огнеупора.
Кроме того, как показано на РИС. 3, общая высота камеры сгорания 56 могут быть значительно уменьшены (до 2-4 футов) по сравнению с обычными высокотемпературными печами 10 , а более низкие температуры (1640°F против 2100°F) увеличивают срок службы огнеупора внутри горелки. камера 56 почти на 100%.
Наконец, еще одним существенным недостатком печей предшествующего уровня техники является то, что при их рабочих температурах образуются токсичные газы NOx. Настоящее изобретение, однако, работает при температуре 1880°F и существенно предотвращает образование NOx, тем самым снижая затраты и значительно повышая безопасность.
Обратимся теперь к ФИГ. 5-7, еще одно усовершенствование, обеспечиваемое настоящей печью, заключается в конфигурации каналов (обозначенных 21 a — c на фиг. 1 и 2), соединяющих под 12 , насосную скважину 14 и хорошо зарядить 18 . Однако, в отличие от проходов предшествующего уровня техники, не все проходы согласно настоящему изобретению представляют собой по существу горизонтальные отверстия, образованные на полу , 24, печи или рядом с ним.
Как лучше всего показано на РИС. 6, проход 72 , образованный в огнеупорной стене печи, который отделяет под 12 от насосного колодца 14 , наклонен вниз от пода к насосному колодцу. Преимущество этого наклонного прохода 72 состоит в том, чтобы втягивать расплавленный металл, находящийся в верхней части пода (т. е. самый горячий металл в поде), в насосную скважину 14 . Эта новая конфигурация прохода пода/насосного колодца 72 является значительным улучшением по сравнению с печами предшествующего уровня техники, которые втягивают расплавленный металл, ближайший к полу 24 печи (т. е. самый холодный металл в поде), в насосный колодец. Более высокая температура расплавленного металла, поступающего в насосный колодец в настоящем изобретении, улучшает плавление твердого металла, вставленного ниже по потоку от насосного колодца 14 (например, материала, отложившегося в загрузочном колодце 18 ).
Проход 74 Соединяет зарядный колодец 18 и под 12 . Как и проход 72 , этот проход загрузки/пода 74 отличается от проходов предшествующего уровня техники тем, что он также расположен под углом. Однако проход 74 расположен под углом вверх от отверстия, образованного на дне загрузочного колодца или рядом с ним. В предпочтительном варианте этот угол 75 составляет от трех до пятнадцати градусов и основан на соотношении размеров между шириной 76 печи и номинальной рабочей глубиной 9.0003 77 печи. Наклонный вверх канал 74 направляет относительно холодный расплавленный металл, вытекающий из загрузочного колодца 18 , к нагретой горелкой буферной пластине 54 , тем самым погружая более холодный металл в самую горячую область расплавленной ванны внутри пода 12 .
В одном предпочтительном неограничивающем варианте осуществления прочный износостойкий вкладыш 78 вставлен в проходы 72 и 74 . Лайнеры 78 предпочтительно формировать из соответствующей керамики, чтобы исключить любую возможную эрозию, которая в противном случае могла бы произойти с огнеупорной стенкой из-за изменения направления расплавленного металла, когда он циркулирует в печи.
Обратимся теперь к ФИГ. 8-10 показан альтернативный предпочтительный вариант осуществления настоящего изобретения с отдельной верхней камерой 56 горелки, подвижной относительно неподвижной нижней камеры 58 продукта. В частности, верхняя камера 9 горелки0003 56 может перемещаться из а) рабочего положения (показанного на ФИГ. 9 и 10), в котором камера 56 горелки расположена над верхними стенками нижней камеры 58 , в b) положения очистки (показанного на ФИГ. 8) где камера горелки 56 удалена от нижней камеры 58 и имеется доступ к внутреннему резервуару для расплавленного металла.
В этом варианте осуществления вертикальные огнеупорные стенки 52 камеры горелки 56 заканчиваются плоской нижней поверхностью 80 . Отделение и уплотнение камеры 56 горелки, кроме нижней камеры 58 , представляет собой буферную пластину 154 , которая, за исключением следующего, идентична по конструкции пластине 54 , описанной выше. В отличие от пластины 54 буферная пластина 154 этого варианта осуществления не является по существу плоской по всей своей длине, вместо этого два противоположных конца 156 этой пластины образуют каналы 158 , в которые входят нижние части вертикальных стенок 9.0003 52 с вложенной в него нижней поверхностью 80 .
В конфигурации, показанной на РИС. 8-10, буферная пластина 154 включает по существу плоскую часть 160 , охватывающую печь, и внутреннюю стенку канала 162 , отходящую вертикально вниз от каждого конца 156 . Обычно горизонтальная часть седла 164 проходит от стенки внутреннего канала 162 и охватывает толщину поверхности стенки 80 . Внешняя стенка канала 166 выступает вверх от гнезда 164 , образуя канал 158 . Различные материалы огнеупорных стенок 52 и буферной пластины 154 требуют наличия некоторого дополнительного пространства или зазоров для обеспечения различного теплового расширения и сжатия различных материалов, образующих камеру 56 . Настоящее изобретение дополнительно предусматривает это расширение за счет использования только одной механической застежки (например, болта 9). 0003 170 ) крепления буферной пластины 154 к наружным стенкам камеры 56 . Как лучше всего показано на фиг. 10, каждая наружная стенка 166 канала включает расположенную в центре (в центре масс) вертикальную прорезь 167 , которая совмещена с резьбовым отверстием (не показано), выполненным в стенке печи. Механическое крепление 170 соединяет пластину 154 с нижним концом камеры 56 горелки, при этом допуская термическое расширение металлической пластины.
Для обеспечения удовлетворительного уплотнения верхняя поверхность 82 огнеупорных стенок нижней камеры горелки включает прокладку или уплотнение 84 , изготовленное из соответствующего материала, такого как материал 64 , описанный выше. В рабочем положении камера горелки 56 и буферная пластина 154 опираются на верхнюю поверхность 82 нижней камеры 58 , изолируя печь от окружающей атмосферы. Аналогично другая прокладка 86 расположен между поверхностью 80 и верхней поверхностью пластины 154 .
В проиллюстрированном варианте осуществления верхняя камера 56 горелки может перемещаться отдельно от нижней камеры 58 с помощью шарнирного соединения 88 , которое позволяет верхней камере поворачиваться вверх от нижней камеры 58 . В других неограничивающих вариантах шарнирное соединение может быть заменено краном или цепным механизмом, который физически поднимает верхнюю камеру 9.0003 56 подальше от нижней камеры 58 .
Настоящее изобретение не должно ограничиваться вариантом осуществления, показанным на чертежах и описанным в описании, которое дано в качестве примера, а не ограничения.
Из вышеприведенного описания специалист в данной области легко поймет, что настоящее изобретение направлено на усовершенствованную печь, которая герметично отделяет горелки печи от нагреваемого продукта с помощью увеличенной буферной пластины из суперсплава. Буферная пластина позволяет перемещать горелки намного ближе к нагреваемому продукту, чем это было возможно ранее, и позволяет формировать камеру, содержащую нагретый продукт, которая может быть заполнена инертным газом, чтобы уменьшить образование нежелательных побочных продуктов внутри. расплав. Хотя настоящее изобретение было описано с конкретной ссылкой на различные предпочтительные варианты осуществления, специалисту в данной области техники будет понятно из предшествующего обсуждения и сопровождающих чертежей, что в настоящее изобретение могут быть внесены изменения, модификации и вариации, не отступая от его сущности и объема. .
Металлы | Бесплатный полнотекстовый | Интеграция печи с открытой шлаковой ванной с реакторами прямого восстановления для сталеплавильного производства нового поколения
Основными технологическими операциями процесса являются DR-шахта, установка риформинга, головной скруббер газа, компрессоры продуктового газа и теплообменники. Установка риформинга позволяет обрабатывать природный газ, давая энергию, необходимую для производства синтез-газа. Верхний скруббер позволяет уменьшить водяной пар внутри реактора, чтобы контролировать температуру во время восстановительных операций. На самом деле температуру и давление внутри реактора можно легко контролировать. Впрыск ПГ может осуществляться на различных стадиях процесса: ПГ в качестве ввода в газ риформинга, в качестве энерговклада для нагрева установки риформинга или нагревателя восстановительного газа, а также непосредственно в дымовой газ перед входом в шахтную печь. В этой конфигурации водород впрыскивается в природный газ перед обработкой в установке риформинга. Когда вместо природного газа используется водород, установка риформинга заменяется нагревателем газа, представляющим собой комбинацию модели газовой горелки, смесителя и теплообменника (это основное решение, разработанное для установок Midrex). Энергия, подводимая к нагревателю, также может быть обеспечена ПГ. Обе смоделированные конфигурации основаны на одних и тех же предположениях, чтобы получить сопоставимые результаты; это те же составы и количества твердого исходного материала, а также те же основные предположения для шахты DR (например, степень восстановления, характер науглероживания, распределение температуры и т.
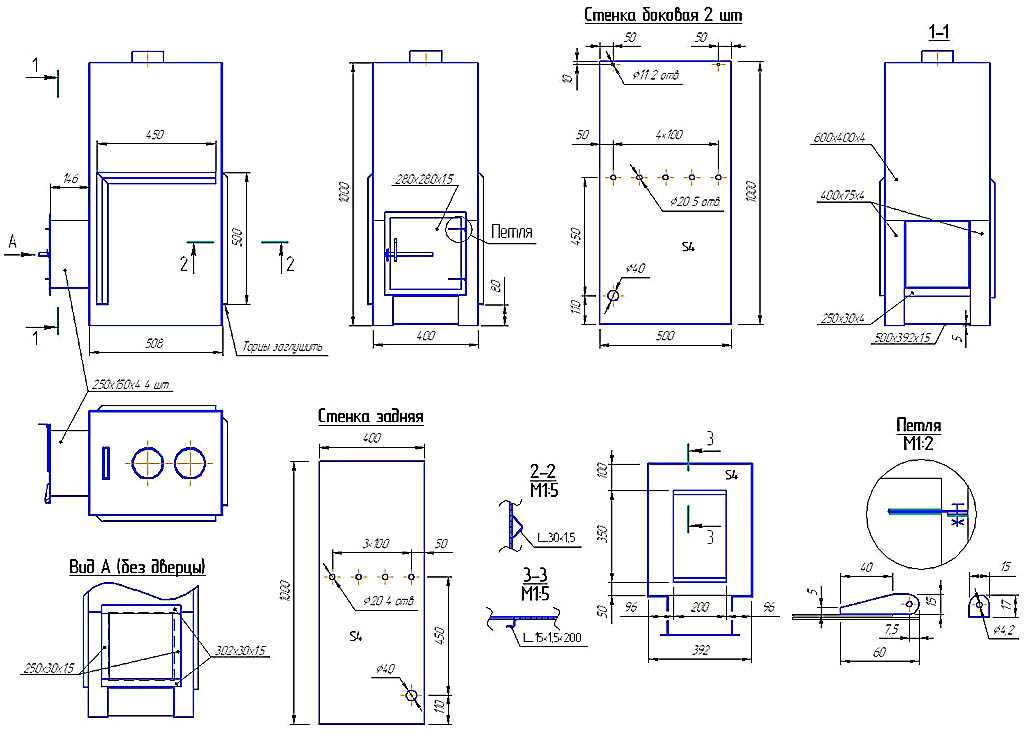
Природный газ, который используется во время операций риформинга, обогащения для науглероживания железом или нагревания газа, представляет собой основной источник углерода в технологии прямого восстановления на основе природного газа. В этой конфигурации основной выход углерода измеряется в отходящем газе установки риформинга. Около 124 кг C/т DRI, что эквивалентно примерно 453 кг CO 2 /tDRI, выдается в этом разделе. Для сравнения, выход углерода в процессе DR-H 2 почти поровну распределяется между выбросами прямого восстановления и дымовыми выбросами (высвобождаемыми при использовании колошникового газа в качестве дымового газа для нагревателя), что составляет 17 и 11 кг C/tDRI соответственно. . Основным источником углерода в этом случае также является ПГ, необходимый для поддержания содержания углерода в ПВЖ (Rechberger et al., 2020).
Как уже упоминалось, установка TENOVA может работать с различными концентрациями водорода в питающем газе. Данные установки в зависимости от состава подаваемого газа приведены в таблице 2.
При увеличении содержания водорода в газовой смеси общая энергия, необходимая для процесса, уменьшается. Так, фиксируются высокие показатели экономии электроэнергии.
Использование продуктов этого реактора прямого восстановления в качестве исходного сырья в доменной печи или электродуговой печи позволяет добиться значительного сокращения выбросов двуокиси углерода. Результаты по сравнению с традиционным маршрутом BF-BOF представлены на рис. 8.
Данные HDRI (Hydrogen DRI) относятся к газовой смеси с 70% H 2 и 30% НГ. Все данные учитывают прямые и косвенные выбросы с допущением 0,5 кг CO 2 /кВтч. Маршрут HDRI-EAF имеет уровень выбросов углекислого газа 25% по сравнению с традиционным маршрутом BF-BOF. Производство водородного чугуна считается будущим в этой очень широкой области [12].
Говоря о переводе производства стали с традиционного метода доменного и конвертерного производства на метод, основанный на технологии прямого восстановления, важно сосредоточиться на использовании сырья, его доступности и эффективности. Во-первых, при использовании электродуговых печей самым экологичным способом является переработка стали. Независимо от этого, многие недавние отчеты показывают, что концентрация посторонних элементов в ломе увеличивается и несовместима со многими высококачественными марками стали, поэтому необходимо разбавление первичным железом (ГБЖ, ПВЖ, чугун, чугун в чушках). Пример приведен в таблице 3 с особым вниманием к концентрации меди.
Все данные относятся к электродуговой печи нового поколения со следующими характеристиками: тип, полноплатформенная печь переменного тока с ЭЛТ и диаметром кожуха 8900 мм; размер крана, 240 т; годовая производительность 2,2 млн т; мощность трансформатора 240 МВА; система впрыска, 17 000 Нм
Недавние исследования показывают, что прогноз доступности окатышей DR-класса очень плоский. Идеальный химический состав для окатышей марки DR: Fe > 67%, SiO 2 + Al 2 O 3 + TiO 2 < 3 % и p < 0,03 %. Расчетный спрос на морские окатыши сорта DR и их экспорт показаны на Рисунке 9 [13].
Таким образом, доступность окатышей марки DR ограничена по сравнению с мировым производством стали. Итак, основные препятствия для прямого преобразования производства стали в основном представлены наличием сырья, соответствующего марковым требованиям. Фактически, успешная и производительная работа линии DR-EAF требует использования высококачественных окатышей (пустая порода менее 5%, возможно, основная). Кроме того, указаны некоторые ограничения для установки маршрута DR-EAF на интегрированных заводах. С учетом энергосистемы 250–300-тонные ЭДП (соответствующие размеру отвода крупных преобразователей, чтобы соответствовать существующему МНЛЗ) подходят для трансформаторов мощностью 200–260 МВА, что оказывает огромное влияние на энергосистему для генерации мерцания. Интеграция доменной печи и электродуговой печи не так проста; типичные времена цикла BF и EAF не совпадают. ЭДП обычно требует 45–55 минут и еженедельных остановок на техническое обслуживание для ремонта/замены футеровки огнеупоров.
Принимая во внимание все описанные аспекты, хорошим решением представляется интеграция прямого восстановления с большими плавильными печами. Таким образом, количество окатышей марки BF в реакторе DR может быть уменьшено за счет решения проблемы наличия высококачественных окатышей марки DR. Восстановленный материал известен как DRP (гранулы прямого восстановления). Их переработка в крупной OSBF позволяет решить электрические и логистические ограничения использования электродуговых печей. Учитывая, что научно-техническая информация ограничена, далее мы дадим подробное описание этой большой плавильной печи.
Обычно наблюдается, что плавка становится легче и эффективнее, поскольку температура ликвидуса шлака и вязкость низки. Эти два аспекта благоприятствуют разделению материала и его течению за счет снижения энергозатрат на плавку. Процессы в печах с погруженной дугой (SAF) являются саморегулирующимися, и материал нагревается до оптимальных условий для течения. Все восстановительные реакции протекают на образовавшемся слое кокса. Температуры сильно различаются в разных зонах: от 1700 °С на конце электрода до 500 °С в верхней части шихты. Это очень важно, поскольку распределение температуры определяет эффективность процесса. В этом контексте регулирование электрода имеет основополагающее значение как для производительности печи, так и для срока службы электрода.
Другими факторами, влияющими на распределение температуры, являются плотность тока, состав шлака и расстояние между электродом и металлом. Действительно, по мере увеличения основности шлака повышается его температура плавления и, следовательно, повышается температура зоны реакции.
Потребляемую мощность можно контролировать, изменяя положение электрода; это позволяет изменять сопротивление дуги и тем самым контролировать ток дуги. По мере повышения температуры степень восстановления увеличивается, если для образования СО обеспечивается достаточно кокса. Уголь также улучшает проводимость ванны за счет повышения эффективности процесса.
Основное различие между OSBF и SAF заключается в том, что в первом электроды расположены в верхней части печи, поэтому они не погружены в шихту. Эта конфигурация дуги известна как щеточная дуга или открытая дуга. Эта дуга создается путем изменения положения кончика электрода (рис. 10).
Эта технология предлагает несколько ключевых преимуществ. Смесь внутри печи не влияет на электрический ток, поскольку электроды не погружены в воду. По этой причине мелочь также может быть легко расплавлена. Наоборот, в СНФ проницаемость шихты может быть пределом процесса. Учитывая, что создается открытая шлаковая ванна, шлак и металл очень быстро и легко разделяются. Подаваемая смесь влияет на химию процесса (которую можно точно контролировать), а затем и на эффективность процесса. Учитывая, что электроды не погружены в воду, можно зафиксировать ввод мощности; таким образом, свойства шихты не влияют на процесс. Поэтому, как правило, допускается точное и улучшенное управление печью. Кинетика восстановления может легко регулироваться процентным введением DRI.
Независимо от этого, при работе с открытой дугой следует подчеркнуть некоторые ограничения. Открытая площадь бани приводит к большим потерям тепла через крышу. Это приводит к рассеиванию энергии и быстрому износу огнеупоров, который можно уменьшить соответствующим охлаждением.
Материал подается в печь по питающим трубам. Образовавшиеся кормовые штабели потребляются из нижней части печи, а также из днищ штабелей. Сочетание большой подводимой мощности и образования дуги на более тугоплавком шлаке позволяет перегревать чугун (рис. 11).
При повышении температуры реакции в железе обнаруживается более высокое содержание углерода за счет растворения и снижения температуры плавления железа. Это имеет тенденцию к увеличению выхода железа, поскольку промывка желоба и ковша сведена к минимуму. В OSBF также достигается улучшение удаления серы благодаря использованию более высокой основности шлака:
Основной реакцией, протекающей в OSBF, является, очевидно, восстановление оксида железа:
Часть оксида железа обычно остается невосстановленной и переходит в шлак. Кроме того, в зависимости от кислородного потенциала шлака, другими реакциями восстановления с участием соединений дополнительной загрузки являются:
Очевидно, что эффективность восстановления зависит от активности кислорода и температуры печи.
OSBF — это успешный метод производства жидкого чугуна из прямого восстановления, который позволяет модифицировать химический состав шлака, тем самым повышая эксплуатационную гибкость. Большая площадь поверхности ванны OSBF приводит к меньшему подъему шлака, что снижает риск вспенивания шлака. OSBF имеет гораздо более длительный срок службы, что снижает логистические требования, связанные с заменой футеровки ЭДП (кран, здание, частые простои и т. д.). Потребление электроэнергии аналогично (разница 10%), но эксплуатационные расходы при использовании электродов Сёдерберга, используемых в OSBF, по сравнению с графитовыми электродами ниже, хотя и варьируются. Поток отходящего газа OSBF имеет высокое содержание CO, который можно использовать в качестве топлива для нагревателя технологического газа DRI. Использование окатышей BF в маршруте DRI-OSBF позволяет снизить стоимость сырья на 20% (со 150 до 120 долларов США/т при переходе от сорта DR к окатышам BF). Кроме того, продемонстрировано, что ТМ, производимые новым DRP-OSBF, могут быть объединены с потоком, поступающим от существующих BF. Анализ ТМ и температура выпуска могут быть скорректированы для оптимизации совместимости и минимизации выбросов CO 2 поколение.
Последние результаты, относящиеся к реактору DRI мощностью 2,5 Мт/год, интегрированному с OSBF и BOF, показывают сокращение выбросов CO 2 , показанное на рисунке 12.
стационарная работа ОСБФ, требующая замены огнеупоров каждые 5–7 лет. Наоборот, техническое обслуживание и ремонт оболочки в ДСП требуется после каждых 100–120 плавок (каждые 2 недели). Детальный анализ всего процесса показывает важность использования сырья, указанного в таблице 4.
Как уже упоминалось выше, контроль температуры имеет основополагающее значение. Значительные потери энергии могут быть зарегистрированы, как только новый материал подается в печь, мощность необходима для плавления твердого нового материала, и ее недостаточно для поддержания оптимальной температуры в уже расплавленной ванне. Это серьезное состояние (которое может привести к снижению энергоэффективности на 30 %) известно как «состояние перезарядки». Очевидно, что поток шихты должен точно контролироваться, потому что, наоборот, недостаточная шихта может привести к нежелательному повышению температуры с последующим повреждением огнеупоров. Этот аспект необходимо тщательно учитывать, и основными факторами, влияющими на реакции восстановления в печи, являются химический состав подаваемого материала, профиль температуры в печи и эффекты вторичного плавления. Принимая во внимание химию материала, крайне важно постоянно контролировать поток материала и его состав; оба эти фактора влияют на развитие реакции. Влияние потока свежей руды на химию печи может привести к следующим трем различным состояниям: перегрузка, сопровождающаяся падением энергии, подаваемой на материал в печи, недозагрузка, сопровождающаяся увеличением энергии и температуры печи, и сбалансированная зарядка, сопровождающаяся оптимальным плавлением материала при достаточной мощности и нагреве.
Точная корреляция между этими условиями и скоростью подачи заряда показана на рисунке 13 [15].
По существу, если потребляемая мощность постоянна, то после подачи нового материала в печь энергия, подаваемая на расплав, уменьшается. В условиях избыточного заряда материал имеет тенденцию накапливаться к электродам, вызывая усадку ванны. В этих условиях температура снижается, и, следовательно, степень восстановления замедляется. Первым индикатором этого состояния является то, что процент восстанавливаемого оксида титана быстро уменьшается. Кроме того, равновесие смещается в сторону более окислительных условий и в шлаке обнаруживается повышенное процентное содержание оксида железа. Кроме того, в ванне возникают очень разные условия реакции. Углерод накапливается, создавая огнеупорность ванны и увеличивая ее сопротивление. Таким образом, контроль шлака имеет основополагающее значение для всего процесса. Считается, что химический состав шлака определяется оксидами магния и кальция, как показано на рис. 14.
Температура ликвидуса регулируется процентным содержанием CaO независимо от соотношения MgO/SiO 2 . При изменении процентного содержания CaO от 20 до 14 температура ликвидуса снижается с 1600 до 1350 °C. Процентное содержание SiO 2 определяет превращение шпинели и температуру ликвидуса (от 1500 до 1350 °C, если процентное содержание варьируется от 18 до 24%). Принимая во внимание совместное влияние CaO и MgO, можно отметить, что температура ликвидуса шлака изменяется от 1520 °C при 30 % CaO и 0 % MgO до минимума 1340 °C при 18 % CaO и 12 % MgO до новое увеличение при 1505 °C при 0% CaO и 30% MgO.
Многие исследования показывают, что соотношение Ti 3+ /Ti 4+ приводит к изменению температуры шлака. Зависимость между соотношением и содержанием TiO 2 показана на рисунке 15.
Как видно из рисунка ниже, изменение ленты обусловлено основностью шлака. Это ключевой фактор для настоящего анализа. Как правило, небольшое изменение основности шлака приводит к значительным различиям в температуре ликвидуса. Сводка по выбранным условиям представлена на рис. 16.
Наиболее важной переменной состояния восстановления является основность шлака. Теперь на температуру ликвидуса влияет современное влияние основности шлака и степени окисления титана; можно сделать вывод, что температура ликвидуса в случае шлаков с высокой основностью (CaO/SiO 2 = 1,4) снижалась при увеличении степени восстановления (более высокие отношения Ti 3+ /Ti 4+ ). Как следствие, в случае низкоосновных шлаков (CaO/SiO 2 < 0,8) температура ликвидуса снижается, а восстановление увеличивается. Таким образом, можно изменить температуру ликвидуса и Ti 3+ /Ti 4+ путем изменения соотношения основности. Химический состав печи обычно контролируется путем точного контроля подачи материала и мощности электрода. При работе печи с открытой шлаковой ванной качество продукции и производительность регулируются настройкой соотношения мощность/подача. Во-первых, состав сырья чутко влияет на общий процесс. Кроме того, скорость подачи приводит к сильным колебаниям энергопотребления. Очевидно, что в случае предварительно восстановленных железных руд контроль состава имеет основополагающее значение для оптимального развития превращений металла и шлака.
Как правило, интегрированный традиционный маршрут BF-BOF не так чувствителен к процентному содержанию элементов пустой породы (SiO 2 , Al 2 O 3 и TiO 2 ) по сравнению с новой разработанной DR -маршрут ЭАФ. При превращении ДП основной процент соединений пустой породы переходит в шлак (порядка 150–300 кг/т) с общей основностью порядка 1 и очень низким содержанием железа (около 1 %). Таким образом, содержание кремния в жидком металле, поступающем в конвертер, находится в пределах 0,2–0,7 %. Общая тенденция заключается в том, что по мере уменьшения содержания кремния в доменной печи снижается потребность в энергии и увеличивается производительность [16]. Многочисленные данные исследований (самые последние относятся к доменной печи в Лулео) показывают, что минимальный предел содержания SiO 2 в гранулах BF составляет около 2%.
Замена спеченного материала гранулами оказывает исключительное влияние на потребление энергии в доменной печи. В этой конфигурации содержание кремнезема в окатышах не так важно для маршрута доменной печи. С другой стороны, в случае пути прямого восстановления это содержание очень важно, поскольку процесс происходит в твердом состоянии. В этом случае весь материал направляется в электропечь, где увеличивается содержание шлака по мере увеличения содержания пустой породы.
Кремний в жидком чугуне, а также кремнезем и другие элементы пустой породы в ПВР влияют на количество шлакообразователей, которое необходимо добавить в конвертерный или электродуговую печь, чтобы достичь насыщения шлака MgO, а основность обычно около 2 и более. Насыщенность MgO зависит от температуры шлака и состава в зависимости от различных соединений, таких как FeO, CaO, SiO 2 , P 2 O 5 , Al 2 O 3 , TiO 2 и ВО 2 . Таким образом, процесс должен контролироваться добавлением извести, поэтому по мере увеличения содержания пустой породы необходимо увеличивать процентное содержание извести [17].
На измельчение окатышей сильно влияют основные свойства, такие как пористость, размер частиц и химический состав фаз, присутствующих в руде. Это должно быть максимальным для достижения высокой восстанавливаемости, производительности и высоких степеней металлизации железа прямого восстановления.
Одним из технических ограничений является то, что с увеличением степени металлизации увеличиваются потери в железе из-за образования пустой породы. Металлизация, очевидно, зависит от хвостового содержания руд, которое может находиться в пределах 10–20%.
Очевидно, что на образование шлака в ЭДП большое влияние оказывает качество лома, используемого в процессе. Это приводит к образованию 70 кг шлака на тонну стали в случае использования в ДСП 100 % лома. По этой причине отходы должны быть хорошо обработаны перед поступлением в ЭДП, чтобы уменьшить это неудобство.
Учитывая это, разумное количество шлака в конце процесса DR-EAF составляет около 150 кг/т стали. Это характерно для производства низкоуглеродистой стали, где в шлаке может обнаруживаться высокое процентное содержание FeO.
Опять же, высокий процент шлака приводит к снижению производительности, а также к увеличению потребления энергии и извести, что отрицательно сказывается на экономике процесса. При использовании ПВЖ из железной руды более высокого качества возможно соотношение шлак/сталь порядка 100–120 кг/т при высоком процентном содержании ПВЖ в шихте (более 80%) с соответствующими улучшениями вышеупомянутых факторов и результирующей экономией.
В новом предлагаемом решении реактор DR представляет собой реактор TENOVA HYL с расчетной базой 900 000 т/год DRP. OSBF имеет корпус диаметром 16 500 мм, оснащенный электродами Содерберга диаметром 1700 мм и установкой мокрой газоочистки. Выходной материал имеет состав, указанный в Таблице 5.
Был проведен глубокий анализ для оценки экономической рентабельности решения. Во-первых, в Таблице 6 указаны затраты на горячее ПВП или горячее ПВП, которые будут использоваться в ЭДП и в ОСБТ соответственно.
Во-первых, затраты, связанные с использованием пеллет BF, заметно ниже, чем пеллет прямого восстановления. Затраты, связанные с NG, немного ниже в случае сокращения окатышей DRI. В случае ДРП зафиксировано снижение потребления кислорода почти на 20%. Затраты на DRP на 18% ниже, чем на DRI. В Таблице 7 перечислены затраты, относящиеся к маршрутам ЭДП и ОСБФ.
Во-первых, на трассе OSBF нельзя использовать обрезки. Потребление электродов и соответствующие различия в стоимости должны быть подчеркнуты.
На самом деле следует учитывать маршрут конвертера, поскольку металл OSBF очень похож на чугун. Затраты, связанные с операциями кислородного конвертера для материала DRP-OSBF, перечислены в таблице 8.
Учитывая низкое качество сырья, проблема летучих микроэлементов имеет решающее значение для вопросов окружающей среды и конечного качества жидкой стали [ 18]. В процессе производства стали в окружающую среду выбрасывается много тяжелых металлов и металлоидов. Из-за высоких цен и низкой доступности руды с высоким содержанием, промышленность перейдет на использование большего количества руды с низким содержанием, характеризующейся повышенным процентным содержанием примесей (с высоким содержанием Pb, Cd, Cr и As). Эти тяжелые металлы и металлоиды высокотоксичны, не разлагаются и очень опасны при попадании в землю и водные источники. С другой стороны, летучие соединения обычно улавливаются и перерабатываются в скрубберах [19].].
Степень улетучивания как функция температуры (T) и степени улетучивания (α) может быть выражена следующим образом:
где k(T) – константа скорости улетучивания в единицах с −1 , а f(α) – функция механизма.
Константа скорости улетучивания k(T) имеет аррениусовскую зависимость от температуры:
где A — предэкспоненциальный множитель (с −1 ), E — кажущаяся энергия активации (кДж моль −1 ), R — универсальная газовая постоянная. В неизотермических условиях скорость нагрева можно считать постоянной:
Таким образом, степень улетучивания можно выразить как:
Интегрируя дифференциальную форму f(α), можно получить модель реакции:
Выполняя преобразования и приближения, включая интегрирование Коутса-Редферна:
Параметры E, A и G(α) (или f(α)) представляют собой кинетический триплет, который необходимо определить в ходе кинетического анализа.
Как правило, энергия активации выше 40 кДж/моль указывает на то, что этапом, регулирующим скорость, являются химические реакции; с другой стороны, для значений энергии ниже 20 кДж / моль диффузия является стадией, контролирующей скорость.
Многие экспериментальные результаты показывают, что улетучивание таких элементов, как S, Li, Sn и Pb, можно описать с помощью диффузионной модели. Фактически значения энергии активации улетучивания Pb и S составляют 26,75 и 19,22 кДж/моль соответственно, в то время как Li и Sn показывают более низкое значение 11,65 кДж/моль.
Теперь, во время всего процесса, частицы железной руды растрескиваются с помощью множества различных механизмов, таких как температурные градиенты внутри каждой частицы, изменения скорости набухания из-за минералогии руд, локальное давление из-за процессов улетучивания и диффузии. Этот макроскопический термический крекинг происходит при восстановлении оксида железа и при всех других химических реакциях. Таким образом, поведение летучих элементов влияет на общий процесс. Они могут улетучиваться непосредственно из-за повышения температуры или могут улетучиваться непосредственно во время термического крекинга. Одним из этих двух механизмов может быть этап контроля скорости улетучивания элементов.
Очевидно, что каждый элемент действует по-своему из-за своей внутренней природы. На самом деле такие элементы, как As, S, Li, Sn и Pb, непрерывно испаряются от комнатной температуры до 1000 °C. Так как Pb и S улетучивались в огромных количествах после 500 °C; это согласуется с разложением глины и преобразованием оксида железа в гематит-магнетит-вюстит.